The Industrial Control & Factory Automation Market size was estimated at USD 212.71 billion in 2024 and expected to reach USD 238.00 billion in 2025, at a CAGR 12.16% to reach USD 423.58 billion by 2030.

Innovative Era of Industrial Control and Factory Automation Unveiled Through Emerging Technologies and Strategic Significance for Modern Manufacturing
The industrial control and factory automation arena has entered an era defined by unprecedented technological convergence and strategic importance for manufacturers worldwide. Digitalization has reshaped traditional process control, introducing real-time monitoring, predictive maintenance, and adaptive optimization that drive operational excellence. As organizations grapple with complex global supply chains, automation technologies have become central to enhancing resilience, reducing downtime, and maintaining competitive differentiation.
In this landscape, stakeholders are prioritizing solutions that integrate communication and networking capabilities with advanced analytics. Control devices that once served only simple regulatory functions now interface seamlessly with enterprise resource planning systems to deliver holistic visibility across production lines. Moreover, the proliferation of robotics and intelligent sensors has unlocked new levels of precision and throughput while minimizing waste and energy consumption. Consequently, executives must appreciate the strategic convergence of technology, workforce, and data to unlock the full potential of factory automation.
This introduction sets the stage for an in-depth examination of the forces driving transformation, the impact of geopolitical maneuvers on supply chain economics, and the segmented insights that illuminate where value is being created across products, components, automation types, applications, and industry verticals
Pivotal Technological and Market Shifts Transforming Control Systems With Artificial Intelligence Connectivity and Sustainability Driving New Manufacturing Paradigms
Manufacturing is undergoing a transformative shift as artificial intelligence, edge computing, and digital twins converge to redefine the capabilities of industrial control systems. AI-driven algorithms now optimize process parameters in real time, while edge devices collect and process data locally to reduce latency and bolster cybersecurity. Across the sector, digital twin technologies replicate physical assets in virtual environments, enabling scenario testing that accelerates time-to-market and mitigates risks.
Connectivity paradigms have evolved alongside these innovations, with 5G networks expanding bandwidth and reliability for mission-critical operations. The integration of operational technology (OT) and information technology (IT) is more seamless than ever, empowering cross-functional teams to collaborate on digital transformation initiatives. At the same time, sustainability objectives are driving the adoption of energy-efficient controllers and eco-friendly robotics, aligning automation strategies with corporate environmental commitments.
Regulatory frameworks are also adapting, with cybersecurity mandates and data privacy standards prompting the market to prioritize secure by design architectures. These converging shifts are reshaping the manufacturing value chain, demanding agility and foresight from decision-makers who must balance innovation, compliance, and long-term operational integrity
Cumulative Consequences of United States Tariffs on Industrial Control and Factory Automation Supply Chains and Cost Structures Throughout 2025
In 2025, the United States expanded its tariff regime on key industrial electronics, impacting major categories of factory automation imports. These measures have introduced elevated duties on devices originating from strategic trading partners, compelling manufacturers to reassess sourcing strategies and cost models. As a result, some companies are accelerating reshoring initiatives to mitigate tariff exposure, while others are seeking alternative supply bases in regions with preferential trade agreements to preserve margin targets.
Tariffs have also influenced capital expenditure cycles, as procurement teams weigh short-term cost increases against long-term productivity gains. Automation vendors have responded by localizing assembly operations and enhancing service portfolios to add value beyond hardware sales. Moreover, end-users are renegotiating contracts to incorporate total cost of ownership analyses that reflect import duties, currency fluctuations, and logistics expenses.
