The Hydrogen Tank Material Market size was estimated at USD 1.04 billion in 2024 and expected to reach USD 1.12 billion in 2025, at a CAGR 8.12% to reach USD 1.66 billion by 2030.

Unlocking the Promise of Hydrogen Storage for a Clean Energy Future
Hydrogen has emerged as a cornerstone of decarbonization efforts globally, promising to revolutionize sectors ranging from transportation to industrial processes. As the world accelerates towards net zero, the performance, safety, and efficiency of storage solutions become critical. Central to these solutions is the material selection for hydrogen tanks, where innovations in composites, metal alloys, and advanced polymers are enabling higher pressures, reduced weight, and enhanced durability. The interplay between material science breakthroughs and evolving regulatory frameworks is reshaping market dynamics, compelling manufacturers and end users to reassess their strategies for next-generation storage systems.
In this executive summary, we explore the transformative developments influencing material design, regulatory drivers including projected tariff impacts, and a comprehensive segmentation analysis that illuminates trends across material type, tank design, pressure ratings, production scales, and end-user sectors. Regional perspectives reveal distinct growth patterns in the Americas, Europe, Middle East & Africa, and Asia-Pacific markets, while insights into leading companies highlight competitive strategies in research, partnerships, and capacity expansion. Actionable recommendations guide industry leaders on optimizing supply chains, investing in technological advancements, and navigating policy uncertainties. The methodology section outlines our rigorous approach to market intelligence, and the conclusion synthesizes key findings to inform strategic decision-making. This summary offers a clear lens on the current landscape and future trajectory of hydrogen tank materials.
Evolutionary Forces Reshaping Hydrogen Tank Materials
The hydrogen storage market is undergoing a profound transformation driven by an alignment of regulatory mandates, environmental imperatives, and technological breakthroughs. Governments worldwide are setting ambitious zero-emission targets that necessitate safer and more efficient storage solutions. This pressure has accelerated the shift from traditional steel tanks toward advanced composites and hybrid configurations that offer superior strength-to-weight ratios and corrosion resistance.
Meanwhile, advances in material science have opened new frontiers: carbon fiber composites are being optimized for ultra-high pressure applications, fiberglass composites are tailored for cost-efficient mid-range use cases, and high-density polymer composites are emerging as a versatile solution balancing performance and manufacturability. Simultaneously, metal composite alloys and titanium variants are being engineered to withstand extreme conditions in industrial environments.
The maturation of digital technologies, including digital twins, additive manufacturing, and real-time sensor integration, is enhancing design precision and predictive maintenance capabilities. These innovations are fostering closer collaboration between OEMs, material suppliers, and research institutions, resulting in modular tank systems capable of rapid deployment across mobility and stationary platforms.
In tandem with these technical shifts, strategic alliances are emerging to de-risk supply chains and accelerate scale-up. Partnerships between automotive OEMs and composite manufacturers are accelerating the road-to-market for fuel cell vehicles, while energy companies are investing in polymer-based storage for grid-scale applications. As a result, the hydrogen tank material landscape is evolving at an unprecedented pace, setting the stage for widespread adoption in the coming decade.
Assessing the Repercussions of 2025 US Tariffs on Hydrogen Tanks
The implementation of US tariffs slated for 2025 represents a pivotal factor in the hydrogen tank material market, imposing import duties on critical components such as carbon fiber precursors, specialty polymer resins, and strategic metal alloys. These measures are expected to elevate production costs for manufacturers reliant on overseas supply chains, compelling a reassessment of sourcing strategies.
As a result, domestic producers are accelerating capacity expansions in fiber manufacturing, resin compounding, and alloy processing to mitigate exposure to tariff-induced price volatility. At the same time, international suppliers are pursuing tariff-engineering solutions, including the establishment of local fabrication facilities and joint ventures to preserve market access.
Cost pressures are likely to cascade through the value chain, influencing pricing for end users in sectors such as automotive, energy storage, and industrial gas handling. Moreover, the tariffs may stimulate investment in alternative materials that circumvent duty classifications, reinforcing the trend toward high-density polymer composites and certain stainless steel grades that carry more favorable trade treatments.
Stakeholders must navigate this landscape with agility, leveraging predictive analytics to model tariff impacts under various scenarios. Strategic procurement, inventory optimization, and collaborative R&D efforts will be essential to maintain competitiveness. In this context, the 2025 US tariff regime serves not only as a challenge but also as a catalyst for reshaping the market toward greater resilience and self-sufficiency.
