The Lathe Machines Market size was estimated at USD 17.76 billion in 2024 and expected to reach USD 18.69 billion in 2025, at a CAGR 5.14% to reach USD 24.01 billion by 2030.

The Pivotal Role of Lathe Machines in Shaping Manufacturing Efficiency
The lathe machine, long regarded as the backbone of precision metalworking, plays an increasingly pivotal role in modern manufacturing environments. By enabling intricate turning operations and facilitating tight tolerances on cylindrical components, lathe machines support a diverse range of industries spanning automotive, healthcare, aerospace and general manufacturing. Their inherent ability to deliver consistent quality at scale has cemented their importance in today’s cost-competitive and quality-focused production landscape.
Over recent years, lathe technology has undergone a dramatic evolution. The convergence of computer numerical control mechanisms, advanced sensor integration and real-time data analytics has elevated traditional turning operations into fully automated, intelligent manufacturing processes. Predictive maintenance protocols and adaptive tooling strategies now converge within state-of-the-art lathe cells to maximize machine uptime, optimize throughput and reduce material waste. Additionally, digital twinning techniques enable virtual simulation of turning cycles, further enhancing process reliability and shortening product development timelines.
This executive summary presents a holistic examination of the lathe machine market, offering decision-makers clear visibility on emerging trends, trade-policy disruptions, segmentation dynamics, regional variations and the competitive terrain. By synthesizing rigorous qualitative insights with robust data validation, this summary delivers actionable intelligence that empowers manufacturing leaders to navigate market complexities and leverage lathe technology for sustained operational excellence. Throughout this analysis, emphasis is placed on bridging technical depth with strategic foresight to equip stakeholders with the clarity needed for informed investment and process-optimization decisions.
Emerging Forces Redefining the Global Lathe Machine Landscape
An unprecedented wave of industry transformation is reshaping how manufacturers deploy lathe machines across production facilities. Increasing demand for customized components has driven a shift from high-volume, standardized turning operations toward flexible manufacturing cells capable of rapid changeovers. This paradigm shift has been further accelerated by the rise of smart factory initiatives, where integration of automation platforms and data-driven process control transforms conventional lathe tools into intelligent systems that self-adjust parameters in real time.
Technological convergence continues to redefine product capabilities, as lathe controls now incorporate edge computing, machine learning algorithms and augmented-reality interfaces for operator training and maintenance guidance. In this evolving ecosystem, sliding headstock lathe configurations and turret lathe variants integrate seamlessly with robotic loading mechanisms, while manual bench and tool room lathes maintain relevance in low-volume, high-precision workshops. These hybrid production models allow manufacturers to balance automation benefits with the artisanal expertise that manual lathe operations deliver, ensuring both efficiency and craftsmanship.
Moreover, sustainability concerns and the push for greener manufacturing have prompted innovations in energy-efficient drive systems and eco-friendly coolant management. Materials such as advanced composites and lightweight alloys now undergo turning processes that require minimal tool wear and reduced energy consumption. As a result, lathe technology stands at the crossroads of digitalization, customization and environmental stewardship, driving transformative shifts that will define the next era of precision machining.
Assessing the Ripple Effects of 2025 U.S. Tariffs on Lathe Machine Trade
The implementation of new U.S. tariffs on imported lathe machines in 2025 has introduced a complex set of challenges for global equipment suppliers and end users alike. With levies targeting key manufacturing imports, the relative cost of advanced lathe machinery has increased, prompting buyers to reassess capital expenditure plans and seek alternative sourcing strategies. As a direct consequence, some established international vendors have accelerated local assembly initiatives to mitigate tariff burdens and preserve market competitiveness.
In response to the shifting trade landscape, supply chain leaders have realigned their distribution networks, prioritizing nearshoring and regional partnerships to reduce exposure to import duties. These strategic realignments have spurred investments in domestic machining centers and component manufacturing hubs, enabling faster delivery times and tighter quality control. At the same time, manufacturers operating in high-tariff environments have pursued value engineering efforts by consolidating machine modules and substituting critical components to maintain overall performance within revised cost structures.
