The Injection Molding Market size was estimated at USD 11.06 billion in 2024 and expected to reach USD 11.62 billion in 2025, at a CAGR 5.00% to reach USD 14.83 billion by 2030.

Setting the Stage for Injection Molding Dynamics
Injection molding stands at the heart of modern manufacturing, powering the creation of complex components across a spectrum of industries. This executive summary distills the essential findings of a rigorous market analysis that investigates technological advancements, regulatory influences, and shifting customer expectations. By synthesizing secondary data sources alongside expert interviews, our aim is to present a clear, concise perspective on the forces propelling and challenging the injection molding industry today.
Beginning with a macro assessment, this overview identifies key drivers and risk factors, then transitions into a layered examination of segmentation dynamics, regional performance, and competitive profiles. Emphasis is placed on delivering actionable intelligence that supports both strategic decision-making and technical innovation. Whether guiding investment priorities, informing product development, or shaping operational roadmaps, readers will gain the insights needed to navigate complexity and capture emerging opportunities in a rapidly evolving market landscape.
Emerging Forces Reshaping the Injection Molding Arena
Injection molding is evolving under the influence of multiple transformative forces, reshaping both its technological base and its strategic imperatives. Foremost among these is the rise of Industry 4.0, where sensors, data analytics, and machine learning converge to drive predictive maintenance and adaptive process control. Manufacturers who integrate connected automation are gaining measurable improvements in throughput and quality consistency.
Simultaneously, sustainability is taking center stage as environmental regulations tighten and end users demand greener products. Innovations in recyclable resins and energy-efficient hydraulic systems are rapidly transitioning from pilot projects to standard offerings. Material science breakthroughs, such as bio-derived polymers and optimized blends of polycarbonate and polypropylene, are unlocking new performance thresholds. In tandem, the push toward miniaturization has elevated techniques like micro injection molding, enabling intricate geometries for medical devices and electronics. Together, these shifts are redefining competitive advantage, challenging incumbents to adapt or risk obsolescence.
Assessing the 2025 U.S. Tariff Effects on Injection Molding
The cumulative impact of United States tariffs implemented in 2025 has introduced significant complexity to the injection molding value chain. Tariffs on imported resin grades, particularly polyamide and polycarbonate, have elevated material costs and prompted procurement teams to explore alternative suppliers in Asia-Pacific and domestic production. In turn, these adjustments have influenced machine utilization rates and capital investment cycles, as companies seek to balance cost pressures against efficiency targets.
On the operational front, the pass-through of tariff-induced expenses has resulted in tighter margins for contract manufacturers, encouraging long-term supply agreements and localized resin blending facilities. Meanwhile, original equipment manufacturers have reevaluated design specifications to accommodate more readily available or locally sourced plastic types. This strategic realignment has driven a wave of collaborative partnerships aimed at securing stable feedstocks. As these new sourcing models take hold, industry participants are building resilience into their networks, readying themselves for potential future shifts in trade policy.
Deep Dive into Market Segmentation Patterns
A nuanced understanding of market segmentation is essential to navigate the injection molding landscape. The analysis by end use industry reveals that automotive applications command substantial share, encompassing exteriors that demand high-impact polystyrene blends, streamlined interiors leveraging flexible polypropylene components, and powertrain parts forged from heat-resistant polyamide compounds. In building and construction, door and window profiles have gravitated toward rigid PVC formulations, while plumbing fittings often rely on durable polyethylene variants. Consumer goods maintain robust demand for household appliances molded from polycarbonate-acrylonitrile butadiene styrene alloys, intricate furniture details in composite plastics, and toys engineered to meet exacting safety standards. The electrical and electronics sector favors thin wall injection techniques to produce consumer electronics housings from acrylonitrile butadiene styrene, as well as precision electrical components molded from flame-retardant polypropylene. In medical and healthcare, micro injection processes enable the fabrication of medical device components in high-purity plastics, while pharmaceutical packaging increasingly uses rigid and flexible formats of polyethylene and polypropylene. Packaging in general has evolved toward specialized solutions, with flexible films derived from low-density polyethylene and rigid containers molded from high-impact polystyrene blends.
