Introduction to the Machine Tending Landscape
The evolution of machine tending solutions marks a critical juncture for manufacturing operations worldwide. As production environments demand higher precision, efficiency, and adaptability, the integration of automated systems for loading, unloading, and handling workpieces has emerged as a strategic imperative. Manufacturers are transitioning from manual labor and semi-automated processes toward fully integrated robotic cells that deliver consistent throughput, minimize human exposure to hazards, and enable rapid changeovers.
This shift is propelled by advancements in robot design, vision technology, and control software that offer seamless interoperability between CNC machines, injection molders, and assembly lines. Consequently, businesses gain greater flexibility to respond to fluctuating demand, implement just-in-time production, and maintain stringent quality standards. By embedding machine tending solutions within broader digital transformation initiatives, enterprises can unlock real-time monitoring, predictive maintenance and data-driven process optimization.
In the sections that follow, we explore the transformative forces shaping adoption, including regulatory dynamics, tariff implications, segmentation strategies, regional variations, competitive differentiation, and actionable guidance for leaders seeking to harness the full potential of automated tending.
Transformative Shifts Driving Machine Tending Adoption
The machine tending market is undergoing profound change fueled by megatrends in digitalization, artificial intelligence, and human–machine collaboration. Industry 4.0 frameworks are embedding smart sensors and analytics into every stage of production, enabling operators to monitor loading and unloading cycles with unprecedented granularity. Meanwhile, machine learning algorithms refine robot trajectories for complex tasks such as delicate part insertion or rapid palletizing, driving continuous improvement in throughput and reducing scrap rates.
Collaborative robots are blurring the line between manual labor and automation, allowing workers to focus on high-value tasks like programming and quality assurance while cobots handle repetitive loading operations. Simultaneously, cloud-based platforms are facilitating remote diagnostics and fleet management, empowering maintenance teams to predict failures before they occur and schedule interventions during planned downtimes.
As manufacturing ecosystems embrace digital twins and virtual commissioning, machine tending cells can be tested and optimized in simulated environments, shortening time to deployment and mitigating integration risks. These transformative shifts are not only streamlining individual processes, but also redefining supply chain agility, resilience and competitiveness in a rapidly evolving global marketplace.
Cumulative Impact of 2025 United States Tariffs
United States tariff measures scheduled for 2025 are set to influence cost structures across machine tending ecosystems. Levies on imported CNC equipment, robotic arms and vision components are expected to increase capital expenditure for manufacturers relying on offshore sourcing. In response, businesses may accelerate investments in domestic production capabilities or seek alternative suppliers in tariff-free regions to mitigate additional duties.
These trade barriers could spur localization of key subsystems such as servo motors and sensors, encouraging collaboration between tier-one OEMs and local tier-two vendors. As duties reshape supply chains, integrators may adopt modular cell architectures to swap components from multiple manufacturers, preserving flexibility and negotiating leverage.
Conversely, elevated import costs could dampen near-term automation projects for small and medium enterprises with tight budgets. Strategic planning will require scenario analysis to balance the benefits of immediate deployment against the financial impact of tariffs. Ultimately, firms that proactively assess sourcing strategies, qualify dual-source components and engage in tariff engineering will maintain a competitive edge amid evolving trade landscapes.
Key Segmentation Insights for Targeted Strategies
Insight into machine tending adoption varies significantly across diverse market segments, revealing tailored opportunities for growth. Based on industry applications, aerospace customers prioritize assembly, component testing and inspection for complex airframe parts, while automakers focus on assembly lines, body shop operations-specifically painting and welding-and quality inspection to meet stringent safety standards. Electronics manufacturers leverage automated testing, circuit board assembly and soldering to maintain high throughput, whereas food and beverage producers integrate canning with labeling and sealing alongside filling operations and packaging to ensure product integrity. Healthcare facilities are increasingly adopting laboratory automation, medical equipment handling and pharmaceutical manufacturing to accelerate diagnostics and maintain sterile conditions.
