Introduction: Understanding the Crucial Role of Separators and Coatings
Lithium battery separators and pole piece coating materials play a pivotal role in modern energy storage systems, directly influencing cell safety, performance, and lifespan. As the world transitions toward electrified mobility and renewable energy integration, separators ensure ionic conductivity while preventing short circuits, and pole piece coatings enhance electrode stability under demanding charge–discharge cycles. Technological enhancements in separator porosity, thickness control, and ceramic or polymeric coatings have driven notable gains in energy density and thermal resilience. Meanwhile, evolving regulatory frameworks, raw material availability, and supply chain realignments are reshaping production strategies worldwide. Against this backdrop, decision-makers across automotive, consumer electronics, industrial, and stationary storage sectors must closely monitor material innovations, tariff developments, and regional dynamics to secure competitive advantage. This executive summary synthesizes transformative shifts, tariff impacts, segmentation insights, regional highlights, key player strategies, and concrete recommendations, equipping stakeholders with the strategic foresight needed to navigate a rapidly evolving marketplace.
Transformative Shifts Reshaping Battery Separator and Coating Markets
The landscape for lithium battery separators and pole piece coatings is experiencing transformative shifts driven by surging electrification and storage demands. In the automotive arena, accelerating electric vehicle adoption is spurring investment in high-temperature–resistant polyester separators and multilayer polyethylene films that offer both mechanical strength and enhanced safety under fast-charge regimes. Meanwhile, grid storage developers are seeking ceramic coatings based on alumina and zirconia to elevate thermal stability for large-scale installations. Concurrently, manufacturers are embracing advanced coating technologies-dip coating, sol-gel, and spray techniques-alongside roll-to-roll processing to achieve uniform, ultrathin films at scale. Sustainability also features prominently: companies are exploring recyclable polypropylene separators and biobased polymer alternatives to minimize environmental footprint. Geopolitical tensions are driving near-shoring of production facilities, while digital twins and in-situ coating monitoring are improving process yields. Together, these dynamics are reshaping material selection, process integration, and supply chain resilience, laying the foundation for next-generation battery performance.
Cumulative Impact of United States Tariffs 2025 on Supply Chains
As the United States implements a cumulative tariff regime in 2025, the ripple effects on separator and pole piece coating supply chains are becoming evident. Import levies on key polymer precursors, including polyethylene and polypropylene feedstocks, are elevating input costs for monolayer and multilayer film manufacturers, prompting many to hedge via long-term supply contracts or strategic partnerships with domestic resin producers. Meanwhile, tariffs on ceramic powders such as magnesia and zirconia are increasing ceramic coating expenses, driving some producers to localize synthesis or identify alternative mineral sources. For coating houses reliant on wet-process phase separation and porogen leaching, higher water-treatment and compliance costs are squeezing margins. Conversely, companies with integrated in-house extrusion stretching lines and lamination capabilities are better positioned to offset tariff impacts through vertical integration. End-users-ranging from electric vehicle manufacturers to battery pack assemblers-are responding by renegotiating supplier agreements and reevaluating safety stock policies. Overall, the 2025 tariff landscape is accelerating regionalization of production, incentivizing innovation in material formulations, and reshaping competitive dynamics across the value chain.
Key Segmentation Insights Across Applications, Materials, and Processes
Segmentation by application underscores the breadth of market demand: within automotive, electric vehicles are driving demand for separators optimized for high-rate fast charge, while hybrid and plug-in hybrids require durable, standard-charge profiles. In consumer electronics, laptops and smartphones prioritize ultrathin, low-impedance films, whereas tablets and wearables seek flexible, conformal coatings. Energy storage systems further diversify needs: grid storage projects favor robust, thermally stable ceramic-coated separators, and residential energy storage emphasizes cost-effective, monolayer polyethylene membranes. Industrial applications extend to material handling equipment where resilience under repetitive cycling is paramount, as well as power tools and robotics demanding consistent performance. Material type segmentation highlights ceramic coatings-specifically alumina, magnesia, and zirconia-gaining traction for safety, while polyester options, available in high-temperature–resistant and standard grades, balance cost and performance. Polyethylene and polypropylene separators, offered in monolayer and multilayer configurations, cater to diverse charge-rate requirements.
