Transforming Food and Beverage Safety with Cutting-Edge Inspection Technologies to Elevate Quality and Operational Resilience Across Processing Facilities
Inspection technologies are no longer peripheral tools but central pillars that bolster both safety and efficiency across food and beverage facilities. In an era where consumer expectations are driven by transparency and rapid turnaround, organizations must transcend traditional quality control paradigms and adopt holistic inspection strategies. This opening discussion synthesizes the imperatives reshaping inspection protocols, underscores the convergence of digital and regulatory pressures, and elucidates how integrated solutions can deliver seamless oversight from raw material intake to final product dispatch.
By contextualizing the inspection landscape within broader industry dynamics-such as evolving legislative frameworks, rising incidences of supply chain disruptions, and the proliferation of data analytics capabilities-this section establishes the foundational concepts that guide subsequent analyses. It illuminates the interplay between technological advances like AI-enabled vision platforms and conventional detection methodologies, emphasizing how each modality contributes to layered defense mechanisms against contamination, foreign materials, and labeling errors. Transitioning toward an overview of critical factors, readers will gain clarity on why inspection systems have emerged as strategic assets rather than operational afterthoughts.
Navigating the Paradigm Shift in Food and Beverage Processing Driven by Smart Automation and Heightened Regulatory Demands
Across the past decade, food and beverage processing has undergone seismic shifts propelled by the relentless integration of automation and the tightening grip of international standards. Facilities that once relied exclusively on manual checks now harness a hybrid matrix of AI-enabled vision inspection, X-ray screening, and spectroscopic analysis to detect anomalies with unprecedented speed and precision. This section dissects the technological trajectories redefining inspection efficacy, illustrating how machine learning algorithms refine defect recognition while adaptive sensors deliver real-time alerts to minimize downtime and waste.
Simultaneously, regulatory bodies worldwide have escalated their scrutiny of food safety practices, mandating comprehensive traceability and risk management protocols. As a result, processors are compelled to weave inspection processes into the broader tapestry of digital supply networks, ensuring that every batch, from bakery goods to meat cuts, adheres to exacting quality criteria. By charting these convergent currents-technological innovation dovetailed with rigorous compliance-this analysis spotlights the paradigm shift that is elevating inspection from reactive checkpoints to proactive guardians of consumer trust and operational continuity.
Unpacking the Compound Effects of 2025 United States Tariff Policies on Equipment Sourcing and Supply Chains for Inspecting F&B Products
In 2025, sweeping tariff adjustments enacted by the United States government have reverberated across supply chains, exerting varied pressures on the procurement of inspection equipment. With levies imposed on imported steel and specialized electronic components, manufacturers of conveyors, X-ray units, and spectroscopic analyzers have encountered elevated input costs, which in turn cascade to end-users in the form of higher capital expenditures. As processors contend with these escalated hardware prices, many are reexamining their sourcing strategies-shifting assembly operations back onshore or seeking alternative suppliers in tariff-free or lower-duty jurisdictions.
Moreover, the cumulative impact of additional duties on Chinese-origin electronic modules has spurred strategic partnerships between equipment vendors and local component fabricators to mitigate cost volatility. While some firms have absorbed these tariff pressures through margin adjustments, others have accelerated the adoption of service-based models that decouple inspection performance from outright equipment ownership. The net effect is a recalibrated operating environment in which total cost of ownership calculations must integrate tariff scenarios, lead-time fluctuations, and compliance overhead to safeguard both financial resilience and inspection rigor.
Revealing Key Market Segmentation Dimensions to Guide Strategic Adoption of Inspection Solutions Across Diverse Food Processing Categories
By dissecting the market along product type, it becomes evident that bakery operations prioritize rapid metal detection to accommodate continuous production lines, whereas dairy processors lean heavily on spectroscopic analysis to verify compositional purity and detect adulterants. Meanwhile, the beverage sector relies on X-ray inspection to identify glass or plastic fragments, and meat processors integrate ultrasonic testing to assess texture and density anomalies before packaging. Confectionery manufacturers, for their part, often deploy visual inspection systems to ensure color consistency and shape fidelity, leveraging automated AI-enabled solutions to scale with complex product designs.
