Market Dynamics and Scope of Low Shrinkage Polypropylene
Low shrinkage polypropylene combines enhanced dimensional stability with the inherent benefits of conventional polypropylene, offering lower deformation under heat, superior mold fidelity, and reduced internal stresses. This specialty polymer addresses critical challenges in high-precision applications where tolerances are tight, such as exterior automotive trim that must resist warping during paint curing, injection-molded medical device housings requiring seamless optical clarity, and rigid packaging formats that demand consistent wall thickness. With rising demand for lightweight materials that do not compromise performance, low shrinkage grades are gaining traction in sectors ranging from consumer electronics to advanced textiles. Moreover, advances in catalyst design and process control have yielded homopolymers, block copolymers, and random copolymers with tailored crystallinity profiles to meet specific shrinkage thresholds. As sustainability considerations intensify, developers are also exploring bio-based feedstocks and closed-loop recycling to lower environmental impact without sacrificing dimensional control. In this context, understanding the core drivers, material innovations, and application requirements for low shrinkage polypropylene is essential for manufacturers and end-users aiming to secure a competitive edge.
Transformative Shifts Reshaping Low Shrinkage Polypropylene Landscape
The landscape for low shrinkage polypropylene is undergoing transformative shifts driven by new performance benchmarks and regulatory imperatives. Regulatory frameworks targeting reduced volatile organic compound emissions and stricter automotive light-weighting mandates are propelling the adoption of ultra-stable polymer formulations. At the same time, materials science breakthroughs in block copolymerization enable unprecedented control of crystallinity gradients, expanding design freedom in injection molding and blow molding processes. Digital manufacturing platforms equipped with in-line monitoring and adaptive process control are enhancing consistency from batch to batch. Concurrently, the circular economy is reshaping supply chains, with chemical recycling technologies and mechanically recycled feedstocks becoming integral to product roadmaps. Cross-industry collaborations are accelerating, as automotive OEMs, medical device producers, and packaging giants seek co-development of next-generation resins. Furthermore, the integration of simulation tools for shrinkage prediction is reducing development cycles and improving product quality. Together, these dynamics are redefining how low shrinkage polypropylene is formulated, processed, and validated, unlocking opportunities for differentiated offerings that meet stringent performance and sustainability criteria.
Assessing the Cumulative Impact of United States Tariffs in 2025
The cumulative impact of United States import tariffs enacted in 2025 is reshaping global supply chains and cost structures for low shrinkage polypropylene. Increased duties on key polymer feedstocks and finished resin imports have elevated input costs, prompting processors to reassess sourcing strategies in favor of regional production hubs. As a result, capacity expansions in North America have accelerated to capture local demand for high-precision automotive components and medical packaging. Simultaneously, tier-two suppliers in Asia and Europe are leveraging cost advantages to serve export markets previously dominated by U.S. exports. The necessity for dual-sourcing strategies has intensified, driving greater inventory buffers and longer lead times, while long-term contracts are being renegotiated to include tariff pass-through clauses and flexible pricing mechanisms. In response, innovative logistics models and trade finance solutions are emerging to mitigate tariff volatility. Ultimately, the tariff landscape is catalyzing a shift toward more resilient, geographically diversified supply networks, influencing material availability and cost competitiveness across end-use segments.
Key Segmentation Insights for Strategic Market Positioning
Detailed segmentation analysis reveals distinct performance requirements and adoption rates across application, polymer type, end-use industry, processing technology, and material property considerations. In automotive exterior parts, interior components, and under-the-hood applications, formulators are prioritizing high crystallinity block copolymers and general grade homopolymers to ensure dimensional precision under thermal cycling. Consumer goods segments such as furniture parts and home appliances are driving demand for random copolymers with high melt flow rates for smooth surface finishes. In healthcare, medical device manufacturers value optical grade random copolymers and high impact grade homopolymers for transparent, low-stress injection-molded housings and precise pharmaceutical packaging. Agricultural machinery and greenhouse films demand chemical resistant homopolymers engineered for acid and alkali exposure. Film and sheet extrusion processes, including blown and cast film techniques, are optimized with high crystallinity block copolymers, while micro and thin-wall injection molding benefit from high impact grade homopolymers. Flexible packaging applications exploit the transparency of specialized random copolymers for both indoor and outdoor uses, whereas rigid packaging maximizes the flexural modulus of homopolymer grades. This granular segmentation underscores the importance of aligning polymer selection with end-use demands and processing constraints for optimal performance.
