Introduction to Knife Gate Wafer Valve Industry
The knife gate wafer valve is a specialized isolation valve designed to handle viscous fluids, slurries, powders, and bulk solids with minimal pressure drop. Its slender gate moves through the media, slicing cleanly through solids to ensure a tight shutoff in abrasive and corrosive environments. Unlike traditional gate valves, the wafer design seats between two pipeline flanges, offering a compact profile that reduces installation space and material costs. This configuration has become indispensable in industries such as water treatment, mining, pulp and paper, and food and beverage, where efficient handling of slurries and fibrous materials is critical.
As global infrastructure spending rises and process plants demand higher uptime, manufacturers and end users alike are seeking valves that combine rugged construction with advanced operational capabilities. Emerging materials and actuation technologies now allow knife gate wafer valves to meet stringent environmental regulations and extended maintenance intervals. In parallel, digital integration through smart sensors and automated control systems is accelerating, empowering operators to monitor valve performance in real time and predict service needs.
This executive summary delves into key trends, regulatory impacts, segmentation insights, regional dynamics, and competitive strategies shaping the knife gate wafer valve sector. By synthesizing these dimensions, decision makers can formulate resilient strategies that optimize total cost of ownership and align with sustainability and digitalization imperatives.
Transformative Shifts Reshaping the Knife Gate Wafer Valve Landscape
In recent years, rapid advancements in automation and digital technologies have revolutionized the knife gate wafer valve landscape. Smart valve technology now integrates Internet of Things–enabled sensors and predictive maintenance systems, providing continuous performance data that drive operational efficiency. Consequently, asset managers can schedule service interventions precisely when needed, reducing unplanned downtime and extending valve life.
Moreover, escalating environmental regulations around leakage and fugitive emissions have placed a premium on advanced sealing technology. Manufacturers are responding with innovative materials and precision machining techniques that deliver near-zero leakage rates, even in high-pressure or high-temperature applications. In addition, the push for sustainable operations has spurred development of polymer and corrosion-resistant alloys that minimize corrosion and chemical exposure throughout valve lifecycles.
Supply chain dynamics have also shifted. Nearshoring and diversification of sourcing have emerged as strategies to mitigate geopolitical risks and tariff pressures. As a result, suppliers are establishing regional production hubs and forging strategic partnerships to ensure resilient component availability. Together, these transformative shifts are redefining performance benchmarks and competitive differentiation across the valve market.
Cumulative Impact of U.S. Tariffs 2025 on Supply and Production
The introduction of U.S. tariffs in 2025 on imported valve assemblies and critical components has generated significant ripple effects across the industry. Valve manufacturers that previously relied on lower-cost imports face increased input costs, compelling many to reevaluate their global sourcing strategies. In response, several leading producers have accelerated investments in domestic manufacturing capabilities and local supply networks to offset import duties.
Consequently, some OEMs have explored alternative sourcing in regions not subject to the new levies, including Southeast Asia and select European suppliers. This geographic pivot has introduced fresh logistical complexities, such as extended lead times and expanded inventory management requirements. To mitigate these challenges, companies are implementing advanced planning systems that align procurement cycles with production schedules and demand forecasts.
At the same time, operators in end use industries are grappling with the option to absorb higher valve costs or pass them along through pricing adjustments. This dynamic has heightened the emphasis on total cost of ownership analyses, encouraging users to select valves with longer maintenance intervals and superior energy performance. Ultimately, the 2025 tariff landscape is accelerating a broader shift toward supply chain resilience and product innovation.
Key Segmentation Insights Across Product, Material, Industry, and Technology
Analysis breaks product type into automated, electric, hydraulic, manual, and pneumatic knife gate wafer valves, with electric variants further distinguished by motor-operated and solenoid-operated configurations, revealing divergent growth trajectories driven by varying levels of automation. Material insights highlight alloy, carbon steel, cast iron, ductile iron, polymer, and stainless steel options, with polymer variants subdivided into thermoplastic and thermoset, underscoring the role of chemical compatibility, abrasion resistance, and lifecycle costs in valve selection.
End use segmentation spans food and beverage, mining, oil and gas, pharmaceuticals, power generation, pulp and paper, and water treatment. Within food and beverage, beverage production and food canning and bottling impose strict hygiene and washdown requirements, while mining’s conveyance systems and ore processing demand robust abrasion resistance. The oil and gas sector covers upstream exploration, midstream transportation, and downstream processing, each with unique pressure and temperature profiles. Power generation distinguishes between hydroelectric plants and thermal power plants, where valve reliability governs uptime. Pulp and paper differentiation into bleaching processes, paper manufacturing, and pulp production highlights the need for corrosion resistance, and water treatment’s split between industrial wastewater treatment and municipal water treatment underscores divergent chemical exposure scenarios.
