Introduction to the Lift Truck Stamping Die Market
The lift truck stamping die market plays a pivotal role in the global manufacturing landscape by enabling the mass production of precision components essential for material handling equipment. These dies are the heart of the stamping process, converting raw metal sheets into intricate parts that ensure the structural integrity, performance, and safety of lift trucks. As industries worldwide demand greater efficiency and reliability, the design, development, and deployment of advanced stamping dies have become critical levers for competitive differentiation.
Today's lift truck stamping die sector is characterized by a melding of traditional mechanical expertise and cutting-edge technologies. From the selection of high-strength alloys to the integration of automation in fabrication, industry stakeholders must navigate a complex web of material properties, production techniques, and supply chain dynamics. This introduction lays the groundwork for a deeper examination of the market’s transformative shifts, regulatory pressures, segmentation insights, and strategic imperatives. As we progress, readers will gain a comprehensive understanding of how emerging trends are reshaping the industry and what leading organizations are doing to capitalize on new opportunities.
Transformational Shifts Reshaping the Lift Truck Stamping Die Landscape
Over the past decade, the lift truck stamping die market has undergone a series of transformative shifts driven by digitalization, advanced materials, and an intensified focus on sustainability. With Industry 4.0 frameworks gaining traction, smart die systems equipped with embedded sensors now monitor wear, temperature and force in real time, enabling predictive maintenance and minimizing downtime. Concurrently, the adoption of finite element analysis and simulation tools has accelerated die design cycles, reducing time-to-market and enhancing dimensional accuracy.
Material innovation has also reshuffled traditional paradigms. High-strength aluminum alloys such as 6061 and 7075 are increasingly favored for their strength-to-weight ratios, while the versatility of stainless steel and hot-rolled steel continues to support applications requiring corrosion resistance and durability. In parallel, tightening environmental regulations and corporate sustainability targets have spurred investments in energy-efficient hydraulic and magnetic workholding systems, further optimizing resource utilization.
Moreover, the convergence of additive manufacturing with conventional stamping techniques has unlocked hybrid processes that streamline tooling production and enable rapid prototyping. In turn, these advancements are compelling die manufacturers to retool operations, upskill workforces and establish digital ecosystems that connect die shops, suppliers and end users. Collectively, these transformative forces are redefining value chains and setting new benchmarks for quality, flexibility and operational excellence.
Assessing the Cumulative Impact of US Tariffs in 2025 on Lift Truck Stamping Die
The implementation of United States tariffs in 2025 has exerted significant pressure across every facet of the lift truck stamping die market. Tariffs on imported raw materials, notably cold-rolled and hot-rolled steel, have elevated input costs, compelling manufacturers to reassess sourcing strategies and negotiate long-term contracts. At the same time, aluminum imports subject to higher duties have triggered similar concerns for producers relying on 6061 and 7075 alloys.
To mitigate these headwinds, many organizations are diversifying supply chains, increasing engagement with domestic steel mills and forging strategic alliances with regional casters. Such initiatives aim to secure material availability while preserving margin stability. Furthermore, heightened customs scrutiny and evolving trade policies have underscored the importance of robust compliance frameworks, prompting die producers to invest in advanced tariffs management software and dedicated trade teams.
The tariff-driven landscape has also accelerated discussions around onshoring and nearshoring. By relocating critical tooling operations closer to OEM assembly plants, stakeholders can not only reduce exposure to cross-border duties but also benefit from improved lead times and enhanced collaboration. Ultimately, the cumulative impact of these trade measures is fostering resilience and adaptability among die manufacturers, reshaping procurement, production and distribution strategies.
Key Segmentation Insights for the Lift Truck Stamping Die Market
A nuanced understanding of market segmentation illuminates the varied demands and growth drivers within the lift truck stamping die sector. Material Type segmentation reveals a bifurcation between aluminum and steel, with the former dominated by high-performance grades such as 6061 and 7075, and the latter encompassing cold-rolled, hot-rolled and stainless steel variants that cater to diverse strength and corrosion requirements. In Application segmentation, aerospace and automotive industries drive demand for fuselage components, wing structures, body parts and engine assemblies, while the consumer electronics segment seeks precision battery enclosures and casing components, and home appliances rely on robust motor housings and panel enclosures.