Insightful Segmentation Reveals Market Dynamics at Every Level
Material selection emerges as a primary determinant of performance, with the market stratified across composite materials, metals, and polymers. Within composite materials, carbon fiber composites deliver exceptional tensile strength and weight savings for ultra-high pressure applications while fiberglass composites offer a cost-effective alternative for mid-tier pressure vessels. High-density polymer composites provide a tailored balance of rigidity and manufacturability, and metal composites combine metallic and fiber-reinforced constituents to achieve hybrid performance profiles. Metal tanks, encompassing aluminum, composite metal alloys, stainless steel, and titanium, continue to be favored in applications requiring robust structural integrity and resistance to aggressive environmental conditions. Polymers such as polyamide, polyethylene, and polypropylene enable lightweight, corrosion-resistant solutions for lower-pressure systems and niche industrial uses.
Tank design preferences further delineate market demand, with Type I and Type II steel-based cylinders remaining prevalent in applications prioritizing cost efficiency and established manufacturing workflows. The emergence of Type III units, featuring metallic liners reinforced with composite overwraps, offers a midpoint solution that enhances weight-to-strength ratios. Meanwhile, Type IV tanks deploy fully polymeric liners encapsulated by composite layers, achieving the highest weight reduction and fatigue resistance for transportation and aerospace sectors. Pressure rating classification-spanning low-pressure (up to 200 bar), medium-pressure (201 to 350 bar), and high-pressure (351 to 700 bar) thresholds-guides material and design choices based on safety margins, storage density requirements, and regulatory compliance.
Production volume dynamics reveal a dichotomy between custom manufacturing, small-scale production, and large-scale manufacturing. Custom manufacturing services accommodate specialized applications and rapid prototyping, leveraging additive techniques and bespoke tooling. Small-scale production fulfills niche market demands, enabling agility for emerging applications in sectors such as healthcare and specialty chemicals. In contrast, large-scale manufacturing operations achieve economies of scale, driving down per-unit costs for mass-market deployments in automotive and utility storage, underpinned by automated layup processes and high-throughput composite winding machinery.
End user industries exert significant influence on material and design selection. The automotive and transportation sector demands ultra-lightweight, high-pressure tanks to extend range and reduce vehicle mass, driving preference for carbon fiber composites and fully wrapped polymer liners. Chemical companies require corrosion-resistant solutions that withstand aggressive reagents, directing interest toward stainless steel and specialized polymer blends. Energy and utility applications prioritize durability and safety for stationary storage, favoring modular metallic and composite systems. The healthcare arena leverages low-pressure polymer cylinders for portable medical gas delivery, while industrial sectors adopt a diverse range of materials to balance cost, performance, and regulatory mandates.
This comprehensive research report categorizes the Hydrogen Tank Material market into clearly defined segments, providing a detailed analysis of emerging trends and precise revenue forecasts to support strategic decision-making.
- Material Type
- Tank Type
- Pressure Rating
- Production Volume
- End User Industry
Regional Nuances Driving Global Hydrogen Tank Adoption
In the Americas, the convergence of stringent emissions targets and robust infrastructure development has catalyzed demand for advanced hydrogen storage solutions. North America's focus on building a regional hydrogen backbone, supported by government incentives and private investments, has propelled composite tank adoption in both mobility and stationary markets. South American initiatives, particularly in Brazil and Argentina, are exploring green hydrogen for fertilizer production and energy export, driving interest in cost-effective polymer-based storage. The proximity of material suppliers in the United States and Canada has also fostered supply chain resilience, enabling faster commercialization cycles and collaborative R&D across border markets.
The Europe, Middle East & Africa region exhibits diverse growth trajectories shaped by policy landscapes and industrial priorities. The European Union’s Green Deal has instituted rigorous standards for hydrogen storage, accelerating the deployment of Type III and IV tanks with composite reinforcements. In the Middle East, sovereign wealth funds are investing in large-scale green hydrogen projects, prompting the demand for durable metal-composite storage suitable for harsh desert environments. Meanwhile, Africa’s emerging markets leverage polymer-based cylinders for decentralized energy applications, with pilot programs in South Africa and Morocco highlighting the potential for localized manufacturing hubs that serve regional energy needs.
