The In-Plant Logistics Market size was estimated at USD 13.56 billion in 2024 and expected to reach USD 14.94 billion in 2025, at a CAGR 9.68% to reach USD 23.62 billion by 2030.

Exploring the Foundation of In-Plant Logistics Excellence by Unpacking Core Dynamics, Stakeholder Priorities, and Operational Imperatives
In-plant logistics has emerged as a critical differentiator for manufacturers striving to reconcile efficiency, agility, and cost containment within increasingly complex supply chains. At its core, this domain encompasses the orchestration of materials, components, and finished goods across the factory floor, intersecting with production planning, quality control, and distribution networks. Effective in-plant logistics delivers not only throughput optimization but also underpins broader organizational goals such as lean manufacturing, just-in-time delivery, and sustainability targets.
Recent years have witnessed escalating pressures on plant operations: fluctuating consumer demand, supply chain disruptions, and heightened cost scrutiny have forced decision-makers to reevaluate legacy processes. This executive summary frames the essential dynamics of modern in-plant logistics, illuminating both the tangible benefits of technological integration and the strategic challenges that accompany transformational initiatives. Throughout this narrative, stakeholders will gain clarity on market segmentation, regional divergences, tariff impacts, and actionable strategies for seizing competitive advantage.
As manufacturing environments continue to evolve, understanding the interplay between equipment, software, workforce capabilities, and regulatory factors remains paramount. This introduction establishes the foundation for a granular exploration of in-plant logistics, setting the stage for data-driven recommendations tailored to executive leadership and operational managers alike.
Unveiling the Major Technological, Organizational, and Regulatory Transformations Reshaping In-Plant Logistics and Redefining Operational Priorities
The landscape of in-plant logistics is undergoing a profound metamorphosis driven by converging technological, organizational, and regulatory forces. Industry 4.0 paradigms have elevated robotics and advanced automation from pilot projects to mission-critical assets, while the proliferation of Industrial Internet of Things architectures has enabled real-time visibility and predictive insights across material flows. Concurrently, heightened emphasis on sustainability and decarbonization has spurred investment in energy-efficient systems and circular economy practices.
Organizational models are also shifting, with cross-functional teams integrating logistics, production, and quality assurance to foster holistic process improvements. This structural evolution encourages the adoption of digital twins and simulation tools, empowering managers to experiment with layout changes and throughput scenarios before committing valuable capital. Moreover, the regulatory environment has become more stringent, as safety standards and environmental compliance requirements introduce new layers of complexity to plant operations and material handling equipment approvals.
Together, these transformative shifts are redefining in-plant logistics strategies, compelling manufacturers to invest not only in hardware and software but also in talent and governance frameworks. In this context, success hinges on the capacity to align emerging technologies with strategic objectives and to navigate a dynamic regulatory landscape without sacrificing agility or cost competitiveness.
Assessing the Cumulative Effects of 2025 United States Tariff Measures on Equipment Costs, Supply Chains, and In-Plant Logistics Strategies
In 2025, the cumulative impact of United States tariff measures has added notable cost pressures and supply chain complexities for manufacturers and logistics providers alike. Incremental duties on key materials-most prominently steel components used in conveyor frames and automated guided vehicles, as well as aluminum assemblies integral to sortation systems-have elevated capital expenditures and forced procurement teams to reevaluate sourcing strategies. These levies, building upon prior tariff cycles, have effectively reshaped cost curves for imported equipment and commodities.
As a result, many operations have accelerated nearshoring initiatives, seeking local fabrication partners and regional assembly hubs to mitigate duty exposure. While this shift improves supply chain resilience and reduces lead times, it also demands closer coordination with domestic suppliers and can entail higher labor costs. To balance these trade-offs, logistics managers are increasingly negotiating total cost of ownership agreements, integrating asset lifecycle considerations with service contracts and maintenance plans.
Furthermore, the ripple effects of tariff-induced cost inflation have spurred greater emphasis on modular system designs, enabling plant managers to upgrade or reconfigure existing conveyors, sortation modules, and robotics cells without full capital replacement. This modularity has become a critical lever for insulating long-term operational budgets from further tariff volatility, underscoring the strategic importance of equipment versatility in today’s tariff-constrained environment.
