The Iron Casting Market size was estimated at USD 132.62 billion in 2024 and expected to reach USD 140.95 billion in 2025, at a CAGR 6.10% to reach USD 189.25 billion by 2030.
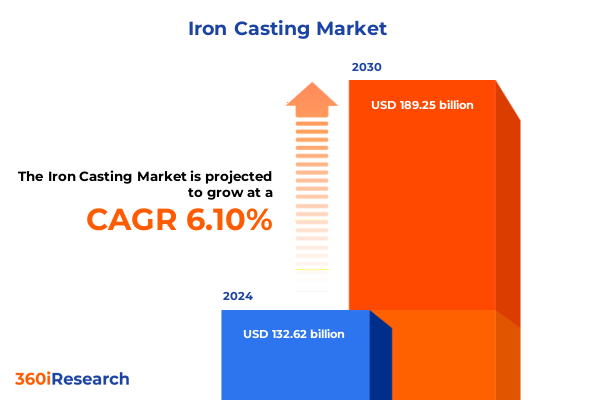
Introduction to the Iron Casting Market: Scope and Objectives
The iron casting market stands at a pivotal crossroads, shaped by rapid technological advancements, evolving end-user demands and shifting global trade dynamics. As legacy foundries modernize operations and new entrants leverage additive manufacturing, the competitive landscape is undergoing profound transformation. This summary distills critical insights, offering a concise yet thorough examination of recent disruptive trends, policy impacts and strategic segmentation that define today’s environment.
Drawing on extensive primary research and expert interviews, this overview equips decision-makers with the clarity needed to navigate complexity, identify high-value opportunities and mitigate emerging risks. It establishes a foundation for deeper analysis of tariff regimes, regional growth pockets and competitive positioning strategies. By framing the current market contours, this introduction underscores both the urgency and potential for innovation, setting the stage for targeted recommendations that drive sustainable growth and operational excellence.
Transformative Shifts in the Iron Casting Landscape
Over the past decade, the iron casting sector has witnessed a series of transformative shifts that extend beyond mere production volumes. Automation and Industry 4.0 integration have elevated quality control and throughput, enabling foundries to reduce cycle times and scrap rates while enhancing metallurgical precision. Concurrently, digital twin technology and real-time data analytics are redefining predictive maintenance protocols, minimizing unplanned downtime and improving energy efficiency.
In parallel, end-user industries such as automotive and energy are pressing foundries to deliver lighter, more complex castings, prompting increased adoption of ductile alloys and hybrid materials. Sustainability mandates and carbon-neutral objectives have accelerated investment in electric induction furnaces and closed-loop recycling systems, reshaping supply chains and influencing raw-material sourcing strategies. Furthermore, strategic partnerships between foundries and engineering firms are fostering co-development of tailor-made casting solutions, expanding the value chain and unlocking new application niches.
Together, these developments signal a fundamental reorientation of traditional practices, compelling stakeholders to embrace agile manufacturing models and elevate collaborative innovation efforts.
Assessing the Cumulative Impact of 2025 U.S. Tariffs on Iron Casting
In 2025, the United States introduced a new tranche of tariffs aimed at bolstering domestic manufacturing and countering perceived unfair trade practices. The cumulative impact of these measures is already manifesting across cost structures and supply-chain resilience. Import duties on raw pig iron and certain finished castings have increased input costs for foundries reliant on overseas scrap and alloy shipments, eroding profit margins and prompting a reevaluation of supplier portfolios.
Simultaneously, domestic producers are recalibrating capacity utilization to capitalize on reduced import competition, leading to a temporary uptick in pricing power. However, end-users, particularly in automotive and energy sectors, are facing component cost inflation that risks downstream project delays and budget overruns. To adapt, several firms have accelerated nearshoring initiatives, relocating production closer to final assembly plants and diversifying procurement across tariff-exempt allies.
Overall, the 2025 tariff regime underscores the dual challenge of safeguarding national industries while preserving global competitiveness, compelling market participants to innovate both operationally and strategically.
Key Segmentation Insights Shaping Industry Dynamics
The market’s complexity becomes more apparent when dissected by key segmentation parameters. Based on Type, demand oscillates between high-strength ductile iron casting, versatile gray iron casting, specialized alloyed iron casting and malleable iron casting, each finding unique applications. When viewed through an Application lens, agricultural equipment requirements for plowing equipment and tractor components contrast sharply with automotive needs for braking systems-which themselves split into discs, drums and pads-engine parts and suspension components. Construction demand spans drainage systems, foundations and frame structures, while the energy sector prioritizes nuclear plant castings and wind turbine components. Home appliances rely on cookware and heating equipment, and industrial machinery calls for compressors-both air compressors and gas compressors-alongside heavy equipment and turbines.
