The Machining Centers Market size was estimated at USD 25.47 billion in 2024 and expected to reach USD 27.06 billion in 2025, at a CAGR 6.51% to reach USD 37.19 billion by 2030.

Revolutionizing Production with Next-Generation Machining Centers
The machining centers sector stands at a pivotal juncture as manufacturers worldwide strive to enhance precision, throughput, and cost efficiency. Recent technological developments have accelerated a transition toward smarter, more interconnected equipment capable of adaptive machining strategies. As digitalization proliferates across shop floors, executives and engineers alike must navigate a complex web of automation platforms, data analytics tools, and sustainable manufacturing practices. This report offers a panoramic yet detailed perspective, synthesizing critical factors that shape the competitive landscape.
With rising demand from aerospace, automotive, medical devices, and energy sectors, machining centers have become integral to streamlining production cycles and reducing waste. The integration of advanced control systems and multi-axis architectures enables more intricate part geometries while maintaining stringent quality thresholds. Simultaneously, supply chain disruptions and shifting trade policies underscore the need for agility in procurement and planning. By examining recent market shifts, this analysis elucidates how leading manufacturers are harnessing emerging technologies to redefine productivity benchmarks.
Structured to deliver actionable intelligence, the report addresses strategic priorities across market participants, from OEMs to end users. In the following pages, readers will gain clarity on transformative trends, tariff implications, segmentation nuances, regional dynamics, and the competitive actions shaping growth trajectories.
Emerging Forces Redefining the Machining Centers Ecosystem
Over the past few years, the machining centers landscape has experienced a wave of innovation that transcends incremental upgrades. The convergence of artificial intelligence with real-time sensor feedback is empowering predictive maintenance strategies that minimize unplanned downtime and extend machine lifecycles. Concurrently, the advent of digital twins has enabled engineers to simulate entire machining processes, optimizing parameters before physical runs and thus conserving both time and material resources.
Additive manufacturing is also catalyzing new hybrid systems, blending subtractive and additive capabilities in a single platform. This shift allows complex components-especially in aerospace and medical device applications-to be fabricated with superior surface finishes and internal lattice structures for lightweighting. Moreover, the rise of collaborative robots has redefined how operators interact with equipment, transforming the traditional human–machine interface into an intuitive, safety-centric workspace.
These technological strides are underpinned by evolving customer expectations for rapid customization and shorter lead times. As digital ecosystems mature, platforms that facilitate seamless data exchange between design software, shop floor control, and enterprise resource planning systems will become indispensable. The landscape is no longer defined solely by horsepower or spindle speed, but by the ability to orchestrate a connected, intelligent network of assets that drive efficiency across the value chain.
Assessing the 2025 Tariff Wave Reshaping U.S. Machining Supply Chains
In 2025, a recalibration of U.S. tariff policy has introduced a complex set of duties targeting imported machine tools, components, and raw materials. These measures, aimed at safeguarding domestic manufacturing, have triggered a comprehensive reassessment of global procurement strategies. Manufacturers are now weighing the incremental cost of higher tariffs against the agility benefits of diversified supply bases. The immediate outcome has been a shift in sourcing toward regions with preferential trade agreements, complemented by increased onshore production investment.
Tariff-induced price escalations for key modules such as linear guides, spindles, and control cabinets have compelled OEMs to renegotiate contracts and explore alternative suppliers in Asia-Pacific and Europe. At the same time, certain high-precision collets and specialized tooling segments have seen near-term supply constraints, prompting firms to stockpile critical inventory or accelerate capital expenditure on in-house fabrication capabilities. This strategic pivot has underscored the importance of robust supplier relationships and transparent cost structures.
Longer term, the tariffs are stimulating innovation in materials engineering and modular design principles, enabling easier component interchangeability and localized assembly. While some stakeholders express concern over short-term margin compression, others recognize an opportunity to bolster domestic value-add and reduce exposure to external shocks. As data continues to emerge, the machining centers market is adapting to a new equilibrium where resilience and flexibility dictate sustainable growth.
Unveiling Critical Market Divisions Driving Machine Tool Demand
A granular examination of the machining centers market reveals that configuration choices profoundly influence both application fit and return on investment. Horizontal machining centers excel in high-volume production of long, slender parts by optimizing chip evacuation, whereas vertical machining centers deliver superior visibility for complex, multi-sided workpieces. Each type’s distinct architecture informs workshop layout, automation compatibility, and programming strategies.
Axis count delineates capability tiers. Three-axis centers remain the backbone for conventional milling operations, offering cost-effective precision for prismatic components. The addition of a fourth axis opens opportunities for contour machining and reduced setup times, while five-axis machines usher in the most sophisticated level of versatility, enabling intricate geometries and undercut features in a single setup. These multi-axis systems are particularly prized in aerospace and medical device production, where design complexity meets strict tolerance demands.
