The Industrial Tubes Market size was estimated at USD 715.42 million in 2024 and expected to reach USD 765.75 million in 2025, at a CAGR 6.97% to reach USD 1,072.28 million by 2030.

Exploring the Industrial Tubes Sector’s Strategic Significance
The industrial tubes sector has emerged as a cornerstone of modern infrastructure and manufacturing, underpinned by decades of innovation in materials science and process engineering. As global supply chains have evolved, tubes have become essential in applications ranging from fluid transport in energy installations to structural reinforcement in construction. Today’s stakeholders confront a complex blend of drivers-including rapid urbanization, heightened environmental regulations, and the push for energy efficiency-that shape demand for advanced tube solutions.
This introduction unpacks the sector’s multifaceted nature, highlighting how diverse alloys, polymers and fabrication techniques converge to meet stringent performance requirements. It explores the rising emphasis on corrosion resistance in chemical facilities, the demand for lightweight aluminum systems in transportation, and the pursuit of seamless production methods to optimize mechanical integrity. By setting the stage with this broad perspective, decision-makers will appreciate the strategic intersections of technology, policy and end-use imperatives that define the sector’s trajectory.
Unveiling the Forces Driving Profound Industry Evolution
The landscape of industrial tubes is experiencing transformative shifts driven by converging forces in technology and regulation. Advanced material formulations are enabling tubes to withstand extreme temperatures and corrosive environments, unlocking new applications in hydrogen fuel networks and high-efficiency heat exchangers. Concurrently, the rise of additive manufacturing and automated welding systems is reshaping production paradigms, accelerating throughput while minimizing defects.
Simultaneously, evolving regulatory frameworks around emissions and product safety compel manufacturers to adopt eco-friendly alloys and implement rigorous quality protocols. Environmental considerations now influence material selection, spurring research into recyclable polymers and low-carbon steel variants. On the demand side, the integration of digital twins and real-time monitoring has elevated performance standards, prompting tube producers to embed sensors and smart coatings. These dynamics collectively herald a shift from commodity supply toward high-value, application-specific solutions that align with the emerging needs of energy, infrastructure and mobility sectors.
Assessing the 2025 Tariff Impact on Supply Chains and Competitiveness
United States tariffs introduced in 2025 have recalibrated global supply chains for industrial tubes, altering trade flows and competitive positioning. The increased duties on key imports have incentivized near-shore manufacturing investments, as producers seek to mitigate cost pressures and maintain delivery reliability. In response, several domestic facilities have expanded capacity, focusing on high-end stainless and alloy steel products where import costs pose the greatest challenge.
At the same time, the ripple effects of these tariffs have reached upstream suppliers, prompting raw material providers to diversify sourcing and renegotiate long-term agreements. As traditional export markets adjust to the new cost structure, producers in the Americas and Asia-Pacific have reoriented their sales strategies, emphasizing value-added metallurgical services and rapid turnarounds. While some sectors face transient supply constraints, the overall environment has spurred innovation in production efficiency and logistical resilience. Ultimately, the tariff landscape of 2025 has become a catalyst for redefined partnerships and more self-reliant manufacturing models.
Extracting Strategic Value from Segmentation Dynamics
Drawing insights from material categories reveals that aluminum retains its leadership due to its weight-to-strength ratio, with alloyed variants catering to aerospace and automotive sectors and pure grades favored for corrosion-sensitive applications. Copper continues to secure niches in electrical assemblies, while plastic tubes expand in chemical handling and water treatment. In the realm of ferrous materials, austenitic stainless steel dominates corrosion-resistant demands and ferritic grades deliver cost-effective structural performance. Alloy steel emerges where enhanced tensile properties are critical, and carbon steel sustains its ubiquity in general-purpose infrastructure.
Examining end-use industries underscores the prominence of automotive and chemical processing, with construction projects deploying tubes across commercial, infrastructure and residential developments. Energy companies leverage tubes in upstream, midstream and downstream operations, while power generation utilities focus on high-temperature exchangers. Manufacturing techniques divide between seamless approaches-through extrusion and rotary piercing-and welded methods such as electric fusion or resistance welding, each offering distinct advantages in throughput and dimensional precision. Applications span conveying systems for both gas and liquid substances, hydraulic and pneumatic controls, plus structural frameworks in diverse industrial settings. Finally, an array of cross-sectional shapes from rectangular to round and square ensures that design requirements across sectors can be optimally fulfilled.
This comprehensive research report categorizes the Industrial Tubes market into clearly defined segments, providing a detailed analysis of emerging trends and precise revenue forecasts to support strategic decision-making.
- Material
- End Use Industry
- Manufacturing Technique
- Application
- Shape
Illuminating Regional Strengths and Emerging Opportunities
Regional analysis reveals that the Americas maintain strong vertical integration, with North American facilities advancing in high-purity stainless and alloy steels while Latin American markets grow around infrastructure and energy transport tubes. Innovations in precision welding and value-added finishing services have strengthened the region’s position in critical applications for oil and gas.
In Europe, Middle East & Africa, stringent emission standards and ambitious renewable energy targets drive demand for specialized tubing solutions. Manufacturers leverage advanced metallurgy to meet regulatory benchmarks, particularly in power generation and chemical processing plants. Growing construction initiatives across Middle Eastern nations further elevate requirements for durable structural tubes.
The Asia-Pacific region stands out for rapid capacity expansion and cost-competitive production, particularly in seamless and welded steel tubes. Investments in automation and digital integration have yielded significant productivity gains, supporting surges in end-use industries from automotive manufacturing in East Asia to large-scale infrastructure projects in South Asia and Australia.