This comprehensive research report categorizes the Low Shrinkage Polypropylene market into clearly defined segments, providing a detailed analysis of emerging trends and precise revenue forecasts to support strategic decision-making.
- Application
- Types
- End Use Industries
- Processing Technology
- Properties
Regional Developments Driving Polypropylene Demand Patterns
Regional dynamics are shaping the trajectory of low shrinkage polypropylene adoption worldwide. In the Americas, strong automotive manufacturing clusters and robust packaging demand for food and consumer goods are catalyzing investment in localized resin capacity and downstream compounding facilities. Europe, the Middle East & Africa exhibit a balanced mix of building & construction growth driven by insulation systems and piping solutions, coupled with stringent environmental regulations that accelerate bio-based and recycled content integration. The Asia-Pacific region remains the fastest growing arena, fueled by rapid expansion of electrical & electronics industries, infrastructure development, and burgeoning healthcare sectors demanding high-performance medical devices. Multi-national resin producers are forging strategic alliances with regional converters to streamline supply chains and co-develop application-specific solutions that address both performance requirements and local regulatory frameworks. These geographic distinctions highlight the necessity of tailoring market strategies to regional end-use priorities and policy environments.
This comprehensive research report examines key regions that drive the evolution of the Low Shrinkage Polypropylene market, offering deep insights into regional trends, growth factors, and industry developments that are influencing market performance.
- Americas
- Asia-Pacific
- Europe, Middle East & Africa
Leading Players Shaping the Low Shrinkage Polypropylene Market
Leading chemical and petrochemical companies are intensifying R&D investments and capacity expansions to capture the high-value low shrinkage polypropylene segment. BASF SE is advancing catalyst technologies to refine polymer chain architectures, while Borealis AG is scaling circular economy initiatives to incorporate chemical recycling streams. Braskem S.A. is leveraging its bio-based feedstock capabilities to introduce sustainable polypropylene variants. Chevron Phillips Chemical Company LP and ExxonMobil Chemical Company are utilizing integrated refining and chemical operations to optimize cost structures and ensure feedstock security. Daelim Industrial Co., Ltd. and Formosa Plastics Corporation are expanding regional production footprints to meet growing demand in Asia. Haldia Petrochemicals Ltd and Reliance Industries Limited capitalize on feedstock integration to offer competitive pricing, whereas INEOS Group AG emphasizes process innovations for energy efficiency. LyondellBasell Industries N.V. and TotalEnergies Petrochemicals & Refining are deploying advanced recycling technologies, and Mitsui Chemicals, Inc. along with Sumitomo Chemical Co., Ltd. are focusing on specialty grades tailored for medical and electronics applications. Such diversified strategies underscore a competitive landscape where technological leadership and supply chain resilience drive market share.
This comprehensive research report delivers an in-depth overview of the principal market players in the Low Shrinkage Polypropylene market, evaluating their market share, strategic initiatives, and competitive positioning to illuminate the factors shaping the competitive landscape.
- BASF SE
- Borealis AG
- Braskem S.A.
- Chevron Phillips Chemical Company LP
- Daelim Industrial Co., Ltd.
- ExxonMobil Chemical Company
- Formosa Plastics Corporation
- Haldia Petrochemicals Ltd
- INEOS Group AG
- LyondellBasell Industries N.V.
- Mitsui Chemicals, Inc.
