Introduction to High-Voltage Coil Winding Machining Dynamics
In today’s increasingly sophisticated electrical and manufacturing sectors, high-voltage coil winding machines stand at the intersection of precision engineering and advanced automation. These specialized systems enable the reliable production of coils for power transformers, inductors, motors, and a range of critical components in energy, industrial, and transportation applications. Through rigorous integration of servo-driven winders, programmable logic controllers, and digital feedback loops, modern coil winding machinery boosts consistency, reduces material waste, and accelerates throughput. As stakeholders demand higher voltage capacities, tighter tolerances, and enhanced safety features, manufacturers are investing heavily in research, development, and process optimization. This summary unpacks the key forces reshaping the landscape, examines policy impacts, decodes segmentation nuances, highlights regional and competitive dynamics, and offers strategic guidance for decision-makers seeking to harness emerging opportunities.
Transformative Shifts Driving Automation, Digitalization, and Sustainability
The coil winding market is undergoing transformative shifts fueled by digitalization, sustainability mandates, and cross-industry convergence. First, the adoption of smart factory principles has accelerated the integration of Internet of Things (IoT) sensors and real-time analytics, enabling condition-based maintenance and adaptive process control. Consequently, operators can detect winding tension variances or insulation anomalies before they escalate into costly defects. Second, the push for cleaner energy and electrification has expanded demand for coils capable of handling extra high and ultra high voltage scenarios, driving investments in advanced insulation materials and precision servo control. In parallel, machine builders are embedding machine learning algorithms to optimize winding patterns based on material behavior and historical performance data, resulting in faster changeovers and reduced operator intervention. Finally, collaborations between original equipment manufacturers and component suppliers are deepening, fostering modular architectures where programmable controllers, digital drives, and user-friendly HMI suites can be tailored to specific end-use requirements. Together, these developments are propelling coil winding equipment toward higher levels of flexibility, reliability, and return on investment.
Cumulative Impact of United States Tariffs Implemented in 2025
With new tariff measures taking effect in 2025, import duties on high-voltage coil winding machines and critical subcomponents have increased, prompting immediate supply chain recalibration. Equipment manufacturers reliant on overseas servo motors, programmable controllers, and precision winding wire have seen input costs rise, compressing margins. In response, several leading producers have diversified procurement channels, sourcing insulation materials and core laminations from domestic suppliers to mitigate additional duty exposure. Meanwhile, service organizations are adapting by expanding local maintenance capabilities, reducing downtime risk associated with cross-border shipments. As manufacturers revisit total landed cost models, some are considering strategic in-country assembly to preserve competitive pricing without compromising quality standards. Furthermore, longer-term negotiations aim to secure tariff exclusions for essential components under trade-policy carve-outs, reflecting industry advocacy for smoother flow of advanced manufacturing technologies. Through these collective actions, the market is balancing short-term cost pressures with proactive measures to safeguard operational resilience.
Key Segmentation Insights Across Technology, Component, Application, and More
Analysis across multiple dimensions reveals distinct patterns in machine adoption and customization. Based on technology, demand splits among manual coil winding operations for low-volume runs, semi-automatic winding for mid-scale production, and fully automatic systems, the latter leveraging programmable controllers alongside high-precision servo motors for complex coil geometries. Component segmentation highlights core material preferences, distinguishing between air core designs used in high-frequency inductors and magnetic core assemblies for power transformers, while insulation choices span fiberglass, polyethylene, and polypropylene to balance dielectric strength against thermal performance. Primary and secondary windings are optimized separately to support varying current and voltage demands. In terms of end-use industry, automotive applications straddle electric vehicle traction motors and traditional internal combustion engine ignition coils, whereas electrical and electronics deployments encompass consumer electronic inductors and large-scale power generation units, and industrial machines cover both heavy-duty presses and robotic manipulators. Application insights underscore inductors, subdivided into air coil and ferrite types, alongside single-phase and three-phase motor winding systems, and specialized winding for power transformers. Materials for winding wire types range from copper to aluminum and copper-clad aluminum, selected according to conductivity, weight, and cost targets. Functionality requirements categorize machines into capacitive winding for filter circuits, inductive winding for energy storage, and resistive winding for heating elements. Voltage capacity segmentation differentiates low-voltage controls, medium-voltage distribution coils, and high-voltage solutions, the latter further classified into extra high and ultra high voltage variants. Control schemes vary between analog interfaces preferred for simplicity and fully digital platforms enabling advanced diagnostics. Finally, coil architecture segmentation embraces helical, solenoid, and toroidal forms, each serving unique electromagnetic performance criteria.
This comprehensive research report categorizes the High-Voltage Coil Winding Machine market into clearly defined segments, providing a detailed analysis of emerging trends and precise revenue forecasts to support strategic decision-making.
- Technology
- Component
- End-Use Industry
- Application
- Winding Wire Type
- Functionality
- Voltage Capacity
- Control Type
- Coil Type
Key Regional Insights Shaping Investment and Deployment Patterns
Regional dynamics reflect diverse end-market drivers and regulatory landscapes. In the Americas, robust infrastructure modernization programs and an expanding electric vehicle charging network are accelerating investments in high-voltage coil winding systems that deliver rapid changeovers and strict safety certifications. Europe, the Middle East & Africa exhibit strong demand influenced by renewable energy expansion, with wind turbine and solar inverter manufacturers prioritizing machines capable of handling novel composite insulations and tighter environmental standards. In Asia-Pacific, rapid industrialization, government incentives for domestic manufacturing, and a growing electronics sector are fueling adoption of both entry-level semi-automatic winding equipment and high-throughput automated lines, particularly in markets like China, India, and Southeast Asia. Across all regions, policy alignment around energy efficiency and electromobility continues to shape capital spending patterns, steering manufacturers toward solutions that balance productivity gains with sustainable operation.
