The Industrial Robotic Arms Market size was estimated at USD 20.63 billion in 2024 and expected to reach USD 23.30 billion in 2025, at a CAGR 12.81% to reach USD 42.53 billion by 2030.

Industrial Robotic Arms Redefining Modern Manufacturing
Industrial robotic arms have emerged as indispensable assets across modern manufacturing environments, driving unprecedented gains in productivity and precision. Over the last decade, their adoption has accelerated as manufacturers strive to meet complex production demands, enhance product quality, and reduce operational costs. The integration of robotics into assembly lines and material handling systems illustrates a fundamental shift in how goods are produced, from high-volume commodity items to bespoke, high-complexity components. This evolution is anchored by breakthroughs in control systems, sensor technology, and human-machine interfaces that empower robotic arms to operate with remarkable speed and adaptability.
With global supply chains under constant pressure to deliver agility and resiliency, the demand for flexible automation solutions continues to rise. In particular, collaborative robots, or cobots, have unlocked new use cases by safely interacting with human operators without the need for extensive safety fencing. This human-robot partnership model amplifies the capabilities of production teams and facilitates greater customization in manufacturing workflows. Moreover, the convergence of robotics with data analytics and cloud-based platforms enables real-time performance monitoring and predictive maintenance, ensuring uptime remains a strategic priority.
As markets embrace digital transformation imperatives, industrial robotic arms are no longer confined to traditional heavy-industry environments. From electronics assembly to food and beverage packaging, manufacturers seek to harness robotic precision and repeatability across diverse end-user segments. The result is a dynamic competitive landscape in which companies that invest in advanced robotic capabilities can achieve cost leadership, accelerate time-to-market, and respond swiftly to evolving customer requirements. This introduction outlines the critical role industrial robotic arms play in shaping the future of manufacturing excellence.
Emerging Technologies Catalyzing Next-Generation Robotics
The industrial robotics landscape is undergoing a paradigm shift, driven by the rapid maturation of artificial intelligence, advanced sensor suites, and collaborative design philosophies. As manufacturers transition from rigid, single-task robots to versatile systems capable of dynamic path planning, agility has become the defining characteristic of next-generation robotic arms. The rise of edge computing and AI-enabled vision systems allows robots to interpret their environments, detect anomalies, and adjust operations on the fly. This autonomy reduces downtime and degrades reliance on fixed programming, unlocking more complex applications in high-mix, low-volume production.
Concurrently, sustainability considerations are reshaping investment decisions. Energy-efficient motors, regenerative braking systems, and modular constructions minimize the environmental footprint of robotic deployments. These eco-friendly designs not only align with corporate social responsibility targets but also drive down total cost of ownership. The increasing prevalence of digital twin technology further streamlines automation rollouts by simulating workflows, optimizing cell layouts, and validating process changes virtually, thereby accelerating implementation cycles.
Workforce dynamics are also evolving in tandem with robotic capabilities. Upskilling initiatives and human-robot collaboration frameworks empower technicians and engineers to focus on higher-value tasks such as process optimization and quality assurance. As a result, the integration of industrial robotic arms is not merely a matter of capital expenditure; it is a strategic lever that transforms operational models, enhances labor productivity, and fosters innovation across the manufacturing enterprise.
Navigating Trade Barriers in a Tariff-Driven Environment
The imposition of new U.S. tariffs on imported robotic arms in 2025 has prompted a comprehensive reassessment of global supply chains. By increasing the cost basis of systems sourced from traditional manufacturing hubs in Asia and Europe, these trade measures have introduced material price volatility and disrupted lead-time predictions. Organizations that once relied on low-cost, high-volume imports now face pressure to absorb additional duties or pass them onto end users, potentially dampening demand for advanced automation solutions.
In response, a growing cohort of manufacturers is accelerating the localization of robotic arm production. Regional production facilities are being established in the Americas to circumvent tariff hurdles and strengthen domestic supply networks. At the same time, tier-one suppliers are diversifying their sourcing strategies, forging partnerships with original equipment manufacturers (OEMs) in duty-free jurisdictions. These strategic pivots not only mitigate financial exposure to tariff fluctuations but also contribute to enhanced supply chain resilience in the face of geopolitical uncertainty.
Moreover, the tariff landscape has spurred dialogue around policy advocacy and bilateral trade negotiations, as industry stakeholders seek relief measures and clarity on duty classifications. Companies with established lobbying channels and data-driven market intelligence are better positioned to influence trade frameworks and secure exemptions for critical automation components. Looking ahead, the cumulative impact of these tariffs is reshaping procurement strategies, fostering innovation in domestic manufacturing, and reinforcing the imperative for agile sourcing models.
Deep Dive into Market Segmentation Nuances
When examining the industrial robotic arms market through the lens of robot type, articulated solutions lead with versatile multi-axis configurations that excel in arc welding and complex assembly tasks. Cartesian robots maintain dominance in linear pick-and-place operations, particularly for high-precision electronics manufacturing. Collaborative arms, with their integrated safety features, have unlocked new opportunities in small-batch production and manual assistance roles. Meanwhile, delta and SCARA systems continue to hold strategic niches in high-speed material handling and precision insertion operations, respectively, driven by their lightweight construction and swift cycle times.