Ultimately, the cumulative impact of these tariff adjustments in 2025 underscores the interconnected nature of global manufacturing ecosystems. Supply chain resilience and strategic diversification have become paramount considerations, reshaping partnerships among OEMs, distributors, and system integrators. Organizations that proactively adapt to this evolving tariff environment are better positioned to sustain operational continuity and competitive advantage
Comprehensive Segmentation Insights Revealing How Product Types Components Automation Types Applications and Industry Verticals Shape the Control and Factory Automation Landscape
A nuanced understanding of market segmentation reveals where innovation and investment are converging within the industrial control and factory automation landscape. Insights across product types highlight that communication and networking technologies are essential for enabling converged IT/OT infrastructures, while control devices-encompassing distributed control systems, human-machine interfaces, programmable logic controllers, and supervisory control and data acquisition tools-remain the backbone of automated processes. Within robotics, articulated units offer dexterity for complex tasks, Cartesian architectures ensure straightforward pick-and-place operations, and SCARA robots specialize in high-speed precision assembly. Sensor and actuator segments further support real-time feedback loops and motion control.
Component-level analysis underscores the importance of hardware platforms, service offerings, and software ecosystems. Consulting, maintenance and support, system integration, and training and education services are vital for deployment success and ongoing optimization. Software suites, whether integrated into larger platforms or offered as standalone solutions, drive analytics, predictive maintenance, and workflow orchestration.
Examining automation types uncovers distinct deployment models: fixed automation excels in repetitive high-volume tasks, flexible automation adapts to mixed production runs, integrated automation harmonizes cross-process functions, and programmable automation allows rapid reconfiguration. Applications span assembly line automation to material handling systems, packaging and labeling solutions, and advanced quality inspection methods.
Industry vertical segmentation illustrates specialization in aerospace and defense projects, automotive component manufacturing and vehicle assembly, chemical processing, circuit manufacturing and device assembly in electronics and semiconductors, as well as packaging automation and processing equipment for food and beverage. Oil and gas, pharmaceuticals, power and energy, and textiles each present unique automation requirements that drive tailored solution stacks
This comprehensive research report categorizes the Industrial Control & Factory Automation market into clearly defined segments, providing a detailed analysis of emerging trends and precise revenue forecasts to support strategic decision-making.
- Product Type
- Component
- Automation Type
- Application
- Industry Vertical
Regional Dynamics and Growth Drivers Across Americas Europe Middle East Africa and Asia Pacific Influencing Industrial Control and Factory Automation Adoption and Innovation
Regional dynamics are shaping divergent growth trajectories across the primary markets for industrial control and factory automation. In the Americas, the United States remains a leader in advanced manufacturing, with Mexico strengthening its role as a nearshore hub for automotive and electronics production. Canada’s focus on resource-driven industries continues to fuel investments in process control and monitoring solutions, reflecting a blend of efficiency and environmental stewardship.
Across Europe, Middle East, and Africa, Germany and other advanced economies are driving high-value automation through Industry 4.0 roadmaps, supported by robust research and development ecosystems. The United Kingdom and France are integrating sustainability mandates into automation strategies, while the Middle East leverages factory automation to diversify energy-intensive sectors beyond hydrocarbons. In Africa, emerging economies present nascent opportunities for industrial modernization, with pilot deployments in mining and agribusiness highlighting market potential.
Asia-Pacific remains a powerhouse of manufacturing scale, led by China’s commitment to smart factory initiatives and Japan’s continuous innovation in robotics and control architectures. India’s expanding industrial base, supported by government-backed investment programs, is accelerating factory automation adoption. Smaller markets such as those in Southeast Asia and Oceania are also gaining traction, driven by demand for flexible and scalable automation platforms
This comprehensive research report examines key regions that drive the evolution of the Industrial Control & Factory Automation market, offering deep insights into regional trends, growth factors, and industry developments that are influencing market performance.
- Americas
- Europe, Middle East & Africa
- Asia-Pacific
Strategic Company Profiles and Collaborations Highlighting Innovations Partnerships and Competitive Moves by Leading Industrial Control and Factory Automation Providers
Leading companies in industrial control and factory automation are continually redefining their competitive positions through innovation, strategic partnerships, and portfolio expansion. Siemens has intensified its focus on digital enterprise solutions, integrating its open automation ecosystem with cloud-based analytics platforms to deliver end-to-end transparency. Rockwell Automation’s acquisitions of specialized software providers have bolstered its offerings in predictive maintenance and cybersecurity, enabling customers to secure critical infrastructure.