Asia-Pacific stands at the forefront of hydrogen economy expansion, underpinned by government-led roadmaps and industrial partnerships. Japan and South Korea are scaling up composite and alloy tank production for fuel cell vehicles, leveraging domestic strengths in advanced manufacturing and materials engineering. China’s integrated supply chain-from carbon fiber precursors to full-scale tank fabrication-has driven cost reductions, enabling large-scale adoption in public transportation fleets. Southeast Asian nations are piloting hydrogen refueling infrastructure, with an emphasis on polymer-lined tanks for lower-pressure applications. Australia’s export-oriented green hydrogen initiatives further stimulate demand for both stationary and transport storage solutions.
This comprehensive research report examines key regions that drive the evolution of the Hydrogen Tank Material market, offering deep insights into regional trends, growth factors, and industry developments that are influencing market performance.
- Americas
- Europe, Middle East & Africa
- Asia-Pacific
Leading Players Steering Innovation in Tank Materials
Several key companies are shaping the trajectory of hydrogen tank materials through targeted investments and strategic collaborations. Hexagon Purus, a leader in composite overwrapped pressure vessels, has expanded its North American manufacturing footprint to meet rising demand for Type IV tanks in heavy-duty transport. Worthington Industries continues to optimize its metal alloy processing capabilities, deploying advanced stainless steel formulations for industrial gas and energy storage applications.
Luxfer Gas Cylinders harnesses additive manufacturing techniques to accelerate prototyping and produce lightweight composite-metal hybrid designs tailored for aerospace and defense sectors. NPROXX has forged joint ventures with automotive OEMs to co-develop carbon fiber composite liners that exceed global safety standards while achieving weight reductions of up to 40 percent. Quantum Fuel Systems emphasizes vertically integrated polymer compounding, ensuring consistent resin quality and enhanced supply chain control for Type III tank assemblies.
These industry leaders are not only investing in production capacity but also forging R&D partnerships with academic institutions and national labs to advance next-generation materials. Strategic alliances with resin manufacturers, fiber suppliers, and digital solution providers are enabling rapid iteration and improved quality assurance. By diversifying material portfolios and establishing regional production hubs, these companies are positioning themselves to capture market share in a rapidly evolving landscape.
This comprehensive research report delivers an in-depth overview of the principal market players in the Hydrogen Tank Material market, evaluating their market share, strategic initiatives, and competitive positioning to illuminate the factors shaping the competitive landscape.
- Arkema Group
- AVANCO Composites GmbH
- Cevotec
- Envalior by Koninklijke DSM N.V.
- Everest Kanto Cylinders Ltd.
- Faber Industrie SPA
- H2MOF
- Hexcel Corporation
- Hyosung Advanced Materials
- Luxfer Holdings PLC
- Mitsubishi Chemical Corporation
- NPROXX B.V.
- OPmobility SE
- Pragma Industries
- Praxair Technologies, Inc.
- Quantum Fuel Systems LLC
- Solvay S. A.
- Tenaris
- Toray Industries, Inc.
- Toyota Motor Corporation
- Umoe Advanced Composites AS
- Worthington Industries Inc.
Strategic Imperatives to Thrive in a Competitive Landscape
Industry leaders should prioritize investment in advanced composite and polymer technologies to secure a competitive edge. Allocating resources toward research on novel fiber architectures and high-performance resin systems can unlock further weight and cost efficiencies. Simultaneously, diversifying material sources by establishing partnerships with regional suppliers will mitigate tariff exposure and supply chain disruptions.
In addition, organizations must adopt digital transformation strategies, integrating real-time monitoring and predictive maintenance tools to enhance safety and prolong service life. Leveraging digital twins and simulation platforms will streamline design validation and accelerate time-to-market. Cross-sector collaboration-spanning automotive, energy, and aerospace-will facilitate the harmonization of safety standards and best practices, contributing to scalable commercialization.
Finally, companies should develop flexible manufacturing frameworks that accommodate both custom and large-scale production requirements. Implementing modular production cells and scalable automation will enable rapid shifts between low-volume prototyping and high-volume rollouts. By coupling these operational enhancements with proactive regulatory engagement, stakeholders can anticipate policy changes and influence standard-setting processes, ensuring long-term growth and resilience.
Furthermore, sustainability considerations must be integrated into material selection and lifecycle management. Applying circular economy principles-such as recycling composite waste and repurposing decommissioned tanks-will contribute to environmental goals and reduce raw material dependency. By embedding sustainability metrics into strategic planning, leaders can enhance brand reputation and meet the expectations of eco-conscious stakeholders.
Rigorous Methodology Underpinning Market Intelligence
This analysis is grounded in a rigorous market intelligence framework that synthesizes primary and secondary research. Primary insights were obtained through in-depth interviews with key industry stakeholders, including material scientists, OEM engineers, and regulatory authorities. These expert perspectives provided nuanced understanding of emerging trends, technical challenges, and policy impacts.
