The Machine Tool Market size was estimated at USD 76.84 billion in 2024 and expected to reach USD 81.15 billion in 2025, at a CAGR 5.76% to reach USD 107.54 billion by 2030.

Pioneering the Future of Precision Manufacturing
The machine tool sector stands at a pivotal crossroads as digitalization, geopolitical shifts, and evolving customer demands converge to redefine manufacturing paradigms. Advanced machining technologies are no longer confined to traditional metalworking; they are integral to industries from aerospace to healthcare, driving precision and efficiency at unprecedented scales. As emerging markets expand their industrial bases and established economies pursue reshoring initiatives, the competitive landscape intensifies, underscoring the need for strategic clarity and responsiveness.
Against this backdrop, our executive summary illuminates the critical drivers, challenges, and opportunities shaping the global machine tool industry. By synthesizing transformative trends and granular insights, we equip senior executives with the analytical framework required to navigate a rapidly shifting market. The following sections delve into the forces remapping supply chains, the tariff-induced realignments of 2025, segment-specific performance levers, regional growth trajectories, and the competitive maneuvers of leading players. A rigorous methodology underpins every conclusion, ensuring that recommendations are grounded in robust primary and secondary research.
This report empowers manufacturing leaders to anticipate disruptions, optimize investment decisions, and chart a sustainable growth path. Through a blend of strategic foresight and detailed analysis, we illuminate the road ahead for stakeholders committed to mastering the next wave of machine tool innovation.
Navigating Industry 4.0 and Emerging Disruptions
The machine tool landscape is undergoing a seismic shift fueled by the integration of smart technologies and the pursuit of operational excellence. Industry 4.0 has ushered in a new era of connectivity, where real-time data streams and predictive analytics drive machine uptime and quality control. Manufacturers increasingly adopt digital twins to simulate processes, enabling rapid iteration and minimizing waste. Additive manufacturing, while still nascent in heavy-duty machining, complements subtractive processes by facilitating complex geometries and reducing lead times for prototypes.
Sustainability initiatives have also emerged as transformative forces. Energy-efficient spindles, closed-loop cooling systems, and biodegradable tooling materials reflect a broader commitment to reducing carbon footprints across production lines. Simultaneously, the resurgence of reshoring and nearshoring strategies is reshaping global supply networks, compelling machine tool providers to offer agile delivery models and localized service capabilities.
As technological convergence accelerates, collaboration between machine builders, software developers, and research institutions has intensified. Startups specializing in artificial intelligence and robotics are partnering with established original equipment manufacturers to co-develop next-generation platforms. This cross-pollination of expertise is driving breakthroughs in autonomous machining cells, where machines self-optimize cutting parameters to enhance throughput and part accuracy. The result is a manufacturing ecosystem defined by flexibility, sustainability, and intelligent automation.
Assessing the 2025 Tariff Shock on Machine Tools
The tariff measures enacted in 2025 have triggered far-reaching consequences for the machine tool industry. Imposed duties on key components and finished equipment have elevated input costs, compelling manufacturers to reevaluate sourcing strategies. For domestic producers, the levies have created a temporary advantage by insulating them from lower-cost imports. However, sustained pricing pressures have forced end users to absorb higher capital expenditures or seek creative financing solutions.
Global suppliers have responded by diversifying production footprints and forging partnerships with contract manufacturers outside affected regions. These strategic relocations, while mitigating tariff impacts, introduce fresh operational challenges such as regulatory compliance and quality control across dispersed sites. Meanwhile, after-sales service revenues have become increasingly critical to offset margin compression, with service contracts, spare parts, and retrofits emerging as vital profit centers.
On the demand side, certain sectors have shown resilience despite rising costs. Automotive and aerospace OEMs continue to invest in high-precision equipment to meet stringent quality certifications, while energy and utilities firms prioritize heavy-duty machines for infrastructure maintenance. Conversely, smaller shops in price-sensitive industries have deferred capital investments or migrated toward manual alternatives. This polarization underscores the importance of segment-specific strategies to sustain growth in a tariff-constrained environment.
