Introduction to Conveyor Maintenance in a Dynamic Industrial Landscape
Conveyor systems serve as the circulatory network of modern manufacturing, enabling continuous material movement across production, distribution, and packaging facilities. These mechanized belts and rollers support everything from bulk handling in mines to precision sorting in electronics assembly. As industries pursue higher throughput and tighter delivery schedules, the resilience of conveyor infrastructure emerges as a critical determinant of operational success. Maintenance strategies that blend routine inspections with advanced diagnostics not only safeguard equipment health but also unlock opportunities for performance optimization.
This executive summary distills key trends, regulatory influences, and strategic levers shaping conveyor system maintenance. It examines shifting paradigms-from corrective repairs to predictive analytics-while highlighting the ripple effects of trade policies on supply chains. By mapping insights across industry verticals, maintenance methodologies, and service offerings, this summary equips decision-makers with a holistic understanding of current challenges and transformative solutions.
Structured to deliver concise yet comprehensive analysis, the following sections sequentially explore market dynamics, segmentation perspectives, geographic considerations, and competitive benchmarks. Actionable recommendations are presented to guide industry leaders in enhancing system reliability, optimizing investment, and fostering agile maintenance ecosystems. Ultimately, this document aims to inform strategic planning, stimulate informed dialogue, and drive continuous improvement across conveyor maintenance operations.
Emphasizing preventive and condition-based approaches over reactive fixes, maintenance teams can anticipate wear patterns, preempt disruptions, and reduce unplanned downtime. Integrating sensor networks and real-time monitoring enhances visibility into belt tension, motor vibration, and component wear, laying the foundation for data-driven decision-making. With stakeholders facing increasing pressure to balance productivity with safety and sustainability mandates, the stage is set for transformative adoption of holistic maintenance frameworks.
This executive summary refrains from providing granular forecasts, instead focusing on directional insights and contextual analysis. It serves as a strategic compass for plant managers, maintenance engineers, and C-level executives seeking to elevate conveyor reliability and streamline asset life-cycle management.
Transformative Shifts Reshaping Maintenance Practices
Digital transformation has revolutionized maintenance paradigms, propelling the rise of predictive analytics and artificial intelligence in condition monitoring. Robust sensor integration, cloud-based platforms, and machine learning algorithms enable real-time data capture and anomaly detection, shifting maintenance interventions from scheduled repairs to need-driven servicing.
As organizations adopt Industry 4.0 frameworks, conveyor systems are increasingly instrumented with networked devices that track performance metrics such as belt speed variance, motor current fluctuations, and temperature thresholds. This granular visibility facilitates proactive interventions, reducing reactive labor and spare-parts inventory. Coupled with remote diagnostics, stakeholders can conduct virtual inspections and guide on-site technicians through augmented-reality overlays, accelerating troubleshooting and fostering knowledge transfer.
Workforce dynamics are undergoing a parallel shift, with upskilling initiatives equipping maintenance personnel in data literacy and digital tool utilization. Collaborative robotics and automated guided vehicles are being introduced to complement manual tasks, relieving technicians from repetitive inspections and enabling focus on high-value analysis.
From a regulatory standpoint, stringent safety and environmental standards are catalyzing the adoption of greener lubricants, energy-efficient motors, and modular belt designs that facilitate swift component replacement. Sustainability imperatives are driving circular maintenance models, wherein refurbished rollers and reclaimed belts are reintegrated into service cycles, reducing waste and lowering life-cycle costs.
Building on these digital and operational advances, the convergence of cybersecurity and maintenance emerges as a critical frontier. Protecting networked conveyor assets against cyber threats requires secure communication protocols, access controls, and incident response strategies that safeguard both data integrity and equipment uptime.
Cumulative Impact of United States Tariffs 2025
The introduction of new tariffs on imported conveyor components and spare parts in early 2025 has reverberated across maintenance supply chains, compelling organizations to reassess sourcing strategies and cost structures. Duty increases on critical elements-ranging from high-strength rollers to specialized sensors-have elevated procurement expenses and extended lead times, challenging just-in-time inventory models.
