The Insulation Coating Materials Market size was estimated at USD 11.56 billion in 2024 and expected to reach USD 12.65 billion in 2025, at a CAGR 8.91% to reach USD 19.31 billion by 2030.

Unlocking the Potential of the Insulation Coating Market
In the dynamic landscape of insulation coating materials, stakeholders are encountering converging imperatives for enhanced performance, greater sustainability, and cost efficiency. As energy consumption regulations tighten and asset lifecycles become a focal point of operational planning, the role of advanced coatings that deliver superior thermal insulation and corrosion protection has never been more critical.
Manufacturers, suppliers, and end users are responding to heightened environmental standards and evolving customer expectations by investing in high-performance polymers, novel formulations, and application techniques that maximize durability while minimizing environmental impact. These innovations span across acrylic, epoxy, polyurethane, and silicone chemistries, each offering distinct advantages in terms of chemical resistance, adhesion, and application versatility.
This executive summary synthesizes key market drivers, transformative trends, tariff implications, segmentation insights, regional dynamics, leading company strategies, and actionable recommendations. It serves as a guide for decision-makers seeking to align product portfolios with emerging opportunities, mitigate supply chain risks, and position their organizations at the forefront of a rapidly evolving insulation coating ecosystem.
Navigating Transformative Shifts Reshaping the Industry
The insulation coating industry is undergoing transformative shifts driven by technological breakthroughs, sustainability imperatives, and changing customer demands. Nanocoating and smart coating technologies are redefining performance benchmarks, delivering self-healing and self-cleaning functionalities that extend asset lifespans and reduce maintenance costs. Meanwhile, digital process controls and automation in application methods are elevating consistency and efficiency in high-volume production environments.
Environmental regulations and circular economy initiatives are compelling manufacturers to reformulate products with lower volatile organic compound content, waterborne systems, and bio-based raw materials. This regulatory momentum is fostering rapid adoption of solvent-free powder coatings and water-based alternatives that meet stringent emission standards without sacrificing performance.
Furthermore, supply chain resilience and localization strategies are reshaping procurement practices. Companies are repositioning regional manufacturing hubs closer to end-use markets to mitigate geopolitical risks and tariff disruptions. As end users demand customized coatings for niche applications-ranging from aerospace thermal barriers to oil and gas pipeline protection-flexible manufacturing configurations and agile R&D processes become essential competitive enablers.
Assessing the Ripple Effects of 2025 U.S. Tariff Changes
The introduction of United States tariffs on imported insulation coating materials in 2025 has initiated a cascade of strategic realignments across the value chain. Manufacturers reliant on overseas resins and additives are experiencing upward pressure on raw material costs, prompting a re-evaluation of supplier portfolios and pricing strategies. Importers are recalibrating landed cost models to account for additional duties, while domestic producers are accelerating capacity expansions to capture increased local demand.
Consequently, some end-use industries such as automotive and construction are facing margin compression, leading to selective product reformulation or shifts toward alternative coating solutions. Pipeline operators and steel infrastructure projects are recalculating total lifecycle costs, factoring in both tariff-induced material price increases and potential performance trade-offs of locally sourced substitutes.
To navigate this new tariff environment, leading organizations are diversifying feedstock origins, negotiating long-term contracts with tier-one suppliers, and exploring backward integration opportunities. Collaboration between coating formulators and raw material manufacturers is intensifying to develop cost-optimized blends that preserve critical performance attributes while mitigating the impact of import duties.
Decoding Key Segmentation for Strategic Growth
When the market is dissected by material, it reveals a competitive interplay among acrylic, epoxy, polyurethane, and silicone chemistries. Epoxy coatings, further divided into liquid and powder variants, continue to gain traction for their exceptional adhesion and chemical resistance. Polyurethane systems-available as one-component and two-component formulations-are prized for their flexibility and abrasion resistance across diverse environments.
Analyzing the market through the lens of coating type uncovers distinctions between powder coatings, solvent-based systems, and water-based alternatives. Electrostatic powder processes and fluidized bed techniques underpin the broader powder coating segment, delivering high thickness build and minimal VOC emissions. Solvent-based formulas remain relevant where rapid cure profiles are essential, while water-based coatings advance in sectors with strict environmental mandates.
