The Machine Condition Monitoring Market size was estimated at USD 3.35 billion in 2024 and expected to reach USD 3.60 billion in 2025, at a CAGR 7.19% to reach USD 5.08 billion by 2030.

Exploring the Evolution of Machine Condition Monitoring
Machine condition monitoring has become a cornerstone of modern industrial operations, empowering organizations to transition from reactive maintenance to predictive and prescriptive strategies that optimize asset performance. Advances in sensor technology, data analytics, and connectivity are converging to deliver unprecedented levels of visibility into equipment health. As manufacturing, energy, transportation, and other asset-intensive sectors grapple with the dual pressures of rising operating costs and the imperative for greater uptime, condition monitoring emerges as a strategic enabler of reliability and efficiency.
In this landscape of rapid technological evolution, executives and engineers alike require a clear understanding of the forces shaping the market, the competitive dynamics among key providers, and the most effective approaches to integrating monitoring solutions into existing operations. This executive summary offers a concise yet comprehensive overview of the critical trends, regulatory influences, segmentation patterns, regional dynamics, and actionable recommendations that will inform strategic investments and partnership decisions.
Transformative Shifts Driving Machine Monitoring Innovation
The machine condition monitoring landscape is undergoing transformative shifts driven by advances in connectivity, artificial intelligence, and edge computing. The proliferation of IoT-enabled sensors and real-time data ingestion platforms is redefining how organizations detect, diagnose, and predict equipment failures. Rather than relying solely on periodic manual inspections, companies are harnessing continuous monitoring capabilities to identify early warning signs of degradation and intervene before unplanned downtime occurs.
Concurrently, the integration of machine learning algorithms and cloud-based analytics is enabling more sophisticated pattern recognition and anomaly detection. Predictive models are increasingly capable of accounting for complex interdependencies among multiple variables, such as vibration signatures, temperature fluctuations, and lubricant quality. Edge processing architectures are decentralizing analytics, allowing for low-latency decision-making at the device level and reducing the burden on centralized infrastructure. Together, these shifts are fostering a new generation of condition monitoring solutions that deliver higher reliability, scalability, and actionable insights.
Cumulative Impact of 2025 US Tariffs on Monitoring Solutions
The implementation of new tariffs by the United States in 2025 has exerted a cumulative impact on the lifecycle cost and supply chain strategies associated with machine condition monitoring systems. Hardware components such as sensors, data acquisition units, and connectivity modules have experienced cost pressures due to duties on imported electronics, prompting vendors to reevaluate sourcing and manufacturing footprints. In response, some providers have accelerated regional assembly and diversified supplier networks to mitigate exposure to tariff fluctuations.
At the same time, service-based offerings have gained prominence as organizations seek to offset capital expenditures with subscription-style models that bundle remote monitoring and consulting. This shift has deepened collaboration between equipment OEMs and specialized service providers, leading to hybrid deployments that blend on-premises software, cloud platforms, and managed services. Moreover, software vendors have introduced modular licensing structures to accommodate budgetary constraints, enabling customers to scale analytic capabilities over time and align cost structures with evolving maintenance strategies.
Revealing Insights Across Key Market Segments
Insight into the market’s segmentation reveals distinct growth trajectories and adoption patterns across various categories. In terms of offering, hardware remains foundational for capturing machine signals, while services-spanning consulting, predictive maintenance, and remote monitoring-have emerged as critical enablers of continuous performance optimization. The software realm has bifurcated into cloud-hosted analytics platforms that support cross-site benchmarking and on-premises installations designed for latency-sensitive environments.
From a monitoring technique perspective, traditional approaches such as vibration monitoring and oil analysis continue to retain strong relevance, particularly within heavy machinery contexts. Simultaneously, motor current analysis and pressure monitoring are gaining traction in applications where non-intrusive measurements reduce operational disruption, whereas thermography and ultrasound emission monitoring offer complementary diagnostic insights for specific fault domains.
Component segmentation highlights the growing importance of connectivity modules that facilitate data transmission across multi-vendor networks, alongside advanced sensors capable of multi-parameter measurement. Data acquisition systems have evolved to support higher channel counts and improved sampling rates, while signal conditioners ensure the fidelity of raw signals under harsh industrial conditions.
