The In Space Manufacturing Market size was estimated at USD 1.21 billion in 2024 and expected to reach USD 1.48 billion in 2025, at a CAGR 22.47% to reach USD 4.10 billion by 2030.

Unveiling the Boundless Frontier of Extraterrestrial Production Pioneering the Next Era of Manufacturing Beyond Earth’s Atmosphere and Gravity Constraints
Unveiling the boundless frontier of extraterrestrial production invites stakeholders to reimagine manufacturing far beyond terrestrial confines. The shift toward fabricating components in low gravity and vacuum environments catalyzes an entirely new value chain characterized by enhanced material properties accelerated innovation cycles and reduced dependency on Earth-based supply networks. As the cost of launch continues to decline and the capabilities of space-rated additive manufacturing and assembly technologies reach maturity a broad spectrum of industries stands poised to capitalize on the unique advantages of in-space fabrication.
Today’s innovators are leveraging microgravity and orbital platforms to produce high-performance optical fibers crystals semiconductors and even biologics that surpass their terrestrial counterparts in purity and structural integrity. This evolution is underpinned by a collaborative ecosystem spanning private enterprises government agencies and academic research institutes each contributing specialized expertise in robotics automation molecular beam epitaxy and vapor deposition techniques. The confluence of these forces signals a profound transformation in how complex systems and advanced materials will be designed manufactured and deployed throughout the emerging orbital economy.
Charting Revolutionary Technological and Operational Paradigm Shifts Reshaping Manufacturing Processes in the Unique Environment of Space and Low Earth Orbit
The landscape of in-space manufacturing is undergoing revolutionary paradigm shifts driven by breakthroughs in additive cell assembly robotics and microgravity casting methodologies. Additive manufacturing payloads now routinely demonstrate the precision deposition of metals polymers and composites within orbital stations while molecular beam epitaxy processes are being repurposed for spaceborne semiconductor fabrication under ultra-clean conditions. Concurrently in-orbit assembly techniques are enabling the construction of large structures beyond launch vehicle fairing limitations fostering more ambitious deep space platforms and modular orbital architectures.
These technological advances coincide with evolving business models that emphasize service-as-a-platform and collaborative public-private partnerships. Providers of on-orbit manufacturing services are integrating production facilities with teleoperation capabilities bridging ground-based design with space-resident execution. Investors are catalyzing infrastructure development through strategic joint ventures bringing together materials specialists system integrators and end-use customers such as satellite operators and biopharmaceutical companies. Altogether these transformative shifts are forging a new industrial fabric wherein manufacturing extends seamlessly from Earth’s surface through extended orbital and deep space missions.
Analyzing the Ripple Effects of U.S. Space Manufacturing Tariffs Evaluating Their Strategic Consequences on Industry Ecosystem and Supply Chain Resilience
The imposition of U.S. tariffs in early 2025 on critical space manufacturing components and raw materials has precipitated a cascade of strategic adjustments across the industry. Components essential for 3D printing feedstock and robotics subsystems have experienced increased landed costs prompting manufacturers to reassess their supplier networks and inventory buffers. This tariff framework, while aimed at bolstering domestic production resilience, has also spurred accelerated qualification of alternative materials such as locally sourced polymers and ceramics and driven a parallel surge in investment toward in-house feedstock extrusion and recycling capabilities.
Furthermore the ripple effects extend to collaboration agreements as international partners realign contractual terms to absorb or share tariff impacts. Original equipment manufacturers are negotiating revised cost-plus arrangements to maintain project viability, and research institutes have adapted their test programs to emphasize technologies less susceptible to trade barriers. In response some integrators are expanding production footprints to U.S. territories to capitalize on tariff exemptions, while others are establishing pre-positioned warehouses in free trade zones to hedge against future tariff escalations. Collectively these measures underscore the necessity for robust supply chain agility and legislative foresight in sustaining in-space manufacturing momentum.
Illuminating Diverse Technological Material Platform Application and End Use Segmentation Revealing Critical Insights Driving Stakeholder Strategies
A comprehensive examination of in-space manufacturing reveals distinct opportunities across multiple axes of segmentation. From a technological standpoint, additive manufacturing via 3D printing remains the workhorse for rapid prototyping and low-volume production, while the maturation of in-orbit assembly techniques unlocks the potential for large-scale structural fabrication in microgravity. Microgravity casting offers unique crystalline microstructures not achievable on Earth, and molecular beam epitaxy is establishing itself as the gold standard for fabricating ultra-high purity semiconductors in vacuum conditions. Meanwhile robotics automation continues to streamline operations and vapor deposition techniques are optimizing thin film coatings for advanced optical and electronic components.