The choice between CNC and manual control shapes workforce requirements and production throughput. CNC machining centers offer repeatability and integration potential within smart factory initiatives, whereas manual centers retain relevance for small-batch jobs and maintenance tasks. Sales channel dynamics further influence procurement approaches: traditional offline dealerships provide comprehensive service portfolios, while online platforms streamline lead times and price transparency. End users from aerospace and defense to energy and metal fabrication are calibrating their capital investments to align with evolving product life cycles and compliance standards, crafting a dynamic interplay between market needs and equipment capabilities.
This comprehensive research report categorizes the Machining Centers market into clearly defined segments, providing a detailed analysis of emerging trends and precise revenue forecasts to support strategic decision-making.
- Type
- Axis
- Control Type
- Sales Channel
- End-Use
Mapping Regional Dynamics in the Global Machining Centers Market
Regional trends underscore distinct competitive advantages and demand drivers within the machining centers market. In the Americas, a renewed focus on domestic reshoring has reinvigorated demand for high-speed machining and turnkey automation solutions, with U.S. and Canadian plants seeking to minimize external vulnerabilities. This region’s emphasis on aerospace, defense, and automotive innovation supports a healthy pipeline of advanced machining orders.
Across Europe, the Middle East, and Africa, stringent sustainability regulations and labor cost considerations are accelerating adoption of energy-efficient spindle technologies and automated material handling systems. German and Italian machine tool manufacturers continue to dominate this geography, exporting premium equipment while local production in emerging economies expands to address growing infrastructure and resource development projects.
Asia-Pacific remains the largest consumption hub, underpinned by robust manufacturing growth in China, Japan, South Korea, and India. Investments in smart manufacturing corridors and Industry 4.0 initiatives have fostered an ecosystem where robotics, IoT-enabled sensors, and cloud-based analytics converge. Government-led programs incentivize modernization, driving regional players to leapfrog legacy systems and establish competitive advantages through advanced machining capabilities.
This comprehensive research report examines key regions that drive the evolution of the Machining Centers market, offering deep insights into regional trends, growth factors, and industry developments that are influencing market performance.
- Americas
- Europe, Middle East & Africa
- Asia-Pacific
Profiling Industry Leaders Shaping Machining Center Innovation
The competitive landscape is characterized by a mix of established machine tool giants and nimble upstarts. Industry leaders continuously reinvest in R&D to unveil next-generation spindle architectures, precision control algorithms, and integrated automation modules. Their broad product portfolios cater to diverse end-use sectors, enabling turnkey production solutions from concept design to postprocess inspection.
Mid-tier players differentiate by emphasizing customization, service-led sales models, and rapid deployment options. These firms excel in collaborating with OEMs to deliver specialized fixtures, quick-change tooling systems, and adaptive software packages that align with unique production workflows. Their agility allows for faster prototyping cycles and more personalized client support.
Software-focused entrants are forging partnerships to embed advanced analytics into machine controls, providing real-time performance dashboards and predictive alerts. By leveraging machine learning, these companies help users optimize cutting parameters and forecast maintenance needs with greater precision. As digital ecosystems mature, alliances between hardware manufacturers and software providers will intensify, creating integrated solutions that capture value across the machining lifecycle.
This comprehensive research report delivers an in-depth overview of the principal market players in the Machining Centers market, evaluating their market share, strategic initiatives, and competitive positioning to illuminate the factors shaping the competitive landscape.
- Ace Micromatic Group
- Breton S.p.A
- Brother Industries, Ltd.
- DMG Mori Seiki Co., Ltd.
- DN Solutions Co., Ltd
- Fanuc Corporation
- FFG European & American Holdings GmbH
- GROB-WERKE GmbH & Co. KG
- Hardinge Inc.
- Hurco Companies, Inc.
- Jiuh-Yeh Precision Machinery Co., Ltd.
- JTEKT Corporation
- JUARISTI Boring and Milling Machines S.L.U.
- Komatsu NTC Ltd.
- MAG IAS GmbH
- MAKA Systems GmbH
- Makino, Inc.
- Matsuura Machinery Corporation
- Mitsubishi Electric Corporation
- Okuma Corporation
- SCM GROUP S.p.A.
- Trevisan Macchine Utensili S.p.A
- WIDMA Machining Solutions Group Limited
- Yamazaki Mazak Corporation
- Yeong Chin Machinery Industries Co., Ltd.
Strategic Playbook for Executives Navigating Machining Trends
Executives must adopt a multifaceted strategy to thrive amid rapid technological and geopolitical shifts. A prudent first step involves auditing existing equipment portfolios against emerging production requirements, identifying candidates for retrofit with IoT sensors or transitions to multi-axis platforms. Concurrently, forging strategic partnerships with control system providers and third-party integrators can accelerate digital transformation journeys.
