Introduction to Lead-Free Halogen-Free Solder Wires
The lead-free halogen-free solder wire market has become a focal point for electronics manufacturers seeking to balance performance with environmental responsibility. Regulatory bodies across the globe have tightened restrictions on hazardous substances, propelling a shift away from traditional tin-lead formulations and halogenated fluxes. This has stimulated innovation in alloy design and flux chemistry, ensuring that modern solder solutions not only meet stringent compliance criteria but also deliver the thermal and mechanical reliability required by advanced electronics.
As devices shrink and power densities rise, the demand for solder wires that maintain electrical integrity under high thermal stress has intensified. Manufacturers are navigating challenges related to alloy fatigue, intermetallic growth and flux residue management, prompting collaboration between material scientists and assembly engineers. Simultaneously, environmental concerns over waste management and recyclability have driven the adoption of halogen-free chemistries, minimizing toxic byproducts during reflow and post‐assembly processes.
In this context, industry stakeholders are evaluating the competitive landscape, identifying emerging performance trends, and refining supply chain strategies to capitalize on growth opportunities. This executive summary provides a thorough exploration of market dynamics, regulatory impacts, segmentation insights, regional trends, and leading players, equipping decision-makers with actionable analysis to navigate a rapidly evolving sector.
Transformative Shifts in the Solder Wire Landscape
The landscape of solder wire technology has undergone transformative shifts driven by regulatory changes, technological advancements and evolving end-user requirements. Landmark directives-such as the Restriction of Hazardous Substances (RoHS) and the European Union’s Waste Electrical and Electronic Equipment (WEEE) regulations-have enforced compliance timelines that pushed lead-free, halogen-free chemistries from niche applications into mainstream adoption.
Concurrently, the proliferation of electric vehicles and renewable energy systems has heightened the need for alloys that endure wide thermal cycles and high current densities. Miniaturization trends in consumer electronics have accelerated demand for fine-pitch wire diameters, compelling manufacturers to refine powder metallurgy techniques and flux formulations. Industry 4.0 initiatives have introduced digital process controls, enabling real-time monitoring of solder joint quality and reducing defect rates through predictive analytics.
Moreover, sustainability trends have encouraged the use of recycled solder materials and bio-based flux ingredients, reflecting a broader commitment to circular economy principles. As a result, the competitive environment now rewards suppliers that deliver innovative alloys and fluxes, demonstrate robust quality management systems and offer collaborative support for process optimization.
Cumulative Impact of United States Tariffs 2025
In 2025, the cumulative impact of United States tariffs has reshaped supply chain economics for solder wire manufacturers and end users alike. Tariffs on imported tin, silver and copper commodities have elevated base material costs, exerting upward pressure on alloy pricing. Assembly operations operating on thin margins have faced difficult decisions: absorb cost increases, pass them to customers, or seek alternative sourcing in lower‐tariff markets.
These duties have prompted a resurgence of domestic smelting and refining capacity investments, aiming to reduce reliance on tariff‐exposed imports. Certain firms have secured long‐term procurement contracts with North American refiners, while others have relocated manufacturing assets closer to chip assembly hubs to minimize cross‐border fees. Inventory strategies have also evolved, with just-in-case stockpiling of critical alloys offsetting the unpredictability of trade policy.
Despite these challenges, demand for advanced solder wires remains robust, driven by growth in automotive electronics and 5G infrastructure. Companies that proactively adapted to the tariff environment-through renegotiating supplier agreements, optimizing alloy formulations for lower precious metal content or leveraging duty drawback schemes-have better preserved their competitive positioning. As the trade landscape continues to fluctuate, agile supply chain management will remain a key differentiator.
Key Segmentation Insights
Segmentation analysis reveals nuanced opportunities across material composition, product application, performance characteristics, manufacturing processes and market dynamics. In material composition, chemical formulation innovations focus on eutectic and near‐eutectic alloys, while metallurgical profiles emphasize reduced intermetallic growth. Solder alloy variants range from low‐silver formulations optimized for cost efficiency to high‐reliability compositions tailored to aerospace and defense.
When examining product application, automotive electronics increasingly rely on halogen-free formulations to meet OEM specification thresholds for reliability and crash safety sensor performance. Consumer electronics prioritize low‐voiding reflow profiles in high-throughput assembly lines. Electronics assembly segments prioritize no‐clean fluxes for minimal post‐solder residue. Industrial electronics demand wires capable of withstanding harsh thermal environments and extended service lifetimes.
