The Industrial Centrifuge Market size was estimated at USD 9.24 billion in 2024 and expected to reach USD 9.74 billion in 2025, at a CAGR 5.41% to reach USD 12.68 billion by 2030.

Understanding the Critical Role and Evolving Dynamics of Industrial Centrifuges Across Key Process Industries and Emerging Applications
Industrial centrifuges serve as indispensable workhorses across diverse sectors, facilitating the efficient separation of solids, liquids, and gases in processes ranging from wastewater treatment to pharmaceuticals production. By imparting high centrifugal forces, these machines achieve rapid and precise separation outcomes that conventional methods cannot replicate. This capability underpins critical applications such as clarifying biotech solutions, dewatering mineral concentrates, and isolating organic compounds in chemical synthesis. As end users prioritize throughput, purity, and operational reliability, centrifuge technology continues to evolve to meet stringent performance and compliance standards.
The introduction of advanced materials, digital monitoring tools, and energy-efficient designs has propelled the industry into a new era of precision separation. In tandem, regulatory bodies worldwide have adopted tighter environmental and safety regulations, further highlighting the necessity for robust and compliant equipment. Against this backdrop, stakeholders-from process engineers to C-suite executives-require a comprehensive understanding of market dynamics to inform procurement strategies and capital investment decisions. This report delves into the prevailing trends, structural shifts, and key drivers shaping the industrial centrifuge arena, providing a foundational framework for strategic planning and risk mitigation.
Identifying the Transformative Shifts Reshaping the Industrial Centrifuge Landscape Through Technological Advancements, Regulatory Evolution, and Operational Demands
Recent years have witnessed transformative shifts in the industrial centrifuge domain, marked by accelerated digitalization, heightened environmental scrutiny, and evolving customer expectations for flexible, high-throughput processing solutions. Automation platforms now integrate real-time analytics and predictive maintenance algorithms, enabling operators to preempt performance bottlenecks and extend asset lifespans. Furthermore, modular centrifuge architectures facilitate rapid reconfiguration to accommodate diverse feedstocks, empowering manufacturers to adapt swiftly to fluctuating production requirements.
Simultaneously, sustainability imperatives have spurred the adoption of energy-efficient drive systems and closed-loop solvent recovery modules that minimize waste and reduce carbon footprints. Regulatory landscapes have also tightened, incentivizing equipment suppliers to prioritize compliance features such as explosion-proof components for hazardous environments and advanced sealing technologies to prevent emissions. As a result, research and development investments increasingly target next-generation materials and coatings designed to withstand extreme temperatures and corrosive media, reinforcing centrifuge resilience and longevity.
Moreover, the convergence of industry 4.0 principles with centrifugal separation processes is reshaping competitive dynamics. Companies that harness digital twins, remote diagnostics, and IoT-enabled sensors are unlocking new value streams by delivering performance guarantees and outcome-based service agreements. In this context, manufacturers and end users must stay apprised of these seismic shifts to remain at the vanguard of operational excellence and regulatory compliance.
Examining the Cumulative Impact of 2025 United States Tariff Measures on Industrial Centrifuge Supply Chains and Operational Costs
In 2025, the introduction of revised United States tariff measures on key raw materials and finished centrifuge exports has exerted a layered impact on supply chain economics and procurement strategies. Tariffs on imported alloy steels and precision machined components have driven up input costs, compelling original equipment manufacturers to reassess supplier relationships and geographic sourcing priorities. These adjustments have ripple effects across lead times, with some suppliers consolidating production to mitigate expense pressures and ensure continuity of supply.
End users have responded by exploring localized manufacturing alternatives and increasing collaboration with domestic fabricators to offset elevated import duties. Concurrently, aftermarket service offerings have taken on heightened importance as operators seek to extend the operational lifespan of existing centrifuge assets rather than pursue costly full-scale replacements. Refurbishment programs and component-level retrofits have emerged as cost-effective strategies to maintain performance levels within tighter capital budgets.