End-User Industry segmentation distinguishes among construction, manufacturing and mining sectors, each with specialized needs: commercial and residential construction demand load-bearing bracketry, manufacturing aftermarket and OEM channels require replacement dies and original tooling respectively, and surface and underground mining operations depend on heavy-duty die designs for earth-moving equipment. Technology Type segmentation highlights the adoption of gang dies, progressive dies and transfer dies: gang die configurations excel in blanking and fabrication, progressive dies leverage compound and sequential operations, and transfer dies utilize hydraulic and mechanical press systems. Capacity segmentation differentiates high, medium and low-capacity stamping, correlating large-scale production with high-capacity tooling, moderate-scale runs with medium-capacity dies, and bespoke or small batch outputs with low-capacity stamping solutions. Finally, Workholding Systems segmentation identifies hydraulic and magnetic systems, where hydraulic fixture and hole clamping ensure precision under extreme loads, and magnetic systems-both electro-permanent and permanent-offer rapid part changeovers and minimal mechanical stress.
This comprehensive research report categorizes the Lift Truck Stamping Die market into clearly defined segments, providing a detailed analysis of emerging trends and precise revenue forecasts to support strategic decision-making.
- Material Type
- Application
- End-User Industry
- Technology Type
- Capacity
- Workholding Systems
Regional Dynamics and Insights in the Lift Truck Stamping Die Sector
Regional dynamics within the lift truck stamping die market illustrate distinct priorities and competitive landscapes. In the Americas, robust infrastructure investment and a healthy manufacturing sector drive demand for advanced die solutions, while proximity to major OEMs encourages collaborative product development and just-in-time delivery models. Trade policy volatility has led North American die makers to streamline domestic sourcing and cultivate redundancy in supplier networks.
Across Europe, the Middle East and Africa, stringent safety and emissions regulations require stamping dies that can consistently produce lightweight yet durable components. This region’s focus on sustainability has catalyzed the use of stainless and high-strength steels, as well as closed-loop recycling processes. Collaborative research initiatives between member states have accelerated the integration of smart die technologies into traditional metalworking hubs.
In the Asia-Pacific region, rapid industrialization and the expansion of automotive and consumer electronics manufacturing underpin demand for high-capacity stamping dies. Local government incentives and economic partnerships have bolstered die production capacity, while cost competitiveness remains a key differentiator. Manufacturers in this region increasingly adopt progressive and transfer die technologies to meet the scale and speed requirements of large-volume producers.
This comprehensive research report examines key regions that drive the evolution of the Lift Truck Stamping Die market, offering deep insights into regional trends, growth factors, and industry developments that are influencing market performance.
- Americas
- Asia-Pacific
- Europe, Middle East & Africa
Major Players Driving the Lift Truck Stamping Die Market
Major global players are driving innovation, scale and strategic direction in the lift truck stamping die market. Aisin Corporation continues to advance die automation and wear-resistant coatings, while Dana Incorporated leverages its materials science expertise to optimize aluminum and steel die alloys for weight reduction and extended tool life. FTech Inc. emphasizes integrated die design platforms that shorten development cycles, and Gestamp Automoción capitalizes on high-volume progressive die systems for the automotive sector.
Hitachi Metals, Ltd. focuses on specialty steel formulations that enhance fatigue resistance in stamping dies, and JBM Group invests in additive-assisted die manufacturing for rapid prototyping. Kobe Steel, Ltd. (Kobelco) integrates digital quality control into its die production lines, while Magna International Inc. and Martinrea International Inc. deploy modular tooling concepts to serve diverse OEM requirements. Nippon Steel Corporation advances workholding innovations, and Noel Welding and Fabrication delivers bespoke die assemblies for niche applications.
Shiloh Industries, Inc. develops hybrid die solutions that combine stamping with secondary machining, and SMS Group GmbH drives large-scale transfer die installations for heavy equipment manufacturers. Tohken Co., Ltd. focuses on compact, high-precision die designs, whereas Tower International, Inc. emphasizes global service networks and aftermarket support, ensuring consistent die performance across multiple regions.