Unveiling Market Segments Driving Machine Tools Demand
In analyzing the market across machine type, broaching machines maintain a niche presence, serving specialized applications in gear and spline manufacturing, while drilling and turning centers dominate volumes due to their versatility in prototyping and high-mix production. Grinding equipment commands premium pricing for finishing operations that demand sub-micron tolerances, whereas milling machines underpin a broad array of machining tasks across metals and composites. Planers and shapers, though representing a smaller share, remain indispensable for low-volume, large-format components with unique geometric requirements.
When segmented by control type, the ascendancy of computer numerical control platforms highlights the industry’s drive for automation and precision, even as direct numerical control systems persist in retrofit scenarios. Traditional numerical control interfaces continue to serve entry-level applications but face gradual obsolescence. Across the automation spectrum, fully automatic cells are increasingly favored by high-throughput manufacturers seeking minimal human intervention, while manual machines retain relevance in low-volume workshops for their flexibility and lower capital outlay.
End user diversity further complicates demand patterns. Aerospace firms demand multi-axis machining centers tailored for lightweight alloys, while automotive producers invest in robust, high-speed lines for chassis and engine components. Electronics manufacturers prioritize micro-milling machines for circuit board enclosures, and energy companies deploy heavy-duty turning lathes for turbine shafts. Healthcare device makers rely on precision grinders and milling machines for surgical tools, whereas industrial machinery producers maintain a balanced mix based on product complexity. Distribution channels bifurcate between established offline dealer networks offering hands-on demonstrations and emerging online platforms that streamline procurement through digital catalogs and virtual consultations.
This comprehensive research report categorizes the Machine Tool market into clearly defined segments, providing a detailed analysis of emerging trends and precise revenue forecasts to support strategic decision-making.
- Machine Type
- Control Type
- Automation Level
- End User Industry
- Distribution Channel
Regional Dynamics Steering Global Market Growth
The Americas region continues to leverage advanced manufacturing initiatives and governmental incentives to upgrade aging equipment, fostering strong demand for retrofits and new installations alike. The United States, in particular, has seen a renaissance of domestic machining centers as reshoring programs gain momentum and OEMs seek supply chain resilience. Canada’s growing aerospace cluster further amplifies demand for multi-axis machining solutions, while Mexico’s automotive plants maintain steady procurement for high-volume lines and robust service ecosystems.
Within Europe, Middle East and Africa, regulatory alignment on emissions and energy use has spurred investment in energy-efficient spindles and enclosed machining cells across Western Europe. The Middle East’s diversification away from hydrocarbons has propelled spending on industrial machinery for defense and infrastructure projects. Meanwhile, North African countries are gradually building machining capabilities to support local automotive assembly and electronics manufacturing, albeit with lingering challenges in financing and logistics.
Asia-Pacific remains the fastest-growing market, driven by China’s ongoing industrial consolidation and India’s government-backed manufacturing corridors. Southeast Asian nations, led by Vietnam and Thailand, are emerging as low-cost machining hubs for consumer electronics and automotive components. Japan and South Korea continue to command premium segments with ultra-precision grinders and high-speed milling centers, benefiting from deep R&D investments and mature supply chains.
This comprehensive research report examines key regions that drive the evolution of the Machine Tool market, offering deep insights into regional trends, growth factors, and industry developments that are influencing market performance.
- Americas
- Europe, Middle East & Africa
- Asia-Pacific
Competitive Landscape Leaders and Innovators in Machine Tools
Leading machine tool manufacturers have intensified R&D spending to differentiate through advanced control algorithms, integrated sensors, and machine learning capabilities. Heritage players in Japan and Germany retain technological edges in multi-axis platforms, while North American firms excel in modular, scalable cells tailored for small to mid-size enterprises. Partnerships between software providers and machine builders are becoming more common, enabling seamless integration of shop floor execution systems and enterprise resource planning modules.
