Unveiling the Critical Role of Linear Encoders in Precision Machine Tool Operations and Their Strategic Importance in Modern CNC Machining Environments
In today’s precision-driven manufacturing environment, linear encoders have emerged as indispensable components within CNC machining systems, delivering the critical feedback necessary for sub-micron accuracy and repeatable motion control. These devices translate physical displacement into electrical signals, enabling sophisticated machine tool control algorithms to maintain tight tolerances in high-speed milling, turning, and grinding applications. As production requirements evolve, the performance expectations for linear encoders have intensified, demanding enhancements in resolution, environmental resilience, and seamless integration with digital architectures.
Transitioning from legacy analogue solutions to advanced digital feedback systems, manufacturers are leveraging linear encoders to underpin innovations such as closed-loop control and adaptive machining processes. This shift is driven by the convergence of automation, artificial intelligence, and data analytics, which together propel continuous improvement in machine utilization and product quality. Against this backdrop, the role of linear encoders extends beyond simple position sensing, positioning them as foundational technologies in the quest for smarter, more responsive, and highly efficient manufacturing operations.
Charting the Technological Revolution Driving Smart Manufacturing Through Advanced Encoder Integration and Industry 4.0 Adoption in Machine Tool Automation
The landscape of linear encoders is undergoing a profound metamorphosis as Industry 4.0 and smart factory initiatives reshape expectations for motion feedback systems. Encoders are now embedded within interconnected ecosystems, providing real-time data streams that feed digital twins, predictive maintenance platforms, and cloud analytics. This evolution has prompted vendors to embed communication protocols such as EtherCAT and PROFINET directly into encoder firmware, ensuring plug-and-play connectivity within diverse machine tool architectures.
In parallel, performance benchmarks continue to rise, with optical scales achieving sub-micron resolution and magnetic tape encoders offering exceptional ruggedness in harsh machining environments. Developments in non-contact sensing, such as capacitive and inductive technologies, have expanded the application envelope, enabling feedback solutions that resist contamination, temperature fluctuations, and mechanical shock. Manufacturing stakeholders are gravitating toward absolute encoder variants to eliminate homing cycles and enhance operational safety, reinforcing the trend toward fully deterministic motion control.
Moreover, the synergy between CNC machining centers and collaborative robots has spurred multi-disciplinary collaboration among encoder manufacturers, system integrators, and OEMs. These partnerships have yielded turnkey packages that integrate condition monitoring sensors, vibration analysis, and closed-loop control functions within unified platforms. By marrying high-precision feedback with advanced diagnostics, these next-generation encoders are redefining the boundaries of machine tool performance and reliability, fueling new standards for productivity and uptime.
Evaluating the Compound Effects of the 2025 United States Section 301 Tariff Increases on CNC Machining Components and Supply Chain Resilience Dynamics
The Biden administration’s decision to finalize Section 301 tariff hikes on select imports from China has introduced notable cost pressures for machine tool builders and end users reliant on encoder technologies imported from Asia. Effective January 1, 2025, duties on semiconductor materials rose to 50%, while certain tungsten products and wafers saw a 25% levy. These measures aim to counter unfair industrial practices and bolster domestic supply chains, yet they carry implications for the procurement and total cost of ownership of high-precision encoder components used in CNC machining systems.
Concurrently, the USTR expanded an exclusion process for industrial machinery classified under specific HTS subheadings, offering temporary relief through May 31, 2025, for select machine tool equipment. This provision allows certain encoder scales and related assemblies to petition for exemption, mitigating the immediate impact of tariff increases on critical production assets. However, stakeholders must navigate complex regulatory requirements to secure these exclusions and incorporate potential duty reinstatements into their strategic sourcing plans.
In aggregate, the 2025 tariff adjustments underscore the need for diversification of supplier networks, increased domestic manufacturing capabilities, and proactive tariff mitigation strategies. By balancing short-term exclusion opportunities with long-term investments in local production and alternative sourcing, industry participants can preserve cost competitiveness and supply chain resilience amid an evolving geopolitical and trade policy environment.
Decoding Market Segmentation to Reveal How Technology Types Product Variants End Users Materials Outputs Accuracies and Channels Shape Encoder Demand
The linear encoder market’s segmentation across technology modalities reveals distinct value propositions that cater to diverse operational demands. Capacitive systems deliver high immunity to contaminants through near-field sensing, while inductive encoders excel in environments with conductive or magnetic debris. Magnetic solutions strike a balance between affordability and robustness, and optical scales continue to set the benchmark for ultimate resolution in precision-critical machining applications.
