Introduction to the Marine Forgings Industry Landscape
The marine forgings sector forms a critical pillar in the shipbuilding and offshore industries, delivering robust components that withstand extreme pressure, temperature fluctuations, and corrosive sea environments. Forged elements such as shafts, propellers, and rudder assemblies underpin vessel reliability, safety, and fuel efficiency. In recent years, increasing demand for large commercial carriers, naval modernization programs, and a resurgence of offshore energy exploration have intensified pressure on manufacturers to enhance quality, reduce lead times, and curb costs. Advanced alloys and precision forging processes have emerged as central enablers of performance improvements, while sustainability imperatives and digital transformation are reshaping every stage of the value chain. Against this backdrop, decision-makers must navigate evolving trade policies, raw material volatility, and technology shifts to maintain competitive advantage. This executive summary outlines the defining trends, tariff impacts, segmentation insights, regional dynamics, leading players, and strategic imperatives that industry stakeholders should consider to chart a resilient growth trajectory.
Transformative Shifts Redefining Marine Forgings Dynamics
Over the past decade, the marine forgings landscape has undergone a profound metamorphosis driven by technological breakthroughs, material innovations, and evolving customer requirements. Additive manufacturing augmentation is now complementing traditional closed die and open die forging techniques, enabling intricate geometries in titanium and alloy steel components that were once cost-prohibitive. At the same time, advanced heat treatment processes have unlocked higher strength-to-weight ratios, allowing designers to optimize hulls and propulsion systems for fuel savings and emissions reduction. Automated forging systems, powered by artificial intelligence and robotics, are boosting throughput while minimizing human error and scrap. Meanwhile, heightened environmental regulations and a push toward decarbonization are fostering the adoption of lightweight aluminum open die forgings in recreational and commercial vessels alike. In parallel, integrated supply chain platforms are granting greater visibility into raw material sourcing, particularly for carbon steel and stainless steel inputs, thereby mitigating the risk of geopolitical disruptions. Collectively, these transformative shifts are redefining cost structures, quality benchmarks, and time-to-market expectations across the industry.
Cumulative Impact of United States Tariffs 2025 on Marine Forgings
The implementation of United States tariffs in 2025 has created a ripple effect throughout the marine forgings ecosystem. Stepped increases on imported alloy steel and aluminum forgings have prompted U.S. shipyards and component suppliers to reassess their sourcing strategies, accelerating a shift toward domestic production or nearshore partnerships. As import duties rose, lead times for critical items like contoured rolled rings and seamless rolled rings expanded, placing pressure on project schedules for both commercial shipping and naval vessel programs. In response, several defense contractors have initiated strategic alliances with U.S. forging facilities, thereby securing priority allocations for titanium closed die forgings and stainless steel open die forgings. Concurrently, margins for Tier 2 and Tier 3 manufacturers have compressed, driving consolidation and capacity rationalization across the supply chain. Although the short-term cost burden has challenged operators, the tariffs have also stimulated investment in hot forging, precision forging, and upset forging lines stateside, bolstering long-term resilience against future policy shifts.
Key Segmentation Insights Shaping Market Analysis
A granular examination of market segmentation reveals critical drivers of demand and growth opportunities. On the product spectrum, closed die forgings-including both alloy steel and titanium variants-remain indispensable for high-load, corrosion-resistant applications, while open die forgings of aluminum, carbon steel, and stainless steel cater to larger structural components where custom geometry is paramount. Ring rolled forgings, ranging from contoured rolled rings to seamless rolled rings, continue to provide superior mechanical properties for propulsion assemblies. Application segmentation underscores the prominence of connecting rods in high-speed marine engines, with piston ends and rod bolts engineered for extreme cyclic loads. Propeller systems bifurcate into controllable pitch and fixed pitch propellers, each demanding unique forging tolerances. Rudder assemblies split between balanced and semi-balanced rudders, optimizing maneuverability and stability, whereas shaft systems encompass propeller shafts and torsion shafts, the latter subdividing into collapsible shafts and universal joints to accommodate torsional dynamics. Material type further refines market understanding: alloy steel and stainless steel deliver strength in naval vessels, aluminum alloy offers weight advantages in recreational boats, and composites-spanning carbon fiber reinforced and fiberglass reinforced varieties-gain traction for specialized hull components. End-user insights spotlight commercial shipping segments such as cargo ships and tankers, defense requisitions covering naval vessels and attack or ballistic missile submarines, and the burgeoning recreational boat market with motor yachts and sailing yachts. Manufacturing process segmentation highlights cold forging for precision, hot forging for high-deformation needs, precision forging for critical tolerances, and upset forging for flanged components. Capacity-based segmentation distinguishes Tier 1 manufacturers driving volume projects, Tier 2 suppliers filling niche demands, and Tier 3 shops focusing on high-mix, low-volume runs. Finally, technological advancement segmentation showcases the integration of 3D printing augmentation for rapid prototyping, advanced heat treatment processes for enhanced mechanical performance, and automated forging systems for productivity gains.