In response, organizations are exploring nearshoring and local manufacturing partnerships to mitigate exposure to tariff-induced cost volatility. By engaging domestic vendors, maintenance teams can accelerate delivery cycles, reduce customs-related delays, and foster closer collaboration on custom component development. Simultaneously, renegotiating long-term service agreements has become a priority, as stakeholders seek to stabilize unit costs and secure flexible contract terms.
These tariff dynamics have also spurred investments in component standardization, allowing interchangeable parts to serve multiple conveyor models and minimizing the complexity of spare-parts catalogs. Standardization reduces the number of unique line items subject to varied duty rates and streamlines maintenance planning.
Furthermore, the cumulative impact of tariffs has highlighted the importance of robust total cost of ownership analyses. Maintenance managers now place greater emphasis on evaluating life-cycle implications of hardware choices, factoring in duty burdens and potential replacement cycles. Engaging cross-functional teams-including procurement, finance, and engineering-in maintenance strategy discussions ensures comprehensive understanding of trade policy risks and fosters resilient supply chain design.
As supply chain architectures adapt to tariff pressures, the resilience of conveyor maintenance operations hinges on strategic diversification and informed decision-making. With this context in mind, the following section delves into key segmentation insights that illuminate market priorities across diverse industry and application dimensions.
Key Segmentation Insights Across Multiple Dimensions
Analyzing conveyor system maintenance through multiple segmentation lenses reveals nuanced priorities and investment patterns. Across industry categories such as food and beverage, manufacturing, mining, and packaging, manufacturing emerges as a focal point, particularly within automotive and electronics sub-sectors where high throughput and precision requirements amplify the need for stringent service regimes. In mining, conveyors operate under dust-laden conditions, driving emphasis on robust sealing and abrasion-resistant components, while packaging lines demand rapid belt changeovers and hygiene-compliant designs in food and beverage facilities.
Maintenance strategy segmentation further underscores a transition from corrective maintenance triggers toward predictive and preventive frameworks. Corrective approaches still address unanticipated breakdowns, but predictive techniques powered by data analytics and sensor integration capture vibration patterns and thermal anomalies ahead of failure, reducing unplanned stoppages. Preventive schedules provide systematic inspection intervals, ensuring component wear is caught before it impedes throughput.
End-user profiles influence service preferences, as engineers seek detailed diagnostic reports, maintenance managers prioritize cost-efficient repair cycles, operators value user-friendly interfaces for routine checks, and safety managers focus on compliance audits and risk assessments. Service offerings span inspections, installation, repairs, and upgrades, with upgrades encompassing component replacement and system overhaul to extend asset life and incorporate performance enhancements.
Technology platform segmentation highlights the proliferation of automation software, control systems, remote monitoring solutions, and an ecosystem of sensors and IoT devices that supply real-time insights. Finally, industry applications ranging from bulk handling to continuous movement to precise material sorting dictate specialized maintenance considerations, from roller alignment in bulk systems to high-speed belt tension calibration in sorting conveyors. Together, these segmentation perspectives map a comprehensive view of market demands and service imperatives.
This comprehensive research report categorizes the Industrial Conveyor System Maintenance market into clearly defined segments, providing a detailed analysis of emerging trends and precise revenue forecasts to support strategic decision-making.
- Industry Categories
- Maintenance Strategies
- End-User Profiles
- Service Offerings
- Technology Platforms
- Industry Applications
Regional Dynamics Driving Maintenance Priorities
In the Americas, emphasis centers on leveraging automation and remote monitoring to optimize operations across sprawling distribution centers and manufacturing hubs, with safety protocols and cost control measures shaping maintenance programs. In Europe, Middle East & Africa, stringent regulatory frameworks around equipment safety and environmental impact drive investments in energy-efficient motors, eco-friendly lubricants, and compliance-oriented inspection routines, while emerging markets within the region focus on scaling infrastructure and workforce training.
Asia-Pacific markets display rapid adoption of digital maintenance solutions, as high-volume electronics and automotive sectors seek to maximize uptime amid competitive pressures. Companies in this region integrate remote diagnostics and cloud platforms to conduct predictive analyses across distributed sites, enabling centralized oversight. Across all regions, service providers tailor offerings to align with local labor dynamics, regulatory landscapes, and supply chain maturity, ensuring maintenance programs resonate with regional operational realities and strategic objectives.