End-user dynamics illustrate the varied drivers of adoption. The automotive sector’s focus on lean manufacturing and zero-defect initiatives is driving increased investment in real-time monitoring. Manufacturing industries leverage analytics to bolster quality assurance and throughput, oil & gas operators emphasize asset integrity and safety compliance, and power generation facilities prioritize reliability to minimize unplanned outages and regulatory penalties.
This comprehensive research report categorizes the Machine Condition Monitoring market into clearly defined segments, providing a detailed analysis of emerging trends and precise revenue forecasts to support strategic decision-making.
- Offering
- Monitoring Technique
- Component
- End User
Regional Dynamics Shaping the Global Monitoring Landscape
Regional dynamics play a pivotal role in shaping the machine condition monitoring landscape. Within the Americas, strong industrial automation initiatives and robust capital spending in upstream and downstream energy projects are fueling demand for integrated monitoring solutions. North America’s emphasis on digital transformation programs has led to the widespread deployment of cloud analytics and edge intelligence platforms.
In Europe, Middle East & Africa, regulatory directives on equipment safety and emissions control are driving manufacturers to adopt condition-based maintenance strategies. The region’s mature transportation and utilities sectors are early adopters of thermography and vibration diagnostics, while emerging Middle Eastern markets are investing heavily in oil & gas infrastructure resilience. Cross-border collaboration and standardized protocols are enhancing interoperability among system providers.
The Asia-Pacific region is characterized by rapid industrial expansion and a strong focus on smart manufacturing initiatives. Governments in key markets are incentivizing Industry 4.0 adoption, leading to heightened integration of IoT sensors and predictive analytics in automotive assembly and electronics production. Investments in renewable energy generation and mining operations are further bolstering the uptake of advanced monitoring techniques tailored to harsh environmental conditions.
This comprehensive research report examines key regions that drive the evolution of the Machine Condition Monitoring market, offering deep insights into regional trends, growth factors, and industry developments that are influencing market performance.
- Americas
- Europe, Middle East & Africa
- Asia-Pacific
Profiling Leading Players Driving Market Advancements
Leading companies in the machine condition monitoring space are executing multifaceted strategies to strengthen their market positions. Major industrial automation suppliers are integrating sensor technologies with comprehensive software suites, offering end-to-end portfolios that address signal capture, data management, and advanced analytics. Specialized service providers are differentiating through industry-specific expertise, delivering tailored consulting engagements and managed monitoring contracts that drive long-term client retention.
Software vendors are forging partnerships and strategic alliances to expand cloud infrastructure and embed artificial intelligence capabilities into their platforms. They are also pursuing acquisitions to gain access to niche analytics algorithms and enhance their geographic coverage. Hardware manufacturers, facing tariff-driven cost challenges, are investing in local assembly and component standardization to streamline production and reduce lead times.
Across the competitive landscape, emphasis on interoperability and open architectures has increased. Vendors are collaborating on framework standards that enable seamless integration of third-party sensors and analytics engines, thereby fostering an ecosystem where customers can assemble best-in-class solutions tailored to their unique operational requirements.
This comprehensive research report delivers an in-depth overview of the principal market players in the Machine Condition Monitoring market, evaluating their market share, strategic initiatives, and competitive positioning to illuminate the factors shaping the competitive landscape.
- ALS Limited
- Analog Devices Inc.
- Baker Hughes Company
- NSK Ltd.
- Canstar Instruments Inc.
- Emerson Electric Co.
- Teledyne FLIR LLC
- Fluke Corporation
- General Electric Company
- Honeywell International Inc.
- National Instruments Corporation
- Parker Hannifin Corporation
- Amphenol Corporation
- Rockwell Automation Inc.
- SKF AB
- Infineon Technologies AG
Strategic Recommendations for Industry Leaders to Capture Value
To capture sustainable value in this rapidly evolving market, industry leaders should prioritize modular, future-proof system architectures that accommodate emerging sensor types and analytic techniques. They must invest in artificial intelligence and machine learning capabilities to extract deeper insights from multi-dimensional datasets, enabling prescriptive recommendations that transcend traditional predictive alerts.