ABB has expanded its robotics and discrete automation footprint through joint ventures and technology alliances, ensuring its solutions cater to both traditional process sectors and emerging high-tech industries. Schneider Electric’s EcoStruxure architecture exemplifies its commitment to convergence, delivering modular control systems and scalable analytics that support sustainability targets. Emerson has leveraged its DeltaV distributed control system to address complex process challenges in oil and gas, refining, and chemical processing, while also introducing mobile interfaces for remote operations.
In the robotics domain, Fanuc’s continued enhancements in machine learning-enabled motion control and Mitsubishi Electric’s integration of automation software into their MELFA robot lineup underscore the importance of seamless software-hardware integration. These leaders are complemented by emerging entrants and specialized integrators that provide niche capabilities, such as edge AI platforms and cybersecurity services, fostering a dynamic ecosystem
This comprehensive research report delivers an in-depth overview of the principal market players in the Industrial Control & Factory Automation market, evaluating their market share, strategic initiatives, and competitive positioning to illuminate the factors shaping the competitive landscape.
- ABB Ltd.
- Accurate Industrial Controls Pvt. Ltd.
- Ametek. Inc.
- Autodesk Inc.
- CODESYS GmbH
- Delta Electronics, Inc.
- Emerson Electric Co.
- FANUC CORPORATION
- Fuji Electric Co., Ltd.
- General Electric Company
- Hitachi, Ltd.
- Honeywell International Inc.
- KUKA AG
- Mitsubishi Electric Corporation
- Murata Manufacturing Co., Ltd
- Omron Corporation
- Panasonic Corporation
- Robert Bosch GmbH
- Rockwell Automation, Inc
- Schneider Electric SE
- Seiko Epson Corporation
- SEW-Eurodrive GmbH & Co KG
- Siemens AG
- Texas Instruments Incorporated
- Toshiba Corporation
- UiPath, Inc.
- Unitronics Ltd.
- Yokogawa Electric Corporation
Actionable Strategies for Industry Leaders to Navigate Supply Chain Disruptions Technological Advancements and Regulatory Challenges in Industrial Control and Factory Automation
To thrive in the evolving landscape of industrial control and factory automation, executives should prioritize investments in digital twin technologies that enable rapid process validation and virtual commissioning. Augmenting this with edge computing architectures reduces system latency and strengthens cybersecurity defenses at the operational level. Organizations must also diversify supply chains by engaging multiple sourcing partners and establishing local assembly footprints to mitigate geopolitical and tariff risks.
Furthermore, fostering strategic alliances with system integrators and specialized service providers can accelerate deployment timelines and ensure best-practice implementation. Emphasizing workforce development through targeted training programs and certification pathways will address the skills gap and empower employees to manage increasingly complex control architectures. In parallel, embedding sustainability criteria into automation roadmaps will align capital expenditures with corporate environmental goals, unlocking potential incentives and enhancing brand reputation.
Finally, adopting an open automation framework that supports interoperability across multi-vendor environments positions manufacturers to integrate emerging AI and analytics tools seamlessly. By following these recommendations, industry leaders can maintain operational resilience, drive continuous improvement, and secure a competitive advantage in a rapidly transforming market
Rigorous Research Approach Integrating Primary Interviews Secondary Data Verification and Advanced Analytical Frameworks to Deliver Deep Insights on Automation Markets
The research underpinning this report combines a structured primary and secondary approach to ensure depth, accuracy, and relevance. Primary research included structured in-depth interviews with C-level executives, plant managers, and technology leaders across key markets, providing firsthand insights into adoption drivers, investment priorities, and deployment challenges. Additionally, expert panels with industry analysts and academic researchers were convened to validate emerging trends and forecast strategic imperatives.
Secondary research involved rigorous examination of public filings, regulatory publications, patent databases, and technical white papers. This was supplemented by analysis of case studies highlighting successful implementations and benchmarking studies that compare performance metrics across industries. All data points were cross-validated through triangulation, ensuring consistency across multiple sources.