Recent mergers and acquisitions underscore a trend toward consolidation. Larger conglomerates are acquiring specialized startups focused on robotics and vision systems to round out their automation portfolios. Concurrently, service-oriented business models are gaining prominence, with usage-based leasing and subscription offerings allowing end users to convert capital expenditures into predictable operating costs. This shift has sparked competition among aftermarket networks to deliver remote diagnostics, predictive maintenance, and rapid spare parts fulfillment.
In parallel, regional champions in emerging markets are carving out niches by offering competitively priced machines adapted to local energy and infrastructure constraints. These agile competitors often supplement equipment sales with training programs and financing solutions, establishing stronger customer relationships. As the market evolves, success will hinge on the ability to marry hardware excellence with digital services and to navigate the interplay between global scale and local responsiveness.
This comprehensive research report delivers an in-depth overview of the principal market players in the Machine Tool market, evaluating their market share, strategic initiatives, and competitive positioning to illuminate the factors shaping the competitive landscape.
- 3D Systems, Inc.
- AMADA MACHINERY CO., LTD.
- Autodesk, Inc.
- BIG DAISHOWA SEIKI CO., LTD.
- Ceratizit S A
- CHIRON Group SE
- Dassault Systèmes SE
- DMG MORI CO., LTD.
- DN Solutions
- FANUC Corporation
- FFG European & American Holdings GmbH
- Fraisa SA
- Gleason Corporation
- Guhring, Inc.
- Haas Automation Inc.
- Hardinge Inc.
- Hexagon AB
- Hyundai WIA Corporation
- Ingersoll Machine Tools, Inc.
- ISCAR LTD.
- JTEKT Corporation
- Kennametal Inc.
- Komatsu NTC Ltd.
- Kyocera Corporation
- Makino Inc.
- Mitsubishi Electric Corporation
- Murata Machinery, Ltd.
- Nachi-Fujikoshi Corp
- Okuma Corporation
- OSG USA, INC.
- PTC Inc.
- Renishaw plc
- Robert Bosch GmbH
- Sandvik Group
- Schuler AG
- Siemens AG
- Stanley Black & Decker, Inc.
- Sumitomo Electric Hartmetall GmbH
- Tongtai Machine & Tool Co., Ltd.
- TRUMPF Inc.
- Yamazaki Mazak Corporation
Strategic Imperatives for Machine Tool Executives
Executives must prioritize digital transformation by investing in IoT-enabled platforms and digital twins to enhance predictive maintenance and reduce unplanned downtime. Diversifying supply chains beyond tariff-exposed regions will mitigate geopolitical risks; forming strategic partnerships with contract manufacturers in tariff-free zones can preserve cost advantages while maintaining quality standards. Embracing green manufacturing through energy recovery systems and eco-friendly cutting fluids will satisfy regulatory requirements and bolster brand reputation among sustainability-minded customers.
To unlock new revenue streams, machine tool firms should expand aftermarket service portfolios, offering performance-based contracts and remote monitoring services. Cultivating talent through apprenticeship programs and partnerships with technical institutes will address the widening skills gap, ensuring a pipeline of operators proficient in advanced controls and data analytics. Collaboration with software firms to develop open automation architectures will accelerate deployment of plug-and-play modules, reducing integration times and total cost of ownership.
Finally, leaders should adopt a customer-centric approach by co-creating solutions with key accounts, tailoring machine configurations to specific production challenges. Pilot projects that demonstrate return on investment in high-profile verticals can serve as reference cases, accelerating broader adoption. By aligning technology roadmaps with end-user priorities, machine tool providers will secure lasting competitive advantage and drive industry-wide progress.
Rigorous Methodology Behind Our Market Analysis
Our analysis draws on a hybrid research framework combining primary interviews with senior executives, plant managers, and product engineers across leading OEMs and end-user segments. These conversations were complemented by expert roundtables featuring thought leaders in automation, supply chain strategy, and sustainability. Secondary research encompassed global trade data, patent filings, and financial disclosures, ensuring a comprehensive view of market drivers and competitive dynamics.