Application-based dynamics reveal that assembly processes maintain the largest concentration of robot usage, attributable to robust stability requirements and repeatability metrics. Machine tending automation follows closely, offering labor redeployment benefits in CNC machining and injection molding cells. Material handling has evolved into a multifaceted domain encompassing packaging, palletizing, pick-and-place, and sorting workflows, where robotic arms deliver consistent throughput and reduced error rates. Painting applications harness robotics for uniform coatings and lower environmental emissions, while welding segments-comprising arc, laser, and spot methodologies-leverage enhanced motion control to meet stringent automotive and heavy-industry standards.
Across end-user industries, the automotive sector remains the primary growth engine, supported by electrification trends and assembly line modernization. The electronics industry demands ultra-precision and miniaturization capabilities for semiconductor handling and circuit board assembly. In the food and beverage segment, hygiene compliance and rapid changeover requirements have spurred the adoption of stainless-steel robots and easy-clean designs. Logistics and warehousing operations capitalize on robotic loading and unloading to streamline order fulfillment, while general manufacturing continues to integrate automation as a means to address labor shortages and maintain competitive parity.
This comprehensive research report categorizes the Industrial Robotic Arms market into clearly defined segments, providing a detailed analysis of emerging trends and precise revenue forecasts to support strategic decision-making.
- Robot Type
- Application
- End User Industry
Regional Dynamics Shaping Robotic Automation Adoption
The Americas region benefits from strong domestic manufacturing infrastructures in the United States, Canada, and Mexico, where automation investment is spurred by reshoring initiatives and incentives for advanced technology adoption. Latin American markets are gradually embracing robotic arms in automotive components and beverage production, driven by growing middle-class consumption and infrastructure upgrades.
In Europe, Middle East and Africa, a blend of established industrial powerhouses and emerging economies defines the landscape. Western European nations leverage high-precision robotics in premium automotive and aerospace applications, while Eastern European facilities focus on cost-competitive assembly operations. Middle Eastern and North African markets are increasingly investing in food processing automation to bolster food security, supported by government modernization agendas.
The Asia-Pacific region remains the largest consumer of industrial robotic arms, underpinned by manufacturing giants in China, Japan, and South Korea. Rapid industrialization, robust electronics ecosystems, and government-led smart factory programs continue to drive automation uptake. Southeast Asian countries are following suit, with Malaysia and Thailand emerging as regional hubs for automotive and electronics production, seeking to upgrade legacy assembly lines with collaborative and articulated robot deployments.
This comprehensive research report examines key regions that drive the evolution of the Industrial Robotic Arms market, offering deep insights into regional trends, growth factors, and industry developments that are influencing market performance.
- Americas
- Europe, Middle East & Africa
- Asia-Pacific
Competitive Landscape of Key Robotics Providers
Global automation leaders have continued to refine their portfolios through targeted R&D investments and strategic alliances. Established players with broad product lines dominate high-end, precision-centric segments, while agile newcomers focus on lightweight, collaborative solutions. Partnerships between robotics manufacturers and software innovators have accelerated the integration of advanced control algorithms and user-friendly programming interfaces. This convergence has lowered the barrier to entry for mid-sized manufacturers seeking turnkey automation cells.
Leading companies are also expanding service offerings, embedding connectivity modules for remote monitoring, and leveraging subscription-based maintenance contracts. These value-added services create recurring revenue streams and reinforce long-term customer relationships. At the same time, open-architecture strategies are gaining traction, enabling greater interoperability between robotic arms and third-party systems, fostering an ecosystem approach to automation.
Mergers and acquisitions remain a key growth lever, as firms seek to augment their geographic footprints and access complementary technology stacks. Smaller, specialized robotics providers are being absorbed by larger conglomerates, bringing niche capabilities-such as advanced vision systems and end-of-arm tooling-into mainstream product portfolios. This dynamic realignment has intensified competitive differentiation, with top companies vying to deliver the most comprehensive, vertically integrated automation solutions.
This comprehensive research report delivers an in-depth overview of the principal market players in the Industrial Robotic Arms market, evaluating their market share, strategic initiatives, and competitive positioning to illuminate the factors shaping the competitive landscape.
- FANUC Corporation
- Yaskawa Electric Corporation
- ABB Ltd.
- KUKA AG
- Nachi-Fujikoshi Corp.
- DENSO Corporation
- Kawasaki Heavy Industries, Ltd.
- Mitsubishi Electric Corporation
- Seiko Epson Corporation
- Universal Robots A/S
Strategic Blueprint for Robotics-Driven Growth
Industry leaders should prioritize the integration of AI-driven vision and motion control systems to unlock new application frontiers and boost operational efficiency. By aligning automation strategies with digital transformation roadmaps, organizations can ensure that robotic deployments deliver both short-term ROI and long-term scalability. Furthermore, investing in workforce development programs will be instrumental in cultivating the hybrid skill sets required for programming, maintenance, and process optimization in automated environments.