Turning to plastic type segmentation, acrylonitrile butadiene styrene retains strength in consumer electronics housings, whereas polyamide remains integral to engineering components requiring thermal stability. Polycarbonate’s impact resistance underpins safety-critical applications, and polyethylene spans packaging to plumbing. Polypropylene sees universal use across multiple industries, complemented by specialized polystyrene and polyvinyl chloride offerings where cost-efficiency or chemical resistance is paramount.
Machine type further differentiates market opportunities, with electric presses capturing attention for their precision and energy efficiency, hybrid systems balancing capital outlay with performance, and hydraulic units persisting in heavy-duty, high-tonnage applications. Clamping force segmentation highlights the demand for less than 500 ton machines in consumer and medical niches, 500 to 1000 ton systems for mid-range automotive and building applications, and above 1000 ton presses for exterior panels and large packaging forms. Process innovations such as co injection, gas assisted injection, micro injection, standard injection, and thin wall injection each unlock specific design freedoms and material efficiencies. By mapping these segmentation layers, stakeholders can pinpoint growth corridors and align resource allocation with highest-value opportunities.
This comprehensive research report categorizes the Injection Molding market into clearly defined segments, providing a detailed analysis of emerging trends and precise revenue forecasts to support strategic decision-making.
- End Use Industry
- Plastic Type
- Machine Type
- Clamping Force
- Process Type
Regional Performance Highlights in Injection Molding
Regional dynamics remain integral to strategic planning in the injection molding industry. In the Americas, demand is buoyed by the resurgent automotive sector and increasing adoption of lightweight materials in aerospace and medical devices. Investments in localized resin blending facilities and electric machine installations underscore a drive for greater supply chain resilience and sustainability.
Within Europe, Middle East and Africa, stringent regulatory frameworks around recyclability and emissions have accelerated the deployment of energy-efficient presses and bio-based polymers. The region’s mature automotive and construction industries continue to spur innovation, while emerging markets in North Africa present nascent opportunities for building and consumer goods applications.
The Asia-Pacific landscape is defined by rapid capacity expansion and escalating domestic consumption. Countries with established plastics manufacturing ecosystems are advancing toward smart factories, whereas developing economies prioritize cost-effective standard injection solutions. Cross-border investments and joint ventures are reshaping the competitive map, enabling global players to capture local market share and optimize their regional footprints.
This comprehensive research report examines key regions that drive the evolution of the Injection Molding market, offering deep insights into regional trends, growth factors, and industry developments that are influencing market performance.
- Americas
- Europe, Middle East & Africa
- Asia-Pacific
Strategic Profiles of Leading Injection Molding Players
Market leadership in injection molding is concentrated among a cadre of equipment OEMs and resin suppliers that excel in innovation and customer support. Pioneering high-speed electric presses, one leading manufacturer has driven efficiency gains for electronics and medical customers, while another global player has doubled down on turnkey solutions that integrate material handling, robotics, and process analytics. Resin producers have responded by co-developing tailored formulations, including flame-retardant grades and bio-based blends, to meet evolving end use requirements.
Mid-sized equipment providers are carving out niches through specialized capabilities such as micro injection and thin wall molding, often collaborating with tool makers to deliver vertically integrated solutions. Service organizations differentiate on rapid-response maintenance networks and performance guarantee contracts, helping contract manufacturers maintain uptime and consistency. Throughout the competitive landscape, strategic alliances are emerging to unify automation, digital monitoring, and sustainability metrics into cohesive offerings that address both cost and environmental imperatives.
This comprehensive research report delivers an in-depth overview of the principal market players in the Injection Molding market, evaluating their market share, strategic initiatives, and competitive positioning to illuminate the factors shaping the competitive landscape.
- Haitian International Holdings Limited
- Arburg GmbH + Co KG
- Engel Holding GmbH
- Sumitomo (SHI) Demag Plastics Machinery GmbH
- KraussMaffei Group GmbH
- JSW Plastics Machinery, Inc.
- Nissei Plastic Industrial Co., Ltd.
- Milacron Holdings Corp.
- Shibaura Machine Co., Ltd.
- BOY Machines, Inc.
Actionable Strategies to Navigate Market Complexity
To thrive amid intensifying competition and regulatory complexity, industry leaders should accelerate the digitalization of their operations. Embedding advanced process control and real-time analytics within molding cells will unlock productivity gains while reducing scrap rates. Equally, forging deeper partnerships with resin suppliers to develop custom materials can yield performance differentiation and buffer against cost volatility.