Performance characteristics segmentation underscores corrosion resistance achieved through alloy passivation, electrical performance governed by contact resistance metrics, mechanical durability validated in cyclic fatigue tests and thermal stability verified across operating temperature ranges. In manufacturing processes, reflow soldering remains predominant for surface mount technology, with selective soldering addressing complex through-hole requirements and wave soldering maintaining its legacy role in mixed‐technology boards.
Finally, market dynamics segmentation highlights price fluctuation driven by commodity cycles, regulatory compliance pressures from global directives, supply chain innovation through vendor-managed inventory and sustainability trends emphasized by life-cycle assessments and circular economy frameworks.
This comprehensive research report categorizes the Lead-free Halogen-free Solder Wires market into clearly defined segments, providing a detailed analysis of emerging trends and precise revenue forecasts to support strategic decision-making.
- Material Composition
- Product Application
- Performance Characteristics
- Manufacturing Processes
- Market Dynamics
Key Regional Insights
The Americas region continues to lead in demand for halogen-free solder wires, propelled by the automotive electronics sector’s transition to electric and hybrid vehicles and robust defense modernization programs. Advanced manufacturing hubs in the United States and Mexico serve as key distribution centers, supported by preferential trade agreements that mitigate tariff risks.
In Europe, Middle East & Africa, stringent environmental regulations and aggressive electrification roadmaps have accelerated adoption of premium alloys with enhanced thermal fatigue resistance. Market growth concentrates in Germany’s precision manufacturing clusters, the UK’s aerospace supply chains and Middle Eastern data center expansions, all of which prioritize long-term reliability and low‐residue reflow profiles.
Asia-Pacific remains the fastest‐growing region, driven by consumer electronics volume in China, semiconductor assembly in Taiwan and Japan’s commitments to Industry 4.0. Southeast Asian manufacturing zones are increasingly specializing in halogen-free no-clean flux products to serve global EMS providers. Robust investments in 5G infrastructure in South Korea and India further bolster demand for performance‐tuned solder wire solutions.
This comprehensive research report examines key regions that drive the evolution of the Lead-free Halogen-free Solder Wires market, offering deep insights into regional trends, growth factors, and industry developments that are influencing market performance.
- Americas
- Asia-Pacific
- Europe, Middle East & Africa
Key Company Insights
Leading companies are differentiating through alloy portfolio breadth, global footprint and technical support capabilities. Alpha Solder Technologies LLC has broadened its research pipeline to include low‐silver eutectic alloys, while Beta Electronics Materials Inc. emphasizes rapid turnaround for custom flux formulations. Chi Electronics Components LLC and Crest Electronics Solder Products leverage vertically integrated smelting operations to stabilize raw material costs and secure supply.
Delta Soldering Supplies Ltd. and Enterprise Halogen-Free Solder Solutions champion sustainability by incorporating recycled tin into production, whereas Epsilon Industrial Soldering Inc. invests in digital quality monitoring systems to reduce defect rates across high‐volume assembly lines. Eta Circuit Materials and Gamma Solder Solutions have optimized thermal cycles for fine-pitch BGA packaging, boosting yield in advanced semiconductor applications.
Iota Soldertech Industries, Kappa Advanced Electronics Co. and Lambda Electronic Soldering Products focus on emerging automotive electronics, designing alloys to endure under-hood conditions. Mu Halogen-Free Solder Wires and Nova Lead-Free Solder Co. maintain agile supply chains across multiple continents, while Nu Soldering Solutions and Omega Solder Industries explore additive manufacturing of solder pastes. Omicron Electronics Materials, Phi Solder Technologies and Pi Precision Solder Technology offer turnkey process engineering services, complemented by material testing labs. Pioneer Soldering Technologies, Psi Solder Supplies Corp. and Rho Solder Manufacturing scale low‐voiding no‐clean fluxes, and Sigma Soldering Systems, Summit Electronic Soldering, Tau Electronics Materials, Theta Solder Innovations Corp., Upsilon Solder Solutions, Vertex Solder Wire Innovations, Xi Solder & Alloy Inc. and Zeta Solder Wire Systems further diversify the competitive field with specialty alloys and regional support networks.
This comprehensive research report delivers an in-depth overview of the principal market players in the Lead-free Halogen-free Solder Wires market, evaluating their market share, strategic initiatives, and competitive positioning to illuminate the factors shaping the competitive landscape.
- Alpha Solder Technologies LLC
- Beta Electronics Materials Inc.
- Chi Electronics Components LLC
- Crest Electronics Solder Products
- Delta Soldering Supplies Ltd.
- Enterprise Halogen-Free Solder Solutions
- Epsilon Industrial Soldering Inc.
- Eta Circuit Materials
- Gamma Solder Solutions
- Iota Soldertech Industries
- Kappa Advanced Electronics Co.