Divergence in product type segmentation underscores the differing priorities between absolute and incremental feedback architectures. Absolute encoders provide unique positional data from startup, eliminating homing procedures and enhancing safety in automated processes. Incremental variants offer cost-effective solutions with straightforward integration into existing control loops, appealing to applications where homing cycles are tolerable and budget constraints are paramount.
End user segmentation highlights the aerospace sector’s demand for aerospace-grade materials and multi-axis synchronization, the automotive industry’s focus on high-throughput assembly lines, the electronics market’s requirement for sub-micron metrology in semiconductor fabrication, and the machine tool domain’s need for specialized CNC milling, turning, and grinding feedback packages. Each vertical imposes unique performance and reliability prerequisites on encoder solutions.
Material-based segmentation distinguishes glass scales for thermal stability and ultra-low linear expansion, magnetic strips for flexibility and cost efficiency, and metal tape for rugged, long-travel applications. Output connectivity varies from legacy analogue signals suitable for simple retrofits to sophisticated digital interfaces enabling advanced diagnostics and closed-loop feedback. Precision tiers further differentiate high-precision encoders, delivering sub-micron accuracy for the most demanding tasks, from standard-precision options optimized for general-purpose motion control.
Finally, segmentation by sales channels illustrates the strategic significance of direct sales relationships in high-value, custom-engineered projects, the role of authorized and third-party distributors in broadening market access, and the burgeoning influence of online channels-both company websites and e-commerce platforms-in democratizing access to standardized encoder products and accelerating order fulfillment.
This comprehensive research report categorizes the Linear Encoders for Machine Tools & CNC Machining market into clearly defined segments, providing a detailed analysis of emerging trends and precise revenue forecasts to support strategic decision-making.
- Technology
- Product Type
- End User
- Scale Material
- Output
- Accuracy
- Sales Channel
Comparative Regional Dynamics Highlighting How Americas EMEA and Asia Pacific Strategies Influence Linear Encoder Adoption and Manufacturing Competitiveness
In the Americas, intensified nearshoring initiatives have been galvanized by the CHIPS and Science Act’s substantial subsidies for semiconductor research and manufacturing. These incentives, complemented by provisions such as the Advanced Manufacturing Tax Credit, are catalyzing regional investment in encoder production capabilities, forging a more resilient North American supply chain and reducing dependency on foreign imports. U.S. machine tool OEMs are actively pursuing partnerships with domestic sensor manufacturers to capitalize on favorable policy frameworks and secure a localized component ecosystem.
Within Europe, Middle East & Africa, the European Chips Act has galvanized €43 billion of policy-driven investments aimed at doubling the EU’s global semiconductor market share by 2030. This commitment extends to creating integrated production facilities and research pilot lines, which in turn stimulate demand for high-performance encoder technologies within the automotive, aerospace, and industrial automation sectors. Member states are coordinating supply chain alert mechanisms and crisis response initiatives to safeguard strategic manufacturing capabilities and enforce functional safety standards across connected machinery.
Across Asia-Pacific, legacy policies such as Made in China 2025 and Japan’s Society 5.0 have laid the groundwork for cutting-edge manufacturing ecosystems emphasizing intelligent automation and advanced materials. Despite challenges in mastering high-end machine tools domestically, Chinese equipment makers are closing quality gaps through targeted R&D and collaborative ventures with global technology providers. In parallel, South Korea and Japan are extending smart factory grants and robotics subsidies to drive local adoption of digital feedback systems, reinforcing the region’s status as a manufacturing innovation hub.
This comprehensive research report examines key regions that drive the evolution of the Linear Encoders for Machine Tools & CNC Machining market, offering deep insights into regional trends, growth factors, and industry developments that are influencing market performance.
- Americas
- Europe, Middle East & Africa
- Asia-Pacific
Insight into Leading Encoder Manufacturers and Industry Innovators Shaping Product Portfolios Partnerships and Technological Roadmaps in CNC Applications
Leading encoder manufacturers are intensifying efforts to expand their product portfolios and embed more advanced functionalities into their feedback devices. Renishaw has introduced extended-length FORTiS enclosed linear absolute scales, accommodating machine tool travels up to 4.24 meters while maintaining high environmental resistance and sub-micron accuracy. This enhancement reflects Renishaw’s strategy to capture larger-scale CNC applications in automotive casting and aerospace fabrication environments.