Investment in modular, flexible manufacturing platforms is recommended to accommodate shifting product lifecycles and evolving end use preferences. By standardizing automation interfaces and leveraging modular toolsets, producers can compress lead times and tailor production volumes more efficiently. Additionally, integrating sustainability initiatives-such as closed-loop recycling streams and energy recovery systems-will not only align with regulatory mandates but also resonate with end customers demanding greener products.
Finally, market diversification remains a vital hedge against regional or sector-specific downturns. Expanding service offerings into adjacent areas like additive manufacturing or value-added assembly can unlock new revenue streams and stabilize utilization. By adopting a proactive posture on strategic foresight and resource allocation, executives can position their organizations to outpace peers and seize growth in both established and emerging segments.
Rigorous Research Framework Underpinning the Analysis
This analysis is underpinned by a comprehensive research framework that combined both secondary and primary methodologies. Secondary research involved a systematic review of industry publications, regulatory filings, corporate financial disclosures, and patent databases to establish foundational understanding and identify emerging technology trends. In parallel, primary research entailed in-depth interviews with key stakeholders, including manufacturing executives, R&D heads, and supply chain specialists, ensuring that qualitative insights complemented quantitative data.
Key findings were validated through a rigorous triangulation process, cross-referencing insights from different sources to mitigate bias and enhance reliability. Data points were benchmarked against historical performance metrics and comparable production technologies to contextualize their significance. This methodological rigor ensures that the conclusions drawn reflect a balanced and accurate portrayal of the injection molding market as it stands today.
Explore AI-driven insights for the Injection Molding market with ResearchAI on our online platform, providing deeper, data-backed market analysis.
Ask ResearchAI anything
World's First Innovative Al for Market Research
Synthesizing Insights for Informed Decision Making
In synthesizing the investigation’s insights, several overarching themes emerge. Technological innovation, particularly in digitalization and material science, is reshaping competitive dynamics while sustainability imperatives redefine cost and performance benchmarks. Tariff pressures and regional variances continue to influence supply chain strategies, driving collaboration and localized production solutions. Segmentation analysis highlights distinct opportunities across industry verticals, plastic types, machine configurations, and process methodologies, guiding stakeholders toward the most attractive growth corridors.
Taken together, these findings offer a strategic roadmap for companies looking to navigate uncertainty and capitalize on emerging trends. By aligning operational capabilities with the evolving needs of end use industries, embracing modular automation, and adopting eco-conscious materials, market participants can secure lasting advantage. This executive summary serves as a foundational tool for decision-makers seeking to chart a course through the complexities of the injection molding landscape.
This section provides a structured overview of the report, outlining key chapters and topics covered for easy reference in our Injection Molding market comprehensive research report.
- Preface
- Research Methodology
- Executive Summary
- Market Overview
- Market Dynamics
- Market Insights
- Cumulative Impact of United States Tariffs 2025
- Injection Molding Market, by End Use Industry
- Injection Molding Market, by Plastic Type
- Injection Molding Market, by Machine Type
- Injection Molding Market, by Clamping Force
- Injection Molding Market, by Process Type
- Americas Injection Molding Market
- Europe, Middle East & Africa Injection Molding Market
- Asia-Pacific Injection Molding Market
- Competitive Landscape
- ResearchAI
- ResearchStatistics
- ResearchContacts
- ResearchArticles
- Appendix
- List of Figures [Total: 26]
- List of Tables [Total: 511 ]
Secure Your Comprehensive Injection Molding Report Today
Secure your leadership position in the injection molding market by accessing the full in-depth analysis authored by Ketan Rohom, Associate Director, Sales & Marketing. For tailored guidance and immediate access to proprietary insights that can inform strategic investments and operational optimizations, reach out today to explore purchase options and discover how this report can catalyze your next phase of growth.
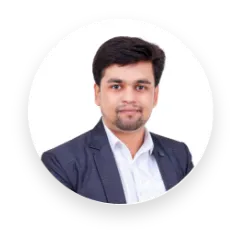
- How big is the Injection Molding Market?
- What is the Injection Molding Market growth?
- When do I get the report?
- In what format does this report get delivered to me?
- How long has 360iResearch been around?
- What if I have a question about your reports?
- Can I share this report with my team?
- Can I use your research in my presentation?