Furthermore, aftersales operations and spare-part logistics have felt the reverberations of increased duties, compelling service networks to explore localized warehousing strategies and alternative distribution channels to maintain rapid response times. Looking ahead, proactive collaboration between equipment providers, component suppliers and original equipment manufacturers will be essential to navigate the tariff-driven volatility. Companies that leverage flexible sourcing agreements and cultivate multi-tiered supplier ecosystems can minimize the financial impact of trade barriers, ensuring continued access to cutting-edge lathe solutions without compromising on precision, reliability or throughput.
Unveiling Market Dimensions Through Comprehensive Segmentation
A nuanced understanding of lathe machine demand requires a granular segmentation framework that encompasses machine type, spindle orientation, construction style and end-use industry. The machine type division distinguishes between automatic systems-encompassing sliding headstock and turret variants-and manual formats that include bench, engine and tool room lathes. This bifurcated view reveals how customer preferences shift according to production scale, precision requirements and automation objectives, with sliding headstock lathes excelling in high-volume bar feeding operations and turret configurations addressing complex multi-axis part handling, while manual bench and tool room solutions cater to specialized prototyping and maintenance workflows.
Spindle orientation further clarifies market dynamics by differentiating between horizontal and vertical arrangements, each delivering unique process advantages. Horizontal setups dominate bulk turning applications where gravity assists chip evacuation, whereas vertical orientations offer superior stability for tall workpieces and specialized vertical machining tasks. Construction style adds another layer of insight, segmenting the market into flat bed, gap bed and slant bed platforms. Flat bed machines deliver uncompromising rigidity and ease of maintenance, gap bed variants enable machining of larger diameter workpieces, and slant bed configurations improve chip flow and operator ergonomics in high-speed environments.
Finally, industry verticals shape demand drivers, as lathe applications span aerospace, automotive, general manufacturing and healthcare sectors, alongside oil and gas markets that bifurcate into upstream exploration and downstream processing needs. This end-use analysis highlights how stringent tolerances in aerospace foster demand for ultra-precise turning, automotive assembly lines prioritize cycle time optimization, healthcare instrumentation insists on contamination-free processes, and oil and gas operations call for bespoke solutions to withstand harsh field conditions both upstream and downstream. By integrating these segmentation lenses, stakeholders can pinpoint the most attractive submarkets, tailor product portfolios and align service offerings to evolving customer specifications.
This comprehensive research report categorizes the Lathe Machines market into clearly defined segments, providing a detailed analysis of emerging trends and precise revenue forecasts to support strategic decision-making.
- Machine Type
- Spindle Orientation
- Construction Type
- End Use Industry
Geographic Nuances Driving Regional Lathe Machine Dynamics
In the Americas, a robust convergence of automotive, aerospace and energy production hubs sustains healthy demand for both automated and manual lathe solutions. North American manufacturers leverage advanced automation platforms and comprehensive aftermarket service networks to preserve uptime across critical production schedules. Meanwhile, Latin American markets display an increasing appetite for mid-range manual lathes, driven by cost-sensitive industrial sectors and small-scale job shops that prioritize reliability over full automation.
Europe, Middle East & Africa presents a mosaic of regulatory environments and industry specializations that influence lathe machine adoption. European producers emphasize precision and digital integration, often coupling slant bed constructions with intelligent tool monitoring systems to comply with stringent quality standards. Oil and gas infrastructures in the Middle East have created demand for heavy-duty, gap bed units capable of machining large diameter tubing, while Africa’s burgeoning manufacturing initiatives have spurred interest in accessible bench and engine lathe configurations suitable for localized infrastructure projects.
Asia-Pacific maintains its position as the largest volume market, propelled by expansive manufacturing investments in China, India and Southeast Asia. Rapid industrialization in these economies has made sliding headstock lathes the preferred choice for high-throughput metalworking, while smaller vertical lathes and specialized tool room units support niche electronics and medical device applications. Furthermore, government incentives for smart factory deployments have accelerated adoption of connected lathe technologies that integrate data analytics, predictive maintenance and remote monitoring capabilities. Across these three regions, distinct market drivers and regulatory landscapes shape regional strategy, compelling manufacturers to calibrate their offerings for optimal competitive advantage.