Material selection plays an equally critical role with metals and composites favored for structural elements, polymers offering lightweight versatility and ceramics enabling high-temperature applications. Biomaterials are emerging as foundational substances for biopharmaceutical processing and regenerative medicine platforms, underscoring the sector’s expansion into healthcare & biotechnology. Platform diversity encompasses deep space habitats designed for extended missions, orbital platforms tailored for production and research, and space stations serving as testbeds for system validation and pharmaceutical manufacturing. Applications are broadening from communication satellites and optical fiber drawing to automotive component manufacturing and semiconductors fabrication & assembly, with targeted efforts in biologics, disease modeling & 3D bioprinting, medical devices & implants, and regenerative medicine. End-use adoption spans commercial ventures leveraging cost-efficient production models, government programs advancing national security and exploration objectives, and research institutes driving scientific discovery and proof-of-concept demonstrations.
This comprehensive research report categorizes the In Space Manufacturing market into clearly defined segments, providing a detailed analysis of emerging trends and precise revenue forecasts to support strategic decision-making.
- Technology
- Materials
- Platform
- Application
- End Use
Uncovering Regional Dynamics and Unique Market Drivers Across the Americas Europe Middle East Africa and Asia Pacific in Extraterrestrial Manufacturing
Regional dynamics illustrate divergent maturity curves and strategic priorities. In the Americas the convergence of NASA’s Artemis program objectives with private sector innovation has created an ecosystem rich in orbital and deep space manufacturing initiatives. Major U.S. commercial integrators are collaborating with research institutes to refine microgravity casting processes and scale up additive manufacturing payloads while Latin American nations evaluate participation through technology transfer agreements and regional partnerships.
Across Europe the Middle East and Africa, the European Space Agency’s in-orbit servicing roadmap and emerging regional spaceports are enabling new manufacturing testbeds. National agencies and commercial players are coalescing around projects aimed at producing high-performance optical fibers and biomaterials aboard orbital platforms. Meanwhile initiatives in the Middle East are focusing on developing free-flyer manufacturing modules supported by sovereign wealth funding and advanced university research networks, and African space hubs are exploring niche capabilities in robotics automation and microgravity-adapted composites.
In the Asia-Pacific region, growth is being driven by Japan’s leadership in precision manufacturing technologies and China’s ambitious space station programs. Indian space enterprises are investigating cost-effective deployment of in-space 3D printing for satellite bus components, and Australian research centers are evaluating vapor deposition techniques for advanced semiconductors. Collaborative partnerships across this region are gaining momentum as stakeholders seek to integrate local supply chains and capitalize on government incentives for space technology R&D.
This comprehensive research report examines key regions that drive the evolution of the In Space Manufacturing market, offering deep insights into regional trends, growth factors, and industry developments that are influencing market performance.
- Americas
- Europe, Middle East & Africa
- Asia-Pacific
Highlighting Leading Innovators Pioneering Breakthrough Solutions and Strategic Collaborations Shaping the Future of Spaceborne Fabrication
Leading innovators are distinguishing themselves through targeted investments and collaborative frameworks. Companies specializing in modular additive manufacturing payloads have integrated robotics automation with real-time teleoperation interfaces to expedite production cycles. Meanwhile organizations focused on molecular beam epitaxy and vapor deposition have formed strategic alliances with semiconductor incumbents to adapt their ground-based processes for vacuum-optimized fabrication in orbit. Enterprises in the biomaterials domain are partnering with pharmaceutical pioneers to validate biologics and 3D bioprinting platforms within microgravity laboratories.
Strategic collaborations extend to end-use providers as satellite operators and healthcare companies engage in co-development initiatives to fine-tune product specifications. Some commercial integrators have secured long-term contracts with national space agencies to deploy in-orbit manufacturing modules aboard space stations, while others have diversified into deep space mission support through joint ventures focused on large-scale in-space assembly. Through acquisitions and cross-sector partnerships these key players are consolidating technologies, expanding service offerings and establishing integrated ecosystems that span the full value chain from design and material supply to production and in-orbit deployment.
This comprehensive research report delivers an in-depth overview of the principal market players in the In Space Manufacturing market, evaluating their market share, strategic initiatives, and competitive positioning to illuminate the factors shaping the competitive landscape.
- Airbus SE
- Anisoprint SARL
- ARKA Group, LP
- Astroscale Holdings Inc.
- Axiom Space, Inc.
- Dcubed GmbH
- Lockheed Martin Corporation
- Lunar Resources, Inc.
- Maxar Technologies Holdings Inc.
- Momentus Inc.
- Northrop Grumman Corporation
- Orbital Composites Inc.
- Redwire Corporation
- Rocket Lab USA, Inc.
- Sierra Nevada Corporation
- Space Exploration Technologies Corp.
- Space Forge Inc.
- Space Tango LLC
- Thales Group
- Varda Space Industries, Inc.
- Virgin Galactic Holdings, Inc.
- Voyager Technologies, Inc.
Presenting Actionable Roadmaps and Tactical Initiatives Empowering Industry Leaders to Capitalize on Emerging Opportunities in Space Manufacturing Ecosystem
Industry leaders should prioritize the establishment of resilient supply chains by diversifying material sources and cultivating partnerships that span continental markets and orbital jurisdictions. Investments in dual-use technologies capable of transitioning between terrestrial and space applications can spread development risk and deliver incremental revenue streams. Equally critical is the acceleration of workforce development initiatives focused on microgravity process engineering advanced robotics operations and space systems integration to build the talent pipelines required for sustained growth.
