Introduction to Industrial Grade Borated Polyethylene Materials
Borated polyethylene represents a crucial class of polymeric materials engineered to combine the hydrogen-rich matrix characteristic of polyethylene with boron-based additives that significantly enhance neutron attenuation. This synergy has propelled its adoption in safety-critical environments such as medical imaging suites, nuclear power facilities, defense installations, and research laboratories. The intrinsic properties of these materials-ranging from impact resistance and thermal stability to chemical resistance-ensure both operational longevity and regulatory compliance. As global emphasis intensifies on radiation protection, the demand for industrial grade borated polyethylene has accelerated, driven by evolving safety standards, technological advancements in manufacturing processes, and the imperative to reduce environmental footprint.
Looking ahead, technological innovations such as advanced extrusion and lamination techniques, coupled with rigorous ASTM and ISO testing regimes, are redefining performance benchmarks for shielding materials. Meanwhile, end-user industries ranging from aerospace and defense to healthcare and automotive increasingly require customized solutions that balance form factors-blocks, pellets, rods, and sheets-with precise density and thickness specifications. The dynamics of raw material sourcing and finished product packaging further shape value chains, underscoring the importance of agile supply networks and strategic partnerships. This executive summary distills these complexities into actionable insights, setting the stage for a deeper dive into transformative shifts, tariff impacts, segmentation analysis, regional variations, and competitive landscapes.
Transformative Shifts Reshaping the Borated Polyethylene Sector
Over the past five years, the borated polyethylene market has undergone a series of transformative shifts driven by technological, regulatory, and application-level developments. First, advanced manufacturing processes such as precision extrusion, multi-layer lamination, and high-pressure molding have enabled fabricators to achieve tighter tolerances and complex geometries, meeting the nuanced requirements of medical imaging facilities, nuclear power plants, and aerospace components. Moreover, the integration of enhanced testing protocols aligned with ASTM and ISO standards has elevated quality assurance, reducing batch-to-batch variability and reinforcing stakeholder confidence in product performance.
Simultaneously, material property innovations have broadened the functional envelope of borated polyethylene. Enhanced thermal resistance formulations now accommodate higher temperature applications without compromising structural integrity, while impact- and chemical-resistant grades ensure durability in harsh operational environments. Density optimization, spanning low-, medium-, and high-density grades, allows for tailored neutron attenuation profiles-a critical consideration for radiation shielding in commercial buildings, industrial sites, and research laboratories. In addition, the emergence of ultra-thin and ultra-compact sheet variants has unlocked new use cases in mobility aids components and electronics manufacturing, where space constraints and weight considerations are paramount.
Furthermore, digital transformation initiatives are reshaping supply chain resilience and customer engagement. Real-time tracking, predictive analytics, and collaborative platforms streamline order fulfillment and optimize inventory levels across regions. Combined with growing regulatory pressures for sustainable manufacturing and waste reduction, these developments underscore a market in flux, where agility and innovation define competitive advantage.
Assessing the 2025 United States Tariffs on Borated Polyethylene
Beginning January 2025, the implementation of revised United States tariffs on borated polyethylene imports has introduced a significant inflection point for both domestic producers and global suppliers. The revised duty schedules, which impose higher rates on specific tariff classifications associated with polymer-based radiation shielding materials, have elevated landed costs for inbound shipments. As a result, many end-users in healthcare, nuclear energy, and defense sectors now face tighter budgetary constraints and must reassess procurement strategies to mitigate cost escalation.
In response, several membrane fabricators and converters have accelerated plans to localize production within the Americas, leveraging existing extrusion, lamination, and molding infrastructure to capture tariff-free supply. This shift has translated into strategic capital investments in domestic manufacturing lines and joint ventures with regional partners. At the same time, importers are exploring tariff engineering techniques, such as reclassifying finished product forms and leveraging customs reconciliations, to optimize duty exposure.
These adjustments have ripple effects throughout the value chain. Distributors are renegotiating terms with raw material suppliers, while integrators in construction and engineering adapt project budgets to reflect adjusted material costs. In parallel, pricing dynamics have led some international suppliers to absorb portions of the tariff increases, preserving market share at the expense of margin compression. As global trade negotiations continue, industry players must remain vigilant, monitoring policy developments and aligning supply chain configurations to sustain competitiveness.
Key Market Segmentation for Borated Polyethylene Materials
The borated polyethylene market can be dissected through multiple segmentation lenses, each revealing distinct opportunities and priorities for materials developers and end-users. Based on product type, the market encompasses solid blocks, precision pellets, structural rods, and versatile sheets, with each form factor tailored to specific installation and fabrication workflows. Across density variations-ranging from low- to medium- to high-density grades-tuning boron content and polymer matrix composition optimizes neutron attenuation efficiency while balancing weight and mechanical properties.