Deriving Strategic Implications from Detailed In-Plant Logistics Segment Classifications Spanning Product Types to Order Management
Analyzing the in-plant logistics landscape through a multi-dimensional segmentation lens provides targeted insights into demand drivers and solution adoption patterns. By product type, stakeholders can differentiate between automated guided vehicles offering flexible material transport, conveyor systems designed for high-volume throughput, traditional material handling apparatus, advanced robotics cells, sortation systems optimizing parcel flows, and integrated warehouse management systems that unify workflow control. Such granularity illuminates where capital allocation may yield the highest efficiency returns.
Industry vertical considerations further refine this perspective, with the automotive sector’s blend of manufacturing and parts distribution demanding precision sequencing and high uptime. Energy and utilities environments, by contrast, prioritize robustness in extreme conditions, while the food and beverage domain’s split between beverages and perishable goods underscores temperature, traceability, and hygiene imperatives. Within perishable logistics, requirements for fresh produce diverge from frozen foods, each presenting unique freeze protection and handling protocols. Pharmaceutical operations similarly bifurcate between cold chain logistics and drugs and medicines handling, mandating strict regulatory compliance. Meanwhile, retail and e-commerce fulfillment spans apparel and accessories, electronics, and home furniture, each carrying distinct size, fragility, and packaging considerations.
From a technology standpoint, adoption patterns vary among automation software suites-encompassing logistics management platforms and predictive analytics engines-barcode systems for rapid scanning, IoT frameworks linking connected devices and smart sensors, and RFID solutions distinguishing active from passive implementations. End-user functions such as picking and packing, receiving, shipping, and storage drive specific feature needs, while component segmentation among hardware, services including installation, maintenance, and training, and software licenses shapes vendor engagement models. Order types, whether bulk or individual, influence system throughput and customization levels, and process orientation between pull-based make-to-order models versus push-based make-to-stock workflows dictates buffer capacities and scheduling philosophies. This multifaceted segmentation approach enables executives to align investment and implementation roadmaps with their precise operational profiles.
This comprehensive research report categorizes the In-Plant Logistics market into clearly defined segments, providing a detailed analysis of emerging trends and precise revenue forecasts to support strategic decision-making.
- Product Type
- Industry Vertical
- Technology Type
- End-User Function
- Component
- Order Type
- Process Type
Uncovering Regional Variations in In-Plant Logistics Demand, Innovation Adoption, and Operational Resilience across Americas, EMEA, and Asia-Pacific
Regional dynamics play a pivotal role in shaping in-plant logistics strategies, with each geography presenting distinct adoption rates, regulatory environments, and workforce ecosystems. In the Americas, a mature manufacturing base coupled with escalating e-commerce demand has catalyzed widespread deployment of automation technologies, particularly in automotive assembly and retail distribution centers. North American operations also benefit from established service networks, which facilitate rapid deployment and minimize downtime through localized maintenance support.
Over in Europe, Middle East & Africa, the confluence of stringent environmental regulations and strong sustainability mandates has driven manufacturers to invest in energy-efficient material handling solutions and closed-loop processes. European supply chains often integrate renewable energy sources and demand advanced analytics to monitor carbon footprints, while Gulf Cooperation Council markets are selectively embracing automation to enhance throughput in oil & gas logistics. African manufacturing hubs, still emerging, are exploring cost-effective automation models to leapfrog traditional labor-intensive practices.
In Asia-Pacific, rapid industrial expansion and competitive labor markets have positioned the region at the forefront of cost-efficient automation uptake. China’s advanced robotics ecosystem powers high-speed sortation and AGV fleets, while Southeast Asian countries leverage modular conveyor architectures to scale operations quickly. Japan continues to innovate in autonomous mobile robotics, and India is forging strategic partnerships to localize equipment manufacturing. Together, these regional narratives inform how global players tailor solutions to address divergent market maturity, regulatory frameworks, and labor cost structures.
This comprehensive research report examines key regions that drive the evolution of the In-Plant Logistics market, offering deep insights into regional trends, growth factors, and industry developments that are influencing market performance.