Application categories include diverting valves, erosion resistant valves, flow control valves, isolation valves, and shut-off valves, reflecting specialized performance requirements. Size considerations range from large diameters above 10 inches to medium diameters between 2 and 10 inches-further classified into full bore and standard bore-and small diameters up to 2 inches, guiding selection based on installation constraints and flow characteristics. Connectivity options cover butt-weld end, flanged end, and wafer-lug styles, with butt-weld variants differentiated into plain end and socket weld end to accommodate diverse piping methodologies. Finally, technology segmentation contrasts advanced sealing techniques and conventional designs with automated control systems and smart valve technologies, where Internet of Things–enabled devices and predictive maintenance frameworks stand out for their transformative impact on operational visibility.
This comprehensive research report categorizes the Knife Gate Wafer Valve market into clearly defined segments, providing a detailed analysis of emerging trends and precise revenue forecasts to support strategic decision-making.
- Product Type
- Material Type
- End Use Industry
- Application
- Size
- Connectivity
- Technology
Regional Dynamics Driving Market Opportunities
In the Americas, abundant water treatment projects and a robust oil and gas sector underpin sustained demand for knife gate wafer valves, particularly in shale processing and municipal wastewater infrastructure. Furthermore, stringent environmental standards in North America are driving adoption of advanced sealing and automation features to reduce fugitive emissions and optimize energy usage.
Europe, Middle East & Africa present a complex tapestry of mature markets and emerging economies. In Western Europe, aging industrial assets prompt modernization initiatives, while mining expansions in select African nations and infrastructure growth in the Middle East foster new valve installations. Harmonized safety regulations and ambitious decarbonization targets in EMEA encourage investments in durable materials and integrated control systems.
Asia-Pacific emerges as the fastest-growing region, propelled by large-scale infrastructure programs, expanding chemical and pharmaceuticals sectors, and rapid urbanization. China and India serve as both major manufacturing hubs and significant end users, with Southeast Asian economies increasingly serving as cost-effective production bases. In addition, government-led water treatment and energy projects across the region continue to fuel demand for high-performance knife gate wafer valves tailored to local regulatory and environmental conditions.
This comprehensive research report examines key regions that drive the evolution of the Knife Gate Wafer Valve market, offering deep insights into regional trends, growth factors, and industry developments that are influencing market performance.
- Americas
- Asia-Pacific
- Europe, Middle East & Africa
Competitive Landscape: Leading Companies and Strategic Positioning
AVK International A/S continues to reinforce its leadership in ductile iron and cast iron wafer valves, leveraging a global distribution network and localized assembly facilities to minimize lead times. DeZURIK, Inc. maintains a competitive edge through its custom-engineered solutions and responsive aftermarket support, particularly in the mining and pulp and paper sectors. Emerson Electric Co. integrates knife gate wafer valves into comprehensive automation platforms that offer end users centralized control and diagnostic capabilities.
FCI Flow Control Industries Inc. differentiates itself with polymer-based valves suited for corrosive chemical applications, while ITT Inc. advances its portfolio with high-performance sealing technologies designed for extreme environments. John Crane Inc. melds mechanical seal expertise with valve offerings to deliver holistic fluid handling solutions. Orbinox Valves International focuses on heavy-duty gate valves engineered for demanding slurry applications in mining, complementing its wafer designs with premium wear-resistant trims.
Pentair Plc. broadens its reach through strategic acquisitions and a diversified fluid management portfolio, whereas Valmet Corporation leverages its pulp and paper heritage to tailor valve solutions for cellulose processing. Velan Inc. competes on innovation in high-specification valves for power generation and oil and gas, and Weir Group Plc. brings deep expertise in slurry-handling technologies, supporting global mining operations with robust wafer valve designs. Collectively, these leading companies deploy product innovation, strategic partnerships, and expanded regional footprints to secure market share.
This comprehensive research report delivers an in-depth overview of the principal market players in the Knife Gate Wafer Valve market, evaluating their market share, strategic initiatives, and competitive positioning to illuminate the factors shaping the competitive landscape.
- AVK International A/S
- DeZURIK, Inc.
- Emerson Electric Co.
- FCI Flow Control Industries Inc.