Quantitative data was subjected to cross-validation through a triangulation process, reconciling inputs from multiple sources to enhance accuracy and consistency. A bottom-up approach was employed to assess equipment demand by application, incorporating installation rates, retrofit cycles, and utilization metrics. Regional analyses integrated macroeconomic indicators, industrial output statistics, and policy developments to contextualize growth differentials.
Advanced analytics techniques, including regression analysis and scenario modeling, were utilized to explore the potential impacts of tariff fluctuations, technology adoption rates, and supply chain disruptions. This rigorous methodology ensures that presented insights are not only reflective of current market realities but are resilient against alternative future states. The result is a robust decision-support tool that guides strategic planning and investment in the global machine tool arena.
Explore AI-driven insights for the Machine Tool market with ResearchAI on our online platform, providing deeper, data-backed market analysis.
Ask ResearchAI anything
World's First Innovative Al for Market Research
Synthesizing Insights for Informed Decision Making
The global machine tool industry is poised at the intersection of technological innovation and geopolitical realignment. Transformative forces-ranging from Industry 4.0 breakthroughs to tariff-induced supply chain recalibrations-are redefining competitive dynamics and customer expectations. Segmentation analysis reveals distinct performance drivers across machine types, control systems, and end-use industries, underscoring the need for tailored go-to-market strategies.
Regional insights highlight divergent growth profiles, with the Americas focusing on reshoring and modernization, Europe, Middle East and Africa embracing energy efficiency and defense applications, and Asia-Pacific leading volume growth through industrial expansion. In parallel, the competitive landscape is evolving as legacy manufacturers augment their digital capabilities and newcomers differentiate through localized service models.
For industry leaders, the path forward demands a balanced emphasis on digital transformation, sustainability, and supply chain agility. By leveraging rigorous research and embracing customer-centric innovation, firms can unlock new value streams and fortify their market positions. The insights presented herein offer a clear roadmap for stakeholders committed to mastering the next era of machine tool manufacturing.
This section provides a structured overview of the report, outlining key chapters and topics covered for easy reference in our Machine Tool market comprehensive research report.
- Preface
- Research Methodology
- Executive Summary
- Market Overview
- Market Dynamics
- Market Insights
- Cumulative Impact of United States Tariffs 2025
- Machine Tool Market, by Machine Type
- Machine Tool Market, by Control Type
- Machine Tool Market, by Automation Level
- Machine Tool Market, by End User Industry
- Machine Tool Market, by Distribution Channel
- Americas Machine Tool Market
- Europe, Middle East & Africa Machine Tool Market
- Asia-Pacific Machine Tool Market
- Competitive Landscape
- ResearchAI
- ResearchStatistics
- ResearchContacts
- ResearchArticles
- Appendix
- List of Figures [Total: 26]
- List of Tables [Total: 241 ]
Secure Your Comprehensive Machine Tool Market Intelligence
For decision makers seeking to harness the full potential of machine tool market insights, direct your inquiries to Ketan Rohom, Associate Director of Sales & Marketing. Engage with his team to explore tailored packages, gain deeper analytical briefings, and secure access to exclusive data sets that will empower strategic planning. Reach out today to transform your market intelligence into actionable growth strategies and stay ahead of industry disruptions.
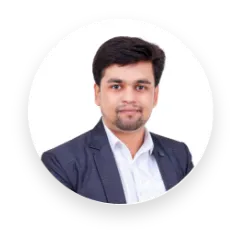
- How big is the Machine Tool Market?
- What is the Machine Tool Market growth?
- When do I get the report?
- In what format does this report get delivered to me?
- How long has 360iResearch been around?
- What if I have a question about your reports?
- Can I share this report with my team?
- Can I use your research in my presentation?