Thickness considerations further refine material selection, as medium and thick panels deliver robust shielding for nuclear power plants and industrial sites, whereas thin and ultra-thin films serve compact medical imaging suites and electronics enclosures. Application-driven nuances emerge when examining construction and engineering scenarios, which bifurcate into commercial building projects and heavy-duty industrial facilities, and manufacturing domains that span automotive assemblies and electronics component housing. Within the healthcare sector, borated polyethylene components are integral to both healthcare facilities’ radiation-controlled environments and mobility aids components designed for patient safety. Meanwhile, radiation shielding applications extend from medical imaging units to nuclear reactor containment and advanced research laboratory setups.
Material form represents another axis of differentiation, where finished product forms demand precision fabrication and raw material forms support further downstream processing. End-user industries such as aerospace, defense, healthcare, nuclear energy, and research and development each impose unique performance criteria and certification requirements. Manufacturing processes-including extrusion for continuous profiles, lamination for multi-layered constructs, and molding for complex geometries-drive cost structures and throughput rates, while property-based segmentation highlights chemical resistance, impact resistance, and thermal resistance as critical performance metrics. Finally, alignment with testing standards, whether ASTM benchmarks or ISO protocols, and packaging preferences, spanning bulk shipments to custom-tailored solutions, complete a comprehensive segmentation framework that underpins strategic decision-making.
This comprehensive research report categorizes the Industrial Grade Borated Polyethylene Materials market into clearly defined segments, providing a detailed analysis of emerging trends and precise revenue forecasts to support strategic decision-making.
- Product Type
- Density
- Thickness
- Application
- Form
- End-User Industry
- Manufacturing Process
- Property
- Testing Standards
- Packaging
Regional Dynamics Driving Borated Polyethylene Demand
Northern and Southern Americas continue to dominate demand for borated polyethylene materials, underpinned by a robust pipeline of nuclear energy projects, expansions in medical imaging infrastructure, and defense modernization programs. Supply chain agility and proximity to key raw material sources have enabled manufacturers to optimize lead times and reduce logistics costs, reinforcing the region’s competitive edge. Meanwhile, Europe, Middle East and Africa are characterized by stringent safety regulations and significant investments in research and development, particularly within the nuclear and healthcare sectors. Regional collaborations on standardization, combined with government mandates for enhanced radiation protection, are driving adoption of advanced borated polyethylene composites.
In the Asia-Pacific arena, rapid industrialization, burgeoning healthcare facilities, and a growing fleet of nuclear and renewables-based energy plants are fueling material demand. Local producers are scaling capacity to serve domestic megaprojects, while international suppliers establish partnerships to navigate regional regulatory frameworks and capitalize on emerging infrastructure investments. Across all regions, evolving end-user requirements and regulatory regimes underscore the importance of geographic diversification and localized service capabilities to capture growth opportunities.
This comprehensive research report examines key regions that drive the evolution of the Industrial Grade Borated Polyethylene Materials market, offering deep insights into regional trends, growth factors, and industry developments that are influencing market performance.
- Americas
- Asia-Pacific
- Europe, Middle East & Africa
Leading Suppliers and Strategic Movements in the Industry
The competitive landscape features a mix of specialized entrants and large-scale polymer suppliers, each vying for differentiation through technological innovation, comprehensive service offerings, and strategic partnerships. A-Radiation Shielding Systems leads with customized shielding solutions, while Advanza Materials focuses on high-precision extrusion technologies. Alro Plastics and Amar Industries leverage broad product portfolios to address diverse density and thickness requirements. Boral Material Technologies and Carmel Industries have strengthened market share through investments in lamination capabilities, whereas Ecomass Technologies and Eljen Technology emphasize environmentally sustainable formulations.
Emco Industrial Plastics and Modern Plastics, Inc. provide vertically integrated services spanning raw material compounding to finished component fabrication. Nuclear Lead Co., Inc. and Paragon Medical specialize in medical imaging and healthcare facility applications, and QMP Racing Products demonstrates the versatility of borated polyethylene within niche high-performance sectors. Radiation Protection Products and Shieldwerx offer turnkey project support, combining material supply with installation services. Thermo Fisher Scientific Inc. and Triton Systems, LLC. contribute complementary analytical and engineering expertise, ensuring adherence to rigorous testing standards. This mosaic of competitors highlights the drive toward turnkey solutions, supply chain integration, and continuous product innovation as key differentiators in a maturing market.
This comprehensive research report delivers an in-depth overview of the principal market players in the Industrial Grade Borated Polyethylene Materials market, evaluating their market share, strategic initiatives, and competitive positioning to illuminate the factors shaping the competitive landscape.
- A-Radiation Shielding Systems
- Advanza Materials
- Alro Plastics
- Amar Industries
- Boral Material Technologies
- Carmel Industries
- Ecomass Technologies
- Eljen Technology
- Emco Industrial Plastics
- Modern Plastics, Inc.
- Nuclear Lead Co., Inc.
- Paragon Medical
- QMP Racing Products
- Radiation Protection Products
- Shieldwerx
- Thermo Fisher Scientific Inc.
