Introduction to the Liquid Silicone Based Gap Filler Market
The liquid silicone based gap filler market has emerged as a critical enabler of reliability and performance across a wide array of industrial and consumer applications. Characterized by exceptional thermal stability, electrical insulation, and chemical resistance, these advanced silicones bridge mechanical tolerances and accommodate thermal cycling in demanding environments. As production processes across aerospace, automotive, construction, electronics and medical devices gravitate toward higher precision and longer life cycles, the need for gap fillers that maintain integrity under temperature extremes and mechanical stress becomes paramount.
Robust properties such as low compression set and superior adhesion allow liquid silicone gap fillers to seal and protect interfaces against moisture, dust and vibration-induced fatigue. These characteristics drive adoption in aircraft engine components, vehicle cabin assemblies, building insulation joints and consumer electronics heat sinks. Technological advances in formulation chemistry now enable one-component heat-cure systems alongside two-component addition-cure solutions, delivering tailored viscosity profiles and thermal conductivities.
Against this backdrop, manufacturers seek actionable insights to optimize material selection, streamline supply chains and navigate evolving trade policies. This executive summary outlines transformative trends, tariff impacts, segmentation nuances, regional dynamics and competitive landscapes, culminating in strategic recommendations to guide decision-makers in capitalizing on growth opportunities.
Emerging Transformative Shifts Reshaping the Landscape
Innovation and sustainability imperatives are provoking transformative shifts that redefine how liquid silicone gap fillers are engineered, manufactured and deployed. Rapid advancements in material science have given rise to ultra-low viscosity formulations that permeate micro-gaps in electronics, while high thermal conductivity grades dissipate heat from power semiconductors. Concurrently, regulatory frameworks mandating reduced volatile organic compound (VOC) emissions and compliance with global environmental standards compel producers to adopt greener curing agents and recyclable packaging.
Digital transformation is also reshaping production workflows. The integration of real-time process monitoring, predictive analytics and automated dispensing systems enhances formulation consistency and reduces waste. Such Industry 4.0 initiatives enable precision dosing of one-component acetoxy or oxime cure silicones as well as two-component addition or condensation cure systems, yielding uniform bond lines and reduced rework.
Moreover, customer demands for bespoke solutions drive customization at every level-from thermal conductivity ranges tailored for high-power electronics to dual-hardness architectures for dynamic load-bearing applications. Strategic partnerships between raw material suppliers and end-use manufacturers now focus on co-development of gap fillers that meet specific mechanical, electrical and thermal requirements. This confluence of technological, regulatory and market forces is reshaping competitive benchmarks and value propositions across the industry.
Assessing the Cumulative Impact of United States Tariffs in 2025
In 2025, cumulative tariff adjustments imposed by the United States have exerted significant pressure on global supply chains and cost structures within the liquid silicone gap filler market. A stepped increase in duties on silicone base fluids and filler additives has elevated landed costs, prompting manufacturers to reassess sourcing strategies and negotiate longer-term contracts to hedge against volatility. As a result, some producers have accelerated the qualification of alternative suppliers in low-tariff jurisdictions, while others have pursued backward integration to secure feedstock.
These measures have also triggered shifts in pricing models. OEMs and contract manufacturers are absorbing a portion of the tariff burden to maintain competitive pricing, while tier-two suppliers are renegotiating margin structures. In parallel, the threat of further escalations has spurred regional manufacturing investments-particularly in nearshore facilities-to mitigate import duties and reduce lead times.
Consequently, supply chains have become more fragmented, with dual-sourcing strategies implemented across silicone elastomer producers and additive specialists. This diversification enhances resilience against geopolitical uncertainties but introduces complexity in quality control and logistics coordination. To navigate this environment, stakeholders are prioritizing transparent supplier audits, collaborative demand forecasting and flexible inventory paradigms, ensuring continuity of supply amid evolving trade policies.
Key Insights from Market Segmentation
A granular segmentation analysis unveils how distinct application areas influence demand dynamics and material requirements. In the aerospace sector, gap fillers are formulated for aircraft interiors demanding flame retardancy and engine components requiring extreme temperature resistance. Within automotive, exterior components prioritize UV stability and chemical resistance, while interior components emphasize low odor and user comfort. Construction and building applications split between insulation materials that reduce energy loss and sealing and bonding products that ensure weatherproofing. Electronic and electrical uses bifurcate into consumer devices needing compact heat dissipation and industrial electronics necessitating robust dielectric strength.