Technology segmentation reveals that coating technology choices-dip coating, sol-gel, and spray coating-determine coating uniformity, whereas dry processes such as extrusion stretching and stretching method deliver scalable film production. Wet processes, including phase separation and porogen leaching, enable tailored porosity profiles. Thickness ranges from below 15 microns for ultralight consumer devices to above 25 microns for heavy-duty industrial uses; the 15–25-micron window is further optimized into subranges of 15–18, 19–22, and 23–25 microns. End-user segmentation shows aftermarket channels-battery pack assemblers and energy storage companies-competing alongside OEMs like automobile and electronic device manufacturers. Charge-rate requirements bifurcate into fast-charge and standard-charge applications. Finally, manufacturing process options-co-extrusion, in-situ coating, lamination, and roll-to-roll processing-shape cost structures, throughput, and quality consistency.
This comprehensive research report categorizes the Lithium Battery Separator & Pole Piece Coating Materials market into clearly defined segments, providing a detailed analysis of emerging trends and precise revenue forecasts to support strategic decision-making.
- Application
- Material Type
- Technology
- Thickness
- End-User
- Charge Rate
- Manufacturing Process
Key Regional Insights Highlighting Market Dynamics
The Americas region continues to lead in advanced separator and coating innovation, supported by robust EV infrastructure investments in North America and significant grid modernization projects in South America. Companies here benefit from strong IP protections and proximity to major OEMs, yet face competitive pressure to localize raw material sourcing amid import tariffs. In Europe, Middle East & Africa, regulatory incentives for carbon neutrality are driving rapid uptake of high-performance polyester separators and ceramic coatings for stationary storage and mobility applications. Regional supply chain integration is accelerating, particularly around the European battery alliance. However, the region grapples with feedstock price volatility and complex trade agreements. Asia-Pacific remains the largest production hub, with China, Japan, South Korea, and Taiwan dominating film extrusion and coating technologies. Rapidly expanding EV and portable electronics markets in India and Southeast Asia are fueling demand, while governmental support for local manufacturing is intensifying. Yet geopolitical tensions and raw material security concerns are leading to diversification efforts beyond traditional manufacturing centers.
This comprehensive research report examines key regions that drive the evolution of the Lithium Battery Separator & Pole Piece Coating Materials market, offering deep insights into regional trends, growth factors, and industry developments that are influencing market performance.
- Americas
- Asia-Pacific
- Europe, Middle East & Africa
Key Company Strategies and Technological Leadership
Industry incumbents and emerging challengers are shaping competitive landscapes through technology leadership and strategic alliances. Arkema S.A. and Mitsubishi Chemical Holdings Corporation are leveraging their polymer expertise to expand high-temperature polyester separator offerings. Asahi Kasei Corporation and Sumitomo Chemical Co., Ltd. are advancing ceramic coating formulations to deliver superior thermal and puncture resistance. Celgard LLC and Daramic LLC dominate the polyethylene and polypropylene film space, while Entek International LLC and Freudenberg Group invest in co-extrusion and roll-to-roll processing capabilities. Shenzhen Senior Technology Material Co., Ltd. and Soteria Battery Innovation Group are gaining traction in Asia with innovative wet-process and in-situ coating platforms. SK Innovation Co., Ltd. and Toray Industries, Inc. are intensifying local investments to serve booming EV markets, and Ube Industries, Ltd. is focusing on sustainable precursor materials. BP Polymers, LLC and W-Scope Corporation are forging partnerships to enhance end-to-end supply chain integration, catalyzing new product launches and joint development agreements.
This comprehensive research report delivers an in-depth overview of the principal market players in the Lithium Battery Separator & Pole Piece Coating Materials market, evaluating their market share, strategic initiatives, and competitive positioning to illuminate the factors shaping the competitive landscape.
- Arkema S.A.
- Asahi Kasei Corporation
- BP Polymers, LLC
- Celgard LLC
- Daramic LLC
- Entek International LLC
- Freudenberg Group
- Mitsubishi Chemical Holdings Corporation
- SEEO Inc.
- Shenzhen Senior Technology Material Co., Ltd.
- SK Innovation Co., Ltd.
- Soteria Battery Innovation Group
- Sumitomo Chemical Co., Ltd.
