The Isostatic Pressing Market size was estimated at USD 7.01 billion in 2024 and expected to reach USD 7.46 billion in 2025, at a CAGR 6.55% to reach USD 10.26 billion by 2030.

Isostatic Pressing Unveiled: Comprehensive Introduction to Principles, Process Advantages, Emerging Applications, and Strategic Market Opportunities
Isostatic pressing stands at the forefront of advanced manufacturing techniques, offering unparalleled control over material density and microstructure. By applying uniform pressure through a fluid medium, both cold and hot isostatic pressing enable the consolidation of powders into complex geometries with exceptional mechanical properties. This introduction illuminates the foundational principles underpinning isostatic pressing, outlining how uniform pressure application leads to defect reduction and enhanced material performance.
As global industries pursue lighter, stronger, and more durable components, isostatic pressing emerges as a pivotal enabler for breakthrough innovations. In aerospace applications, it allows for the production of high-performance turbine components and landing gear parts with precise tolerances. The automotive sector benefits from dense structural parts and brake components that meet stringent safety and durability requirements. Additionally, electronics manufacturers leverage isostatic pressing for thermal management components and semiconductor packaging substrates, where uniform microstructure is critical.
Through this introduction, readers will gain a clear understanding of why isostatic pressing has evolved far beyond niche applications to become a mainstream technology. The process’s ability to deliver consistent quality, coupled with its compatibility with emerging additive manufacturing workflows, underscores its strategic importance. With this strong foundation established, subsequent sections will delve into the transformative shifts, tariff impacts, and segmentation dynamics reshaping this versatile market.
Revolutionary Developments Redefining Isostatic Pressing Landscape: Innovations in Materials, Processes, and Industry Collaboration
The isostatic pressing landscape is undergoing profound transformation as new materials, processes, and digital technologies converge to redefine performance parameters. Novel high-performance powders, including advanced metal matrix composites and reinforced ceramics, are shifting the material capabilities that engineers can harness. Simultaneously, the integration of real-time monitoring and artificial intelligence into press controls is enabling unprecedented precision in pressure profiles, temperature regulation, and cycle optimization, driving yields higher and reducing scrap rates.
Moreover, the convergence of additive manufacturing and hot isostatic pressing is unlocking opportunities to densify complex geometries that were previously unachievable. This hybrid workflow not only enhances mechanical properties but also accelerates prototyping cycles for aerospace and medical implants. Sustainability considerations are steering innovation toward energy-efficient equipment designs and low-emission hydraulic fluids, aligning isostatic pressing with corporate environmental targets. In parallel, collaborative research consortia between material suppliers, equipment manufacturers, and end users are catalyzing rapid iteration of process parameters to accommodate next-generation alloys, including high-entropy and refractory metals.
These transformative shifts are collectively elevating isostatic pressing from a support process to a driver of technological differentiation. As industries prioritize lightweighting, miniaturization, and customization, the agility offered by advanced press technologies and materials science partnerships will determine which organizations lead the competitive frontier.
Assessing the Cumulative Impact of United States Tariff Measures in 2025 on Isostatic Pressing Supply Chains and Costs
Throughout 2025, a series of U.S. tariff measures have had a cumulative impact on isostatic pressing supply chains and cost structures. At the outset of the year, the Office of the United States Trade Representative imposed a 50 percent tariff on solar wafers and polysilicon imports, alongside a 25 percent levy on certain tungsten products, as part of its Section 301 action against China effective January 1, 2025. These raw materials are critical for semiconductor packaging substrates and thermal management components, driving end users to explore alternative sourcing and to accelerate qualification of domestic polysilicon and engineered ceramics.
In addition, Section 232 tariffs on steel and aluminum were raised from 25 to 50 percent on June 4, 2025, affecting the supply of high-purity metallic powders such as aluminum and titanium used in hot isostatic pressing for aerospace and medical implants. Earlier in the spring, passenger vehicles and light trucks faced a 25 percent tariff on non-U.S. content beginning April 3, 2025, while key automotive parts-including engines, transmissions, and powertrain components-incurred 25 percent duties from May 3, 2025. These measures have rippled through the automotive supply chain, increasing the cost base for structural parts that often undergo cold isostatic compaction.