- Reliance Industries Limited
- SABIC (Saudi Basic Industries Corporation)
- Sumitomo Chemical Co., Ltd.
- TotalEnergies Petrochemicals & Refining
Actionable Recommendations for Industry Leaders to Gain Competitive Edge
To secure sustainable growth and maintain a competitive advantage, industry leaders should prioritize strategic initiatives across technology, supply chain, and partnerships. First, accelerating collaboration with catalyst developers and research institutes will expedite the commercialization of novel copolymers and tailored homopolymers that deliver precise shrinkage profiles. Second, diversifying raw material sources through joint ventures or long-term feedstock agreements can mitigate tariff and geopolitical risks while ensuring uninterrupted supply. Third, investing in advanced recycling infrastructure and trialing chemically recycled content will address regulatory mandates and corporate sustainability goals. Fourth, integrating real-time process monitoring and digital twin technologies will reduce development cycles and enhance quality assurance across molding and extrusion operations. Fifth, establishing cross-sector alliances with automotive OEMs, medical device manufacturers, and packaging converters will facilitate co-development of application-specific solutions and secure long-term off-take contracts. By adopting these measures, companies can bolster resilience, foster innovation, and capture premium value in the evolving low shrinkage polypropylene landscape.
Explore AI-driven insights for the Low Shrinkage Polypropylene market with ResearchAI on our online platform, providing deeper, data-backed market analysis.
Ask ResearchAI anything
World's First Innovative Al for Market Research
Conclusion: Strategic Imperatives for Low Shrinkage Polypropylene Growth
As markets evolve and performance standards rise, low shrinkage polypropylene will continue to play a pivotal role in high-precision applications across multiple sectors. Manufacturers and converters who embrace innovation in polymer chemistry, invest in sustainable feedstocks, and optimize production through digital capabilities will differentiate themselves in an increasingly competitive environment. Understanding tariff impacts, regional nuances, and segment-specific requirements is fundamental to shaping robust supply chain strategies and product portfolios. Ultimately, success will depend on the ability to anticipate regulatory shifts, collaborate across the value chain, and deliver materials that meet stringent dimensional and environmental criteria. By aligning strategic priorities with these imperatives, stakeholders can unlock new opportunities and position themselves at the forefront of specialty polymer advancement.
This section provides a structured overview of the report, outlining key chapters and topics covered for easy reference in our Low Shrinkage Polypropylene market comprehensive research report.
- Preface
- Research Methodology
- Executive Summary
- Market Overview
- Market Dynamics
- Market Insights
- Cumulative Impact of United States Tariffs 2025
- Low Shrinkage Polypropylene Market, by Application
- Low Shrinkage Polypropylene Market, by Types
- Low Shrinkage Polypropylene Market, by End Use Industries
- Low Shrinkage Polypropylene Market, by Processing Technology
- Low Shrinkage Polypropylene Market, by Properties
- Americas Low Shrinkage Polypropylene Market
- Asia-Pacific Low Shrinkage Polypropylene Market
- Europe, Middle East & Africa Low Shrinkage Polypropylene Market
- Competitive Landscape
- ResearchAI
- ResearchStatistics
- ResearchContacts
- ResearchArticles
- Appendix
- List of Figures [Total: 26]
- List of Tables [Total: 990 ]
Next Steps: Connect with Ketan Rohom for In-Depth Market Intelligence
For a comprehensive analysis and actionable insights tailored to your strategic objectives, connect with Ketan Rohom, Associate Director of Sales & Marketing, to secure the full market research report and drive informed decision-making.
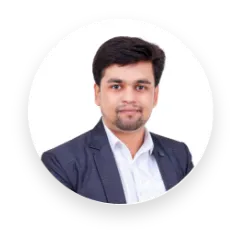
- When do I get the report?
- In what format does this report get delivered to me?
- How long has 360iResearch been around?
- What if I have a question about your reports?
- Can I share this report with my team?
- Can I use your research in my presentation?