Quantitative data was compiled and normalized to reflect relative market dynamics without disclosing proprietary figures, while qualitative inputs were coded to identify thematic patterns. The methodology emphasizes transparency and replicability, with documentation of data sources, interview protocols, and analysis frameworks available upon request
Explore AI-driven insights for the Industrial Control & Factory Automation market with ResearchAI on our online platform, providing deeper, data-backed market analysis.
Ask ResearchAI anything
World's First Innovative Al for Market Research
Synthesis of Key Findings Emphasizing Critical Drivers Barriers and Strategic Imperatives for Sustained Growth in Industrial Control and Factory Automation Sectors
The analysis presented in this executive summary underscores the convergence of digital technologies, supply chain strategies, and regulatory landscapes in reshaping industrial control and factory automation. Technological breakthroughs in AI, edge computing, and digital twins are driving new efficiencies, while sustainability goals and cybersecurity mandates are influencing vendor offerings and deployment models. The 2025 tariff environment has reinforced the importance of supply chain resilience and localized manufacturing strategies.
Segmentation insights reveal that nuanced applications of control devices, robotics, sensors, and software services are central to innovation across diverse industry verticals, from automotive and electronics to pharmaceuticals and energy. Regional dynamics vary significantly, with the Americas benefiting from nearshore networks, EMEA leveraging established research ecosystems, and Asia-Pacific continuing to lead in scale and automation investment.
Strategic moves by leading companies, from digital enterprise platforms to collaborative robotics, demonstrate an ecosystem that values interoperability, service-based models, and advanced analytics. By synthesizing these insights, decision-makers can align investment portfolios with the most impactful technologies and methodologies, ensuring long-term operational excellence and competitive positioning
This section provides a structured overview of the report, outlining key chapters and topics covered for easy reference in our Industrial Control & Factory Automation market comprehensive research report.
- Preface
- Research Methodology
- Executive Summary
- Market Overview
- Market Dynamics
- Market Insights
- Cumulative Impact of United States Tariffs 2025
- Industrial Control & Factory Automation Market, by Product Type
- Industrial Control & Factory Automation Market, by Component
- Industrial Control & Factory Automation Market, by Automation Type
- Industrial Control & Factory Automation Market, by Application
- Industrial Control & Factory Automation Market, by Industry Vertical
- Americas Industrial Control & Factory Automation Market
- Europe, Middle East & Africa Industrial Control & Factory Automation Market
- Asia-Pacific Industrial Control & Factory Automation Market
- Competitive Landscape
- ResearchAI
- ResearchStatistics
- ResearchContacts
- ResearchArticles
- Appendix
- List of Figures [Total: 28]
- List of Tables [Total: 1112 ]
Engaging Call to Action Encouraging Stakeholders to Connect with Ketan Rohom for In-Depth Consultation and Acquisition of the Comprehensive Automation Market Research Report
We invite stakeholders seeking a competitive edge in industrial control and factory automation to reach out to Ketan Rohom, the Associate Director of Sales & Marketing, for personalized guidance and access to the full market research report. Engaging with Ketan ensures direct consultation tailored to your organizational priorities and investment goals, helping you navigate the complexities of supply chain strategies, technological innovations, and regional dynamics.
By connecting, you will gain access to exclusive data tables, in-depth case studies, and strategic frameworks that are not publicly available. This partnership will empower your leadership team to make informed decisions and to capitalize on emerging opportunities in automation, robotics, connectivity, and digital services. Secure your access today and partner with Ketan Rohom to transform insights into actionable strategies for long-term success in the evolving industrial landscape
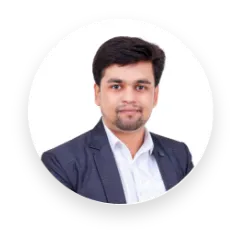
- How big is the Industrial Control & Factory Automation Market?
- What is the Industrial Control & Factory Automation Market growth?
- When do I get the report?
- In what format does this report get delivered to me?
- How long has 360iResearch been around?
- What if I have a question about your reports?
- Can I share this report with my team?
- Can I use your research in my presentation?