Moreover, the introduction of a 50 percent tariff on copper, scrap copper, and derivative products as of August 1, 2025 has elevated costs for electrical and thermal conductivity components produced via isostatic pressing. While some emergency tariffs remain enjoined by recent court rulings, the overall tariff landscape has prompted manufacturers to pursue strategic stockpiling, localize key powder production, and engage with government incentive programs. These adaptations are reshaping procurement strategies and underscoring the need for flexibility in sourcing and process planning.
Key Segmentation Insights Illuminating Market Dynamics Across Applications, Processes, Materials, Equipment Types, and Pressure Ranges
Examining market segmentation through the lenses of application industries, process types, raw materials, equipment categories, and pressure ranges reveals nuanced insights into competitive dynamics and growth pockets. Within aerospace, the demand for landing gear parts, structural components, and turbine components underscores a premium on powder metallurgy solutions that deliver flawless integrity under extreme stress. Conversely, automotive applications are bifurcated between brake and engine components, where powder compaction precision is vital, and structural parts-such as chassis frames and mounting brackets-where material economy and reproducibility drive processing choices.
In electronics, the emphasis on semiconductor packaging and thermal management components highlights the intersection of tight tolerances and advanced ceramics, while energy sector applications span fuel cells, nuclear components, and renewable energy equipment, each with unique material compatibility and densification requirements. Medical markets for dental tools, implants, and surgical instruments increasingly coalesce around advanced hot isostatic pressing of dental and orthopedic implants, where biocompatibility and surface finish are paramount.
Process segmentation further shapes the landscape: cold isostatic pressing, through powder compaction and preforming, anchors high-throughput production of uniform green bodies, whereas hot isostatic pressing of additive manufactured parts and casting densification-including both aluminum and titanium casting densification-enables consolidation of complex geometries and the elimination of internal defects. The choice of raw material, whether alumina or zirconia ceramics, ceramic matrix or metal matrix composites, aluminum, copper, steel, pure titanium or Ti-6Al-4V, or polymers such as polyether ether ketone and thermoplastic polyurethane, dictates the thermal profile and press design, whether batch or continuous. Finally, the distribution of pressure ranges from sub-200 MPa to in excess of 1000 MPa aligns equipment selection with performance requirements, driving specialization among press manufacturers and service bureaus.
This comprehensive research report categorizes the Isostatic Pressing market into clearly defined segments, providing a detailed analysis of emerging trends and precise revenue forecasts to support strategic decision-making.
- Offering
- Type
- Equipment Type
- Material
- CIP Process Type
- End-Use Industry
Regional Dynamics Uncovered: Comparative Analysis of Isostatic Pressing Adoption Trends Across Americas, Europe, Middle East, Africa, and Asia-Pacific
Regional developments are redefining global value chains for isostatic pressing as each geography leverages its industrial strengths and policy frameworks. In the Americas, the confluence of robust aerospace and automotive sectors, supported by established metal and polymer powder manufacturing capacities, drives demand for both cold and hot isostatic pressing. The North American market benefits from proximity to end users and streamlined logistics, while South American players are increasingly investing in local service centers to reduce lead times and currency exposure.
Europe, the Middle East, and Africa exhibit a diverse landscape where established aerospace clusters in Western Europe coexist with emerging renewable energy and defense investments in the Middle East. Rigorous regulatory environments in the European Union catalyze innovation in materials with lower environmental impact, and circular economy initiatives are fostering research into powder recycling and lifecycle analysis. Africa’s nascent industrial base is tapping into joint ventures to access advanced press technologies for energy and infrastructure projects.
In the Asia-Pacific region, electronics-driven markets in Japan, South Korea, and Taiwan maintain leadership in semiconductor packaging and thermal management components, while China’s shipbuilding and automotive industries continue to expand local HIP capacities despite tariff pressures. India and Southeast Asia are anchoring growth in medical and renewable energy equipment, supported by government incentives aimed at import substitution and export promotion. As regional trade agreements and supply-chain resilience objectives evolve, manufacturers are optimizing footprints and forging strategic partnerships to navigate distinct regulatory and cost structures across these zones.
This comprehensive research report examines key regions that drive the evolution of the Isostatic Pressing market, offering deep insights into regional trends, growth factors, and industry developments that are influencing market performance.