Examining end-use industries illuminates the breadth of application contexts. Aerospace sectors demand ultra-light, high-temperature insulators; automotive markets split between OEM and aftermarket requirements; construction divides into commercial, industrial, and residential segments; marine coatings serve both commercial marine vessels and recreational boats; oil and gas infrastructure calls for specialized anti-corrosion systems.
In terms of application function, anti-corrosion coatings-targeting pipelines and steel structures-share the stage with fireproofing, surface protection, and thermal insulation products. Form distinctions between liquid concentrates, ready-to-use solutions, composite powders, and pure powders drive format choices based on application logistics and on-site handling protocols.
Technological segmentation highlights the surge of nanocoating options, such as metal oxide and polymer nanocomposites, alongside self-cleaning and self-healing smart coatings. Traditional formulations remain vital, offering proven reliability in cost-sensitive projects.
This comprehensive research report categorizes the Insulation Coating Materials market into clearly defined segments, providing a detailed analysis of emerging trends and precise revenue forecasts to support strategic decision-making.
- Material
- Coating
- End Use Industry
- Application
- Form
- Technology
Unveiling Regional Dynamics Driving Market Momentum
Across the Americas, robust demand originates from a resurgent automotive sector seeking lightweight insulation solutions and an infrastructure pipeline boom requiring advanced anti-corrosion systems. North American manufacturers are investing in localized production to satisfy rising consumption and to hedge against import duty exposures.
Europe, Middle East & Africa present a mosaic of regulatory drivers and growth pockets. Western Europe’s stringent emissions standards propel water-based and low-VOC powders, while the Middle East’s oil and gas giants procure specialized coatings for extreme temperature and corrosion protection. In sub-Saharan Africa, nascent construction and industrialization projects are beginning to explore high-performance thermal insulation options.
Asia-Pacific leads global consumption through accelerated urbanization and infrastructure investment. Automotive OEM expansions in China and India, combined with large-scale renewable energy installations in Southeast Asia, fuel demand for coatings that balance cost-effectiveness with enhanced durability. Regional producers are forging joint ventures to penetrate new markets and to streamline supply chains.
This comprehensive research report examines key regions that drive the evolution of the Insulation Coating Materials market, offering deep insights into regional trends, growth factors, and industry developments that are influencing market performance.
- Americas
- Europe, Middle East & Africa
- Asia-Pacific
Profiling Leading Players Shaping Industry Evolution
Market leaders are advancing through a combination of targeted acquisitions, strategic alliances, and sustained R&D investments. Key players have established global manufacturing footprints that enable rapid response to regional demand fluctuations while preserving economies of scale. Innovative partnerships with chemical suppliers and technology developers accelerate the commercialization of next-generation formulations and application equipment.
Several companies are differentiating their offerings through value-added services such as on-site application support, real-time performance monitoring, and custom color management. These initiatives deepen customer relationships and extend service lifecycles beyond standard product warranties. In parallel, proprietary intellectual property portfolios in nanocoatings and smart coatings are cementing competitive moats, positioning owners as preferred suppliers for mission-critical applications.
Collaboration ecosystems involving end-users, academic institutions, and innovation incubators are emerging as fertile grounds for breakthrough solutions. By co-developing test protocols and accelerating pilot projects, these coalitions reduce time-to-market and validate performance under real-world conditions. As companies navigate tariff headwinds, agile M&A strategies are enabling consolidation in mature segments while unlocking growth in high-potential niches.
This comprehensive research report delivers an in-depth overview of the principal market players in the Insulation Coating Materials market, evaluating their market share, strategic initiatives, and competitive positioning to illuminate the factors shaping the competitive landscape.
- PPG Industries, Inc.
- The Sherwin-Williams Company
- Akzo Nobel N.V.
- Nippon Paint Holdings Co., Ltd.
- Kansai Paint Co., Ltd.
- Axalta Coating Systems Ltd.
- RPM International Inc.
- Jotun A/S
- BASF SE
- Hempel A/S
Actionable Strategies to Secure Competitive Advantage
To maintain a competitive edge, executives should diversify supply chains by cultivating multiple reliable raw material sources and by leveraging regional production hubs. Investing in nanocoating and smart coating R&D will unlock premium pricing and meet escalating performance requirements in sectors such as aerospace and energy.
