Introduction to Injection Molding Machine Auxiliary Equipment: Overview and Significance
Injection molding machine auxiliary equipment underpins the efficiency and quality of plastic production processes. These essential systems-including blender systems that precisely measure and mix resins, chiller systems that regulate processing temperatures, conveying solutions that transport materials seamlessly, and dryer systems that eliminate moisture-ensure that manufacturers meet stringent performance and product standards. As global demand for intricate plastic components rises across industries such as automotive, medical, and consumer electronics, the performance of auxiliary equipment has become a critical differentiator. Beyond core molding presses, the integration, reliability, and energy efficiency of these supporting units directly influence cycle times, material utilization, and overall cost structures. This executive summary highlights the latest technological advancements, regulatory shifts, and market dynamics shaping the auxiliary equipment sector. It provides decision-makers with concise insights into evolving end-use applications, component innovations, and competitive landscapes, empowering them to optimize investment strategies and maintain operational excellence in a rapidly evolving manufacturing environment.
Transformative Shifts Reshaping the Injection Molding Auxiliary Equipment Landscape
The landscape of auxiliary equipment for injection molding machines has shifted dramatically with the advent of Industry 4.0 and heightened sustainability targets. Smart manufacturing platforms now integrate Internet of Things (IoT) and machine-to-machine (M2M) connectivity, enabling real-time monitoring of chiller performance, blender accuracy, material flow rates, and moisture levels. Energy-efficient chillers with advanced refrigerants reduce power consumption, while predictive analytics software forewarns potential equipment failures before they interrupt production. Moreover, the transition toward all-electric and hybrid technologies has bolstered precision and reduced hydraulic fluid dependencies, driving cleaner operations. Concurrently, regulatory pressures on carbon emissions and resource utilization are accelerating adoption of closed-loop conveying systems and desiccant dryers that optimize energy usage. This wave of digitalization and sustainability not only enhances throughput but also fosters greater flexibility across diverse production processes-from thermoplastic injection molding to compression and blow molding applications. In sum, transformative shifts in automation, connectivity, and eco-design are redefining performance benchmarks and positioning auxiliary equipment as a strategic lever for competitive advantage.
Cumulative Impact of United States Tariffs in 2025 on Auxiliary Equipment
The cumulative impact of United States tariffs implemented in 2025 is reshaping supply chains and cost structures for auxiliary equipment suppliers and end users alike. Additional duties levied on imported blender systems, chiller pumps, and dryer components from key markets have driven up landed costs by double-digit percentages. In response, manufacturers are relocating assembly operations closer to major consumption hubs or forging strategic partnerships with domestic fabricators to mitigate tariff exposure. As a result, some global suppliers have shifted toward localized sourcing of compressor units and pump assemblies, stabilizing lead times and reducing exchange‐rate volatility. However, these adaptations often entail higher capital outlays for tooling and requalification, compressing margins across the value chain. On the flip side, academic and industry consortia are advocating for tariff exemptions on high-efficiency components deemed critical for energy conservation, potentially alleviating cost pressures in future policy reviews. Ultimately, evolving trade regulations demand that equipment manufacturers and molders alike pursue supply-chain diversification, optimize material flow strategies, and embed risk management frameworks to sustain profitability in an increasingly protectionist environment.
Key Segmentation Insights for the Auxiliary Equipment Market
A comprehensive segmentation analysis reveals distinct demand drivers and technological preferences across multiple dimensions. Based on end-use industries, adoption patterns diverge: aerospace applications demand ultra-precise moisture control, automotive manufacturers prioritize high-throughput conveying systems, and medical device producers require validated dryer technologies. When examining machine component types, gravimetric and volumetric blenders deliver accuracy across compound mixing, while air-cooled, water-cooled chillers and chiller pumps each offer tailored temperature regulation options. Conveying systems range from pneumatic air transport to robust mechanical conveyors, and dryer systems span compressed air, desiccant, and vacuum solutions, each optimized for specific resin moisture profiles. Technology type segmentation highlights a growing share of all-electric machines in clean-room settings, hybrid systems balancing speed and energy use, and traditional hydraulic designs in heavy-duty molding applications. Process type analysis shows that while blow and compression molding maintain steady aux-equipment requirements, injection molding predominates, with thermoplastic and thermoset branches influencing resin handling and drying protocols. Resin type considerations separate thermoplastic polymers-such as ABS, polyethylene, polypropylene, and polystyrene-from thermoset families including phenolics and polyurethane, dictating dryer and blender specifications. End-product segmentation spans complex automotive interiors and under-the-hood components, precision electronic housings, life-critical medical devices, and beverage and food packaging containers. Meanwhile, maintenance strategies break down into predictive, preventive, and routine approaches, each supported by condition-monitoring sensors and analytics platforms. Sales channels vary from direct OEM relationships to established distributors and emerging online retail platforms. Finally, integration with manufacturing systems through IoT and M2M architectures underpins the drive toward autonomous production cells, where auxiliary equipment seamlessly exchanges data with primary molding machines and central supervisory control systems.