This comprehensive research report examines key regions that drive the evolution of the High-Voltage Coil Winding Machine market, offering deep insights into regional trends, growth factors, and industry developments that are influencing market performance.
- Americas
- Asia-Pacific
- Europe, Middle East & Africa
Key Company Insights Highlighting Market Leaders and Innovators
Competitive positioning in this market is informed by both global leaders and highly specialized innovators. ACME Mechatronics, Inc.; AL-CO Electric Inc.; and Bachi Company, Inc. have established reputations for reliable standard machines and broad aftermarket support. Gorman Machine Corp. and Hitech Systems Corporation differentiate through turnkey project capabilities and deep system integration expertise. JARSCO Industrial Co. Ltd. and Marsilli S.p.A. drive innovation in servo-based winding platforms, offering modular architectures that can be rapidly configured. Odawara Automation, Inc. and Schleicher International Ltd. focus on precision winding solutions tailored to the power transformer sector, combining advanced tension control with automated inspection. Tanaka Machinery Ltd. rounds out the competitive landscape with compact, cost-effective systems optimized for small to medium enterprises. Together, these companies set performance benchmarks in throughput, customization, and service responsiveness.
This comprehensive research report delivers an in-depth overview of the principal market players in the High-Voltage Coil Winding Machine market, evaluating their market share, strategic initiatives, and competitive positioning to illuminate the factors shaping the competitive landscape.
- ACME Mechatronics, Inc.
- AL-CO Electric Inc.
- Bachi Company, Inc.
- Gorman Machine Corp.
- Hitech Systems Corporation
- JARSCO Industrial Co. Ltd.
- Marsilli S.p.A.
- Odawara Automation, Inc.
- Schleicher International Ltd.
- Tanaka Machinery Ltd.
Actionable Recommendations for Industry Leaders to Drive Growth and Resilience
Industry leaders should pursue a multifaceted strategy to capture emerging opportunities and mitigate risks. First, prioritizing investment in digital control systems and IoT-enabled feedback loops will enhance overall equipment effectiveness and facilitate predictive maintenance, reducing unplanned downtime. Second, diversifying the supplier base for critical components-particularly insulation materials and winding wire-will protect margins against tariff fluctuations and raw material shortages. Third, forging partnerships with robotics integrators and software developers can accelerate the rollout of fully automatic winding lines capable of dynamic changeovers and minimal manual intervention. Fourth, coordinating with regulatory bodies to advocate for streamlined trade provisions and duty relief on advanced manufacturing equipment will support more consistent supply chains. Fifth, expanding workforce capabilities through targeted training programs in digital diagnostics, servo tuning, and quality assurance will ensure technicians can leverage next-generation machine features. Lastly, exploring service-based revenue models-such as performance-based contracts tied to machine uptime-can unlock new streams of recurring income while strengthening client relationships.
Explore AI-driven insights for the High-Voltage Coil Winding Machine market with ResearchAI on our online platform, providing deeper, data-backed market analysis.
Ask ResearchAI anything
World's First Innovative Al for Market Research
Conclusion Emphasizing Strategic Alignment and Market Adaptability
As the high-voltage coil winding market continues its evolution, stakeholders who adeptly integrate digital innovation, optimize supply chains, and engage with emerging regulatory frameworks will secure a competitive edge. Market complexity-driven by technology convergence, material science breakthroughs, and shifting trade dynamics-requires nimble strategies and continuous learning. By aligning investments with long-term sustainability goals and operational agility, equipment manufacturers and end users alike can deliver reliable, cost-effective coil solutions that support the global transition to electrification and renewable energy.
This section provides a structured overview of the report, outlining key chapters and topics covered for easy reference in our High-Voltage Coil Winding Machine market comprehensive research report.
- Preface
- Research Methodology
- Executive Summary
- Market Overview
- Market Dynamics
- Market Insights
- Cumulative Impact of United States Tariffs 2025
- High-Voltage Coil Winding Machine Market, by Technology
- High-Voltage Coil Winding Machine Market, by Component
- High-Voltage Coil Winding Machine Market, by End-Use Industry
- High-Voltage Coil Winding Machine Market, by Application
- High-Voltage Coil Winding Machine Market, by Winding Wire Type
- High-Voltage Coil Winding Machine Market, by Functionality
- High-Voltage Coil Winding Machine Market, by Voltage Capacity
- High-Voltage Coil Winding Machine Market, by Control Type
- High-Voltage Coil Winding Machine Market, by Coil Type
- Americas High-Voltage Coil Winding Machine Market
- Asia-Pacific High-Voltage Coil Winding Machine Market
- Europe, Middle East & Africa High-Voltage Coil Winding Machine Market
- Competitive Landscape
- ResearchAI
- ResearchStatistics
- ResearchContacts
- ResearchArticles
- Appendix
- List of Figures [Total: 34]
- List of Tables [Total: 856 ]
Call-To-Action: Engage with Ketan Rohom to Access the Full Market Research Report
To explore comprehensive data, competitive benchmarking, and in-depth analysis of this dynamic market, contact Ketan Rohom, Associate Director, Sales & Marketing. He can guide you through the report’s insights and help tailor research outcomes to your organization’s strategic objectives. Reach out today to secure your copy and accelerate informed decision-making.
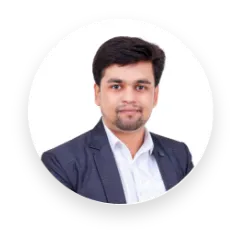
- When do I get the report?
- In what format does this report get delivered to me?
- How long has 360iResearch been around?
- What if I have a question about your reports?
- Can I share this report with my team?
- Can I use your research in my presentation?