Transitioning to the technology segmentation, metal detection systems remain a mainstay across all subsegments, though the ascendancy of X-ray platforms is reshaping how facilities manage multi-material products. Visual inspection has bifurcated into manual checks for intermittent line speeds and automated vision solutions for high-throughput operations; within automation, AI-driven vision engines complement traditional rule-based algorithms, driving down false-reject rates while adapting to product variation. In this context, spectroscopy and ultrasonic testing emerge as specialized modalities, deployed in applications where chemical composition and structural integrity are paramount.
Inspection type segmentation further refines this picture: chemical analysis is indispensable for dairy and beverage quality assurance, microbial testing underpins safety protocols in high-moisture environments, and visual inspection safeguards branding and labeling accuracy. Equipment type considerations-spanning conveyors that integrate inline detectors to packaging machines with built-in fill, label, and seal verification-underscore how mechanical design and inspection functions collide to streamline end-to-end workflows. When viewed through the processing stage lens, facilities invest in sorting and cleaning at preprocessing to reduce contamination loads, embed inspection within processing to detect anomalies in real time, and deploy distribution-stage screening to validate packaging integrity during storage and transit. Finally, end-user segmentation reveals that food service operators prioritize rapid turnaround and cost efficiency, institutional caterers emphasize compliance and traceability, and packaged food producers-whether retail or wholesale-demand scalable, high-precision solutions to uphold brand reputation across diverse distribution channels.
This comprehensive research report categorizes the Inspection System for Food & Beverage Processing market into clearly defined segments, providing a detailed analysis of emerging trends and precise revenue forecasts to support strategic decision-making.
- Product Type
- Technology
- Inspection Type
- Equipment Type
- Processing Stage
- End User
Examining Regional Market Dynamics to Uncover Growth Drivers and Compliance Strategies within the Americas EMEA and Asia-Pacific Food Inspection Sectors
The Americas region is characterized by a robust regulatory framework that emphasizes preventative controls and transparent supply chains, driving widespread investment in end-to-end inspection technologies. North American processors often pilot advanced AI-enabled vision systems to comply with stringent FDA and CFIA standards, while agricultural hubs in South America focus on modular, cost-effective metal detection and microbial testing solutions to support export-oriented commodity processing.
Within Europe, Middle East, and Africa, the landscape is fragmented by divergent regulatory regimes and infrastructure maturity levels. EU member states have harmonized comprehensive digital traceability mandates, prompting the widespread rollout of networked inspection platforms that feed into centralized data repositories. In contrast, Middle Eastern markets are rapidly adopting turnkey X-ray and spectroscopy systems to meet growing domestic demand for processed foods, whereas African operators often rely on portable inspection kits and manual visual checks in lower-throughput contexts, with gradual migration toward automated modalities as connectivity and capital availability improve.
Asia-Pacific showcases a dual dynamic: established markets like Japan and South Korea deploy next-generation hybrid inspection cells combining sonic, optical, and chemical analytics to support premium packaged goods, while rapidly industrializing economies in Southeast Asia and India prioritize affordable, scalable metal detection and labeling verification systems to sustain high-volume snack and beverage production. Collectively, this regional segmentation underscores how local regulatory targets, production scale, and technological infrastructure converge to shape inspection investments globally.
This comprehensive research report examines key regions that drive the evolution of the Inspection System for Food & Beverage Processing market, offering deep insights into regional trends, growth factors, and industry developments that are influencing market performance.
- Americas
- Europe, Middle East & Africa
- Asia-Pacific
Highlighting Leading Industry Players Driving Innovation and Collaboration in Food and Beverage Inspection Technology Ecosystems Worldwide
A cadre of established technology specialists continues to influence the trajectory of inspection innovation. Companies offering metal detection and X-ray platforms have expanded their portfolios to include AI-powered analytics, forging partnerships with software providers to enrich defect detection algorithms and real-time reporting capabilities. Meanwhile, spectroscopy and ultrasonic equipment manufacturers have deepened collaborations with ingredient suppliers and academic research centers to refine sensor accuracy and broaden application scopes across complex product matrices.
