Introduction to Lead-Free Pre-Coated Preform Solder
In an era defined by stringent environmental regulations and rapid technological advancements, the transition toward lead-free pre-coated preform solder has become a cornerstone of electronic assembly. These specialized solder preforms-meticulously engineered to meet exacting geometric specifications-offer a streamlined approach to joining components, eliminating the need for manual solder paste application and reducing process variability. By integrating pre-coated preforms into modern manufacturing workflows, organizations address critical demands for consistency, reliability, and regulatory compliance. Moreover, the elimination of lead aligns with global sustainability initiatives, reinforcing corporate commitments to eco-friendly practices. As manufacturers navigate miniaturization trends, high-density circuit integration, and ever-tightening performance standards, lead-free pre-coated preforms emerge as a strategic enabler, delivering precision, repeatability, and reduced rework rates. This introduction lays the foundation for exploring transformative industry shifts, tariff implications, segmentation nuances, and actionable strategies that will define the competitive landscape.
Transformative Shifts Redefining the Preform Solder Landscape
Over the past decade, the electronics industry has undergone transformative shifts propelled by the convergence of digitalization and sustainability. Internet of Things expansion and the proliferation of electric vehicles have driven demand for high-reliability solder solutions capable of withstanding thermal cycling and mechanical stress. Simultaneously, global regulatory bodies have accelerated mandates to eliminate hazardous substances, further compelling manufacturers to adopt lead-free alternatives. Materials science breakthroughs have yielded advanced alloy compositions-ranging from tin-silver-copper blends to innovative tin-zinc formulations-that balance melting point optimization with mechanical robustness.
On the manufacturing front, automation and artificial intelligence integration are redefining soldering workflows. Reflow ovens equipped with real-time thermal profiling and selective soldering cells guided by machine vision ensure precise heat application, minimizing defects. Wave soldering systems now incorporate closed-loop feedback to adapt to board complexity, while mini-wave and dip soldering variants offer targeted processing for sensitive assemblies. Sustainability considerations have also spurred process efficiency improvements: solvent-free flux chemistries and localized solder application techniques reduce waste and energy consumption. Collectively, these shifts underscore the dynamic interplay between technological innovation and regulatory imperatives shaping the preform solder landscape.
Cumulative Impact of U.S. Tariffs Scheduled for 2025
With the introduction of new U.S. tariffs scheduled for 2025, import costs for electronic solder products will undergo significant upward pressure. Manufacturers heavily reliant on overseas alloy suppliers are reassessing sourcing strategies to mitigate margin erosion. Many are exploring nearshoring options and forging partnerships with domestic producers to stabilize supply chains and reduce exposure to cross-border duties.
In response, global vendors are evaluating tariff-passing strategies versus absorption models, balancing short-term profitability with long-term customer relationships. Some suppliers are accelerating investments in local production capabilities, leveraging regional free trade agreements to circumvent duties. Meanwhile, OEMs are conducting detailed cost-benefit analyses to determine whether reengineering assembly lines for alternate solder compositions could offset tariff-driven cost increases.
This tariff environment will likely catalyze strategic alliances, mergers, and acquisitions as companies seek to consolidate capabilities and diversify alloy sources. By proactively adapting to the evolving trade landscape, industry participants can maintain competitive cost structures and ensure uninterrupted access to high-performance, lead-free solder solutions.
Key Segmentation Insights Across Ten Dimensions
Analysis by product type reveals that solder bar categories continue to serve high-volume applications requiring bulk material flow, while solder paste types cater to fine-pitch surface-mount assemblies demanding precise deposition. Wire solder variants, often pre-tinned, facilitate selective touch-up operations in repair environments. Transitioning to the manufacturing process dimension, reflow soldering techniques dominate surface-mount production, whereas selective soldering procedures-comprising dip soldering and mini-wave processes-address complex through-hole and mixed-technology boards. Wave soldering methods remain integral for robust, high-throughput PCB assembly lines.
Turning to application segmentation, automotive electronics stands out, with infotainment systems and safety systems driving demand for lead-free preforms. Consumer electronics segments, including computing devices, home appliances, and mobile devices, prioritize miniaturization and high joint integrity. In industrial electronics, precision instruments and robotics systems impose stringent solder quality requirements to withstand harsh operating conditions. Renewable energy sectors-particularly solar panels and wind turbines-demand durable, corrosion-resistant solder joints for long life cycles.