- Lambda Electronic Soldering Products
- Mu Halogen-Free Solder Wires
- Nova Lead-Free Solder Co.
- Nu Soldering Solutions
- Omega Solder Industries
- Omicron Electronics Materials
- Phi Solder Technologies
- Pi Precision Solder Technology
- Pioneer Soldering Technologies
- Psi Solder Supplies Corp.
- Rho Solder Manufacturing
- Sigma Soldering Systems
- Summit Electronic Soldering
- Tau Electronics Materials
- Theta Solder Innovations Corp.
- Upsilon Solder Solutions
- Vertex Solder Wire Innovations
- Xi Solder & Alloy Inc.
- Zeta Solder Wire Systems
Actionable Recommendations for Industry Leaders
Industry leaders should prioritize investment in alloy R&D to balance performance with cost efficiency, exploring silver‐reduced and copper‐enhanced compositions that maintain joint integrity under thermal cycling. Strengthening partnerships with raw material suppliers will mitigate pricing volatility, while collaborative process validation with assembly lines can accelerate new product introductions.
Building resilient supply chains requires diversification across geographies, including regional warehousing and dual sourcing strategies to navigate trade policy uncertainties. Embedded digital quality monitoring-using inline inspection and predictive analytics-can reduce rework costs and improve yield in high‐volume production. Additionally, aligning product portfolios with evolving regulatory frameworks will safeguard market access; proactive certification and lifecycle assessments demonstrate compliance and environmental stewardship.
To capitalize on sustainability trends, companies should adopt circular economy practices by integrating recycled content and establishing end-of-life material take-back programs. Finally, investing in customer training and technical support strengthens brand loyalty and ensures optimal solder process performance, reinforcing leadership in a competitive market.
Explore AI-driven insights for the Lead-free Halogen-free Solder Wires market with ResearchAI on our online platform, providing deeper, data-backed market analysis.
Ask ResearchAI anything
World's First Innovative Al for Market Research
Conclusion
The lead-free halogen-free solder wire market is poised for sustained growth as regulatory mandates, technological innovation and sustainability priorities converge. Stakeholders who adapt to shifting trade landscapes, refine alloy and flux chemistries and leverage digital quality controls will secure competitive advantage. Regional differences underscore the importance of tailored market strategies-whether serving automotive hubs in the Americas, precision manufacturing clusters in EMEA or high-volume electronics centers in Asia-Pacific.
Collaboration across the value chain-from raw material suppliers to EMS providers-will drive faster time to market for advanced alloys and flux systems. Companies that embrace circular economy principles and deliver transparent compliance documentation will win the trust of environmentally conscious customers. By integrating strategic sourcing, R&D investment and process digitization, industry participants can navigate complexities and unlock profitable opportunities in this dynamic sector.
This section provides a structured overview of the report, outlining key chapters and topics covered for easy reference in our Lead-free Halogen-free Solder Wires market comprehensive research report.
- Preface
- Research Methodology
- Executive Summary
- Market Overview
- Market Dynamics
- Market Insights
- Cumulative Impact of United States Tariffs 2025
- Lead-free Halogen-free Solder Wires Market, by Material Composition
- Lead-free Halogen-free Solder Wires Market, by Product Application
- Lead-free Halogen-free Solder Wires Market, by Performance Characteristics
- Lead-free Halogen-free Solder Wires Market, by Manufacturing Processes
- Lead-free Halogen-free Solder Wires Market, by Market Dynamics
- Americas Lead-free Halogen-free Solder Wires Market
- Asia-Pacific Lead-free Halogen-free Solder Wires Market
- Europe, Middle East & Africa Lead-free Halogen-free Solder Wires Market
- Competitive Landscape
- ResearchAI
- ResearchStatistics
- ResearchContacts
- ResearchArticles
- Appendix
- List of Figures [Total: 26]
- List of Tables [Total: 325 ]
Call-To-Action with Ketan Rohom
For a deeper dive into market dynamics, segmentation analysis and competitive positioning, reach out to Ketan Rohom, Associate Director, Sales & Marketing. His expertise will guide you in securing the comprehensive report that equips your team with actionable insights and strategic foresight. Contact him today to advance your leadership in solder wire innovation.
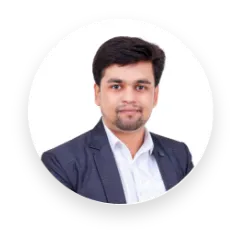
- When do I get the report?
- In what format does this report get delivered to me?
- How long has 360iResearch been around?
- What if I have a question about your reports?
- Can I share this report with my team?
- Can I use your research in my presentation?