Introduction to the Evolution and Importance of Grinding & Polishing Robotics
The industrial grinding and polishing robotics sector has evolved into a cornerstone of modern manufacturing, driven by the relentless demand for precision surface finishing, higher throughput, and cost reduction. As production lines across aerospace, automotive, consumer electronics, and heavy machinery fabrication industries strive for tighter tolerances and flawless aesthetics, robotics solutions have rapidly matured to meet these exacting standards. Manufacturers today leverage advanced CNC platforms, multi-axis robots, and cobot integrations to automate repetitive tasks, eliminate human error, and deliver consistent quality at scale.
Technological breakthroughs in sensor fusion, robotic vision, and artificial intelligence have further accelerated this transition, enabling real-time process adjustments and self-optimizing control loops. Simultaneously, rising labor costs, workforce shortages, and stringent environmental regulations have heightened the urgency for flexible automation. This introduction outlines the key forces propelling the grinding and polishing robot landscape, setting the stage for an in-depth exploration of market shifts, policy impacts, segmentation intelligence, regional dynamics, competitive positioning, and strategic guidance for industry leaders.
Transformative Technology and Operational Shifts Driving Market Evolution
Automation in grinding and polishing has undergone transformative shifts that redefine precision, productivity, and profitability. First, the integration of artificial intelligence with deep learning algorithms has empowered robots to identify real-time surface anomalies, dynamically adjust tool paths, and optimize force application. At the same time, sensor fusion advancements-combining force, vibration, and thermal data-have driven smarter contact management, reducing scrap rates and extending tool life.
Another critical shift is the emergence of hybrid robots that blend grinding and polishing functionalities within a single cell. Adaptive interfaces now allow seamless transitions between coarse material removal and fine surface finishing without manual intervention. In parallel, remote monitoring and real-time analytics platforms have enabled offsite experts to oversee production lines and prescribe adjustments, thereby minimizing downtime and accelerating trouble-shooting.
Operational paradigms have also evolved from batch processing toward continuous, unmanned runs supported by predictive maintenance schedules. Manufacturers are weaving these innovations into aerospace beam polishers, EV battery pack surface treatments, and consumer electronics micro-finishing stations. These cumulative shifts highlight how cutting-edge robotics ecosystems are reshaping the standards for quality, flexibility, and cost-efficiency in surface engineering.
Cumulative Impact of New United States Tariffs on 2025 Automation Costs
The implementation of new United States tariffs in 2025 has created a layered cost structure for imported robotic cells, spare parts, and critical electronic components. Tariff hikes on sensors, drive motors, and AI accelerators have driven OEMs and system integrators to reassess supply chain strategies, accelerating investments in domestic manufacturing and localized sourcing. This push has, in turn, prompted component suppliers to establish or expand North American production lines, mitigating the impact of elevated duties.
For end users, selective tariff pass-through has resulted in modest price increases for turnkey grinding and polishing cells, prompting procurement teams to negotiate long-term service contracts and take-or-pay agreements. Conversely, U.S.-based automation providers have capitalized on duty differentials by offering retrofit kits and remanufactured units that circumvent new levy thresholds. Overall, while short-term cost pressures have been felt, the tariff environment is catalyzing supply chain resilience and fostering a competitive onshore ecosystem for advanced surface finishing robotics.
Key Segmentation Insights Across Type, Application, Material, Operation, and Integration
Comprehensive segmentation analysis reveals nuanced growth drivers, adoption patterns, and competitive landscapes. When examining robot type, standalone grinding robots address bulk material removal for metals and composites, hybrid robots equipped with adaptive interface modules and dual-function tooling seamlessly switch between roughing and polishing, and dedicated polishing robots excel at achieving mirror-like finishes on polymers and ceramics.
Application area segmentation highlights aerospace production’s exacting requirements for turbine blade and structural component polishing, automotive manufacturing’s dual focus on electric vehicle battery modules and combustion engine blocks, consumer electronics assembly’s demand for uniform microfinishing on housings, and heavy machinery fabrication’s need for robust surge polishing on steel and aluminum castings.
Material-processed breakdown underscores wear behavior and cycle time variations across ceramics, advanced composites, polymers, and metals-particularly aluminum alloys prized for weight savings and high-strength steel for durability. Operation mode segmentation spans automated scheduling strategies underpinned by predictive maintenance and real-time monitoring, batch processing workflows that maximize tool usage, continuous operation cells designed for 24/7 throughput, and manual override options reserved for bespoke prototypes.
Finally, technological integration spans artificial intelligence incorporating machine learning and deep learning engines, remote monitoring platforms facilitating offsite diagnostics, robotic vision systems achieving sub-micron alignment tolerances, and sensor fusion arrays orchestrating force, acoustic, and temperature feedback loops. These segmentation lenses unveil strategic entry points, tailored value propositions, and cross-industry scaling opportunities.