Formulators must align product pipelines with evolving environmental regulations by expanding water-based and powder coating offerings. Establishing co-development agreements with end-users can streamline qualification cycles and enhance product fit. Embracing digital tools for application monitoring and predictive maintenance will further differentiate service models and foster long-term client partnerships.
Strategic collaborations between technology providers, raw material producers, and end-use customers are essential to accelerate the adoption of advanced materials. Companies should pursue targeted acquisitions to fill competency gaps-particularly in nano-enabled formulations-and to strengthen geographic coverage. Finally, robust scenario planning for tariff and supply chain disruptions will enable proactive mitigation and sustained operational resilience.
Robust Research Methodology Underpinning Insights
This research integrates qualitative and quantitative methods to ensure comprehensive and credible insights. Primary data sources include interviews with coating formulators, raw material suppliers, end-use decision-makers, and industry experts. These interviews provide firsthand perspectives on emerging challenges, innovation pipelines, and supply chain dynamics.
Secondary research encompasses authoritative trade publications, patent filings, regulatory documents, and financial reports. Data triangulation validates market trends by reconciling disparate sources and identifying consistent patterns. The segmentation framework reflects material chemistry, coating type, end-use industry, application function, form factor, and technology classification to deliver granular visibility into market subsegments.
Analytical techniques such as SWOT assessments, Porter’s Five Forces, and scenario analyses underpin strategic conclusions. Regional market modeling relies on consumption trends, production capacities, and trade flow data. Continuous quality checks and peer reviews ensure data integrity and a robust narrative that aligns with real-world market developments.
Explore AI-driven insights for the Insulation Coating Materials market with ResearchAI on our online platform, providing deeper, data-backed market analysis.
Ask ResearchAI anything
World's First Innovative Al for Market Research
Concluding Insights and Future Outlook
In summary, the insulation coating materials market is at a pivotal moment characterized by rapid technological innovation, evolving regulatory landscapes, and shifting trade dynamics. Stakeholders who proactively incorporate segmentation intelligence, regional dynamics, and tariff impact analysis will be best positioned to capitalize on emerging growth avenues.
Leading organizations are already retooling supply chains, scaling advanced formulations, and forging collaborative ecosystems to maintain momentum. The convergence of sustainability goals and performance demands offers a fertile ground for differentiation and value creation.
As the industry continues to evolve, agility and strategic foresight will separate market leaders from followers. The insights presented here serve as a foundation for informed decision-making, guiding executives toward investments that deliver resilience and competitive advantage.
This section provides a structured overview of the report, outlining key chapters and topics covered for easy reference in our Insulation Coating Materials market comprehensive research report.
- Preface
- Research Methodology
- Executive Summary
- Market Overview
- Market Dynamics
- Market Insights
- Cumulative Impact of United States Tariffs 2025
- Insulation Coating Materials Market, by Material
- Insulation Coating Materials Market, by Coating
- Insulation Coating Materials Market, by End Use Industry
- Insulation Coating Materials Market, by Application
- Insulation Coating Materials Market, by Form
- Insulation Coating Materials Market, by Technology
- Americas Insulation Coating Materials Market
- Europe, Middle East & Africa Insulation Coating Materials Market
- Asia-Pacific Insulation Coating Materials Market
- Competitive Landscape
- ResearchAI
- ResearchStatistics
- ResearchContacts
- ResearchArticles
- Appendix
- List of Figures [Total: 28]
- List of Tables [Total: 769 ]
Partner with Our Expert to Acquire the Full Market Report
Seize the opportunity to deepen your understanding of insulation coating materials by partnering with Ketan Rohom, Associate Director, Sales & Marketing. His expertise will guide you to the precise insights and competitive intelligence needed to inform strategic investments and operational decisions. Connect with Ketan to explore customized access options, secure detailed data analysis, and leverage proprietary findings for sustainable growth. Take this decisive step toward mastering market complexities and driving innovation-reach out today to obtain the complete market research report.
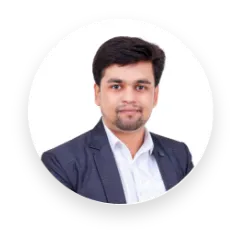
- How big is the Insulation Coating Materials Market?
- What is the Insulation Coating Materials Market growth?
- When do I get the report?
- In what format does this report get delivered to me?
- How long has 360iResearch been around?
- What if I have a question about your reports?
- Can I share this report with my team?
- Can I use your research in my presentation?