Despite near-term cost escalations, market participants view these tariff-driven shifts as catalysts for innovation in design efficiency and supply chain resilience. By prioritizing materials optimization and fostering strategic partnerships, both suppliers and end users can navigate the evolving trade landscape and secure sustainable competitive advantages.
Unveiling Critical Segmentation Insights Based on Type, Application, Material Separation, and Operating Speed Dimensions for Industrial Centrifuges
The industrial centrifuge market exhibits distinct segmentation across four critical dimensions, each influencing equipment design, performance characteristics, and end-use suitability. In terms of type, decanter centrifuges-available in horizontal and vertical configurations-address high-volume solid-liquid separation, whereas disk stack centrifuges, distinguished by manual cleaning and self-cleaning variations, excel at delicate clarifications and emulsification tasks. Pusher centrifuges deliver robust performance in continuous cake discharge scenarios, while tubular bowl designs offer unparalleled resolution for fine solid-liquid partitions.
Application-specific segmentation further delineates the market, reflecting divergent performance requirements and regulatory considerations. Chemical processes bifurcate into inorganic and organic streams, each demanding tailored corrosion-resistant materials and tight separation tolerances. In food and beverage operations, centrifuges handle everything from dairy creaming to beverage clarification, necessitating hygienic construction and ease of sanitation. Mining and mineral processing applications span coal dewatering and resource beneficiation, calling for heavy-duty solids handling and abrasion resistance. Pharmaceutical uses split between biotechnology fermentations and formulation purification, underscoring sterility and process validation imperatives. Finally, wastewater treatment covers both industrial and municipal systems, prioritizing energy efficiency and robust solids management.
Material separation capabilities segment offerings into gas-solid, liquid-liquid, solid-liquid, and solid-solid categories. Within liquid-liquid separation, processes like emulsion breaking and solvent extraction demand precise disk stack designs, while solid-liquid clarification and filtration rely on decanter technology. Solid-solid separation challenges niche recycling and mineral purification sectors, often leveraging specialized centrifuge geometry. Speed-based segmentation reveals that high-speed, low-speed, and ultra-high-speed variants cater to diverse throughput and resolution requirements, enabling end users to match equipment specifications precisely to process objectives.
This comprehensive research report categorizes the Industrial Centrifuge market into clearly defined segments, providing a detailed analysis of emerging trends and precise revenue forecasts to support strategic decision-making.
- Type
- Application
- Material Separation
- Speed
Synthesizing Key Regional Insights to Illuminate Growth Patterns and Challenges Across the Americas, EMEA, and Asia-Pacific Industrial Centrifuge Markets
Regional landscapes for industrial centrifuges present distinct growth trajectories shaped by differing regulatory regimes, end-use industry priorities, and infrastructural capacities. In the Americas, demand for advanced separation technologies is propelled by the maturation of oil and gas operations, burgeoning biopharmaceutical manufacturing hubs, and stringent wastewater treatment mandates. These drivers compel suppliers to offer versatile machines capable of handling heavy sludges, high-throughput clarifications, and sterile bioprocess streams, all while adhering to clean energy targets and US environmental protocols.
Europe, the Middle East, and Africa collectively navigate a complex regulatory mosaic, where strict EU emissions standards and Middle Eastern municipal water treatment expansions coexist with emerging African mining ventures. Suppliers in this region emphasize compliance-ready features, corrosion-resistant builds for arid climates, and service networks that ensure rapid response across vast territories. Sustainability goals within the EU further stimulate innovation in energy recovery modules and membrane-augmented centrifuges.
Asia-Pacific stands as a dynamic engine for centrifuge adoption, driven by large-scale mineral processing projects, a thriving food and beverage sector, and expanding municipal infrastructure programs. Manufacturers cater to diverse end-user needs by delivering scalable, cost-effective solutions that can be rapidly deployed and serviced across densely populated markets. Government initiatives to upgrade sanitation and chemical processing facilities act as catalysts for further equipment uptake, reinforcing Asia-Pacific’s status as a pivotal center of growth.
This comprehensive research report examines key regions that drive the evolution of the Industrial Centrifuge market, offering deep insights into regional trends, growth factors, and industry developments that are influencing market performance.