- Americas
- Europe, Middle East & Africa
- Asia-Pacific
Leading Industry Players Spotlight: Strategic Profiles and Competitive Positions of Key Companies Driving Isostatic Pressing Advancements
The competitive landscape of isostatic pressing is shaped by a blend of equipment OEMs, service bureaus, and alloy producers each vying to expand their technological leadership. Quintus Technologies has fortified its position in high-pressure hot isostatic pressing by deploying next-generation control systems and expanding service centers in key aerospace hubs. Bodycote, a leading heat treatment and specialist materials provider, has leveraged its global footprint to integrate isostatic pressing with complementary surface treatment capabilities, enabling turnkey solutions for medical and automotive clients.
Other prominent players such as FCT Systeme and ECM have differentiated through bespoke press designs that cater to advanced composites and ceramic matrix composites, while ATI Metals and Carpenter Technology have emphasized the development of specialized powders-such as Ti-6Al-4V and high-purity ceramics-to underpin performance gains in critical components. Across these companies, strategic initiatives include targeted acquisitions, investments in digital twin platforms, and partnerships with research institutions to accelerate material qualification cycles.
Despite varying scales, leading firms share a common focus on enhancing process transparency, reducing time to market, and enabling more sustainable operational practices. As market entrants pursue niche applications and regional service expansions, incumbent players continue to leverage their expertise in scale-up, quality assurance, and regulatory compliance to maintain competitive advantage.
This comprehensive research report delivers an in-depth overview of the principal market players in the Isostatic Pressing market, evaluating their market share, strategic initiatives, and competitive positioning to illuminate the factors shaping the competitive landscape.
- Bodycote plc
- Kobe Steel, Ltd.
- Aegis Technology
- American Isostatic Presses Inc.
- Aubert & Duval
- DORST Technologies GmbH
- EPSI International
- FREY & Co. GmbH
- HEDRICH GmbH
- Hiperbaric S.A.
- Höganäs AB
- Isostatic Pressing Services, LLC
- Kennametal, Inc.
- Kittyhawk, Inc.
- Metal Technology Co. Ltd.
- MSE Teknoloji Ltd.
- Nikkiso Co., Ltd.
- Nishimura Advanced Ceramics Co., Ltd.
- Pacific Technology Corporation
- Pressure Technology, Inc.
- Shanxi Golden Kaiyuan Co., Ltd.
- Synertech PM Inc.
Actionable Recommendations for Executives and Engineers to Enhance Performance, Operational Efficiency, and Market Positioning in Isostatic Pressing
To maintain a competitive edge, industry leaders must adopt a multifaceted strategy that emphasizes innovation, supply chain resilience, and operational excellence. Companies should prioritize investment in advanced powder characterization tools and in-situ monitoring technologies to ensure consistent feedstock quality for both cold and hot isostatic pressing. Strengthening partnerships with raw material suppliers will help mitigate volatility introduced by tariffs and geopolitical uncertainties, while co-development agreements can accelerate the introduction of novel alloy and ceramic powders.
In parallel, organizations should explore the integration of automated handling systems and digital twin models to optimize press cycles, reduce energy consumption, and achieve higher throughput. Executives are advised to conduct comprehensive scenario planning around tariff evolutions and to engage with government programs that provide incentives for domestic manufacturing and innovation. Additionally, establishing cross-functional teams that align R&D, production, and quality assurance will facilitate rapid scaling of hybrid additive-HIP workflows for high-value applications.
Finally, cultivating a culture of continuous improvement through targeted training and collaboration with academic partners will ensure that engineering teams remain at the forefront of best practices in material science, process control, and sustainability. By implementing these recommendations, companies can enhance their operational efficiency, strengthen market positioning, and unlock new avenues for growth within the dynamic landscape of isostatic pressing.
Rigorous Research Methodology Overview Detailing Data Collection, Analysis Frameworks, and Validation Approaches Supporting Market Intelligence
The research underpinning this analysis combines primary and secondary methodologies to deliver a robust and defensible market intelligence framework. Primary research encompassed structured interviews with senior executives, engineers, and procurement specialists from leading aerospace, automotive, electronics, energy, and medical device manufacturers. Insights were further enriched through quantitative surveys addressing process adoption rates, material preferences, and investment priorities.