Organizations are advised to engage proactively with regulatory bodies to shape emerging in-orbit production standards and tariff policies, ensuring that operational frameworks remain adaptive to geopolitical shifts. Collaboration with research institutes and startups through open innovation programs can unlock disruptive breakthroughs, while targeted pilot missions demonstrate feasibility and build investor confidence. Finally business models should integrate service-oriented offerings that bundle manufacturing capacity with data analytics and post-production quality assurance to maximize customer value and foster long-term contractual relationships.
Demonstrating Rigorous Research Frameworks and Multimethod Approaches Underpinning Robust Analysis of Space Manufacturing Market Phenomena
The research underpinning this analysis combines primary engagements with domain experts, including engineers and program managers at leading aerospace organizations, and secondary data from technical journals, patent repositories and publicly available mission reports. Qualitative insights were synthesized through structured interviews that explored technology readiness levels, regulatory frameworks and operational modalities across multiple stakeholder groups.
Data triangulation was achieved by cross-referencing interview findings with industry white papers and historical mission outcomes, ensuring robust validation of key trends and drivers. A multimethod approach incorporated comparative case studies of in-orbit and terrestrial analogs, performance benchmarking of manufacturing payloads and scenario planning to assess the influence of policy and macroeconomic variables. Segmentation analysis followed a structured framework encompassing technology, materials, platform, application and end use, while regional assessments leveraged geopolitical analyses and investment tracking to map emerging clusters of activity.
Explore AI-driven insights for the In Space Manufacturing market with ResearchAI on our online platform, providing deeper, data-backed market analysis.
Ask ResearchAI anything
World's First Innovative Al for Market Research
Synthesizing Key Findings and Forward-Looking Perspectives to Illuminate Strategic Imperatives Guiding Next Generation Space Manufacturing Initiatives
Synthesizing the critical findings reveals a rapidly maturing in-space manufacturing domain characterized by accelerating technology convergence and deepening public-private collaboration. The strategic imperative for stakeholders is to integrate multi-segment expertise-from advanced material science to platform operations-while maintaining agile supply chains that can withstand tariff disruptions and regulatory evolution. Forward-looking perspectives emphasize the importance of dual-use systems capable of serving both orbital and terrestrial markets, unlocking diversified value streams and enhancing competitive positioning.
Looking ahead, the trajectory of space manufacturing will be shaped by the orchestration of complex ecosystems that seamlessly connect design centers with orbital production facilities. Success will hinge on forging strategic alliances, investing in workforce readiness and shaping policy frameworks that incentivize innovation while safeguarding intellectual property. By internalizing these insights and adopting an enterprise-wide commitment to in-space production excellence, pioneers will position themselves at the vanguard of the next industrial revolution unfolding beyond our planet.
This section provides a structured overview of the report, outlining key chapters and topics covered for easy reference in our In Space Manufacturing market comprehensive research report.
- Preface
- Research Methodology
- Executive Summary
- Market Overview
- Market Dynamics
- Market Insights
- Cumulative Impact of United States Tariffs 2025
- In Space Manufacturing Market, by Technology
- In Space Manufacturing Market, by Materials
- In Space Manufacturing Market, by Platform
- In Space Manufacturing Market, by Application
- In Space Manufacturing Market, by End Use
- Americas In Space Manufacturing Market
- Europe, Middle East & Africa In Space Manufacturing Market
- Asia-Pacific In Space Manufacturing Market
- Competitive Landscape
- ResearchAI
- ResearchStatistics
- ResearchContacts
- ResearchArticles
- Appendix
- List of Figures [Total: 28]
- List of Tables [Total: 576 ]
Seizing the Opportunity to Acquire Comprehensive Market Intelligence and Engage with Associate Director of Sales and Marketing for Space Manufacturing Success
Unlock unprecedented strategic value by acquiring our comprehensive market intelligence report and engaging directly with Ketan Rohom Associate Director of Sales & Marketing to tailor insights to your organizational goals. This opportunity empowers your team to harness the latest data analytical frameworks design custom go-to-market strategies and refine investment priorities. By partnering with Ketan you will gain privileged access to in-depth interpretation of critical trends and a guided roadmap for deployment that addresses your unique operational and strategic challenges. Seize this chance to convert intelligence into decisive action accelerate time to market and strengthen your competitive position in the rapidly evolving space manufacturing ecosystem.
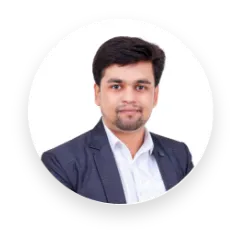
- How big is the In Space Manufacturing Market?
- What is the In Space Manufacturing Market growth?
- When do I get the report?
- In what format does this report get delivered to me?
- How long has 360iResearch been around?
- What if I have a question about your reports?
- Can I share this report with my team?
- Can I use your research in my presentation?