This comprehensive research report categorizes the Industrial Grinding & Polishing Robots market into clearly defined segments, providing a detailed analysis of emerging trends and precise revenue forecasts to support strategic decision-making.
- Robot Type
- Application Area
- Material Processed
- Operation Mode
- Technological Integration
Key Regional Insights Shaping Adoption Patterns and Investment Priorities
Regional dynamics underscore how geographic factors shape adoption trajectories, investment priorities, and competitive intensity. In the Americas, aggressive electrification of the automotive sector and reshoring incentives have fueled demand for automated grinding and polishing lines, particularly within U.S. and Canadian EV battery assembly hubs. Mexico’s integrated manufacturing corridors benefit from nearshore advantages and evolving content requirements.
Across Europe, Middle East & Africa, stringent surface finish standards in aerospace composites and luxury automotive interiors have heightened interest in high-precision polishing cells. European Union incentives for Industry 4.0 modernization and Middle Eastern investment in downstream petrochemical fabrication further elevate demand. African metal fabrication workshops are beginning to adopt compact, cobot-enabled grinding stations for local industrialization initiatives.
Meanwhile, Asia-Pacific leads in consumer electronics volume, with major contract manufacturers in China, South Korea and Taiwan deploying continuous-operation polishing robots to meet smartphone, semiconductor wafer, and display panel quality thresholds. Japan’s emphasis on reliability and precision has driven upgrades to sensor fusion and robotic vision platforms. Additionally, Southeast Asian foundries and heavy machinery fabricators are gradually integrating automated scheduling solutions to optimize tool utilization and reduce scrap rates.
This comprehensive research report examines key regions that drive the evolution of the Industrial Grinding & Polishing Robots market, offering deep insights into regional trends, growth factors, and industry developments that are influencing market performance.
- Americas
- Asia-Pacific
- Europe, Middle East & Africa
Key Company Insights Revealing Innovation, Partnerships, and Competitive Dynamics
The competitive landscape features established incumbents and emerging innovators vying for leadership in grinding and polishing automation. ABB Robotics Ltd and Fanuc Corporation continue to set benchmarks in multi-axis, high-speed polishing modules, while Kawasaki Heavy Industries Robotics and Yaskawa Electric Corporation expand their footprint with sensor-driven force control. KUKA AG and Siemens Industrial Robots leverage their industrial ecosystems to integrate deep learning algorithms into cell controllers.
Bosch Robotics, Comau Robotics, and Dürr AG emphasize turnkey hybrid workstations combining abrasive and buffing functions, whereas Epson Robots and Universal Robots A/S specialize in collaborative robot deployments for light-duty polishing in electronics assembly. Mitsubishi Electric Automation and Rockwell Automation Robotics invest heavily in real-time monitoring platforms and predictive maintenance dashboards, and Omron Adept Technologies focuses on adaptive interface innovations.
Specialty players such as Innovative Surface Robotics Inc., PoliGrind Automation Inc., OptiFinish Robotics Inc., RoboSurface Inc. and Robotic Finishing Solutions Ltd. refine niche polishing routines for medical devices, optics, and precision components. Precision Finishing Technologies, Inc., UltraFinish Automation Pvt. Ltd., MachinaRobotics Corporation and SurfaceTech Robotics champion sensor fusion suites that unify force, acoustic emission and thermal imaging data. Meanwhile, Advanced Robotic Systems LLC, Haas Automation Robotics, Schunk GmbH & Co. KG, Surface ProTech Robotics and Rockwell Automation Robotics maintain strong alliances across automotive, heavy machinery and aerospace segments. This diverse ecosystem underscores a dynamic market where scale, specialization, and technology depth drive competitive advantage.
This comprehensive research report delivers an in-depth overview of the principal market players in the Industrial Grinding & Polishing Robots market, evaluating their market share, strategic initiatives, and competitive positioning to illuminate the factors shaping the competitive landscape.
- ABB Robotics Ltd
- Advanced Robotic Systems LLC
- Bosch Robotics
- Comau Robotics
- Denso Robotics
- Dürr AG
- Epson Robots
- Fanuc Corporation
- Haas Automation Robotics
- Innovative Surface Robotics Inc.
- Kawasaki Heavy Industries Robotics
- KUKA AG
- MachinaRobotics Corporation
- Mitsubishi Electric Automation
- Omron Adept Technologies
- OptiFinish Robotics Inc.
- PoliGrind Automation Inc.
- Precision Finishing Technologies, Inc.
- RoboGrind Technologies
- RoboSurface Inc.