In parallel, emerging players have carved out niches by delivering specialized visual inspection modules that leverage convolutional neural networks to adaptively learn new defect patterns without extensive manual configuration. These agile vendors often integrate their solutions with existing automation frameworks, enabling seamless retrofits and minimal process interruption. Additionally, a cluster of service-oriented firms has risen to prominence by offering subscription-based inspection platforms, which combine hardware leasing, ongoing software updates, and performance-based warranties to align vendor incentives with operational uptime and quality targets.
Collectively, these industry dynamics reflect a collaborative ecosystem in which traditional equipment providers, software innovators, and service integrators converge to deliver comprehensive inspection suites. This cooperative model accelerates technology adoption, distributes risk, and fosters continuous improvement cycles, ensuring that even the most complex food and beverage processes remain under vigilant quality oversight.
This comprehensive research report delivers an in-depth overview of the principal market players in the Inspection System for Food & Beverage Processing market, evaluating their market share, strategic initiatives, and competitive positioning to illuminate the factors shaping the competitive landscape.
- Mettler-Toledo International Inc.
- Thermo Fisher Scientific Inc.
- Minebea Intec GmbH
- Ishida Co., Ltd.
- Marel hf.
- Fortress Technology, Inc.
- Anritsu Corporation
- CEIA S.p.A.
- Sesotec GmbH
- Bühler AG
Strategic Actions for Industry Leaders to Enhance Inspection Capabilities and Advance Quality Assurance Frameworks in Food Processing Operations
To capitalize on the latest inspection advancements, leaders should first conduct a holistic process audit that maps critical control points against product risk profiles. Armed with this intelligence, they can then prioritize technology deployments-starting with modular metal detection upgrades where throughput demands are highest and extending to hybrid vision-spectroscopy cells for high-value product lines. Leadership teams are advised to foster cross-functional committees that bridge operations, quality assurance, and IT, ensuring that technology investments are complemented by robust change-management protocols and staff training programs.
Furthermore, diversifying supply chains through dual-sourcing strategies and tariff-mitigation partnerships can stabilize equipment costs and minimize lead-time shocks. Embracing pay-per-performance or software-as-a-service models allows organizations to hedge capital expenditure while accessing continuous innovation. On the compliance front, industry leaders should engage proactively with regulatory bodies, participate in standards-setting working groups, and pilot blockchain-enabled traceability initiatives to future-proof their inspection frameworks.
Ultimately, success hinges on cultivating a quality-driven culture in which inspection data is democratized across teams and leveraged in real time for root-cause analysis, continuous process optimization, and strategic decision-making. By weaving these recommendations into their operational DNA, food and beverage processors can elevate safety, sustain brand integrity, and unlock new efficiencies in an increasingly competitive environment.
Outlining a Robust Research Framework Combining Primary Insights and Secondary Analysis to Ensure Comprehensive Coverage of F&B Inspection Market Trends
This analysis is grounded in a blend of primary interviews with plant managers, technology integrators, and regulatory officials, alongside secondary review of industry publications, standards documents, and patent filings. Data triangulation was employed to validate emerging trends, with case studies selected across diverse processing segments to capture best-practice insights. Quantitative equipment performance metrics were corroborated through vendor disclosures and anonymized user surveys, ensuring balanced representation of both established and disruptive solutions.
In addition, our methodology incorporated on-site facility assessments in North America, Europe, and Asia-Pacific, enabling direct observation of inspection workflows and integration challenges. Market intelligence was further enriched through partnerships with academic research labs specializing in sensor technologies, which provided technical validation of AI-driven vision accuracy and spectroscopic detection thresholds. Finally, ongoing advisory forums facilitated iterative feedback loops, ensuring that the research deliverables reflect the latest regulatory amendments, tariff announcements, and technology roadmaps.
Explore AI-driven insights for the Inspection System for Food & Beverage Processing market with ResearchAI on our online platform, providing deeper, data-backed market analysis.