- Triton Systems, LLC.
Actionable Recommendations for Industry Leaders
Industry leaders should prioritize investment in flexible manufacturing lines that accommodate both continuous extrusion and precision molding processes, ensuring rapid response to evolving end-user demands. Diversifying supply chains by establishing regional production hubs, particularly within the Americas and Asia-Pacific, will mitigate tariff-related risks and reduce logistics lead times. Engaging proactively with standards organizations to influence and anticipate changes in ASTM and ISO protocols will secure early-mover advantages in compliance-intensive applications.
Collaborative development agreements with equipment OEMs and research institutions can accelerate the introduction of advanced borated polyethylene formulations that offer enhanced thermal and impact resistance. Tailoring packaging solutions-from bulk shipments for large-scale industrial projects to custom configurations for sensitive medical components-will improve customer satisfaction and open new market niches. Implementing digital supply chain management tools, including real-time tracking and predictive demand forecasting, will optimize inventory turnover and minimize stockouts.
Embrace sustainability frameworks by integrating recycled polymers where feasible and reducing process waste through lean manufacturing techniques. Establish in-house training programs to upskill production and quality teams on best practices in radiation safety and material testing. Leverage digital twin simulations to predict performance under varying operational conditions, optimizing product design before physical prototyping. Additionally, negotiate long-term supply contracts for critical raw materials such as boron carbide to secure stable pricing and ensure uninterrupted production. By embedding sustainability and digital innovation within core strategies, organizations will not only enhance operational efficiency but also meet increasingly stringent ESG criteria, strengthening stakeholder trust and opening doors to new funding opportunities.
Explore AI-driven insights for the Industrial Grade Borated Polyethylene Materials market with ResearchAI on our online platform, providing deeper, data-backed market analysis.
Ask ResearchAI anything
World's First Innovative Al for Market Research
Conclusion and Strategic Outlook
The industrial grade borated polyethylene market is at a pivotal juncture, shaped by accelerated technological advances, evolving regulatory landscapes, and shifting trade policies. Detailed segmentation analysis reveals diverse growth pockets across product forms, density grades, and application domains, while regional insights underscore the importance of geographic agility. A review of leading suppliers highlights the competitive imperative to offer integrated solutions that combine material innovation with comprehensive service capabilities. As end-users demand higher performance, tighter tolerances, and rapid delivery, companies that can align manufacturing flexibility with rigorous quality assurance will differentiate themselves.
In sum, a strategic approach that balances investment in advanced processing technologies, proactive standards engagement, and adaptive supply chain configurations will be essential. By leveraging these insights, industry participants can navigate complex market dynamics and secure sustainable growth in an increasingly competitive environment.
This section provides a structured overview of the report, outlining key chapters and topics covered for easy reference in our Industrial Grade Borated Polyethylene Materials market comprehensive research report.
- Preface
- Research Methodology
- Executive Summary
- Market Overview
- Market Dynamics
- Market Insights
- Cumulative Impact of United States Tariffs 2025
- Industrial Grade Borated Polyethylene Materials Market, by Product Type
- Industrial Grade Borated Polyethylene Materials Market, by Density
- Industrial Grade Borated Polyethylene Materials Market, by Thickness
- Industrial Grade Borated Polyethylene Materials Market, by Application
- Industrial Grade Borated Polyethylene Materials Market, by Form
- Industrial Grade Borated Polyethylene Materials Market, by End-User Industry
- Industrial Grade Borated Polyethylene Materials Market, by Manufacturing Process
- Industrial Grade Borated Polyethylene Materials Market, by Property
- Industrial Grade Borated Polyethylene Materials Market, by Testing Standards
- Industrial Grade Borated Polyethylene Materials Market, by Packaging
- Americas Industrial Grade Borated Polyethylene Materials Market
- Asia-Pacific Industrial Grade Borated Polyethylene Materials Market
- Europe, Middle East & Africa Industrial Grade Borated Polyethylene Materials Market
- Competitive Landscape
- ResearchAI
- ResearchStatistics
- ResearchContacts
- ResearchArticles
- Appendix
- List of Figures [Total: 36]
- List of Tables [Total: 640 ]
Connect with Ketan Rohom for In-Depth Market Intelligence
To gain full access to the comprehensive market research report on industrial grade borated polyethylene materials and unlock detailed insights, contact Ketan Rohom, Associate Director, Sales & Marketing. He will guide you through the report’s actionable data, segmentation breakdowns, and regional analyses to support strategic decision-making. Engage now to secure a tailored solution that drives growth and competitive advantage.
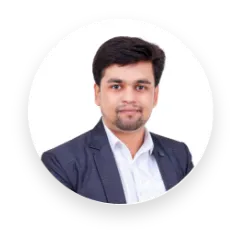
- When do I get the report?
- In what format does this report get delivered to me?
- How long has 360iResearch been around?
- What if I have a question about your reports?
- Can I share this report with my team?
- Can I use your research in my presentation?