End-user industry insights underscore the aerospace community’s need for avionics systems and radar and communications equipment, while healthcare applications such as medical imaging and patient monitoring devices require biocompatible, reliable solder connections. Solder alloy composition preferences vary, with tin-copper alloys offering cost advantages, tin-silver-copper blends balancing performance, and tin-zinc compositions emerging for specialized low-temperature applications. Form factor segmentation highlights preform discs, rings, and washers designed for distinct joint geometries. Technology utilization differentiates between surface-mount and through-hole technologies, each with unique thermal profiles and solder volume requirements. Production volume profiles span high-volume production environments to prototype manufacturing settings, and customer base size ranges from large enterprises with standardized processes to small and medium enterprises prioritizing flexibility. Finally, innovation and development focus on eco-friendly solder alloys aligns with sustainability goals, while high-temperature alloy variants serve demanding automotive and industrial applications.
This comprehensive research report categorizes the Lead-free Pre-coated Preform Solder market into clearly defined segments, providing a detailed analysis of emerging trends and precise revenue forecasts to support strategic decision-making.
- Product Type
- Manufacturing Process
- Application
- End-User Industry
- Solder Alloy Compositions
- Form Factor
- Technology Utilization
- Production Volume
- Customer Base Size
- Innovation & Development Focus
Key Regional Insights Shaping Adoption and Growth
The Americas region benefits from established electronics manufacturing hubs and a strong network of alloy producers in North America, supporting swift adoption of lead-free preforms. Market maturity in the United States and Canada drives demand for specialization in automotive and aerospace applications, bolstered by ongoing investments in EV and defense sectors. In contrast, Europe, the Middle East, and Africa combine rigorous environmental regulations with diverse manufacturing bases; the European Union’s RoHS directives and REACH standards accelerate lead-free transitions, while emerging markets in the Middle East and Africa present nascent opportunities for industrial electronics and renewable energy applications.
Asia-Pacific remains the largest consumer of pre-coated preform solder, propelled by robust electronics assembly in China, South Korea, Japan, and Southeast Asia. High-volume consumer electronics production, coupled with rapid growth in solar panel and electric vehicle manufacturing, underpins strong demand. Regional alliances and trade partnerships within ASEAN and the Comprehensive and Progressive Agreement for Trans-Pacific Partnership further facilitate tariff reductions, reinforcing Asia-Pacific as a critical nexus for global solder material flows.
This comprehensive research report examines key regions that drive the evolution of the Lead-free Pre-coated Preform Solder market, offering deep insights into regional trends, growth factors, and industry developments that are influencing market performance.
- Americas
- Asia-Pacific
- Europe, Middle East & Africa
Key Company Insights Driving Innovation and Service Excellence
Leading the innovation curve, AIM Solder has introduced novel flux chemistries and precision-cut preforms that enhance wetting consistency and joint reliability. Alpha Assembly Solutions leverages its global footprint to provide localized alloy blending services and technical support for high-mix, low-volume environments. Duksan Technopia Co., Ltd. stands out for its proprietary tin-silver-copper formulations tailored to automotive and aerospace applications. Henkel Corporation combines its adhesive and surface treatment expertise to deliver integrated soldering solutions optimized for end-to-end assembly processes.
Heraeus Holding GmbH invests heavily in materials research, advancing high-temperature and corrosion-resistant solder alloys for renewable energy applications. Indium Corporation’s pre-coated preforms target thermal management challenges in LED and power electronics, while Kester focuses on process control technologies that reduce solder voiding. Nathan Trotter & Co., Inc. offers customized alloy services and holds strategic partnerships with defense contractors to meet rigorous military specifications. Nihon Superior Co., Ltd. and Senju Metal Industry Co., Ltd. bring decades of experience in alloy refinement and preform manufacturing, supporting customers across multiple industries with certified lead-free and high-reliability offerings.
This comprehensive research report delivers an in-depth overview of the principal market players in the Lead-free Pre-coated Preform Solder market, evaluating their market share, strategic initiatives, and competitive positioning to illuminate the factors shaping the competitive landscape.
- AIM Solder
- Alpha Assembly Solutions
- Duksan Technopia Co., Ltd.
- Henkel Corporation
- Heraeus Holding GmbH
- Indium Corporation
- Kester
- Nathan Trotter & Co., Inc.
- Nihon Superior Co., Ltd.
- Senju Metal Industry Co., Ltd.