Secondary research involved exhaustive review of government tariff databases, industry association publications, technical patents, and peer-reviewed journals to validate trends in tariffs, material innovations, and equipment enhancements. Publicly filed financial reports and press releases were analyzed to triangulate strategic initiatives of key market participants. This data was synthesized using a multi-layered segmentation model covering application industries, process types, raw materials, equipment categories, and pressure ranges.
To ensure analytical rigor, findings were subjected to triangulation across data sources and peer reviewed by a panel of industry experts. Any discrepancies were reconciled through follow-up consultations, and assumptions were stress-tested against alternative scenarios. This comprehensive approach guarantees that the market insights and recommendations presented herein rest on a solid foundation of empirical evidence and expert validation.
Explore AI-driven insights for the Isostatic Pressing market with ResearchAI on our online platform, providing deeper, data-backed market analysis.
Ask ResearchAI anything
World's First Innovative Al for Market Research
Integration of Insights and Future Outlook: Conclusive Reflections on Isostatic Pressing Trends, Challenges, and Emerging Opportunities
In conclusion, isostatic pressing continues to evolve as a critical enabler for industries demanding high-integrity components and complex geometries. The convergence of advanced materials, digital process controls, and hybrid manufacturing workflows has ushered in a new era of performance capabilities. Concurrently, evolving tariff regimes in 2025 have reshaped supply chains, compelling manufacturers to adopt strategic sourcing and localized production models.
Segmentation insights highlight that opportunities span from aerospace turbine blades and automotive structural parts to semiconductor packaging and medical implants, each driven by distinct material and pressure requirements. Regional dynamics reveal differentiated growth paths, with the Americas focusing on automotive and energy, EMEA emphasizing sustainability and regulatory compliance, and Asia-Pacific advancing electronics and renewable energy applications.
By aligning strategic priorities with actionable recommendations-such as enhancing powder characterization, integrating digital twins, and pursuing collaborative R&D-industry leaders can capitalize on emerging trends and mitigate risks. This comprehensive perspective equips decision-makers with the clarity needed to navigate the complexities of material science, process innovation, and global trade, setting the stage for sustained competitive advantage in isostatic pressing.
This section provides a structured overview of the report, outlining key chapters and topics covered for easy reference in our Isostatic Pressing market comprehensive research report.
- Preface
- Research Methodology
- Executive Summary
- Market Overview
- Market Dynamics
- Market Insights
- Cumulative Impact of United States Tariffs 2025
- Isostatic Pressing Market, by Offering
- Isostatic Pressing Market, by Type
- Isostatic Pressing Market, by Equipment Type
- Isostatic Pressing Market, by Material
- Isostatic Pressing Market, by CIP Process Type
- Isostatic Pressing Market, by End-Use Industry
- Americas Isostatic Pressing Market
- Europe, Middle East & Africa Isostatic Pressing Market
- Asia-Pacific Isostatic Pressing Market
- Competitive Landscape
- ResearchAI
- ResearchStatistics
- ResearchContacts
- ResearchArticles
- Appendix
- List of Figures [Total: 30]
- List of Tables [Total: 554 ]
Engage with Ketan Rohom to Secure Your Customized Market Research Report and Accelerate Strategic Decision-Making in Isostatic Pressing
To explore how isostatic pressing insights can shape your strategic roadmap and drive competitive edge, reach out to Ketan Rohom, Associate Director, Sales & Marketing at 360iResearch. Ketan brings deep market expertise and can guide you through the report’s tailored findings, ensuring you harness the intelligence needed to optimize operations, mitigate risks, and capitalize on emerging opportunities. Engage today to schedule a consultation, discuss customization options, and secure your comprehensive research package that will unlock actionable intelligence for your next phase of growth in isostatic pressing.
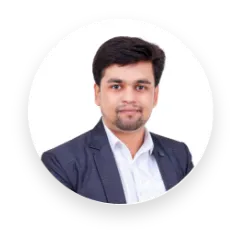
- How big is the Isostatic Pressing Market?
- What is the Isostatic Pressing Market growth?
- When do I get the report?
- In what format does this report get delivered to me?
- How long has 360iResearch been around?
- What if I have a question about your reports?
- Can I share this report with my team?
- Can I use your research in my presentation?