Supply chain diversification is equally critical; developing multi-regional sourcing channels and establishing localized assembly hubs will mitigate exposure to trade disruptions and tariff volatility. Collaborative partnerships with technology providers and academic institutions can foster joint innovation initiatives, accelerating the commercialization of emerging robotic capabilities. Additionally, embedding sustainability metrics into robotic investment decisions-through energy-efficient system selections and circular economy practices-will enhance corporate responsibility credentials and unlock potential incentives.
Ultimately, organizations that embrace a holistic approach to automation-encompassing technology, talent, and supply chain resilience-will be best positioned to navigate market dynamics. By continuously evaluating performance data, refining deployment strategies, and fostering a culture of innovation, industry leaders can transform robotic arms from isolated tools into strategic assets that drive lasting competitive advantage.
Robust Methodology Underpinning Key Insights
This analysis is grounded in a rigorous research framework that synthesizes primary and secondary data sources. Primary research involved in-depth interviews with senior automation engineers, plant managers, and procurement executives across key geographies. These qualitative insights were complemented by questionnaires and structured surveys to validate technology adoption patterns, procurement drivers, and implementation challenges.
Secondary research encompassed a comprehensive review of trade publications, regulatory filings, patent databases, and financial disclosures from leading robotics manufacturers. Industry association reports and government census data provided macroeconomic context, while technology white papers and academic journals informed the assessment of emerging innovations. Triangulation methodology was employed to cross-verify data points, ensuring the accuracy and reliability of findings.
Market segmentation and regional analyses were conducted using a bottom-up approach, integrating shipment volumes, installed base metrics, and revenue disclosures. Segmentation insights were refined through iterative feedback loops with subject-matter experts, guaranteeing that the categorization reflects real-world application nuances. The research process adhered to strict quality control protocols, with multiple review stages to eliminate biases and maintain methodological transparency.
Explore AI-driven insights for the Industrial Robotic Arms market with ResearchAI on our online platform, providing deeper, data-backed market analysis.
Ask ResearchAI anything
World's First Innovative Al for Market Research
Harnessing Robotics for Sustainable Operational Excellence
As industrial robotic arms continue to permeate every facet of manufacturing, their role in advancing efficiency, flexibility, and quality has never been clearer. The synthesis of technological breakthroughs-ranging from AI-augmented control systems to collaborative safety features-marks a decisive turning point in automation strategy. Coupled with evolving trade policies and regional industrial initiatives, these developments shape a market defined by agility and resilience.
The segmentation analysis underscores the diverse application requirements across robot types, industries, and end users. Each use case presents unique challenges and value propositions, reinforcing the importance of tailored automation solutions. Regional insights further reveal how geopolitical factors and infrastructure maturity influence adoption trajectories, while the competitive landscape highlights the ongoing quest for differentiation through innovation and service excellence.
Ultimately, success in the era of robotic automation mandates a cohesive approach that aligns technology investment with organizational capabilities, supply chain strategies, and sustainability objectives. Stakeholders must remain vigilant, continuously reexamining their automation portfolios and forging strategic alliances to capture the full potential of industrial robotic arms.
This section provides a structured overview of the report, outlining key chapters and topics covered for easy reference in our Industrial Robotic Arms market comprehensive research report.
- Preface
- Research Methodology
- Executive Summary
- Market Overview
- Market Dynamics
- Market Insights
- Cumulative Impact of United States Tariffs 2025
- Industrial Robotic Arms Market, by Robot Type
- Industrial Robotic Arms Market, by Application
- Industrial Robotic Arms Market, by End User Industry
- Americas Industrial Robotic Arms Market
- Europe, Middle East & Africa Industrial Robotic Arms Market
- Asia-Pacific Industrial Robotic Arms Market
- Competitive Landscape
- ResearchAI
- ResearchStatistics
- ResearchContacts
- ResearchArticles
- Appendix
- List of Figures [Total: 22]
- List of Tables [Total: 243 ]
Secure Your Competitive Edge with Expert Market Intelligence
To explore how the Industrial Robotic Arms market can empower your organization’s growth strategy, reach out to Ketan Rohom, Associate Director of Sales & Marketing, for a personalized consultation. Ketan Rohom can guide you through bespoke research insights, tailored data packages, and strategic roadmaps that align with your enterprise objectives. Engage directly to uncover deeper market intelligence, optimize your automation investments, and stay ahead of competitive shifts. Contact Ketan Rohom today to secure your comprehensive market research report and leverage critical findings that will drive informed decision-making in the era of robotic automation.
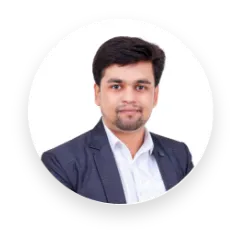
- How big is the Industrial Robotic Arms Market?
- What is the Industrial Robotic Arms Market growth?
- When do I get the report?
- In what format does this report get delivered to me?
- How long has 360iResearch been around?
- What if I have a question about your reports?
- Can I share this report with my team?
- Can I use your research in my presentation?