This comprehensive research report examines key regions that drive the evolution of the Lathe Machines market, offering deep insights into regional trends, growth factors, and industry developments that are influencing market performance.
- Americas
- Europe, Middle East & Africa
- Asia-Pacific
Competitive Insights into Leading Lathe Machine Manufacturers
The competitive landscape for lathe machinery is dominated by established global names that differentiate through innovation, service excellence and strategic partnerships. Companies renowned for pioneering multi-axis turning solutions continue to invest heavily in research and development, integrating artificial intelligence modules into control architectures and expanding their service portfolios with predictive maintenance subscriptions. At the same time, mid-tier players have carved out market niches by offering modular automation kits that retrofit existing manual lathes, enabling rapid cost-effective upgrades without full machine replacement.
Regional manufacturers in Asia and Eastern Europe have achieved significant traction by balancing competitive pricing with localized support structures. These firms often collaborate closely with component suppliers to accelerate lead times and customize machine configurations according to specific industry requirements, such as high-volume automotive stamping or offshore oil and gas operations. In addition, aftermarket service specialists have emerged as critical competitors by bundling comprehensive maintenance contracts and remote diagnostics modules, thereby extending machine lifecycles and optimizing total cost of ownership.
Strategic alliances between technology providers, software developers and machine tool specialists are further intensifying competitive dynamics. By co-developing digital ecosystems and open-platform interfaces, leading manufacturers are creating scalable solutions that interoperate across diverse production environments. This shift towards collaborative innovation underscores a broader industry trend where integrated solutions, rather than standalone equipment, define market leadership and customer loyalty.
This comprehensive research report delivers an in-depth overview of the principal market players in the Lathe Machines market, evaluating their market share, strategic initiatives, and competitive positioning to illuminate the factors shaping the competitive landscape.
- DMG Mori Co., Ltd.
- Yamazaki Mazak Corporation
- Okuma Corporation
- Haas Automation, Inc.
- Doosan Machine Tools Co., Ltd.
- Hardinge Inc.
- JTEKT Corporation
- EMAG GmbH & Co. KG
- Matsuura Machinery Corporation
- Nakamura-Tome Precision Industry Co., Ltd.
Strategic Imperatives for Lathe Machine Industry Leadership
To thrive amid rapid technological change and shifting trade policies, industry leaders must adopt a multifaceted strategy that emphasizes agility, collaboration and customer proximity. Manufacturers should integrate modular automation architectures into their product roadmaps, enabling end users to scale capabilities incrementally without large upfront investments. By offering configurable automation packages that align with diverse production volumes and precision requirements, machine tool suppliers can capture new market segments while preserving existing manual lathe relationships.
Furthermore, investing in digital service platforms that encompass real-time monitoring, predictive maintenance and data analytics will enhance machine availability and unlock recurring revenue streams. As part of this approach, forging partnerships with software vendors and cloud infrastructure providers can accelerate platform development and ensure interoperability across heterogeneous equipment fleets. In parallel, companies should reevaluate their supply chain footprints, exploring nearshoring and local assembly options to mitigate tariff risks and reduce lead times.
Finally, fostering close collaboration with key end-use industries-ranging from aerospace OEMs to medical device startups-will provide critical insights into evolving process requirements and regulatory demands. By co-developing application-specific tooling and hosting hands-on training programs, machine tool providers can strengthen customer relationships and cultivate loyalty. These strategic imperatives, pursued in concert, position industry leaders to capture growth opportunities, optimize asset utilization and reinforce their competitive edge in a dynamic market.
Rigorous Framework Behind Our Lathe Machine Research Approach
This study drew on a combination of primary and secondary research methodologies to ensure a comprehensive and balanced perspective on the lathe machine market. Expert interviews formed the backbone of our primary research phase, engaging senior engineers, production managers and industry consultants to gather firsthand insights on technological adoption, operational challenges and emerging application areas. These dialogues provided nuanced context around factors such as sensor integration, process automation and sustainability initiatives.