Investments in workforce training should parallel capital expenditures, ensuring operators and maintenance teams are proficient with advanced CNC programming, data interpretation, and safety protocols. Cultivating a center of excellence for process optimization will facilitate cross-functional collaboration between engineering, IT, and operations teams, thereby unlocking productivity gains.
On the supply chain front, diversification and dual-sourcing arrangements will mitigate tariff-related risks. Establishing regional support hubs can reduce lead times and enhance service responsiveness. Finally, leaders should engage proactively in consortiums and standards bodies to influence regulatory frameworks and ensure interoperability across equipment ecosystems.
Rigorous Methodology Underpinning Market Research Findings
This market analysis is built upon a hybrid research framework combining exhaustive secondary data collection and targeted primary interviews. Proprietary industry databases and publicly available trade reports were mined to map historical trends, technology adoption rates, and policy impacts. These insights were triangulated with granular financial disclosures and patent filings from leading machinery providers.
Complementing the quantitative backbone, qualitative interviews were conducted with plant managers, OEM engineers, and procurement officers across key regions. Such dialogues illuminated real-world challenges in equipment integration, maintenance practices, and workforce readiness. The methodological rigor was further enhanced by scenario-based modeling, exploring variable tariff and technology diffusion trajectories.
Data integrity was safeguarded through cross-validation protocols, ensuring consistency between multiple data streams. A systematic scoring approach evaluated each market segment on criteria such as growth potential, competitive intensity, and regulatory complexity. This robust methodology underpins the report’s conclusions, delivering reliable guidance for strategic decision-making.
Explore AI-driven insights for the Machining Centers market with ResearchAI on our online platform, providing deeper, data-backed market analysis.
Ask ResearchAI anything
World's First Innovative Al for Market Research
Synthesis of Key Takeaways and Future Outlook
The machining centers sector is undergoing a profound transformation driven by technological convergence, evolving trade policies, and shifting customer expectations. Key takeaways reveal that advanced multi-axis systems, smart sensors, and digital twins are not mere enhancements but foundational elements for the factories of tomorrow. Tariff realignments have introduced both challenges and impetus for onshore innovation, compelling market actors to reimagine supply chain architectures and investment priorities.
Segmentation analysis highlights the nuanced interplay between machine configuration, control sophistication, sales channels, and end-use requirements, underscoring the tailored strategies needed to address distinct application needs. Regional insights reinforce the importance of location-specific dynamics, from reshoring imperatives in the Americas to smart factory initiatives in Asia-Pacific and sustainability-driven modernization in Europe, the Middle East, and Africa.
Ultimately, success in this evolving environment hinges on an integrative approach that aligns technology adoption with workforce empowerment, supply chain resilience, and strategic alliances. Companies that champion agility, foster collaborative ecosystems, and maintain a relentless focus on value delivery will set the pace for growth.
This section provides a structured overview of the report, outlining key chapters and topics covered for easy reference in our Machining Centers market comprehensive research report.
- Preface
- Research Methodology
- Executive Summary
- Market Overview
- Market Dynamics
- Market Insights
- Cumulative Impact of United States Tariffs 2025
- Machining Centers Market, by Type
- Machining Centers Market, by Axis
- Machining Centers Market, by Control Type
- Machining Centers Market, by Sales Channel
- Machining Centers Market, by End-Use
- Americas Machining Centers Market
- Europe, Middle East & Africa Machining Centers Market
- Asia-Pacific Machining Centers Market
- Competitive Landscape
- ResearchAI
- ResearchStatistics
- ResearchContacts
- ResearchArticles
- Appendix
- List of Figures [Total: 26]
- List of Tables [Total: 235 ]
Secure Your In-Depth Machining Centers Insight Today
Elevate your competitive edge with a comprehensive exploration of machining centers that deciphers market dynamics, technological breakthroughs, and strategic imperatives. Engage directly with Ketan Rohom, Associate Director of Sales & Marketing, to secure tailored insights that inform critical investment decisions, accelerate innovation roadmaps, and optimize operational efficiency. Connect today to acquire the definitive market research report and transform your strategic outlook.
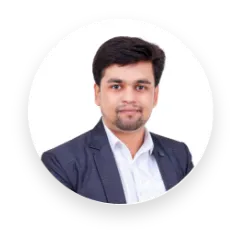
- How big is the Machining Centers Market?
- What is the Machining Centers Market growth?
- When do I get the report?
- In what format does this report get delivered to me?
- How long has 360iResearch been around?
- What if I have a question about your reports?
- Can I share this report with my team?
- Can I use your research in my presentation?