HEIDENHAIN has showcased its latest motion control innovations at major industry events such as Automate 2025, unveiling the KCI 120 Dplus dual encoder, which integrates downstream gearbox feedback in a single compact unit, and the EnDat 3 interface, supporting high-speed digital communication, daisy-chain bus topologies, and functional safety up to SIL 3. These introductions underscore the brand’s commitment to fusing reliable position measurement with Industry 4.0-ready connectivity, reducing cabling complexity and enabling advanced diagnostics within robotic automation cells.
Across the competitive landscape, other key players are forging strategic partnerships to accelerate technology integration and market reach. Companies specializing in sensor fusion and edge analytics are collaborating with encoder OEMs to embed predictive maintenance algorithms directly within encoder modules. Simultaneously, software providers are developing universal drivers and cloud-enabled monitoring platforms that abstract encoder data for easy consumption by machine builders and end users alike. Together, these initiatives reflect a collective industry momentum toward smarter, more connected encoder solutions that anticipate and respond to evolving manufacturing demands.
This comprehensive research report delivers an in-depth overview of the principal market players in the Linear Encoders for Machine Tools & CNC Machining market, evaluating their market share, strategic initiatives, and competitive positioning to illuminate the factors shaping the competitive landscape.
- Dr. Johannes Heidenhain GmbH
- Renishaw plc
- Mitutoyo Corporation
- Keyence Corporation
- Micro-Epsilon Messtechnik GmbH & Co. KG
- SIKO GmbH
- Hexagon AB
- Baumer Holding AG
- Leine & Linde AB
- NOVOTECHNIK Messwertaufnehmer OHG
Actionable Strategic Pathways for Industry Stakeholders to Navigate Tariffs Drive Innovation and Leverage Market Segments in a Disruptive Manufacturing Landscape
Industry leaders should prioritize diversification of supply chains by qualifying multiple encoder suppliers across geographies, leveraging tariff exclusion mechanisms while building domestic partnerships to mitigate future trade policy volatility. Establishing mutual R&D ventures can expedite the localization of critical encoder components, reducing lead times and enhancing cost predictability.
Investing in smart encoder technologies with integrated diagnostics, digital interfaces, and condition monitoring is essential for unlocking predictive maintenance workflows and maximizing machine availability. Companies must align their procurement and engineering roadmaps with Industry 4.0 standards, ensuring encoder compatibility with major industrial communication protocols and IIoT platforms.
Tailoring product offerings to specific vertical demands-whether high-speed aerospace milling, automotive stamping, or semiconductor lithography-will differentiate market positioning. By leveraging detailed segmentation insights, organizations can customize solutions at the intersection of accuracy, durability, and cost-effectiveness, capturing new opportunities in evolving machine tool configurations.
Finally, engaging proactively with policy frameworks such as the CHIPS Act, European Chips Act, and regional manufacturing incentives will unlock funding, tax credits, and infrastructure support. Cultivating strategic alliances with government agencies and industry consortia can pave the way for shared innovation hubs, ensuring sustained competitiveness in a rapidly shifting global manufacturing ecosystem.
Transparent Research Methodology Underpinning Comprehensive Primary and Secondary Data Integration for Informed Analysis of the Linear Encoder Market Landscape
This analysis synthesizes insights from both primary and secondary research methodologies to ensure robust market intelligence. Primary research included in-depth interviews with machine tool OEMs, encoder manufacturers, and automation system integrators, facilitating direct validation of emerging trends, product roadmaps, and supply chain challenges.
Secondary research drew upon public policy announcements, regulatory filings, industry white papers, and reputable media coverage to contextualize tariff developments and regional incentive programs. Authoritative sources such as the Office of the U.S. Trade Representative, European Commission, and government reports underpinned the assessment of trade policy impacts and investment frameworks.
Data triangulation was employed to reconcile divergent perspectives, integrating quantitative trade statistics with qualitative feedback from end users across aerospace, automotive, electronics, and CNC machining sectors. This approach ensures a balanced view of market dynamics, from technological adoption rates to procurement strategies and regional competitive advantages.
