The Industrial 3D Printing Market size was estimated at USD 4.15 billion in 2024 and expected to reach USD 4.87 billion in 2025, at a CAGR 16.74% to reach USD 10.52 billion by 2030.

Understanding the Foundations and Key Drivers Shaping the Industrial 3D Printing Landscape in a Rapidly Evolving Technological Environment
The industrial 3D printing sector has undergone a remarkable evolution, driven by technological breakthroughs, expanding use cases, and a growing emphasis on efficiency and customization. Within this dynamic backdrop, companies across the manufacturing, aerospace, medical, and electronics sectors are increasingly integrating additive processes into their production ecosystems to unlock new design freedoms, reduce lead times, and optimize material usage. This introduction sets the stage for an in-depth exploration of current market dynamics, transformative shifts, and strategic implications that are shaping the trajectory of industrial 3D printing today.
Throughout this summary, the focus will be on delineating the core factors fueling market growth, identifying critical challenges that stakeholders must navigate, and highlighting emerging trends that promise to redefine manufacturing paradigms. The narrative will transition seamlessly from a foundational understanding of key drivers to a detailed examination of regulatory influences, segmentation insights, and regional variations. By doing so, readers will gain a holistic perspective on how technological advancements such as Powder Bed Fusion and Vat Photopolymerization, coupled with material innovations in metals, polymers, ceramics, and composites, are forging new pathways for industrial adoption. Ultimately, this introduction aims to orient decision-makers, investors, and industry leaders, equipping them with the essential context needed to interpret subsequent analyses and craft informed strategic responses.
Exploring the Convergence of Materials Innovation, Digital Integration, and Sustainable Practices Driving Industrial 3D Printing
In recent years, industrial 3D printing has undergone transformative shifts that extend beyond simple adoption of novel machines. The convergence of advanced materials science, data-driven process control, and integrated digital design workflows has fundamentally altered how manufacturers conceptualize product development. Material Jetting and Binder Jetting, for instance, have matured from prototyping tools into reliable production methods capable of producing functional assemblies with complex geometries and fine feature resolution.
Simultaneously, supply chain decentralization and on-demand manufacturing models have emerged as game changers. Organizations are leveraging localized production cells equipped with Material Extrusion and Direct Energy Deposition technologies to minimize inventory costs, mitigate geopolitical risks, and accelerate time to market. This shift is underscored by growing investments in smart factory infrastructure and the adoption of IoT-enabled print farms, where real-time monitoring and predictive maintenance enhance operational uptime.
Moreover, the sustainability agenda has become a pivotal driver for innovation. Manufacturers are seeking eco-friendly resins in Vat Photopolymerization and exploring recyclable metal powders to reduce waste and energy consumption. These developments, coupled with AI-driven process optimization, are characterizing a new era in which additive manufacturing is not only a supplemental technology but a core pillar of digital transformation strategies across industries.
Analyzing the Implications of Newly Implemented United States Tariffs on Materials and Machinery in the 2025 Industrial 3D Printing Ecosystem
The introduction of new United States tariffs in early 2025 has introduced a complex layer of considerations for domestic industrial 3D printing operators and global equipment suppliers alike. With significant duties imposed on imported specialized powders, photopolymers, and select high-precision printers, stakeholders must reassess sourcing strategies and cost structures. Metal Binder Jetting powders, in particular, have been subject to elevated import levies, compelling many service bureaus and original equipment manufacturers to explore domestic alloy production or seek alternative materials with lower tariff exposure.
These regulatory changes have amplified the importance of regional supply chains. Companies are now evaluating partnerships with North American powder producers and resin manufacturers to mitigate the impact of cross-border duties. At the same time, procurement teams are negotiating buffer agreements and flexible contracts to absorb potential cost fluctuations. Although these tariffs have introduced short-term price pressures, they have concurrently stimulated investments in local capabilities, encouraging the expansion of domestic machine fabrication and consumables development.
Looking ahead, navigating this tariff landscape will require agile strategies. Organizations that can leverage forward-buy commitments, optimize inventory rotations, and integrate cost-effective material substitutes are poised to sustain their competitive positioning. As a result, the 2025 tariff adjustments are not simply a fiscal challenge but a catalyst for supply chain innovation and resilience among industrial 3D printing stakeholders.
Unveiling How Technology Categories, Material Types, Machine Classes, and Vertical Industries Interact to Shape Industrial 3D Printing Dynamics
A nuanced segmentation analysis reveals that recent technological advancements are unevenly distributed across the major technology categories. Powder Bed Fusion continues to dominate high-precision metal part production, while Binder Jetting’s evolution into Sand and specialized Metal Binder Jetting subcategories underscores its expanding footprint in complex assemblies and mold making. Material Extrusion remains the go-to for thermoplastic prototypes, but breakthroughs in composite filaments are extending its applications toward end-use components. Concurrently, Material Jetting and Vat Photopolymerization are gaining traction in sectors requiring intricate lattice structures and biocompatible materials, such as healthcare and electronics.