- Americas
- Europe, Middle East & Africa
- Asia-Pacific
Identifying Competitive Strengths, Innovation Trajectories, and Strategic Collaborations among Leading In-Plant Logistics Providers
A cohort of leading providers dominates the in-plant logistics arena through a combination of technological prowess, global support infrastructures, and strategic collaborations. Dematic has leveraged its deep portfolio of conveyor and sortation solutions alongside warehouse management software to offer integrated end-to-end systems, emphasizing modularity and rapid scalability. Honeywell Intelligrated continues to expand its robotics and automated storage retrieval system capabilities, focusing on AI-driven orchestration that enables real-time decision making.
Daifuku stands out for its global footprint in automotive applications, delivering high-precision AGVs and tooling support, while Swisslog is renowned for its automated guided vehicle and robotics integrations within complex cold chain and healthcare environments. Murata Machinery and Vanderlande have advanced the frontier of autonomous mobile robotics, introducing flexible fleets optimized for mixed load profiles. Beyond these marquee names, a vibrant ecosystem of regional integrators and startups is emerging, specializing in niche solutions such as collaborative robots for small parts handling and machine vision-enabled quality inspections. Collectively, these companies are driving competitive differentiation through continuous innovation, strategic M&A activity, and an increasing focus on service-based revenue models.
This comprehensive research report delivers an in-depth overview of the principal market players in the In-Plant Logistics market, evaluating their market share, strategic initiatives, and competitive positioning to illuminate the factors shaping the competitive landscape.
- Access Warehouse Pvt Ltd.
- Autoplant System India Pvt Ltd.
- Axestrack
- BLG LOGISTICS GROUP AG & Co. KG
- Daifuku Co., Ltd.
- Deutsche Post AG
- DGS Translogistics India Pvt. Ltd
- F.W. Neukirch (GmbH & Co.) KG
- Kintetsu World Express, Inc.
- Kion Group AG
- KOBELCO LOGISTICS, LTD.
- LINQcase INDUSTRIAL SOLUTIONS, S.L.
- Mitsubishi Chemical Logistics Corporation
- Nissin Corp.
- NWCC Group
- OAS AG
- ProConnect Integrated Logistics
- Radiant Group
- Redington Limited
- Schenker AG
- Serama Logistics Pvt. Ltd.
- Siemens AG
- SMSA Express Transportation Company Ltd.
- SuperProcure
- TVS Supply Chain Solutions Limited
- Wipro Enterprises (P) Ltd.
- Yusen Logistics Co., Ltd.
Actionable Guidance for Industry Leaders to Drive Automation Integration, Talent Development, and Sustainable Practices in In-Plant Logistics
Industry leaders must adopt a strategic posture that balances immediate efficiency gains with long-term resilience. Embracing modular automation architectures enables scalable deployment, affording plant operations the agility to reconfigure workflows as demand patterns evolve. Concurrently, investing in workforce development-through training programs centered on robotics operation, data analysis, and process optimization-ensures that human expertise complements technological capabilities rather than competing with them.
Digital twin simulations and predictive analytics should become foundational tools in the decision-making arsenal, empowering stakeholders to forecast throughput advantages, identify potential bottlenecks, and optimize maintenance schedules before failures occur. Sustainability considerations must also be embedded in project planning, with energy usage analytics and circular material handling approaches leading the way toward reduced carbon footprints. Finally, fostering collaborative partnerships with technology vendors and academic institutions can accelerate innovation pipelines, unlocking breakthroughs in smart sensors, AI-enabled material sorting, and self-healing conveyor networks. By integrating these recommendations, executives can drive transformative outcomes while safeguarding operational continuity.
Detailing the Structured Research Framework Incorporating Multi-Source Intelligence, Expert Consultations, and Methodological Rigor in Data Collection
The research underpinning this analysis was conducted through a structured, multi-stage methodology designed to ensure methodological rigor and validity. Initial secondary research involved synthesizing data from industry journals, trade association reports, vendor white papers, and publicly available technical standards. These sources provided foundational insights into market segmentation, technology trends, and regulatory frameworks that shape in-plant logistics.