This comprehensive research report categorizes the Marine Forgings market into clearly defined segments, providing a detailed analysis of emerging trends and precise revenue forecasts to support strategic decision-making.
- Product Type
- Application
- Material Type
- End-User
- Manufacturing Process
- Key Players by Production Capacity
- Technological Advancements
Key Regional Insights Driving Global Market Performance
Regional dynamics exert a profound influence on competitive strategies and investment decisions. In the Americas, the resurgence of U.S. shipbuilding and offshore exploration has accelerated demand for domestic forging capacity, particularly in cold forging and hot forging processes tailored to defense contractors and commercial shipping lines. Trade policies and tariffs have further incentivized nearshore partnerships in Canada and Mexico, creating a North American supply corridor for stainless steel and carbon steel open die forgings. In Europe, the Middle East and Africa region, regulatory frameworks emphasizing emissions reduction and circular economy principles are driving manufacturers to refine heat treatment protocols and recycle alloy scrap more efficiently. European yards are also pioneering composite-metal hybrid structures, combining fiberglass or carbon fiber reinforced composites with traditional stainless steel forgings to reduce weight and enhance corrosion resistance in both naval and recreational segments. In Asia-Pacific, rapid expansion of commercial shipping fleets, naval modernization programs in key nations, and the emergence of precision forging hubs in India and Southeast Asia are reshaping capacity balances. Local players are investing heavily in automated forging systems and precision forging lines to meet growing demand for propeller shafts, torsion shafts, and contoured rolled rings, while also integrating 3D printing augmentation to expedite design iterations and reduce time-to-market.
This comprehensive research report examines key regions that drive the evolution of the Marine Forgings market, offering deep insights into regional trends, growth factors, and industry developments that are influencing market performance.
- Americas
- Asia-Pacific
- Europe, Middle East & Africa
Key Companies Insights Illustrating Competitive Landscape
The competitive landscape is anchored by a cohort of global leaders and specialized fabricators. American Axle & Manufacturing Holdings, Inc. and ATI Inc. leverage extensive production networks to serve both defense and commercial shipbuilders with high-strength alloy steel closed die forgings. Ellwood Group, Inc. and Farinia Group provide integrated processing-from forging to heat treatment-for naval and offshore applications, while FRISA Forjados, S.A. de C.V. excels in automotive-grade technologies that cross over into marine forging needs. Huntington Ingalls Industries, Inc. anchors U.S. naval supply chains with precision forging capabilities, and Jacquet Metals (North America) specializes in critical stainless steel and aluminum alloy components. Japan Casting & Forging Corporation brings decades of expertise in seamless rolled rings and high-purity alloys, whereas JSW Steel Ltd and L&T Special Steels and Heavy Forgings Private Limited are expanding capacity in the Asia-Pacific region for both hot and cold forging processes. Milwaukee Forge, LLC and Precision Castparts Corp. (PCC) deliver mission-critical components for high-performance vessels, while Scot Forge Company maintains a reputation for large-scale ring rolled solutions. Shandong Iraeta Heavy Industry Stock Co., Ltd. is scaling advanced heat treatment and forging lines in China, and Thyssenkrupp Forged Technologies continues to innovate in automated forging systems and digital quality assurance across Europe.
This comprehensive research report delivers an in-depth overview of the principal market players in the Marine Forgings market, evaluating their market share, strategic initiatives, and competitive positioning to illuminate the factors shaping the competitive landscape.
- American Axle & Manufacturing Holdings, Inc.
- ATI Inc.