- Toray Industries, Inc.
- Ube Industries, Ltd.
- W-Scope Corporation
Actionable Recommendations for Industry Leaders
Industry leaders should prioritize vertical integration by establishing in-house polymerization and coating lines to mitigate tariff exposure and unlock cost efficiencies. Developing partnerships with resin suppliers and ceramic powder producers will secure raw material pipelines and facilitate co-innovation on high-performance formulations. Investing in advanced process analytics-digital twins and real-time coating thickness monitoring-will reduce waste, improve yield, and accelerate time-to-market. Firms must expand regional manufacturing footprints, targeting emerging markets in Asia-Pacific and the Americas to shorten lead times and capitalize on local incentives. Enhancing R&D capabilities in fast-charge architectures, including novel multilayer polypropylene designs and sol-gel–derived ceramic coatings, will cater to EV and grid-scale applications. Finally, integrating sustainability metrics into product roadmaps-such as recyclable separator materials and energy-efficient roll-to-roll processes-will address regulatory demands and end-customer expectations, securing long-term competitiveness.
Explore AI-driven insights for the Lithium Battery Separator & Pole Piece Coating Materials market with ResearchAI on our online platform, providing deeper, data-backed market analysis.
Ask ResearchAI anything
World's First Innovative Al for Market Research
Conclusion: Navigating Complexity to Drive Future Growth
The lithium battery separator and pole piece coating market stands at a crossroads of technological innovation, regulatory evolution, and shifting trade dynamics. Dynamic segmentation across applications, materials, technologies, thicknesses, end-users, charge rates, and manufacturing processes underscores the market’s complexity and potential. While the 2025 U.S. tariff regime presents headwinds, it also accelerates localization and vertical integration strategies that can yield sustainable advantages. Regional trends highlight diverse growth catalysts, from EV infrastructure in the Americas to regulatory incentives in Europe and mass production in Asia-Pacific. Leading companies are responding with targeted investments in high-performance separators, advanced coating platforms, and robust supply chain partnerships. For stakeholders across the value chain, aligning innovation with regional opportunities, securing strategic alliances, and embedding sustainability are imperative to navigate this dynamic environment successfully.
This section provides a structured overview of the report, outlining key chapters and topics covered for easy reference in our Lithium Battery Separator & Pole Piece Coating Materials market comprehensive research report.
- Preface
- Research Methodology
- Executive Summary
- Market Overview
- Market Dynamics
- Market Insights
- Cumulative Impact of United States Tariffs 2025
- Lithium Battery Separator & Pole Piece Coating Materials Market, by Application
- Lithium Battery Separator & Pole Piece Coating Materials Market, by Material Type
- Lithium Battery Separator & Pole Piece Coating Materials Market, by Technology
- Lithium Battery Separator & Pole Piece Coating Materials Market, by Thickness
- Lithium Battery Separator & Pole Piece Coating Materials Market, by End-User
- Lithium Battery Separator & Pole Piece Coating Materials Market, by Charge Rate
- Lithium Battery Separator & Pole Piece Coating Materials Market, by Manufacturing Process
- Americas Lithium Battery Separator & Pole Piece Coating Materials Market
- Asia-Pacific Lithium Battery Separator & Pole Piece Coating Materials Market
- Europe, Middle East & Africa Lithium Battery Separator & Pole Piece Coating Materials Market
- Competitive Landscape
- ResearchAI
- ResearchStatistics
- ResearchContacts
- ResearchArticles
- Appendix
- List of Figures [Total: 30]
- List of Tables [Total: 950 ]
Call-To-Action: Engage with Ketan Rohom to Acquire the Full Market Report
To explore detailed market insights, strategic analyses, and comprehensive data on separators and coating materials, contact Ketan Rohom, Associate Director, Sales & Marketing, to secure your copy of the in-depth market research report and gain a competitive edge.
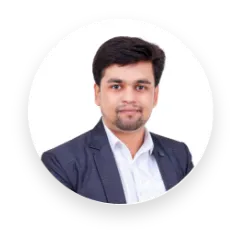
- When do I get the report?
- In what format does this report get delivered to me?
- How long has 360iResearch been around?
- What if I have a question about your reports?
- Can I share this report with my team?
- Can I use your research in my presentation?