- Americas
- Europe, Middle East & Africa
- Asia-Pacific
Exploring Strategic Profiles and Competitive Dynamics of Leading Industrial Centrifuge Manufacturers Driving Innovation and Market Leadership
The competitive landscape is characterized by a diverse set of global and regional players that leverage distinct strategies to capture market share and foster innovation. Major manufacturers distinguish themselves through continuous investment in research and development, leading to product enhancements such as real-time condition monitoring, smart control interfaces, and advanced sealing systems that minimize maintenance downtime. Collaborative ventures between centrifuge specialists and automation solution providers have gained traction, enabling the delivery of integrated separation suites that streamline installation and operator training.
Meanwhile, some companies pursue aggressive aftermarket service expansion, establishing localized refurbishment centers and predictive maintenance platforms that enhance uptime and total cost of ownership. Others focus on strategic geographic penetration, forging partnerships with regional distributors and engineering firms to address specific process conditions-from high-altitude mining operations to hypersaline wastewater scenarios. In response to tariff-induced sourcing challenges, a few manufacturers have diversified their supply chains by dual-shoring critical components, thereby ensuring resilience against trade disruptions.
Collectively, these strategic moves reflect an industry-wide emphasis on customer-centricity, technological differentiation, and operational agility. Companies that effectively integrate digital services with core centrifuge offerings are best positioned to cultivate long-term customer loyalty and unlock new revenue streams.
This comprehensive research report delivers an in-depth overview of the principal market players in the Industrial Centrifuge market, evaluating their market share, strategic initiatives, and competitive positioning to illuminate the factors shaping the competitive landscape.
- Alfa Laval AB
- GEA Group Aktiengesellschaft
- ANDRITZ AG
- SPX FLOW, Inc.
- Flottweg SE
- Pieralisi S.p.A.
- Hiller GmbH
- Royal Duyvis Wiener B.V.
- Ashbrook Simon-Hartley, Inc.
- Deister Machine Company, Inc.
Actionable Strategic Recommendations for Industry Leaders to Capitalize on Technological Trends, Regulatory Changes, and Market Opportunities in Industrial Centrifuges
To capitalize on emerging opportunities and navigate evolving challenges, industry leaders should adopt a multi-pronged strategy that emphasizes both operational excellence and customer value creation. Investing in advanced sensor integration and digital twin capabilities will facilitate predictive maintenance and performance benchmarking, thereby reducing unplanned downtime and enhancing throughput. Simultaneously, diversifying manufacturing footprints and forging strategic alliances with domestic suppliers can mitigate tariff-driven cost pressures and bolster supply chain resilience.
Design innovation must remain a priority, with modular architectures that support rapid changeover and scale-out for expansion projects. Embedding sustainability features-such as energy recovery systems and solvent reclamation modules-will address tightening regulatory requirements and appeal to eco-conscious end users. In parallel, companies should expand their aftermarket service portfolios by offering outcome-based contracts, remote performance guarantees, and customized training programs that drive customer satisfaction and long-term partnerships.
Finally, proactive engagement with regulatory bodies and industry associations will ensure early visibility into forthcoming standards and grant a voice in shaping policy frameworks. By combining technological adaptability with strategic foresight, centrifuge providers can secure competitive advantages and deliver tangible value across the equipment lifecycle.
Detailing the Robust Research Methodology Underpinning Comprehensive Analysis of the Industrial Centrifuge Market Landscape
The research underpinning this analysis employs a rigorous, multi-stage methodology designed to ensure data reliability and insight relevance. Initially, extensive secondary research was conducted by reviewing industry publications, white papers, patent databases, and technical journals to establish foundational knowledge of centrifuge technologies and market drivers. This phase also included an examination of regulatory documents and trade policy announcements to assess external pressures influencing the sector.
Primary research complemented these findings through in-depth interviews with process engineers, procurement specialists, and senior executives at key manufacturing and end-use firms. These structured conversations yielded first-hand perspectives on performance requirements, operational challenges, and strategic priorities. Survey instruments targeting maintenance managers and R&D teams provided quantitative input regarding equipment utilization rates, service needs, and innovation adoption.