- Ellwood Group, Inc.
- Farinia Group
- FRISA Forjados, S.A. de C.V.
- Huntington Ingalls Industries, Inc.
- Jacquet Metals (North America)
- Japan Casting & Forging Corporation (JCFC)
- JSW Steel Ltd
- L&T Special Steels and Heavy Forgings Private Limited
- Milwaukee Forge, LLC
- Precision Castparts Corp. (PCC)
- Scot Forge Company
- Shandong Iraeta Heavy Industry Stock Co., Ltd.
- Thyssenkrupp Forged Technologies
Actionable Recommendations for Industry Leaders to Capitalize on Emerging Trends
Industry leaders should pursue targeted strategies to sustain growth and fortify market position. First, accelerating investment in automated forging systems will unlock productivity gains and ensure consistent quality for high-volume and high-precision components. Second, expanding capabilities in advanced heat treatment processes and 3D printing augmentation will enable rapid prototyping and more efficient metallurgy validation, particularly for titanium closed die forgings in defense applications. Third, diversifying raw material sourcing by cultivating partnerships with domestic alloy steel, aluminum, and composite suppliers will mitigate exposure to future tariff fluctuations and geopolitical disruptions. Fourth, optimizing manufacturing footprints through nearshore facilities or brownfield expansions in strategic regions like North America and Southeast Asia will reduce lead times and logistical complexities. Fifth, forging closer relationships with naval architects and propulsion system OEMs can secure early involvement in design phases, unlocking customization opportunities for balanced rudders, collapsible torsion shafts, and controllable pitch propellers. By implementing these measures, organizations can enhance operational agility, control costs, and deliver greater value to both military and commercial stakeholders.
Explore AI-driven insights for the Marine Forgings market with ResearchAI on our online platform, providing deeper, data-backed market analysis.
Ask ResearchAI anything
World's First Innovative Al for Market Research
Conclusion: Navigating the Future of Marine Forgings
The marine forgings industry stands at a critical juncture where technological innovation, regulatory dynamics, and shifting trade policies intersect. Stakeholders who proactively embrace advanced manufacturing techniques and strengthen regional supply chains will be best positioned to meet escalating performance demands. As market leaders refine segmentation strategies and deepen collaboration with OEMs, they can unlock new applications in defense, commercial shipping, and recreational boating. Ultimately, those who combine data-driven decision-making with strategic investments in automation, sustainability, and materials expertise will chart the most resilient path forward.
This section provides a structured overview of the report, outlining key chapters and topics covered for easy reference in our Marine Forgings market comprehensive research report.
- Preface
- Research Methodology
- Executive Summary
- Market Overview
- Market Dynamics
- Market Insights
- Cumulative Impact of United States Tariffs 2025
- Marine Forgings Market, by Product Type
- Marine Forgings Market, by Application
- Marine Forgings Market, by Material Type
- Marine Forgings Market, by End-User
- Marine Forgings Market, by Manufacturing Process
- Marine Forgings Market, by Key Players by Production Capacity
- Marine Forgings Market, by Technological Advancements
- Americas Marine Forgings Market
- Asia-Pacific Marine Forgings Market
- Europe, Middle East & Africa Marine Forgings Market
- Competitive Landscape
- ResearchAI
- ResearchStatistics
- ResearchContacts
- ResearchArticles
- Appendix
- List of Figures [Total: 30]
- List of Tables [Total: 902 ]
Call to Action: Engage with Ketan Rohom for Comprehensive Market Intelligence
To access the full market intelligence report and gain deeper insights into competitive benchmarks, regional outlooks, and cutting-edge technological innovations, contact Ketan Rohom, Associate Director, Sales & Marketing. Engage directly with Ketan to explore customized research solutions, obtain detailed company profiles, and secure the data you need to drive strategic decisions. Reach out today to unlock comprehensive analysis and transform your marine forgings strategy.
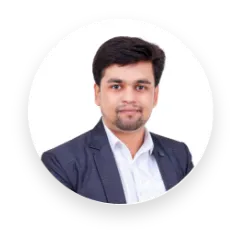
- When do I get the report?
- In what format does this report get delivered to me?
- How long has 360iResearch been around?
- What if I have a question about your reports?
- Can I share this report with my team?
- Can I use your research in my presentation?