Secondary data was collated from a curated set of industry reports, peer-reviewed journals, patent filings, and government publications. Trade data and tariff schedules were meticulously reviewed to assess the implications of the 2025 US tariff regime. The study employed data triangulation techniques to validate findings and ensure consistency across multiple information sources.
Quantitative analyses incorporated segmentation models based on material type, tank classification, pressure ratings, production volume, and end-user industries. Regional market assessments were conducted using country-specific demand indicators, infrastructure development indices, and policy frameworks. Company profiling combined financial performance metrics with strategic initiative mapping to identify competitive positioning.
Our methodological approach emphasizes transparency and reproducibility. Data inputs, assumptions, and analytical procedures are documented in detail within the full report. By adhering to best practices in market research, this study delivers actionable intelligence that stakeholders can trust to inform strategic decisions and investment planning.
Explore AI-driven insights for the Hydrogen Tank Material market with ResearchAI on our online platform, providing deeper, data-backed market analysis.
Ask ResearchAI anything
World's First Innovative Al for Market Research
Synthesis of Insights for Stakeholder Engagement
The hydrogen tank material ecosystem is at a pivotal juncture, driven by a confluence of environmental mandates, technological innovations, and evolving trade dynamics. Advancements in composite, metal, and polymer technologies are enhancing storage performance, enabling higher pressures, lighter weights, and greater durability than ever before.
The anticipated 2025 US tariffs introduce both challenges and opportunities, pushing manufacturers toward domestic capacity expansion and alternative material solutions. Segmentation insights underscore the importance of aligning material choices with application-specific requirements, pressure thresholds, and production scales, while end-user industries continue to dictate stringent performance and safety criteria.
Regional markets exhibit unique growth vectors: the Americas benefit from integrated supply chains and policy support; Europe, Middle East & Africa leverage regulatory incentives and large-scale projects; Asia-Pacific drives down costs through vertical integration and mass production. Leading companies are responding with strategic investments in R&D, partnerships, and manufacturing expansions to capture emerging demand.
Actionable recommendations call for a balanced approach that combines technological innovation, supply chain diversification, digital adoption, and sustainability integration. By deploying these strategies within a robust methodological framework, industry participants can navigate uncertainty and position themselves for long-term growth in the dynamic hydrogen storage market.
This section provides a structured overview of the report, outlining key chapters and topics covered for easy reference in our Hydrogen Tank Material market comprehensive research report.
- Preface
- Research Methodology
- Executive Summary
- Market Overview
- Market Dynamics
- Market Insights
- Cumulative Impact of United States Tariffs 2025
- Hydrogen Tank Material Market, by Material Type
- Hydrogen Tank Material Market, by Tank Type
- Hydrogen Tank Material Market, by Pressure Rating
- Hydrogen Tank Material Market, by Production Volume
- Hydrogen Tank Material Market, by End User Industry
- Americas Hydrogen Tank Material Market
- Europe, Middle East & Africa Hydrogen Tank Material Market
- Asia-Pacific Hydrogen Tank Material Market
- Competitive Landscape
- ResearchAI
- ResearchStatistics
- ResearchContacts
- ResearchArticles
- Appendix
- List of Figures [Total: 26]
- List of Tables [Total: 376 ]
Secure Your Comprehensive Hydrogen Tank Material Report Today
To access the comprehensive analysis, detailed segmentation data, and strategic recommendations presented in this report, connect with Ketan Rohom, Associate Director of Sales & Marketing at 360iResearch. He will guide you through tailored subscription options and provide the insights needed to inform your strategic roadmap.
Secure your copy today to gain a competitive advantage in the evolving hydrogen storage market. Empower your decision-making with expert-driven intelligence and chart a path toward sustainable growth.
Reach out to reserve your report and join leading organizations at the forefront of hydrogen tank material innovation.
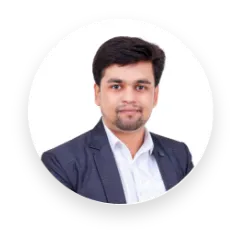
- How big is the Hydrogen Tank Material Market?
- What is the Hydrogen Tank Material Market growth?
- When do I get the report?
- In what format does this report get delivered to me?
- How long has 360iResearch been around?
- What if I have a question about your reports?
- Can I share this report with my team?
- Can I use your research in my presentation?