To maintain analytical rigor, all referenced sources were critically evaluated for credibility and relevance, with citations provided for transparency. This methodology guarantees that the conclusions and recommendations presented herein are grounded in verifiable evidence and reflect the latest developments shaping the linear encoder landscape.
Explore AI-driven insights for the Linear Encoders for Machine Tools & CNC Machining market with ResearchAI on our online platform, providing deeper, data-backed market analysis.
Ask ResearchAI anything
World's First Innovative Al for Market Research
Synthesis of Key Findings Emphasizing the Critical Intersection of Technology Trends Policy Impacts and Strategic Imperatives in the Linear Encoder Sector
The interrogation of market forces reveals a dynamic intersection of technological innovation, policy-driven trade measures, and nuanced customer requirements. Advanced sensing modalities and digital interfaces are driving the next wave of encoder capabilities, aligning tightly with smart manufacturing imperatives and digital transformation strategies.
Trade policy fluctuations, particularly U.S. Section 301 tariff adjustments and progressive regional subsidy frameworks, are reshaping cost structures and supply chain geographies. Manufacturers are adapting through strategic localization efforts, tariff mitigation plans, and diversified sourcing approaches to safeguard operational continuity and margin profiles.
Segmentation analysis underscores the critical importance of aligning encoder specifications-technology, product type, materials, output, precision, and distribution strategy-with the exacting needs of vertical markets. Regional insights highlight how federal incentives and policy roadmaps in the Americas, EMEA, and Asia-Pacific regions catalyze adoption trajectories and competitive positioning.
Ultimately, the evolving encoder ecosystem demands a cohesive approach that synergizes technological prowess, regulatory awareness, and market-centric offerings. Organizations that successfully navigate these dimensions will unlock the full potential of precision motion feedback, driving superior machine tool performance and sustainable growth in CNC machining environments.
This section provides a structured overview of the report, outlining key chapters and topics covered for easy reference in our Linear Encoders for Machine Tools & CNC Machining market comprehensive research report.
- Preface
- Research Methodology
- Executive Summary
- Market Overview
- Market Dynamics
- Market Insights
- Cumulative Impact of United States Tariffs 2025
- Linear Encoders for Machine Tools & CNC Machining Market, by Technology
- Linear Encoders for Machine Tools & CNC Machining Market, by Product Type
- Linear Encoders for Machine Tools & CNC Machining Market, by End User
- Linear Encoders for Machine Tools & CNC Machining Market, by Scale Material
- Linear Encoders for Machine Tools & CNC Machining Market, by Output
- Linear Encoders for Machine Tools & CNC Machining Market, by Accuracy
- Linear Encoders for Machine Tools & CNC Machining Market, by Sales Channel
- Americas Linear Encoders for Machine Tools & CNC Machining Market
- Europe, Middle East & Africa Linear Encoders for Machine Tools & CNC Machining Market
- Asia-Pacific Linear Encoders for Machine Tools & CNC Machining Market
- Competitive Landscape
- ResearchAI
- ResearchStatistics
- ResearchContacts
- ResearchArticles
- Appendix
- List of Figures [Total: 32]
- List of Tables [Total: 912 ]
Connect with Ketan Rohom to Secure Your Comprehensive Market Intelligence Report on Linear Encoders and Drive Strategic Decisions in CNC Machining
To take your strategic planning to the next level and secure unparalleled insights into the linear encoder market for machine tools and CNC machining, reach out to Ketan Rohom, Associate Director of Sales & Marketing. Ketan’s expertise bridges deep technical understanding and market intelligence, ensuring you receive tailored guidance that aligns with your organizational goals and operational priorities. Engaging with him will provide you with the clarity and confidence to invest in the right technologies, partners, and strategies.
Don’t miss the opportunity to gain a competitive edge through comprehensive research, detailed segmentation analysis, and actionable recommendations. Contact Ketan Rohom today to discuss how our market research report can support your business objectives and drive sustainable growth in an evolving manufacturing landscape.
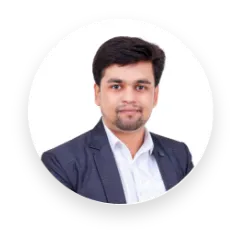
- When do I get the report?
- In what format does this report get delivered to me?
- How long has 360iResearch been around?
- What if I have a question about your reports?
- Can I share this report with my team?
- Can I use your research in my presentation?