Material selection further nuances market dynamics. Metals and polymers maintain a stronghold due to their established performance characteristics, yet ceramics and composite materials are carving out specialized niches where high-temperature stability and weight-to-strength ratios are critical. As end users increasingly demand customized material properties, suppliers are accelerating R&D cycles to develop novel alloys and hybrid formulations.
Divergence also emerges across machine types and end-user industries. Large-format printers are witnessing heightened uptake in aerospace and automotive facilities for tooling and assembly jigs, whereas desktop and industrial-scale systems serve consumer goods and education sectors. Across aerospace, defense, healthcare, and electronics, organizations are tailoring additive solutions to address specific performance requirements, emphasizing certifications, material traceability, and compliance standards unique to each industry.
This comprehensive research report categorizes the Industrial 3D Printing market into clearly defined segments, providing a detailed analysis of emerging trends and precise revenue forecasts to support strategic decision-making.
- Technology
- Material
- Machine Type
- End User Industry
Examining Regional Specializations and Collaborative Ecosystems Driving Industrial 3D Printing Adoption Across the Americas, EMEA, and Asia-Pacific
Geographic nuances have a profound influence on industrial 3D printing adoption and innovation. In the Americas, robust manufacturing traditions coupled with substantial R&D investments have led to concentrated hubs of advanced metal powder production and machine engineering, supporting rapid prototyping and mid-volume production cycles. North American stakeholders are also pushing forward on regulatory frameworks and standards, ensuring that additive processes meet stringent quality and traceability benchmarks.
Meanwhile, Europe, the Middle East, and Africa exhibit diverse ecosystems where established industrial clusters in Germany and the United Kingdom drive high-precision applications, and emerging markets in the Gulf Cooperation Council are exploring additive manufacturing for energy and infrastructure projects. Collaborative initiatives between governments, research institutions, and original equipment manufacturers are accelerating standardization efforts and funding joint R&D programs.
Across Asia-Pacific, the industry is characterized by aggressive capacity expansions and cost-competitive manufacturing at scale. From additive service bureaus in China deploying multi-laser powder bed fusion systems to Japan’s focus on materials innovation and automation, the region epitomizes rapid commercialization. Southeast Asian countries are also integrating local supply networks to support regional demand, creating a dynamic landscape where cost efficiency and technological sophistication intersect.
This comprehensive research report examines key regions that drive the evolution of the Industrial 3D Printing market, offering deep insights into regional trends, growth factors, and industry developments that are influencing market performance.
- Americas
- Europe, Middle East & Africa
- Asia-Pacific
Highlighting Strategic Alliances, Technological Integrations, and Sustainability Initiatives Led by Market-Leading Industrial 3D Printing Providers
Leading enterprises in the industrial 3D printing domain are advancing their competitive edge through strategic partnerships, mergers, and targeted R&D investments. Key players have expanded their portfolios by integrating software solutions for enhanced design automation, simulation, and build process optimization, reflecting the growing importance of digital thread continuity. Machine manufacturers are collaborating with material science firms to co-develop application-specific powders, resins, and filaments, enabling faster time to qualified production under rigorous industry certification requirements.
Moreover, service bureaus are differentiating themselves by offering end-to-end solutions that blend in-house engineering expertise with multi-technology print farms, ensuring clients can access the ideal production technique for each use case. Joint ventures between equipment vendors and aerospace tier-one suppliers showcase a trend toward co-locating additive production cells within traditional manufacturing pipelines, reinforcing additive’s role in hybrid production environments.
Additionally, several top-tier companies are investing in sustainability programs, such as closed-loop powder recycling and low-emission polymer development, to address environmental concerns and regulatory pressures. By fostering cross-industry alliances and expanding service offerings, these organizations are establishing new benchmarks for quality, reliability, and operational excellence in industrial 3D printing.
This comprehensive research report delivers an in-depth overview of the principal market players in the Industrial 3D Printing market, evaluating their market share, strategic initiatives, and competitive positioning to illuminate the factors shaping the competitive landscape.
- Stratasys Ltd.
- 3D Systems, Inc.
- EOS GmbH
- HP Inc.
- General Electric Company
- Materialise NV
- SLM Solutions Group AG
- Renishaw plc
- Desktop Metal, Inc.
- Voxeljet AG
Implementing Digital Integration, Supply Chain Reconfiguration, and Sustainability Strategies to Accelerate Industrial 3D Printing Success
Industry leaders seeking to capitalize on the rising momentum of industrial 3D printing should first prioritize integration of additive technologies into existing digital manufacturing frameworks. By embedding advanced process simulation tools and analytics platforms, organizations can achieve greater build repeatability, reduce material waste, and accelerate qualification cycles. Furthermore, forging strategic alliances with material suppliers and software developers will ensure access to emerging materials and design automation capabilities.
Next, companies should evaluate their supply chain configurations to incorporate regional hubs and on-demand production cells, mitigating risks associated with tariffs or sudden shifts in trade policies. This approach entails close collaboration with local material producers and service bureaus, coupled with dynamic inventory management models that balance cost efficiency and operational agility. Leaders should also invest in skills development programs, training engineers and operators to master multi-technology print farms and adhere to stringent quality standards.