In parallel, our secondary research phase examined a wide array of industry publications, technical white papers, patent filings and trade-association reports. This desk-based review allowed us to cross-validate anecdotal evidence and identify macro-level trends in manufacturing investment, supply chain realignment and regional policy developments. Publicly available regulatory documents and tariff schedules were also analyzed to understand the implications of recent trade measures and compliance requirements.
To ensure data integrity, all quantitative inputs underwent rigorous triangulation against multiple sources and validation through expert peer review. Analytical frameworks were applied consistently across segments, regions and competitive profiles, with anomalies flagged for additional investigation. Ultimately, this structured methodology underpins the report’s reliability, delivering actionable intelligence that reflects the latest market realities and equips stakeholders to make informed decisions.
Explore AI-driven insights for the Lathe Machines market with ResearchAI on our online platform, providing deeper, data-backed market analysis.
Ask ResearchAI anything
World's First Innovative Al for Market Research
Synthesizing Core Insights for the Future of Lathe Technology
The evolving interplay of automation, trade policy and end-use demands has positioned lathe machines at the forefront of precision manufacturing innovation. Through integrated control systems, data analytics and sustainable design improvements, lathe solutions are transcending their traditional roles to become intelligent production hubs. Simultaneously, recent tariff developments have underscored the importance of flexible sourcing strategies and local assembly footprints in safeguarding supply chain resilience.
Segmentation analysis highlights how targeted machine types, spindle orientations and construction formats cater to specific industry needs, from high-volume automotive components to bespoke medical instruments. Regional dynamics further reveal that manufacturers must tailor offerings to diverse market conditions-leveraging advanced automation in North America, modular solutions in emerging EMEA economies and volume-driven approaches in Asia-Pacific hubs. In this competitive landscape, leading companies differentiate by forging ecosystem partnerships, developing open-platform interfaces and prioritizing aftersales services.
Looking ahead, the most successful market participants will blend deep technical expertise with agile business models, delivering scalable automation, robust service networks and responsive supply chains. By aligning strategic investments with customer-driven innovation and regulatory clarity, stakeholders can harness the full potential of lathe technology to drive operational excellence, mitigate trade-policy disruptions and secure long-term growth.
This section provides a structured overview of the report, outlining key chapters and topics covered for easy reference in our Lathe Machines market comprehensive research report.
- Preface
- Research Methodology
- Executive Summary
- Market Overview
- Market Dynamics
- Market Insights
- Cumulative Impact of United States Tariffs 2025
- Lathe Machines Market, by Machine Type
- Lathe Machines Market, by Spindle Orientation
- Lathe Machines Market, by Construction Type
- Lathe Machines Market, by End Use Industry
- Americas Lathe Machines Market
- Europe, Middle East & Africa Lathe Machines Market
- Asia-Pacific Lathe Machines Market
- Competitive Landscape
- ResearchAI
- ResearchStatistics
- ResearchContacts
- ResearchArticles
- Appendix
- List of Figures [Total: 24]
- List of Tables [Total: 324 ]
Secure Expert Guidance and Access Your Complete Lathe Machine Report
To obtain the full market research report and gain deeper insights into lathe machine trends, contact Ketan Rohom, Associate Director, Sales & Marketing. He will guide you through the purchase process, discuss tailored solutions for your organization and provide access to exclusive data tables and expert briefings. Reach out today to secure comprehensive intelligence that will inform your strategic roadmap and drive manufacturing success.
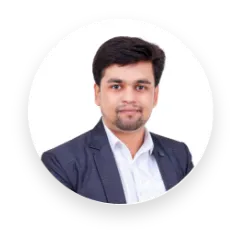
- How big is the Lathe Machines Market?
- What is the Lathe Machines Market growth?
- When do I get the report?
- In what format does this report get delivered to me?
- How long has 360iResearch been around?
- What if I have a question about your reports?
- Can I share this report with my team?
- Can I use your research in my presentation?