- ITT Inc.
- John Crane Inc.
- Orbinox Valves International
- Pentair Plc.
- Valmet Corporation
- Velan Inc.
- Weir Group Plc.
Actionable Recommendations for Industry Leaders
To thrive in this evolving environment, industry leaders should prioritize integration of predictive maintenance systems and Internet of Things–enabled sensors into their valve platforms, thereby transforming service models and enhancing uptime performance. In tandem, R&D investments in advanced sealing materials and coatings will counteract abrasive wear and corrosive damage, extending valve lifecycles and reducing total cost of ownership.
Supply chain resilience demands diversification of component sourcing and establishment of regional manufacturing capabilities to mitigate tariff risks and logistical disruptions. Forming strategic alliances with local fabricators and technology partners can accelerate time to market and strengthen entry into high-growth regions. Simultaneously, companies must refine their aftermarket service frameworks, offering remote diagnostics, rapid field support, and performance-based service agreements to foster long-term customer relationships.
Sustainability considerations call for adoption of environmentally friendly materials and processes, as well as development of valve designs optimized for energy efficiency and minimal fugitive emissions. Marketing and sales teams should equip themselves with data-driven tools and case studies that illustrate lifecycle cost savings and regulatory compliance benefits. Finally, aligning product roadmaps with emerging customer requirements-such as modular designs and digital integration-will ensure that new offerings remain relevant and competitively differentiated.
Explore AI-driven insights for the Knife Gate Wafer Valve market with ResearchAI on our online platform, providing deeper, data-backed market analysis.
Ask ResearchAI anything
World's First Innovative Al for Market Research
Conclusion: Navigating the Next Phase
The knife gate wafer valve sector stands at a crossroads shaped by digital transformation, regulatory pressures, and geopolitical shifts. Stakeholders who understand and anticipate these driving forces will gain a decisive advantage.
By leveraging insights into tariff impacts and supply chain realignment, manufacturers can secure resilient sourcing strategies and reduce cost volatility. Deep segmentation analysis illuminates where specific valve types, materials, sizes, and technologies will find the greatest application value, guiding targeted product development and marketing investments.
Regional dynamics underscore the importance of local presence, from the Americas’ mature infrastructure markets to Asia-Pacific’s rapid urbanization and EMEA’s regulatory-driven modernization. Finally, a clear view of competitive positioning reveals opportunities for differentiation through advanced sealing, smart controls, and service excellence.
In sum, a holistic approach-integrating segmentation, regional, and competitive insights-will empower industry participants to navigate complexity, mitigate risks, and capitalize on latent growth opportunities.
This section provides a structured overview of the report, outlining key chapters and topics covered for easy reference in our Knife Gate Wafer Valve market comprehensive research report.
- Preface
- Research Methodology
- Executive Summary
- Market Overview
- Market Dynamics
- Market Insights
- Cumulative Impact of United States Tariffs 2025
- Knife Gate Wafer Valve Market, by Product Type
- Knife Gate Wafer Valve Market, by Material Type
- Knife Gate Wafer Valve Market, by End Use Industry
- Knife Gate Wafer Valve Market, by Application
- Knife Gate Wafer Valve Market, by Size
- Knife Gate Wafer Valve Market, by Connectivity
- Knife Gate Wafer Valve Market, by Technology
- Americas Knife Gate Wafer Valve Market
- Asia-Pacific Knife Gate Wafer Valve Market
- Europe, Middle East & Africa Knife Gate Wafer Valve Market
- Competitive Landscape
- ResearchAI
- ResearchStatistics
- ResearchContacts
- ResearchArticles
- Appendix
- List of Figures [Total: 30]
- List of Tables [Total: 824 ]
Connect with Ketan Rohom to Acquire the Full Market Research Report
To secure your competitive edge and access the full depth of analysis, contact Ketan Rohom, Associate Director of Sales & Marketing. He will guide you through the comprehensive market research report, equipping you with the detailed insights needed to drive strategic decisions and outperform in the knife gate wafer valve arena. Reach out today to obtain the complete study and position your organization for success.
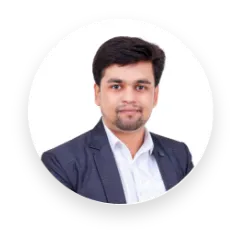
- When do I get the report?
- In what format does this report get delivered to me?
- How long has 360iResearch been around?
- What if I have a question about your reports?
- Can I share this report with my team?
- Can I use your research in my presentation?