Following this, a series of expert consultations with supply chain architects, operations managers, and automation engineers yielded qualitative perspectives on implementation challenges, performance benchmarks, and adoption roadblocks. Primary surveys targeting C-level executives and plant managers supplemented these insights with quantifiable data points on investment priorities, technology satisfaction levels, and future spending intentions. Finally, all findings underwent a comprehensive triangulation process, cross-referencing secondary data, expert feedback, and survey results to validate key themes and eliminate potential biases. This multi-source approach ensures that the conclusions and recommendations presented herein rest on a robust analytical foundation.
Explore AI-driven insights for the In-Plant Logistics market with ResearchAI on our online platform, providing deeper, data-backed market analysis.
Ask ResearchAI anything
World's First Innovative Al for Market Research
Synthesizing Core Insights to Illuminate the Strategic Imperatives Shaping the Future of In-Plant Logistics Ecosystems Across Global Manufacturing Networks
The confluence of advanced automation technologies, evolving tariff and trade landscapes, and region-specific adoption dynamics underscores a pivotal moment for in-plant logistics. Manufacturers that align their strategies with granular segmentation insights-from product types and industry verticals to process orientations-will be best positioned to unlock efficiency gains and competitive differentiation. Moreover, regional nuances in regulatory requirements and labor cost structures mandate customized approaches rather than one-size-fits-all solutions.
Key imperatives include embracing modular architectures to buffer against future tariff volatility, integrating digital twins and predictive analytics for continuous improvement, and cultivating a skilled workforce capable of stewarding complex automation ecosystems. Strategic collaboration with leading solution providers can accelerate innovation adoption, while an unwavering focus on sustainability will address mounting stakeholder and regulatory pressures. Collectively, these imperatives illuminate a clear pathway toward achieving operational resilience and long-term profitability in an era of heightened uncertainty and opportunity.
This section provides a structured overview of the report, outlining key chapters and topics covered for easy reference in our In-Plant Logistics market comprehensive research report.
- Preface
- Research Methodology
- Executive Summary
- Market Overview
- Market Dynamics
- Market Insights
- Cumulative Impact of United States Tariffs 2025
- In-Plant Logistics Market, by Product Type
- In-Plant Logistics Market, by Industry Vertical
- In-Plant Logistics Market, by Technology Type
- In-Plant Logistics Market, by End-User Function
- In-Plant Logistics Market, by Component
- In-Plant Logistics Market, by Order Type
- In-Plant Logistics Market, by Process Type
- Americas In-Plant Logistics Market
- Europe, Middle East & Africa In-Plant Logistics Market
- Asia-Pacific In-Plant Logistics Market
- Competitive Landscape
- ResearchAI
- ResearchStatistics
- ResearchContacts
- ResearchArticles
- Appendix
- List of Figures [Total: 32]
- List of Tables [Total: 1626 ]
Prompting Immediate Engagement with Expert-Led In-Plant Logistics Research Insights to Elevate Manufacturing Performance Under the Guidance of Ketan Rohom
For those seeking to translate deep insights into operational excellence, engaging directly with Ketan Rohom, Associate Director of Sales & Marketing at 360iResearch, presents a unique opportunity. His guidance can tailor the report’s findings to specific organizational priorities, ensuring that strategic decisions are underpinned by rigorous data analysis and forward-looking perspectives. By initiating a conversation with Mr. Rohom, stakeholders can uncover customized paths to enhance throughput, optimize capital investments, and future-proof their in-plant logistics ecosystems.
Secure access to the comprehensive market research report today to harness actionable intelligence and competitive advantage. Whether refining automation roadmaps, benchmarking regional adoption strategies, or navigating evolving tariff landscapes, this report serves as a catalyst for transformative change. Reach out to Ketan Rohom for a personalized briefing and embark on the next phase of logistics innovation.
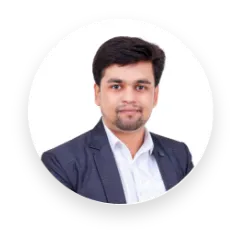
- How big is the In-Plant Logistics Market?
- What is the In-Plant Logistics Market growth?
- When do I get the report?
- In what format does this report get delivered to me?
- How long has 360iResearch been around?
- What if I have a question about your reports?
- Can I share this report with my team?
- Can I use your research in my presentation?