Material property segmentation underscores the importance of curing processes and functional attributes. Heat cure silicones deliver rapid crosslinking in high-temperature environments, whereas room temperature cure grades facilitate on-site application. Thermal conductivity options range from high conductivity solutions for power electronics to low conductivity grades for thermal insulation. Likewise, viscosity profiles span high viscosity formulations suited to gap filling in large joints and low viscosity fluids that penetrate micro-voids.
End-use industry segmentation highlights household applications such as cooking appliances requiring food-safe certifications and washing machines needing vibration damping. Medical devices segment into diagnostic tools that benefit from biocompatible elastomers and surgical equipment demanding sterilization resistance.
Product type differentiation contrasts one-component systems-available as acetoxy or oxime cure-with two-component systems delivered via addition or condensation cure chemistries. Finally, manufacturing techniques distinguish extrusion processes-both cold and hot-from injection molding processes, with thermoplastic injection offering rapid throughput and thermosetting injection ensuring mechanical durability.
This comprehensive research report categorizes the Liquid Silicone Based Gap Filler market into clearly defined segments, providing a detailed analysis of emerging trends and precise revenue forecasts to support strategic decision-making.
- Application Areas
- Material Properties
- End-Use Industries
- Product Type
- Manufacturing Techniques
Regional Dynamics and Strategic Implications
The Americas region has sustained growth driven by a robust aerospace industry in the United States and automotive innovation across North America and Brazil. High demand for lightweight materials and electrified powertrains elevates gap filler requirements for thermal management and structural bonding. Europe, the Middle East & Africa (EMEA) show a resurgence in construction and infrastructure spending alongside stringent environmental regulations, fostering demand for low-VOC sealants and fire-safe silicones. Regional leaders are investing in localized production to adhere to REACH standards and tapping into the Middle East’s oil and gas sector for specialized sealing solutions.
Asia-Pacific remains the largest manufacturing hub for electronics, consumer appliances and automotive assembly, with China, South Korea and Japan at the forefront. Rapid industrialization, expanding renewable energy installations and growing medical device exports underscore a heightened need for high-performance gap fillers. Local producers are scaling capacity and collaborating with global chemical companies to introduce advanced formulations, while governments incentivize domestic R&D for strategic materials. These regional dynamics dictate tailored go-to-market strategies, from innovation partnerships in North America to compliance-driven product launches in EMEA and capacity expansion in Asia-Pacific.
This comprehensive research report examines key regions that drive the evolution of the Liquid Silicone Based Gap Filler market, offering deep insights into regional trends, growth factors, and industry developments that are influencing market performance.
- Americas
- Asia-Pacific
- Europe, Middle East & Africa
Competitive Intelligence on Leading Players
Leading global players are shaping the competitive landscape through diversified portfolios, strategic acquisitions and joint ventures. CHT Germany GmbH emphasizes specialty silicone formulations and partners with OEMs to co-develop tailored gap fillers. Dow Corning Corporation leverages its extensive R&D infrastructure to roll out next-generation high thermal conductivity products. DuPont de Nemours, Inc. integrates advanced polymer science to deliver multifunctional fillers that address both sealing and heat dissipation needs. Elkem Silicones focuses on sustainable manufacturing, offering low-carbon footprint silicones. Henkel AG & Co. KGaA capitalizes on its global adhesives platform to cross-sell silicone-based sealants.
KCC Corporation expands its presence in Asia through capacity additions and local technical centers. Momentive Performance Materials Inc. prioritizes digital application tools to optimize dispensing accuracy across various industries. NuSil Technology LLC targets the medical device segment with biocompatible and sterilization-resistant elastomers. Saint-Gobain S.A. deploys its materials expertise to support construction and electronics markets with customized gap filler solutions. Shin-Etsu Chemical Co., Ltd. continues to refine high-purity silicones for semiconductor and electronics applications. The 3M Company integrates its adhesive technology with silicone gap fillers for industrial assembly applications, while Wacker Chemie AG invests in novel crosslinking chemistries to enhance mechanical performance.
These leading players consistently invest in innovation, expand regional footprints and forge collaborations to sustain competitive advantage.
This comprehensive research report delivers an in-depth overview of the principal market players in the Liquid Silicone Based Gap Filler market, evaluating their market share, strategic initiatives, and competitive positioning to illuminate the factors shaping the competitive landscape.
- CHT Germany GmbH
- Dow Corning Corporation
- DuPont de Nemours, Inc.