Strategic partnerships with cloud service providers and edge computing specialists will be critical for delivering scalable solutions that balance latency and security requirements. Leaders should also explore outcome-based commercial models that align vendor incentives with client performance improvements, fostering long-term relationships grounded in shared results. Equally important is the development of workforce training programs to build data literacy and condition monitoring expertise among maintenance and reliability engineers.
Finally, stakeholders must adopt agile supply chain strategies-leveraging regional manufacturing hubs and alternative sourcing arrangements-to mitigate geopolitical risks and tariff fluctuations. By combining technological innovation with resilient operations and customer-centric service models, providers can solidify their competitive advantage and drive widespread adoption of next-generation condition monitoring solutions.
Robust Methodology Underpinning Market Research Findings
The research methodology underpinning these findings is grounded in a rigorous combination of primary and secondary data collection. Primary research involved in-depth interviews and workshops with equipment OEMs, end-user executives, system integrators, and independent maintenance specialists. This qualitative input was supplemented with quantitative surveys that captured deployment metrics, technology preferences, and budgetary priorities across multiple industry verticals.
Secondary sources encompassed vendor white papers, regulatory filings, industry association reports, and technical journals, providing context on technology roadmaps and compliance frameworks. Data points were cross-validated through triangulation techniques to ensure reliability, while iterative expert reviews were conducted to refine assumptions and interpret emerging trends. The research framework also integrated case studies of representative deployment scenarios, illustrating best practices and common pitfalls encountered in real-world implementations.
Explore AI-driven insights for the Machine Condition Monitoring market with ResearchAI on our online platform, providing deeper, data-backed market analysis.
Ask ResearchAI anything
World's First Innovative Al for Market Research
Navigating the Future of Condition Monitoring
As organizations grapple with the imperative to enhance operational resilience and cost efficiency, machine condition monitoring stands out as a transformative enabler of proactive maintenance strategies. Accelerated by digitalization, the convergence of sensors, analytics, and connectivity is reshaping traditional paradigms of equipment management. At the same time, external factors such as tariff policies have introduced new complexities into procurement and supply chain planning.
Through an examination of segmentation patterns, regional dynamics, and competitive positioning, this executive summary has highlighted the multifaceted drivers and challenges that define the current market landscape. By embracing innovative technologies, collaborative business models, and resilient supply chains, industry participants can navigate uncertainty and unlock the full potential of condition monitoring. The insights and recommendations presented herein offer a strategic blueprint for stakeholders seeking to optimize asset performance and achieve next-generation reliability.
This section provides a structured overview of the report, outlining key chapters and topics covered for easy reference in our Machine Condition Monitoring market comprehensive research report.
- Preface
- Research Methodology
- Executive Summary
- Market Overview
- Market Dynamics
- Market Insights
- Cumulative Impact of United States Tariffs 2025
- Machine Condition Monitoring Market, by Offering
- Machine Condition Monitoring Market, by Monitoring Technique
- Machine Condition Monitoring Market, by Component
- Machine Condition Monitoring Market, by End User
- Americas Machine Condition Monitoring Market
- Europe, Middle East & Africa Machine Condition Monitoring Market
- Asia-Pacific Machine Condition Monitoring Market
- Competitive Landscape
- ResearchAI
- ResearchStatistics
- ResearchContacts
- ResearchArticles
- Appendix
- List of Figures [Total: 24]
- List of Tables [Total: 285 ]
Unlock In-Depth Insights Today
To gain full access to the comprehensive market research report on machine condition monitoring and secure critical competitive intelligence, reach out to Ketan Rohom, Associate Director, Sales & Marketing at 360iResearch. This report delivers proprietary analysis on emerging technologies, detailed segment deep dives, and actionable strategic guidance tailored to executive decision-makers. Purchase the report now to drive operational excellence, unlock new revenue streams, and stay ahead in the rapidly evolving landscape of machine health management
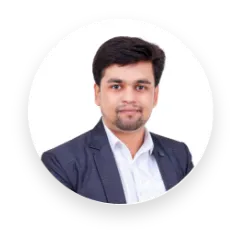
- How big is the Machine Condition Monitoring Market?
- What is the Machine Condition Monitoring Market growth?
- When do I get the report?
- In what format does this report get delivered to me?
- How long has 360iResearch been around?
- What if I have a question about your reports?
- Can I share this report with my team?
- Can I use your research in my presentation?