Process innovations further differentiate market niches: sand casting techniques, including green sand and resin sand casting, coexist with centrifugal casting, die casting, investment casting and shell molding, each offering distinct advantages in precision, surface finish and throughput. Material considerations add another dimension, dividing the market between ferrous materials and non-ferrous materials, the latter encompassing aluminum alloys and copper alloys. End-user orientations, from automotive industry players to lubrication equipment manufacturers, pipe & fittings producers, railroad companies and valves & pumps suppliers, drive bespoke solution development. Finally, casting weight categories-heavy, medium and light-dictate foundry investments in specialized molds, handling equipment and quality-inspection protocols.
By intersecting these segmentation vectors, stakeholders can pinpoint high-growth microsegments, optimize resource allocation and tailor value propositions to precise customer requirements.
This comprehensive research report categorizes the Iron Casting market into clearly defined segments, providing a detailed analysis of emerging trends and precise revenue forecasts to support strategic decision-making.
- Type
- Application
- Process
- Material
- End-User
- Casting Weight
Key Regional Insights Driving Market Divergence
Regional dynamics reveal divergent growth trajectories and competitive advantages. The Americas continue to lead in technological adoption and downstream integration, supported by capacity expansions in North America and robust demand from both automotive and infrastructure projects in South America. In Europe, Middle East & Africa, stringent environmental regulations and carbon-reduction targets are stimulating green casting solutions, while geopolitical trade realignments are prompting firms to seek pan-regional supply-chain resilience. The Asia-Pacific region exhibits the most pronounced expansion, driven by rapid urbanization, energy infrastructure build-out and surge in manufacturing hubs across China, India and Southeast Asia. Each region’s regulatory frameworks, raw-material access and labor cost structures shape how foundries prioritize investments and forge strategic alliances.
This comprehensive research report examines key regions that drive the evolution of the Iron Casting market, offering deep insights into regional trends, growth factors, and industry developments that are influencing market performance.
- Americas
- Asia-Pacific
- Europe, Middle East & Africa
Leading Players and Competitive Dynamics in Iron Casting
Competitive intensity remains high, with established global foundry leaders coexisting alongside agile specialists. Bradken Limited, Calmet and Castings P.L.C. maintain significant footprints in heavy industrial applications, while Georg Fischer AG, Hitachi Zosen Corporation and Hermann Reckers GmbH & Co. KG differentiate through advanced process automation and R&D investments. Regional champions such as Kirloskar Ferrous Industries Limited, Jiangsu Shengrong High End Equipment Manufacturing Industry Co., Ltd. and LIAONING BORUI MACHINERY CO., LTD excel in cost-competitive supply for Asia’s burgeoning energy and infrastructure sectors. Simultaneously, niche innovators including Bunty LLC, Crescent Foundry Company Pvt Ltd, Dotson Iron Castings by MacLean Power Systems and Fonderia Ghirlandina S.p.A. carve out specialized segments in automotive braking components and precision casting for renewable energy.
Large diversified conglomerates like Charlotte Pipe and Foundry Company, Charter Manufacturing Company, Inc. and McWane, Inc. leverage integrated distribution networks to secure long-term contracts, while momentum builds behind modern aluminum castings at Modern Aluminum Castings Co., Inc. and cross-material capabilities at Fusium and G&W Foundry. Companies such as Grede LLC, Grupo Industrial Saltillo, S.A.B. de C.V., JS AutoCast Foundry Pvt Ltd by Bharat Forge and Xinxing Ductile Iron Pipe Co., Ltd. reinforce their positions through vertical integration, acquiring downstream machining and finishing operations. Emerging service-oriented models from Newby Foundries Ltd., OSCO Industries, Pittsburgh Foundry & Machine Company, U.S. Casting Company, Waupaca Foundry, Inc. and Zetwerk Manufacturing Businesses Pvt Ltd emphasize rapid prototyping, digital quoting and just-in-time delivery.
This comprehensive research report delivers an in-depth overview of the principal market players in the Iron Casting market, evaluating their market share, strategic initiatives, and competitive positioning to illuminate the factors shaping the competitive landscape.
- Bradken Limited
- Bunty LLC
- Calmet
- Castings P.L.C.
- Chamberlin PLC
- Charlotte Pipe and Foundry Company
- Charter Manufacturing Company, Inc.
- Crescent Foundry Company Pvt Ltd
- Dotson Iron Castings by MacLean Power Systems
- Fonderia Ghirlandina S.p.A.
- Fusium
- G&W Foundry
- Gartland Foundry Co., Inc.