From the perspective of machine types, automated CNC machines such as lathes and milling machines remain indispensable for precision work, even as collaborative and industrial robotic systems handle higher payloads and complex geometries. Vision systems, encompassing both 2D and 3D modalities, employ laser scanning and structured light imaging to guide pick-and-place tasks and detect surface defects with micron-level accuracy.
Functional segmentation highlights distinct use cases: assembly processes benefit from fastening and joining solutions, handling applications rely on material transport and product sorting, inspection routines use defect detection and rigorous quality control, and packaging workflows integrate boxing and wrapping for outbound logistics.
Component-level analysis underscores the importance of robust hardware-actuators, motors and sensors-complemented by integration services spanning installation and training, maintenance services offering both corrective and preventive support, and advanced software platforms for analytics and control. Customer size influences deployment strategies, with large corporations investing in fully networked systems, medium enterprises opting for modular cells, and small enterprises leveraging turnkey solutions. Distribution channels-direct sales and third-party distributors-further shape go-to-market approaches, ensuring broad coverage and localized expertise.
This comprehensive research report categorizes the Machine Tending Solution market into clearly defined segments, providing a detailed analysis of emerging trends and precise revenue forecasts to support strategic decision-making.
- Industry Applications
- Machine Types
- Functionality
- Component Types
- Customer Size
- Distribution Channels
Regional Dynamics Shaping Market Opportunities
Regional dynamics play a pivotal role in shaping market trajectories and investment priorities. In the Americas, manufacturers are pushing the envelope on automation in automotive, electronics and aerospace sectors, driven by labor cost inflation and nearshoring initiatives. Government incentives for reshoring critical industries bolster demand for integrated machine tending cells and encourage domestic innovation in robotics.
Across Europe, Middle East & Africa, stringent regulatory frameworks on worker safety and product quality are propelling adoption in food and beverage, pharmaceuticals and precision engineering. The region’s strong industrial heritage supports high complexity deployments, though smaller manufacturers may face budgetary constraints. Collaborative programs between public research institutions and industry leaders are fostering next-generation solutions.
The Asia-Pacific region remains the largest growth engine, with China’s manufacturing modernization, Japan’s strong robotics ecosystem and South Korea’s semiconductor expansion driving robust demand. Government stimulus packages and industrial policies in India and Southeast Asia are accelerating automation uptake among both established players and emerging enterprises seeking to enhance productivity and global competitiveness.
This comprehensive research report examines key regions that drive the evolution of the Machine Tending Solution market, offering deep insights into regional trends, growth factors, and industry developments that are influencing market performance.
- Americas
- Asia-Pacific
- Europe, Middle East & Africa
Competitive Landscape: Leading Companies and Differentiators
The competitive landscape of machine tending is defined by a blend of global robotics pioneers and specialized systems integrators, each pursuing innovation in hardware, software and service models. ABB Ltd. continues to leverage its strong portfolio of modular robotic cells and digital control platforms. Denso Wave Incorporated specializes in high-speed SCARA solutions for electronics and automotive subassembly. FANUC Corporation emphasizes seamless CNC-robot integration with its FIELD system architecture, while Kawasaki Heavy Industries Robot Division focuses on payload-optimized models for heavy manufacturing.
KUKA AG drives collaborative automation through its LBR iiwa series, complemented by Mitsubishi Electric Corporation’s real-time vision guidance systems. Nachi-Fujikoshi Corp. combines durable hardware with advanced motion control, whereas Omron Corporation integrates AI-driven defect detection directly into robotic workflows. Panasonic Corporation offers comprehensive mechatronics suites, and Rockwell Automation, Inc. pairs machine tending with its industrial automation and information solutions.
Schneider Electric SE and Siemens AG differentiate through energy-efficient designs and built-in analytics, while Stäubli Corporation caters to precision applications in life sciences. Universal Robots A/S has democratized automation with user-friendly cobots, and Yaskawa Electric Corporation rounds out the field with versatile Motoman series robots. These key players invest heavily in R&D, after-sales support and ecosystem partnerships to address evolving customer needs.
This comprehensive research report delivers an in-depth overview of the principal market players in the Machine Tending Solution market, evaluating their market share, strategic initiatives, and competitive positioning to illuminate the factors shaping the competitive landscape.