This comprehensive research report examines key regions that drive the evolution of the Industrial Conveyor System Maintenance market, offering deep insights into regional trends, growth factors, and industry developments that are influencing market performance.
- Americas
- Asia-Pacific
- Europe, Middle East & Africa
Competitive Landscape and Leading Market Players
Competition in conveyor maintenance services spans global engineering firms, regional specialists, and technology innovators. Companies such as Advanced Beltline Technologies Inc., Apex Industrial Conveyors LLC, and Atlantic Belt Conveying Company have established reputations for customized belt solutions and responsive field services. Beltline Engineering Group Inc. and BeltTech Systems LLC differentiate through proprietary conveyor designs and modular upgrade packages, while Continental Conveyor Systems Inc. and Conveyor Dynamics & Consulting Ltd. leverage extensive integration expertise for large-scale mining and manufacturing projects.
Service-centric organizations including Conveyor Maintenance Solutions, Inc., Delta Conveyor Systems Inc., and Nova Conveyor Services Inc. focus on preventive and corrective maintenance contracts, offering on-site inspections, rapid repairs, and component remanufacturing. Equipment manufacturers like Dorner Manufacturing Corporation and FlexLink International AB extend maintenance portfolios with embedded analytics in control systems, enhancing remote monitoring capabilities.
Global Conveyor Engineering, Inc. and Hytrol Conveyor Company LLC excel in high-speed sorting applications, whereas Industrial Conveyor Technologies GmbH and EuroConveyor Maintenance Services GmbH address stringent European compliance standards. NorthStar Conveyor Inc. and Orion Conveyors and Automation Inc. emphasize turnkey installation and system overhaul, supported by Pacific Conveyor Innovations and Precision Conveyor Services Ltd. for specialized bulk handling solutions.
ProConvey Solutions LLC, Ridge Belt Systems Ltd., and Smart Conveyance Ltd. champion sensor-driven predictive maintenance modules, anchored by Sterling Conveyor Engineering’s focus on component replacement and turnkey retrofits. Summit Conveyor Solutions LLC and Synergy Conveyor Solutions contribute collaborative maintenance platforms, while Titan Conveyors, Inc., United Conveyor Technologies, Vanguard Conveyor Solutions, and Zenith Conveyor Maintenance Inc. represent full-service providers with comprehensive lifecycle support. This diverse competitive landscape ensures that end-users can access tailored maintenance solutions aligned with their operational scale, technical requirements, and service expectations.
This comprehensive research report delivers an in-depth overview of the principal market players in the Industrial Conveyor System Maintenance market, evaluating their market share, strategic initiatives, and competitive positioning to illuminate the factors shaping the competitive landscape.
- Advanced Beltline Technologies Inc.
- Apex Industrial Conveyors LLC
- Atlantic Belt Conveying Company
- Beltline Engineering Group Inc.
- BeltTech Systems LLC
- Continental Conveyor Systems Inc.
- Conveyor Dynamics & Consulting Ltd.
- Conveyor Maintenance Solutions, Inc.
- Delta Conveyor Systems Inc.
- Dorner Manufacturing Corporation
- EuroConveyor Maintenance Services GmbH
- FlexLink International AB
- Global Conveyor Engineering, Inc.
- Hytrol Conveyor Company LLC
- Industrial Conveyor Technologies GmbH
- NorthStar Conveyor Inc.
- Nova Conveyor Services Inc.
- Orion Conveyors and Automation Inc.
- Pacific Conveyor Innovations
- Precision Conveyor Services Ltd.
- ProConvey Solutions LLC
- Ridge Belt Systems Ltd.
- Smart Conveyance Ltd.
- Sterling Conveyor Engineering
- Summit Conveyor Solutions LLC
- Synergy Conveyor Solutions
- Titan Conveyors, Inc.
- United Conveyor Technologies
- Vanguard Conveyor Solutions
- Zenith Conveyor Maintenance Inc.