- Elkem Silicones
- Henkel AG & Co. KGaA
- KCC Corporation
- Momentive Performance Materials Inc.
- NuSil Technology LLC
- Saint-Gobain S.A.
- Shin-Etsu Chemical Co., Ltd.
- The 3M Company
- Wacker Chemie AG
Actionable Recommendations for Industry Leaders
To thrive in this dynamic market, industry leaders should expand R&D investments toward multifunctional formulations that combine thermal management, electrical insulation and mechanical resilience. Establishing regional innovation hubs will accelerate customization for local end-use requirements and regulatory compliance. Strengthening supplier partnerships and dual sourcing of critical silicone elastomer feedstocks will mitigate the impacts of trade tariffs and geopolitical disruptions.
Implementing digital end-to-end supply chain platforms will enhance transparency, optimize inventory and enable predictive demand forecasting. Furthermore, deploying automated dispensing and in-line quality inspection systems will improve production yield and consistency across one-component and two-component processes.
Forging strategic alliances with OEMs, research institutions and additive manufacturing specialists can drive co-development of gap fillers for emerging applications such as electric vehicle battery packs and 5G telecom infrastructure. Companies should also pursue sustainability certifications and circular economy initiatives-such as silicone recycling programs-to meet evolving environmental mandates and brand reputation objectives. By embracing these actions, organizations will bolster resilience, drive innovation and capture high-value opportunities in the liquid silicone gap filler market.
Explore AI-driven insights for the Liquid Silicone Based Gap Filler market with ResearchAI on our online platform, providing deeper, data-backed market analysis.
Ask ResearchAI anything
World's First Innovative Al for Market Research
Conclusion and Strategic Takeaways
The liquid silicone based gap filler market is poised for sustained expansion as industries demand solutions that deliver thermal efficiency, environmental compliance and adaptive performance. Technological breakthroughs in curing chemistries and digital manufacturing are establishing new performance benchmarks, while trade policy shifts and regional diversification strategies continue to reshape supply chains. Comprehensive segmentation analysis reveals nuanced requirements across application areas, material properties, end-use industries, product types and manufacturing techniques-underscoring the importance of targeted product portfolios and agile go-to-market models.
Competitive intelligence highlights a market led by companies that synergize advanced R&D capabilities with global production networks and strategic partnerships. The convergence of sustainability imperatives and digital transformation offers unprecedented potential for differentiation. As decision-makers formulate their next moves, a focus on innovation, resilience and collaboration will be essential to secure leadership positions in this evolving landscape.
This section provides a structured overview of the report, outlining key chapters and topics covered for easy reference in our Liquid Silicone Based Gap Filler market comprehensive research report.
- Preface
- Research Methodology
- Executive Summary
- Market Overview
- Market Dynamics
- Market Insights
- Cumulative Impact of United States Tariffs 2025
- Liquid Silicone Based Gap Filler Market, by Application Areas
- Liquid Silicone Based Gap Filler Market, by Material Properties
- Liquid Silicone Based Gap Filler Market, by End-Use Industries
- Liquid Silicone Based Gap Filler Market, by Product Type
- Liquid Silicone Based Gap Filler Market, by Manufacturing Techniques
- Americas Liquid Silicone Based Gap Filler Market
- Asia-Pacific Liquid Silicone Based Gap Filler Market
- Europe, Middle East & Africa Liquid Silicone Based Gap Filler Market
- Competitive Landscape
- ResearchAI
- ResearchStatistics
- ResearchContacts
- ResearchArticles
- Appendix
- List of Figures [Total: 26]
- List of Tables [Total: 806 ]
Next Steps: Securing Your Comprehensive Report
Ready to gain deeper insights and actionable data on the liquid silicone based gap filler market? Contact Ketan Rohom, Associate Director, Sales & Marketing, to explore customized solutions and secure your comprehensive market research report. Elevate your strategic planning and stay ahead of industry trends with in-depth analysis, competitive benchmarking and targeted recommendations tailored to your business needs. Reach out today to leverage expert intelligence and drive growth in this critical materials sector.
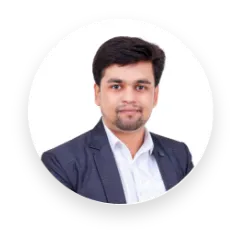
- When do I get the report?
- In what format does this report get delivered to me?
- How long has 360iResearch been around?
- What if I have a question about your reports?
- Can I share this report with my team?
- Can I use your research in my presentation?