- Robotic Finishing Solutions Ltd.
- Rockwell Automation Robotics
- Schunk GmbH & Co. KG
- Siemens Industrial Robots
- Stäubli Robotics Inc.
- Surface ProTech Robotics
- SurfaceTech Robotics
- UltraFinish Automation Pvt. Ltd.
- Universal Robots A/S
- Yaskawa Electric Corporation
Actionable Recommendations for Industry Leaders to Drive Growth and Resilience
To capitalize on emerging opportunities and mitigate risks, industry leaders should adopt a multi-pronged strategy. First, prioritize integration of artificial intelligence and sensor fusion capabilities to enhance process adaptability and yield reduction; collaborating with data scientists and systems integrators will accelerate deployments. Second, diversify supply chains by forming strategic partnerships with regional component manufacturers to buffer against further tariff escalations and logistics disruptions.
Third, develop modular hybrid robot platforms that support both grinding and polishing functions with quick-change interfaces to serve automotive, aerospace, and electronics clients with minimal downtime. Fourth, invest in remote monitoring and predictive maintenance infrastructure to extend uptime, ensure compliance with stringent quality standards, and enable remote support services. Fifth, pursue targeted M&A or strategic alliances with niche specialists in micro-finishing, deep learning software, and advanced abrasives to round out end-to-end offering portfolios.
Finally, maintain agility by continuously evaluating regulatory landscapes, aligning R&D roadmaps with emerging material trends, and deploying pilot lines in key regions to validate new technologies under real-world conditions. These actionable steps will position leaders to drive market share growth, accelerate innovation cycles, and deliver superior total cost of ownership for end users.
Explore AI-driven insights for the Industrial Grinding & Polishing Robots market with ResearchAI on our online platform, providing deeper, data-backed market analysis.
Ask ResearchAI anything
World's First Innovative Al for Market Research
Conclusion: Navigating Technological and Regulatory Inflection Points
The industrial grinding and polishing robotics market is at a pivotal juncture, where technological innovation intersects with evolving regulatory and trade environments. As adoption accelerates across key verticals-from electric vehicle battery modules to aerospace components and consumer electronics-manufacturers must balance investments in advanced automation with strategic supply chain resilience.
By synthesizing insights across segmentation, regional dynamics, tariff impacts, and competitive landscapes, this analysis highlights critical inflection points for growth. Market leaders that harness artificial intelligence, sensor fusion, and hybrid robot architectures will gain a distinct advantage, while those who proactively address policy shifts and supply chain vulnerabilities will secure long-term stability.
Ultimately, success hinges on an integrated approach that aligns technology roadmaps, strategic partnerships, and operational excellence. By navigating these dynamics with agility and foresight, organizations can achieve superior surface finishing performance, cost optimization, and sustainable competitive positioning.
This section provides a structured overview of the report, outlining key chapters and topics covered for easy reference in our Industrial Grinding & Polishing Robots market comprehensive research report.
- Preface
- Research Methodology
- Executive Summary
- Market Overview
- Market Dynamics
- Market Insights
- Cumulative Impact of United States Tariffs 2025
- Industrial Grinding & Polishing Robots Market, by Robot Type
- Industrial Grinding & Polishing Robots Market, by Application Area
- Industrial Grinding & Polishing Robots Market, by Material Processed
- Industrial Grinding & Polishing Robots Market, by Operation Mode
- Industrial Grinding & Polishing Robots Market, by Technological Integration
- Americas Industrial Grinding & Polishing Robots Market
- Asia-Pacific Industrial Grinding & Polishing Robots Market
- Europe, Middle East & Africa Industrial Grinding & Polishing Robots Market
- Competitive Landscape
- ResearchAI
- ResearchStatistics
- ResearchContacts
- ResearchArticles
- Appendix
- List of Figures [Total: 26]
- List of Tables [Total: 460 ]
Unlock Comprehensive Market Insights by Contacting Ketan Rohom
For a deeper, data-driven exploration of market dynamics, segmentation nuances, and competitive benchmarks in the grinding and polishing robotics domain, connect with Ketan Rohom, Associate Director, Sales & Marketing. Equip your executive team and engineering leads with actionable intelligence to outpace competitors and capitalize on emerging growth corridors. Reach out today to secure comprehensive insights and tailor your strategic road map for long-term success.
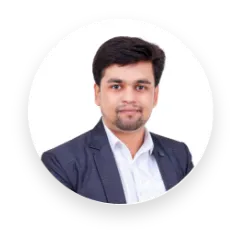
- When do I get the report?
- In what format does this report get delivered to me?
- How long has 360iResearch been around?
- What if I have a question about your reports?
- Can I share this report with my team?
- Can I use your research in my presentation?