Actionable Recommendations for Industry Leaders
- Invest in predictive maintenance programs that leverage sensor integration and data analytics to detect early warning signs and minimize unplanned downtime.
- Standardize critical components and adopt modular belt designs to streamline spare-parts inventory and simplify maintenance workflows.
- Diversify the supply chain by establishing partnerships with domestic and regional manufacturers to mitigate tariff impacts and shorten lead times.
- Implement cloud-based remote monitoring platforms and secure communication protocols to enable real-time oversight and rapid troubleshooting across distributed sites.
- Prioritize workforce development by training technicians in digital tools, augmented-reality diagnostics, and cross-functional collaboration to enhance response agility.
- Align maintenance practices with sustainability objectives by adopting energy-efficient motors, eco-friendly lubricants, and circular maintenance models that promote component refurbishment.
- Engage in proactive regulatory compliance reviews and integrate risk assessments led by safety managers to uphold industry standards and reduce liability.
Explore AI-driven insights for the Industrial Conveyor System Maintenance market with ResearchAI on our online platform, providing deeper, data-backed market analysis.
Ask ResearchAI anything
World's First Innovative Al for Market Research
Conclusion: Steering Maintenance Strategies Toward Excellence
Effective conveyor system maintenance demands an integrated approach that unites technological innovation, operational agility, and strategic foresight. As digital transformation reshapes maintenance paradigms, organizations that embrace predictive analytics, remote monitoring, and cybersecurity measures will unlock new levels of equipment reliability and cost efficiency. Tariff-driven supply chain disruptions underscore the value of sourcing resilience and component standardization, reinforcing the need for diversified vendor networks and robust total cost analyses.
Segmented insights across industry verticals, maintenance methodologies, end-user profiles, service portfolios, and geography reveal distinct priorities that must inform strategy development. By benchmarking against leading providers and adopting actionable best practices, maintenance leaders can drive continuous improvement and align asset-management frameworks with overarching business objectives. Through targeted investments, workforce upskilling, and collaborative vendor relationships, the path toward maintenance excellence becomes both attainable and sustainable.
This section provides a structured overview of the report, outlining key chapters and topics covered for easy reference in our Industrial Conveyor System Maintenance market comprehensive research report.
- Preface
- Research Methodology
- Executive Summary
- Market Overview
- Market Dynamics
- Market Insights
- Cumulative Impact of United States Tariffs 2025
- Industrial Conveyor System Maintenance Market, by Industry Categories
- Industrial Conveyor System Maintenance Market, by Maintenance Strategies
- Industrial Conveyor System Maintenance Market, by End-User Profiles
- Industrial Conveyor System Maintenance Market, by Service Offerings
- Industrial Conveyor System Maintenance Market, by Technology Platforms
- Industrial Conveyor System Maintenance Market, by Industry Applications
- Americas Industrial Conveyor System Maintenance Market
- Asia-Pacific Industrial Conveyor System Maintenance Market
- Europe, Middle East & Africa Industrial Conveyor System Maintenance Market
- Competitive Landscape
- ResearchAI
- ResearchStatistics
- ResearchContacts
- ResearchArticles
- Appendix
- List of Figures [Total: 28]
- List of Tables [Total: 417 ]
Next Step: Connect with Ketan Rohom to Access In-Depth Analysis
To gain comprehensive insights and strategic guidance tailored to your conveyor maintenance challenges, connect directly with Ketan Rohom, Associate Director, Sales & Marketing, to purchase the complete market research report. By securing the full analysis, you will access detailed segmentation findings, competitive benchmarks, and customized recommendations designed to optimize maintenance programs, reduce lifecycle costs, and enhance operational resilience. Reach out today to take the next step toward elevated asset performance and measurable ROI.
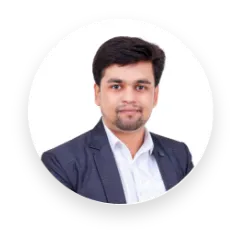
- When do I get the report?
- In what format does this report get delivered to me?
- How long has 360iResearch been around?
- What if I have a question about your reports?
- Can I share this report with my team?
- Can I use your research in my presentation?