This comprehensive research report examines key regions that drive the evolution of the Industrial Tubes market, offering deep insights into regional trends, growth factors, and industry developments that are influencing market performance.
- Americas
- Europe, Middle East & Africa
- Asia-Pacific
Profiling Industry Leaders’ Strategies for Sustainable Growth
Leading companies across the industrial tubes domain are forging strategic alliances and investing in cutting-edge technologies to secure their market positions. Several global manufacturers have established centers of excellence focused on corrosion-resistant alloys and advanced inspection protocols. Simultaneously, mid-tier producers are differentiating through rapid customization services, offering expedited delivery and tailored metallurgical testing.
Collaborations between equipment suppliers and tube producers are enabling process innovations such as real-time weld monitoring and predictive maintenance platforms. This integration of digital solutions not only optimizes operational efficiency but also enhances product traceability from raw material to finished tube. Furthermore, certain players are expanding through targeted acquisitions in high-growth regions, aiming to capture opportunities presented by localized demand and shifting trade policies.
This comprehensive research report delivers an in-depth overview of the principal market players in the Industrial Tubes market, evaluating their market share, strategic initiatives, and competitive positioning to illuminate the factors shaping the competitive landscape.
- Tenaris S.A.
- Vallourec S.A.
- TMK Steel Limited
- Salzgitter AG
- ArcelorMittal S.A.
- Nippon Steel Corporation
- JFE Steel Corporation
- United States Steel Corporation
- Welspun Corp Limited
Actionable Strategies to Navigate Disruption and Drive Growth
Industry leaders should prioritize investments in advanced fabrication capabilities, including automated welding systems and integrated quality assurance technologies, to sustain competitive advantage. Strengthening partnerships with raw material suppliers can secure consistent feedstock quality and cost stability, while co-developing eco-friendly alloy formulations aligns product portfolios with tightening environmental standards.
To capitalize on regional shifts, expanding localized production footprints near key end-use markets-particularly in the Americas and Asia-Pacific-will minimize tariff exposure and enhance responsiveness. Embracing digital platforms for supply chain visibility and predictive analytics can improve decision-making and reduce downtime risks. On the commercial front, offering modular tube solutions with embedded monitoring features will create value-added propositions that resonate with customers’ performance and sustainability objectives.
Methodological Rigor Behind the Comprehensive Analysis
This research combined primary interviews with industry executives, plant managers and technical specialists to gather qualitative insights on emerging trends and operational challenges. Secondary sources such as trade journals, regulatory filings and academic publications were also examined to validate market dynamics and technological developments.
The methodology employed a rigorous cross-validation process, integrating process flow analyses, material performance reviews and comparative regional assessments. Trade data and customs records were analyzed to assess tariff impacts, while case studies from leading manufacturing facilities provided empirical evidence of best practices. Insights were synthesized to ensure coherence and relevance, delivering a comprehensive overview of the industrial tubes landscape without relying on projections or speculative forecasts.
Explore AI-driven insights for the Industrial Tubes market with ResearchAI on our online platform, providing deeper, data-backed market analysis.
Ask ResearchAI anything
World's First Innovative Al for Market Research
Navigating Complexity with Informed Strategic Focus
The evolving industrial tubes landscape presents both challenges and opportunities for stakeholders willing to adapt swiftly and strategically. Shifts in material innovation, regulatory pressures and regional trade policies underscore the need for agile manufacturing models and forward-looking partnerships.
By integrating the insights on segmentation, regional strengths and company strategies, decision-makers are positioned to navigate the complexities of the post-tariff environment. The convergence of digitalization, sustainability and performance optimization will define market leadership, rewarding those who proactively invest in technology and collaborative supply chain solutions.
This section provides a structured overview of the report, outlining key chapters and topics covered for easy reference in our Industrial Tubes market comprehensive research report.
- Preface
- Research Methodology
- Executive Summary
- Market Overview
- Market Dynamics
- Market Insights
- Cumulative Impact of United States Tariffs 2025
- Industrial Tubes Market, by Material
- Industrial Tubes Market, by End Use Industry
- Industrial Tubes Market, by Manufacturing Technique
- Industrial Tubes Market, by Application
- Industrial Tubes Market, by Shape
- Americas Industrial Tubes Market
- Europe, Middle East & Africa Industrial Tubes Market
- Asia-Pacific Industrial Tubes Market
- Competitive Landscape
- ResearchAI
- ResearchStatistics
- ResearchContacts
- ResearchArticles
- Appendix
- List of Figures [Total: 26]
- List of Tables [Total: 595 ]
Secure Your Strategic Edge with Expert Guidance
If you are ready to equip your leadership team with deep insights and gain a competitive advantage in the industrial tubes arena, reach out to Ketan Rohom, Associate Director, Sales & Marketing. He can guide you through tailored solutions to address your strategic priorities and connect you with the full report. Engage today to harness the detailed analysis, segment breakdowns, and actionable recommendations that will power your next phase of growth.
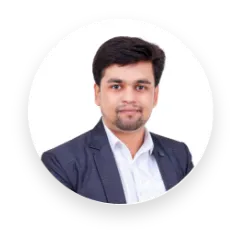
- How big is the Industrial Tubes Market?
- What is the Industrial Tubes Market growth?
- When do I get the report?
- In what format does this report get delivered to me?
- How long has 360iResearch been around?
- What if I have a question about your reports?
- Can I share this report with my team?
- Can I use your research in my presentation?