This comprehensive research report categorizes the Injection Molding Machine Auxiliary Equipment market into clearly defined segments, providing a detailed analysis of emerging trends and precise revenue forecasts to support strategic decision-making.
- End-Use Industries
- Machine Component Type
- Technology Type
- Process Type
- Resin Type
- End-Products
- Maintenance Type
- Auxiliary Equipment Sales Channels
- Integration With Manufacturing Systems
Regional Dynamics Driving Auxiliary Equipment Demand
Regional dynamics play a pivotal role in shaping auxiliary equipment demand and innovation trajectories. In the Americas, stringent energy efficiency standards and near-shoring trends have encouraged investment in high-performance chillers and local assembly operations, with direct sales channels dominating major automotive and packaging hubs. Across Europe, Middle East & Africa, regulatory frameworks targeting carbon footprints have spurred adoption of closed-loop heat recovery systems and desiccant dryers in industries from aerospace to consumer goods, with distribution partners offering tailored maintenance services. In the Asia-Pacific region, rapid industrial expansion and growing domestic molders drive robust uptake of cost-effective volumetric blenders, mechanical conveyors, and hybrid technology packages, supported by online retail platforms that streamline aftermarket component procurement. Each region’s unique blend of regulatory drivers, infrastructure maturity, and industrial focus underscores the need for equipment providers to calibrate product portfolios, after-sales networks, and integration capabilities to local market conditions.
This comprehensive research report examines key regions that drive the evolution of the Injection Molding Machine Auxiliary Equipment market, offering deep insights into regional trends, growth factors, and industry developments that are influencing market performance.
- Americas
- Asia-Pacific
- Europe, Middle East & Africa
Leading Players Shaping the Auxiliary Equipment Market Landscape
Leading equipment suppliers demonstrate differentiated strategies to capture market share and address evolving customer needs. AEC, Inc. (Application Engineering Company) emphasizes custom gravimetric blending solutions calibrated to specific resin formulations, while Conair Group Inc. offers integrated dryer-conveyor-blender modules that simplify installation and service. Koch-Technik targets high-end pharmaceutical and packaging applications with precision chillers and temperature control units, and Kreyenborg GmbH & Co. KG focuses on modular conveying and drying lines for automated production cells. L-R Systems & Engineering, Inc. delivers energy-efficient vacuum dryers and centralized vacuum systems, whereas Maguire Products Inc. leads in volumetric blending and material-handling automation. Motan Colortronic Ltd. pioneers color dosing and weight-based material handling, and MPM Pvt. Ltd. (Moulded Plastic Machinery) caters to emerging markets with competitively priced chiller pumps and compressed air dryers. Novatec, Inc. advances smart conveying and dryer solutions with IoT integration, and Piovan S.p.A champions closed-loop temperature control and material handling for high-volume molding. Plastic Systems S.r.l develops modular volumetric and gravimetric blenders, while Shini USA specializes in industrial dryers and feeders configured for North American specifications. Sterling Systems & Controls, Inc. optimizes ingredient handling with scale-based automation, Summit Systems pioneers integrated dryer-blender assemblies for thermoset processing, and Wittmann Battenfeld GmbH delivers turnkey auxiliary equipment lines synchronized with all-electric molding presses.
This comprehensive research report delivers an in-depth overview of the principal market players in the Injection Molding Machine Auxiliary Equipment market, evaluating their market share, strategic initiatives, and competitive positioning to illuminate the factors shaping the competitive landscape.
- AEC, Inc. (Application Engineering Company)
- Conair Group Inc.
- Koch-Technik
- Kreyenborg GmbH & Co. KG
- L-R Systems & Engineering, Inc.
- Maguire Products Inc.
- Motan Colortronic Ltd.
- MPM Pvt. Ltd. (Moulded Plastic Machinery)
- Novatec, Inc.
- Piovan S.p.A
- Plastic Systems S.r.l.
- Shini USA
- Sterling Systems & Controls, Inc.