- Georg Fischer AG
- Georgsmarienhütte Holding GmbH
- Gontermann-Peipers GmbH
- Grede LLC
- Grupo Industrial Saltillo, S.A.B. de C.V.
- Hermann Reckers GmbH & Co. KG
- Hitachi Zosen Corporation
- Jiangsu Shengrong High End Equipment Manufacturing Industry Co., Ltd.
- JS AutoCast Foundry Pvt Ltd. by Bharat Forge Limited
- Jürgens Holding GmbH
- Kirloskar Ferrous Industries Limited
- LIAONING BORUI MACHINERY CO., LTD
- MAT Holdings Inc.
- McWane, Inc.
- Modern Aluminum Castings Co., Inc.
- Newby Foundries Ltd.
- OSCO Industries
- Pittsburgh Foundry & Machine Company
- U.S. Casting Company
- Waupaca Foundry, Inc.
- Xinxing Ductile Iron Pipe Co., Ltd.
- Zetwerk Manufacturing Businesses Pvt Ltd.
Actionable Recommendations for Industry Leadership
To thrive amidst escalating complexity, industry leaders should prioritize investment in advanced manufacturing technologies that drive yield improvements and reduce energy intensity. Pursuing flexible automation cells capable of swift changeovers between ductile, gray and alloyed iron can unlock responsiveness to fluctuating demand patterns. Concurrently, forging strategic alliances with raw-material suppliers and logistics partners mitigates tariff-related risks and strengthens supply-chain resilience.
Developing modular process architectures that integrate digital twins, predictive analytics and additive-hybrid tooling-including shell molding enhancements-enables continuous quality optimization and accelerates time-to-market. At the same time, embedding sustainability targets such as closed-loop scrap recycling and low-carbon furnace operations aligns with regulatory trajectories and enhances brand equity among environmentally conscious end-users.
Finally, leveraging micro-segmentation insights to tailor value propositions-whether lightweight components for automotive OEMs, corrosion-resistant casings for energy applications or high-volume ductile castings for agricultural equipment-ensures differentiated offerings that command premium margins and foster long-term customer loyalty.
Explore AI-driven insights for the Iron Casting market with ResearchAI on our online platform, providing deeper, data-backed market analysis.
Ask ResearchAI anything
World's First Innovative Al for Market Research
Conclusion: Consolidating Strategic Imperatives
The iron casting landscape is characterized by rapid technological evolution, fluctuating trade policies and nuanced segmentation demands. Stakeholders who embrace digital transformation, diversify material portfolios and establish end-to-end supply-chain partnerships will secure competitive advantages. By aligning process innovation with sustainability imperatives and adapting swiftly to regional market dynamics, foundries can meet stringent quality standards while capitalizing on emerging growth corridors.
Continuous monitoring of tariff landscapes, combined with proactive scenario planning, will shield operating margins from geopolitical shocks. Concurrently, a customer-centric approach that applies granular segmentation intelligence will enhance negotiation power and foster stickier relationships with OEMs and industrial machinery manufacturers. Ultimately, the foundries that integrate agility, resilience and innovation into their strategic roadmaps will shape the future of iron casting.
This section provides a structured overview of the report, outlining key chapters and topics covered for easy reference in our Iron Casting market comprehensive research report.
- Preface
- Research Methodology
- Executive Summary
- Market Overview
- Market Dynamics
- Market Insights
- Cumulative Impact of United States Tariffs 2025
- Iron Casting Market, by Type
- Iron Casting Market, by Application
- Iron Casting Market, by Process
- Iron Casting Market, by Material
- Iron Casting Market, by End-User
- Iron Casting Market, by Casting Weight
- Americas Iron Casting Market
- Asia-Pacific Iron Casting Market
- Europe, Middle East & Africa Iron Casting Market
- Competitive Landscape
- ResearchAI
- ResearchStatistics
- ResearchContacts
- ResearchArticles
- Appendix
- List of Figures [Total: 28]
- List of Tables [Total: 732 ]
Next Steps: Connect with Ketan Rohom to Access the Full Report
To access the comprehensive market research report and engage directly with in-depth analysis, please reach out to Ketan Rohom, Associate Director of Sales & Marketing. He will guide you through tailored insights and support your strategic decision-making process.
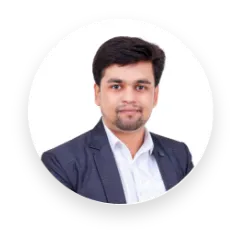
- How big is the Iron Casting Market?
- What is the Iron Casting Market growth?
- When do I get the report?
- In what format does this report get delivered to me?
- How long has 360iResearch been around?
- What if I have a question about your reports?
- Can I share this report with my team?
- Can I use your research in my presentation?