- ABB Ltd.
- Denso Wave Incorporated
- FANUC Corporation
- Kawasaki Heavy Industries Robot Division
- KUKA AG
- Mitsubishi Electric Corporation
- Nachi-Fujikoshi Corp.
- Omron Corporation
- Panasonic Corporation
- Rockwell Automation, Inc.
- Schneider Electric SE
- Siemens AG
- Stäubli Corporation
- Universal Robots A/S
- Yaskawa Electric Corporation
Actionable Recommendations for Industry Leaders
Industry leaders seeking to capitalize on machine tending solutions should pursue a multipronged approach. First, developing digital twin capabilities and embracing virtual commissioning accelerates deployment and reduces integration risk. Second, establishing robust supply chain resilience-through dual-sourcing critical components and qualifying local vendors-mitigates tariff exposure and minimizes downtime.
Third, prioritizing workforce upskilling ensures operators are proficient in robot programming, vision system calibration and data analysis, fostering greater agility in production environments. Fourth, adopting modular, plug-and-produce architectures allows rapid reconfiguration for new product lines, enhancing responsiveness to market shifts. Fifth, fostering strategic alliances with software innovators accelerates the development of AI-driven inspection and predictive maintenance tools, unlocking higher return on automation investments.
Finally, expanding aftermarket services and subscription-based models can generate recurring revenue streams and deepen customer relationships. By implementing these recommendations, companies will strengthen their competitive positioning and deliver sustainable value to stakeholders.
Explore AI-driven insights for the Machine Tending Solution market with ResearchAI on our online platform, providing deeper, data-backed market analysis.
Ask ResearchAI anything
World's First Innovative Al for Market Research
Conclusion: Charting the Path Forward
Machine tending solutions have matured into a cornerstone of modern manufacturing, bridging the gap between human expertise and automated precision. Through strategic integration of robotics, vision and analytics, manufacturers can achieve higher throughput, consistent quality and improved safety. Despite emerging challenges such as tariff disruptions and capital constraints, the adaptability of modular architectures and the rise of collaborative platforms provide a clear path forward.
By leveraging segmentation insights, understanding regional nuances and aligning with leading technology partners, enterprises can craft automation roadmaps that align with operational imperatives and long-term growth objectives. The businesses that proactively embrace digitalization, invest in talent development and refine sourcing strategies will emerge as leaders in the next wave of industrial transformation.
This section provides a structured overview of the report, outlining key chapters and topics covered for easy reference in our Machine Tending Solution market comprehensive research report.
- Preface
- Research Methodology
- Executive Summary
- Market Overview
- Market Dynamics
- Market Insights
- Cumulative Impact of United States Tariffs 2025
- Machine Tending Solution Market, by Industry Applications
- Machine Tending Solution Market, by Machine Types
- Machine Tending Solution Market, by Functionality
- Machine Tending Solution Market, by Component Types
- Machine Tending Solution Market, by Customer Size
- Machine Tending Solution Market, by Distribution Channels
- Americas Machine Tending Solution Market
- Asia-Pacific Machine Tending Solution Market
- Europe, Middle East & Africa Machine Tending Solution Market
- Competitive Landscape
- ResearchAI
- ResearchStatistics
- ResearchContacts
- ResearchArticles
- Appendix
- List of Figures [Total: 28]
- List of Tables [Total: 1126 ]
Call to Action: Connect with Our Sales & Marketing Lead
To access in-depth analysis, custom insights and comprehensive data on machine tending solutions, reach out to Ketan Rohom, Associate Director of Sales & Marketing. Whether you are refining your automation strategy or evaluating new technology partners, Ketan can guide you to the precise market intelligence you need to drive confident decision-making and sustainable growth.
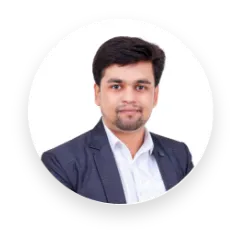
- When do I get the report?
- In what format does this report get delivered to me?
- How long has 360iResearch been around?
- What if I have a question about your reports?
- Can I share this report with my team?
- Can I use your research in my presentation?