- Summit Systems
- Wittmann Battenfeld GmbH
Actionable Recommendations for Industry Leaders
To capitalize on emerging opportunities and mitigate risks, industry leaders should pursue several strategic imperatives. First, deepen investments in IoT-enabled condition monitoring and predictive maintenance solutions to minimize unplanned downtime and optimize lifecycle costs. Second, diversify supply chains by qualifying multiple regional suppliers for critical components, thereby reducing tariff exposure and transportation costs. Third, accelerate development of energy-efficient chiller and dryer systems that meet tightening environmental regulations and appeal to sustainability-focused end users. Fourth, expand digital sales channels and after-sales support through cloud-based service platforms that deliver remote diagnostics and parts replenishment alerts. Fifth, forge partnerships with machine-tool builders to integrate auxiliary equipment seamlessly into turnkey molding cells, enhancing ease of installation and total cost of ownership. Sixth, upskill technical teams to manage complex automation architectures and data analytics tools. Finally, tailor product portfolios to high-growth end-use segments-such as medical devices and packaging-by offering validated compliance features and rapid changeover capabilities. By executing these recommendations, companies can strengthen competitive positioning and capture value in a dynamic market environment.
Explore AI-driven insights for the Injection Molding Machine Auxiliary Equipment market with ResearchAI on our online platform, providing deeper, data-backed market analysis.
Ask ResearchAI anything
World's First Innovative Al for Market Research
Conclusion: Maximizing Competitiveness in Auxiliary Equipment
In conclusion, the auxiliary equipment sector for injection molding machines stands at a crossroads defined by digital transformation, sustainability mandates, and evolving trade policies. Technological advancements in automation, IoT integration, and energy-efficient designs are redefining performance benchmarks, while 2025 tariff changes underscore the importance of supply-chain agility and local sourcing. Segmentation analysis reveals that equipment requirements vary markedly across end-use industries, component categories, technology types, resin families, process methods, and sales channels, necessitating tailored solutions and service models. Regionally, distinct regulatory priorities and infrastructure capabilities shape investment decisions in the Americas, Europe, Middle East & Africa, and Asia-Pacific markets. Leading suppliers distinguish themselves through specialized product innovations, strategic partnerships, and robust after-sales ecosystems. By embracing data-driven maintenance strategies, diversifying sourcing, and aligning R&D with sustainability goals, stakeholders can navigate complexity and secure growth. Ultimately, a proactive approach-fusing technology leadership with market responsiveness-will unlock new efficiencies and drive long-term value creation across the auxiliary equipment landscape.
This section provides a structured overview of the report, outlining key chapters and topics covered for easy reference in our Injection Molding Machine Auxiliary Equipment market comprehensive research report.
- Preface
- Research Methodology
- Executive Summary
- Market Overview
- Market Dynamics
- Market Insights
- Cumulative Impact of United States Tariffs 2025
- Injection Molding Machine Auxiliary Equipment Market, by End-Use Industries
- Injection Molding Machine Auxiliary Equipment Market, by Machine Component Type
- Injection Molding Machine Auxiliary Equipment Market, by Technology Type
- Injection Molding Machine Auxiliary Equipment Market, by Process Type
- Injection Molding Machine Auxiliary Equipment Market, by Resin Type
- Injection Molding Machine Auxiliary Equipment Market, by End-Products
- Injection Molding Machine Auxiliary Equipment Market, by Maintenance Type
- Injection Molding Machine Auxiliary Equipment Market, by Auxiliary Equipment Sales Channels
- Injection Molding Machine Auxiliary Equipment Market, by Integration With Manufacturing Systems
- Americas Injection Molding Machine Auxiliary Equipment Market
- Asia-Pacific Injection Molding Machine Auxiliary Equipment Market
- Europe, Middle East & Africa Injection Molding Machine Auxiliary Equipment Market
- Competitive Landscape
- ResearchAI
- ResearchStatistics
- ResearchContacts
- ResearchArticles
- Appendix
- List of Figures [Total: 34]
- List of Tables [Total: 821 ]
Next Steps: Access the Comprehensive Market Research Report
To gain comprehensive insights and strategic guidance on the auxiliary equipment market, reach out to Ketan Rohom, Associate Director, Sales & Marketing at 360iResearch. Ketan can provide details on how to purchase the full market research report, which delivers in-depth analysis of market dynamics, competitive landscapes, segmentation trends, and actionable recommendations tailored to your strategic priorities.
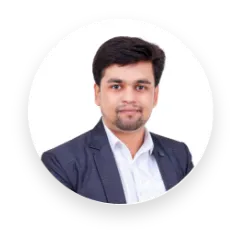
- When do I get the report?
- In what format does this report get delivered to me?
- How long has 360iResearch been around?
- What if I have a question about your reports?
- Can I share this report with my team?
- Can I use your research in my presentation?