This comprehensive research report delivers an in-depth overview of the principal market players in the Lift Truck Stamping Die market, evaluating their market share, strategic initiatives, and competitive positioning to illuminate the factors shaping the competitive landscape.
- Aisin Corporation
- Dana Incorporated
- FTech Inc.
- Gestamp Automoción
- Hitachi Metals, Ltd.
- JBM Group
- Kobe Steel, Ltd. (Kobelco)
- Magna International Inc.
- Martinrea International Inc.
- Nippon Steel Corporation
- Noel Welding and Fabrication
- Shiloh Industries, Inc.
- SMS Group GmbH
- Tohken Co., Ltd.
- Tower International, Inc.
Actionable Recommendations for Industry Leaders
To navigate the evolving market landscape, industry leaders must adopt a multifaceted strategy that balances innovation with operational excellence. First, investing in digital die management systems will enable real-time monitoring of tool health and performance, reducing unplanned downtime and extending die life. Second, establishing flexible supply chains that incorporate both domestic and regional material sources can mitigate tariff-related risks and ensure continuity of production. Third, collaborating closely with end users and OEMs to co-develop application-specific die solutions will foster long-term partnerships and align tooling capabilities with emerging vehicle architectures.
Moreover, prioritizing workforce development through targeted training in advanced die technologies, including simulation software and sensor integration, will build the talent base required for next-generation manufacturing. Finally, embedding sustainability metrics into die design and production processes-such as lifecycle carbon assessment and closed-loop material recycling-will not only satisfy regulatory mandates but also resonate with environmentally conscious customers.
Explore AI-driven insights for the Lift Truck Stamping Die market with ResearchAI on our online platform, providing deeper, data-backed market analysis.
Ask ResearchAI anything
World's First Innovative Al for Market Research
Conclusion
The lift truck stamping die market stands at a crossroads, shaped by technological innovation, regulatory pressures and evolving end-user demands. Organizations that leverage digitalization, diversify supply chains and forge collaborative partnerships will outperform peers in efficiency, cost management and product quality. As the industry continues to embrace sustainability and smart manufacturing, stakeholders who proactively integrate these principles into tooling design and production will secure a competitive edge. By aligning strategic initiatives with market realities, die producers can deliver the precision, reliability and adaptability that lift truck OEMs require.
This section provides a structured overview of the report, outlining key chapters and topics covered for easy reference in our Lift Truck Stamping Die market comprehensive research report.
- Preface
- Research Methodology
- Executive Summary
- Market Overview
- Market Dynamics
- Market Insights
- Cumulative Impact of United States Tariffs 2025
- Lift Truck Stamping Die Market, by Material Type
- Lift Truck Stamping Die Market, by Application
- Lift Truck Stamping Die Market, by End-User Industry
- Lift Truck Stamping Die Market, by Technology Type
- Lift Truck Stamping Die Market, by Capacity
- Lift Truck Stamping Die Market, by Workholding Systems
- Americas Lift Truck Stamping Die Market
- Asia-Pacific Lift Truck Stamping Die Market
- Europe, Middle East & Africa Lift Truck Stamping Die Market
- Competitive Landscape
- ResearchAI
- ResearchStatistics
- ResearchContacts
- ResearchArticles
- Appendix
- List of Figures [Total: 28]
- List of Tables [Total: 1026 ]
Call to Action
Unlock the full potential of your lift truck stamping die operations by acquiring the comprehensive market research report. To explore detailed insights, strategic frameworks and tailored recommendations, contact Ketan Rohom (Associate Director, Sales & Marketing at 360iResearch) today and elevate your tooling strategy.
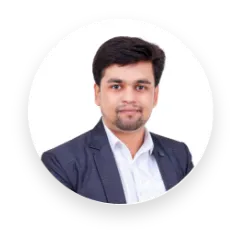
- When do I get the report?
- In what format does this report get delivered to me?
- How long has 360iResearch been around?
- What if I have a question about your reports?
- Can I share this report with my team?
- Can I use your research in my presentation?