Actionable Recommendations for Industry Leaders
Industry leaders should prioritize strategic alloy research to develop next-generation tin-silver-copper and eco-friendly compositions that meet emerging thermal and mechanical demands. Collaborations with research institutions and universities can accelerate material discovery and validation processes. In parallel, investing in localized production footprints-whether through joint ventures or brownfield expansions-will mitigate trade-related cost pressures and enhance supply security.
Manufacturers must also adopt advanced process control systems integrating machine vision and closed-loop feedback to ensure consistent solder joint integrity. Embracing digital twins of soldering lines can facilitate predictive maintenance and optimize thermal profiles across mixed-technology assemblies. Furthermore, aligning sustainability initiatives with product roadmaps-such as certifying solder alloys under globally recognized green chemistry standards-will strengthen value propositions for environmentally conscious OEMs.
To capture emerging end-use markets, companies should tailor preform geometries and alloy selections to specific application requirements, from high-volume consumer electronics to mission-critical aerospace systems. Cultivating deep technical partnerships with OEMs and CEMs, supported by value-added services like joint failure analysis and process training, will differentiate offerings in a competitive landscape. Finally, agile pricing strategies-balancing cost recovery against long-term customer relationships-will be essential for navigating tariff dynamics and fluctuating raw material costs.
Explore AI-driven insights for the Lead-free Pre-coated Preform Solder market with ResearchAI on our online platform, providing deeper, data-backed market analysis.
Ask ResearchAI anything
World's First Innovative Al for Market Research
Conclusion: Charting the Future of Lead-Free Preform Solder
As the market evolves, organizations that integrate material science innovation, process automation, and strategic supply chain adjustments will secure a competitive edge. The convergence of stringent environmental mandates, advanced manufacturing techniques, and shifting trade policies creates both challenges and opportunities for solder material providers. By leveraging the insights outlined above-ranging from segmentation nuances and regional dynamics to tariff impacts and competitive benchmarks-stakeholders can formulate robust strategies that address present demands and anticipate future trends.
Proactive alignment of R&D efforts with customer application needs, combined with investments in digital transformation and sustainability certifications, will drive long-term growth. Engaging in cross-industry collaborations, maintaining agile supply networks, and committing to continuous process improvement are critical. Ultimately, the organizations that demonstrate foresight in adjusting to regulatory changes, embracing new technologies, and delivering tailored, high-performance solder solutions will emerge as leaders in the lead-free pre-coated preform solder market.
This section provides a structured overview of the report, outlining key chapters and topics covered for easy reference in our Lead-free Pre-coated Preform Solder market comprehensive research report.
- Preface
- Research Methodology
- Executive Summary
- Market Overview
- Market Dynamics
- Market Insights
- Cumulative Impact of United States Tariffs 2025
- Lead-free Pre-coated Preform Solder Market, by Product Type
- Lead-free Pre-coated Preform Solder Market, by Manufacturing Process
- Lead-free Pre-coated Preform Solder Market, by Application
- Lead-free Pre-coated Preform Solder Market, by End-User Industry
- Lead-free Pre-coated Preform Solder Market, by Solder Alloy Compositions
- Lead-free Pre-coated Preform Solder Market, by Form Factor
- Lead-free Pre-coated Preform Solder Market, by Technology Utilization
- Lead-free Pre-coated Preform Solder Market, by Production Volume
- Lead-free Pre-coated Preform Solder Market, by Customer Base Size
- Lead-free Pre-coated Preform Solder Market, by Innovation & Development Focus
- Americas Lead-free Pre-coated Preform Solder Market
- Asia-Pacific Lead-free Pre-coated Preform Solder Market
- Europe, Middle East & Africa Lead-free Pre-coated Preform Solder Market
- Competitive Landscape
- ResearchAI
- ResearchStatistics
- ResearchContacts
- ResearchArticles
- Appendix
- List of Figures [Total: 36]
- List of Tables [Total: 768 ]
Call-To-Action: Engage Ketan Rohom to Access the Full Report
To gain comprehensive access to detailed analyses, case studies, and supplier evaluations, please contact Ketan Rohom, Associate Director, Sales & Marketing. He can provide personalized guidance and facilitate purchase of the full market research report addressing your strategic objectives and operational requirements.
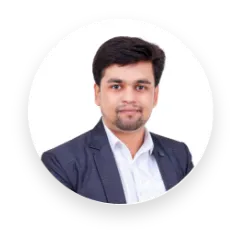
- When do I get the report?
- In what format does this report get delivered to me?
- How long has 360iResearch been around?
- What if I have a question about your reports?
- Can I share this report with my team?
- Can I use your research in my presentation?