Ask ResearchAI anything
World's First Innovative Al for Market Research
Drawing Holistic Conclusions on the Future Trajectory of Food and Beverage Inspection Systems in an Era of Innovation Regulatory Growth and Market Flux
Drawing together the threads of technological innovation, evolving regulatory demands, and shifting supply chain dynamics, it is clear that inspection systems now occupy a strategic nexus within food and beverage processing. The integration of AI-enhanced vision, advanced spectroscopy, and real-time data analytics has elevated defect detection from episodic quality checks to continuous safeguarding mechanisms. Concurrently, tariff adjustments and regional compliance requirements underscore the importance of agile sourcing strategies and proactive regulatory engagement.
As processors embrace modular, service-oriented deployment models, the emphasis will increasingly shift toward performance outcomes rather than capital ownership. This transition promises to democratize access to cutting-edge inspection capabilities, enabling small and mid-scale producers to compete on quality and safety metrics previously reserved for large corporations. Ultimately, the convergence of technology, methodology, and organizational culture will define the next frontier in food and beverage inspection, empowering stakeholders to uphold rigorous standards while driving operational excellence and market differentiation.
This section provides a structured overview of the report, outlining key chapters and topics covered for easy reference in our Inspection System for Food & Beverage Processing market comprehensive research report.
- Preface
- Research Methodology
- Executive Summary
- Market Overview
- Market Dynamics
- Market Insights
- Cumulative Impact of United States Tariffs 2025
- Inspection System for Food & Beverage Processing Market, by Product Type
- Inspection System for Food & Beverage Processing Market, by Technology
- Inspection System for Food & Beverage Processing Market, by Inspection Type
- Inspection System for Food & Beverage Processing Market, by Equipment Type
- Inspection System for Food & Beverage Processing Market, by Processing Stage
- Inspection System for Food & Beverage Processing Market, by End User
- Americas Inspection System for Food & Beverage Processing Market
- Europe, Middle East & Africa Inspection System for Food & Beverage Processing Market
- Asia-Pacific Inspection System for Food & Beverage Processing Market
- Competitive Landscape
- ResearchAI
- ResearchStatistics
- ResearchContacts
- ResearchArticles
- Appendix
- List of Figures [Total: 30]
- List of Tables [Total: 1104 ]
Empowering Stakeholders to Make Informed Decisions with Expert-Guided Research Reports Tailored to Food and Beverage Inspection System Opportunities
As the food and beverage industry continues to evolve, decision-makers face a critical juncture where gaining timely access to accurate, expert-validated insights can spell the difference between capitalizing on emerging opportunities or falling behind. Ketan Rohom, Associate Director of Sales & Marketing, stands ready to guide potential partners through the intricate landscape of inspection technology advancements, regulatory considerations, and supply chain dynamics. By engaging directly, stakeholders can tailor their intelligence requirements to their unique operational contexts, ensuring that investment decisions are aligned with strategic priorities.
Bridging the gap between raw data and actionable intelligence, our comprehensive research offering not only highlights the technological innovations transforming inspection methodologies but also delves into practical implementation frameworks, vendor evaluations, and regulatory risk assessments. Prospective subscribers will benefit from an interactive consultation that clarifies report scope, customization options, and delivery timelines. This collaborative approach guarantees that the final deliverable addresses specific challenges-whether optimizing metal detection systems, advancing AI-driven visual inspection, or navigating evolving tariff regimes.
To secure a competitive edge in a market marked by rapid technological change and increasing quality standards, reach out to Ketan Rohom today. By requesting a personalized demonstration of the research report, organizations will gain a clear roadmap for deploying inspection systems that bolster product safety, streamline operations, and satisfy the most stringent compliance requirements. Take the first step toward transforming your inspection strategy-connect with Ketan Rohom now to explore subscription packages and customized research solutions.
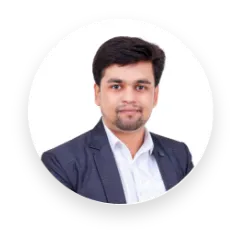
- When do I get the report?
- In what format does this report get delivered to me?
- How long has 360iResearch been around?
- What if I have a question about your reports?
- Can I share this report with my team?
- Can I use your research in my presentation?