Lastly, embedding sustainability criteria into technology selection and materials sourcing decisions will not only address environmental imperatives but also unlock cost savings through closed-loop recycling and energy-efficient machine architectures. By aligning additive strategies with broader corporate digital transformation and ESG objectives, industry stakeholders will be poised to achieve enduring competitive advantages.
Leveraging Comprehensive Secondary Analysis, Expert Interviews, and Quantitative Triangulation to Ensure Robust Industrial 3D Printing Insights
This research report is underpinned by a rigorous, multi-faceted methodology designed to capture the nuanced dynamics of the industrial 3D printing market. Secondary research included analysis of proprietary patent filings, regulatory documentation, and industry publications to map technology developments and identify emerging material formulations. Publicly available financial statements and corporate presentations were reviewed to understand strategic investments, partnership announcements, and product roadmaps.
Primary research comprised in-depth interviews with a cross-section of industry experts, including manufacturing engineers, R&D directors, and supply chain managers, to validate trends, assess technology readiness levels, and explore regional adoption drivers. Structured surveys gathered quantitative insights on technology preferences, material usage patterns, and procurement strategies across diverse end-user industries. These insights were triangulated with third-party shipping data and customs records to quantify the impact of tariff changes and regional production shifts.
The combined data sets were analyzed through advanced statistical techniques and scenario modeling to ensure robustness and accuracy of the findings. Qualitative insights from expert panels were integrated to provide contextual depth, ensuring that the report’s conclusions and recommendations are grounded in real-world industry experience and forward-looking strategic considerations.
Explore AI-driven insights for the Industrial 3D Printing market with ResearchAI on our online platform, providing deeper, data-backed market analysis.
Ask ResearchAI anything
World's First Innovative Al for Market Research
Synthesizing Material Innovations, Regional Ecosystems, and Regulatory Shifts to Illuminate the Path Forward for Industrial 3D Printing
In conclusion, the industrial 3D printing landscape is at a pivotal inflection point, where technology maturation, material innovation, and strategic regulatory shifts converge to redefine manufacturing paradigms. Stakeholders who proactively embrace digital integration, cultivate resilient supply chains, and invest in sustainability will unlock unprecedented operational efficiencies and competitive differentiation. The tariff-induced recalibration of materials sourcing underscores the imperative for localized partnerships and agile procurement strategies, while segmentation insights highlight the opportunities that diverse technologies and materials offer across specialized applications.
Regional ecosystems in the Americas, EMEA, and Asia-Pacific each present unique value propositions, from advanced R&D clusters to cost-efficient production hubs, signaling that a one-size-fits-all approach will be insufficient. Leading companies are demonstrating the power of collaborative models, whether through joint ventures, integrated service offerings, or sustainability alliances, to cement additive manufacturing as a core pillar of modern production systems.
By synthesizing these multifaceted insights, this report equips decision-makers with the knowledge required to navigate complexity, harness emerging capabilities, and drive transformative impact. The path ahead is illuminated by strategic foresight, offering a clear blueprint for leveraging industrial 3D printing as a catalyst for innovation and growth.
This section provides a structured overview of the report, outlining key chapters and topics covered for easy reference in our Industrial 3D Printing market comprehensive research report.
- Preface
- Research Methodology
- Executive Summary
- Market Overview
- Market Dynamics
- Market Insights
- Cumulative Impact of United States Tariffs 2025
- Industrial 3D Printing Market, by Technology
- Industrial 3D Printing Market, by Material
- Industrial 3D Printing Market, by Machine Type
- Industrial 3D Printing Market, by End User Industry
- Americas Industrial 3D Printing Market
- Europe, Middle East & Africa Industrial 3D Printing Market
- Asia-Pacific Industrial 3D Printing Market
- Competitive Landscape
- ResearchAI
- ResearchStatistics
- ResearchContacts
- ResearchArticles
- Appendix
- List of Figures [Total: 26]
- List of Tables [Total: 482 ]
Empowering Your Strategic Vision with Exclusive Access to Cutting-Edge Industrial 3D Printing Market Intelligence from a Trusted Industry Authority
If you are ready to harness the full potential of this comprehensive industrial 3D printing market research and gain an unparalleled strategic advantage, reach out to Ketan Rohom, Associate Director of Sales & Marketing, and secure your copy today. With personalized guidance tailored to your organizational needs, you will receive exclusive insights that can catalyze innovation, inform critical business decisions, and drive revenue growth. Engage with a dedicated expert who will walk you through the report’s methodology, highlight the sections most relevant to your goals, and offer practical support in integrating these findings into your strategic roadmap. Don’t miss this opportunity to transform your understanding of the industrial 3D printing market and position your organization at the forefront of technological advancement and competitive differentiation.
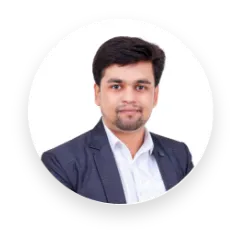
- How big is the Industrial 3D Printing Market?
- What is the Industrial 3D Printing Market growth?
- When do I get the report?
- In what format does this report get delivered to me?
- How long has 360iResearch been around?
- What if I have a question about your reports?
- Can I share this report with my team?
- Can I use your research in my presentation?