Data triangulation was achieved by cross-verifying secondary and primary inputs, followed by the application of qualitative analytical frameworks-including SWOT, PESTEL, and Porter’s Five Forces-to distill critical insights. Finally, segmentation logic was validated through iterative consultations with domain experts, ensuring that categorizations accurately reflect market realities. Throughout the process, rigorous quality checks and peer reviews were conducted to uphold analytical integrity and eliminate bias.
Explore AI-driven insights for the Industrial Centrifuge market with ResearchAI on our online platform, providing deeper, data-backed market analysis.
Ask ResearchAI anything
World's First Innovative Al for Market Research
Concluding Perspectives on Key Insights and Strategic Imperatives Shaping the Future of the Industrial Centrifuge Market
In summary, industrial centrifuges continue to evolve as a cornerstone technology for separation processes across critical industries. Technological advancements and sustainability objectives are driving the development of smarter, more efficient, and more resilient equipment, while trade policies and regulatory reforms introduce new strategic considerations for both suppliers and end users. Segmentation insights highlight the nuanced requirements across types, applications, material separation modes, and operating speeds, emphasizing the need for tailored solutions that align with process demands.
Regional patterns underscore a dynamic global market shaped by varied economic priorities and infrastructural imperatives, from the regulatory rigor of EMEA to the rapid expansion of Asia-Pacific industrial capacities. Competitive dynamics reveal a strong emphasis on digital integration, aftermarket services, and geographic agility as key differentiators. Moving forward, companies that adopt a holistic approach-combining design innovation, strategic partnerships, and proactive regulatory engagement-will be best positioned to navigate uncertainties and sustain growth.
By leveraging the actionable recommendations outlined in this report, industry stakeholders can refine their strategic roadmaps, optimize operational efficiencies, and unlock new value streams. The insights presented here form a comprehensive foundation for informed decision-making in an increasingly complex and opportunity-rich landscape.
This section provides a structured overview of the report, outlining key chapters and topics covered for easy reference in our Industrial Centrifuge market comprehensive research report.
- Preface
- Research Methodology
- Executive Summary
- Market Overview
- Market Dynamics
- Market Insights
- Cumulative Impact of United States Tariffs 2025
- Industrial Centrifuge Market, by Type
- Industrial Centrifuge Market, by Application
- Industrial Centrifuge Market, by Material Separation
- Industrial Centrifuge Market, by Speed
- Americas Industrial Centrifuge Market
- Europe, Middle East & Africa Industrial Centrifuge Market
- Asia-Pacific Industrial Centrifuge Market
- Competitive Landscape
- ResearchAI
- ResearchStatistics
- ResearchContacts
- ResearchArticles
- Appendix
- List of Figures [Total: 26]
- List of Tables [Total: 1178 ]
Engage with Ketan Rohom to Unlock Comprehensive Industrial Centrifuge Market Intelligence and Drive Strategic Growth Initiatives
To explore this market intelligence further and discuss how these insights align with your strategic objectives, contact Ketan Rohom, Associate Director of Sales & Marketing. Through personalized consultations, you can gain clarity on vital trends, regulatory impacts, and segmentation opportunities tailored to your organization’s needs. Engage directly to determine the best approaches for leveraging technological advancements, optimizing supply chains, and addressing regional nuances. Secure your comprehensive copy today and equip your leadership team with the actionable intelligence required to outpace competitors and drive sustained growth.
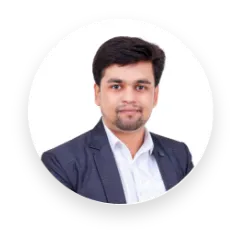
- How big is the Industrial Centrifuge Market?
- What is the Industrial Centrifuge Market growth?
- When do I get the report?
- In what format does this report get delivered to me?
- How long has 360iResearch been around?
- What if I have a question about your reports?
- Can I share this report with my team?
- Can I use your research in my presentation?