Introduction to the Critical Role of Mass Flow Controllers in Semiconductor Manufacturing
Manufacturing semiconductors demands an extraordinary level of precision and repeatability, and the accuracy of gas delivery systems is one of the most critical factors affecting yield and device performance. Mass flow controllers manage the flow of process gases-ranging from corrosive chemistries to inert carriers-with exacting tolerances measured in sccm and beyond. By ensuring stable, leak-free, and responsive control across a wide dynamic range, these devices underpin key steps in deposition, etching, and lithography. In an era of ever-shrinking nodes and advanced packaging techniques, the role of mass flow controllers has expanded beyond simple regulation to become central to process optimization, predictive maintenance, and real-time monitoring.
As semiconductor fabs embrace digital transformation and adopt advanced analytics, mass flow controllers are evolving into intelligent devices capable of self-calibration, remote diagnostics, and seamless integration with Manufacturing Execution Systems (MES). The transition to higher wafer diameters, new materials, and complex multi-gas processes places further demands on these instruments. This Executive Summary provides a concise yet comprehensive exploration of the forces shaping the mass flow controller market for semiconductors, from technological advancements and regulatory pressures to the competitive landscape and strategic imperatives for industry leaders.
Transformative Shifts Reshaping Mass Flow Controller Technology
The semiconductor industry is undergoing its most significant technological leap in decades, driven by the convergence of miniaturization, multi-patterning techniques, and the adoption of new materials. In response, mass flow controller manufacturers are pushing the boundaries of sensor accuracy, response time, and integration capability. Traditional thermal mass and differential pressure technologies are being complemented by Coriolis-based instruments offering direct mass measurement, as well as ultrasonic flow meters that deliver zero-pressure-drop monitoring for fragile chemistries.
Concurrently, the rise of Industry 4.0 has accelerated the demand for digital twins and closed-loop process control, compelling suppliers to embed advanced communication protocols and data analytics within their products. Moreover, stringent environmental regulations and sustainability targets are driving innovation in leak detection, gas recapture, and energy-efficient designs. Additive manufacturing of exotic alloy flow bodies and hermetically sealed designs optimized for corrosive gases is opening new frontiers in performance and reliability.
This era of transformation is defined by the integration of hardware, software, and services. Leading providers are developing ecosystem partnerships with fab automation vendors, ensuring seamless interoperability. As a result, the market is shifting from a purely transactional model to a service-centric approach, emphasizing value-added features such as predictive maintenance, rapid field calibration, and lifecycle management.
Cumulative Impact of United States Tariffs 2025 on Supply Chains
The implementation of new tariffs by the United States in 2025 has introduced fresh complexities into the semiconductor mass flow controller supply chain. With levies applied to key components-including stainless steel fittings, exotic alloy sensor elements, and electronics modules-manufacturers are encountering increased input costs and longer lead times. Suppliers have responded by diversifying production footprints, exploring tariff-free sourcing of critical raw materials, and negotiating long-term agreements with strategic partners to hedge against further escalations.
In addition to direct cost implications, tariff-induced uncertainties are influencing inventory strategies and capital investment decisions among fabricators. Some fabs are pre-ordering components to secure pricing, while others are fast-tracking in-house qualification of alternative controller designs. The combined effect of these measures is a more fragmented sourcing landscape and an accelerated push toward vertical integration. Ultimately, the cumulative impact of tariffs is reshaping procurement roadmaps, intensifying collaborations between suppliers and end users, and elevating the importance of supply chain transparency in decision-making processes.
Key Insights from Comprehensive Segmentation Analysis
A nuanced understanding of segmentation is critical to navigating market opportunities and matching product offerings to process requirements. When flow rate categories-high, medium, and low-are examined, high flow controllers excel in bulk deposition processes while low flow variants deliver the precision demanded by atomic layer deposition. Elastomer-sealed designs offer cost-effective solutions for benign gases, whereas metal-sealed and pressure-insensitive types ensure uncompromised integrity in corrosive or ultra-high-purity environments.
Material choices further refine performance profiles: ceramic bodies resist abrasion and thermal shock, exotic alloys yield exceptional chemical compatibility, fluoride-resistant materials safeguard against aggressive etchants, and stainless steel remains the baseline for general-purpose deployments. Compatibility segmentation underscores the need for specialized variants: corrosive gas compatible controllers incorporate advanced coatings, non-corrosive gas types emphasize cost efficiency, and resistive gas compatible instruments prevent contamination in slight leak scenarios.
Application-specific demands drive deeper specialization. Atomic layer deposition strains the lower end of flow ranges, while chemical vapor deposition splits into high temperature and low pressure subcategories. Physical vapor deposition and lithography require stable flows under vacuum conditions, whereas plasma etching bifurcates into deep reactive ion etching and photoresist strip functions. Technology segmentation highlights the rise of Coriolis instruments, particularly those leveraging direct capillary measurement, alongside differential pressure, thermal mass, and ultrasonic approaches. Functionality options-analog for simplicity, digital for connectivity, and proportional for fine-tuning-address diverse control philosophies. End-user industries span aerospace, chemical processing, medical devices, and semiconductors, each imposing unique regulatory and purity specifications. Finally, pressure range, demand type, and flow direction segmentation complete the landscape, enabling commercial and industrial controllers rated from sub-100 PSIG to above 500 PSIG in both unidirectional and bidirectional configurations.
This comprehensive research report categorizes the Mass Flow Controller For Semiconductor market into clearly defined segments, providing a detailed analysis of emerging trends and precise revenue forecasts to support strategic decision-making.
- Flow Rate
- Type
- Material
- Compatibility
- Application
- Technology
- Flow Meter Functionality
- End-User Industry
- Pressure Range
- Demand
- Flow Direction
Regional Dynamics Influencing Mass Flow Controller Adoption
Regional dynamics reveal distinct drivers and constraints shaping controller adoption. In the Americas, aggressive capital expenditure in advanced node fabs and strong government incentives for domestic semiconductor manufacturing have elevated demand for high-precision, digitally enabled controllers. Local suppliers are forging partnerships with North American equipment OEMs to align product roadmaps with evolving process architectures.
Europe, Middle East & Africa (EMEA) presents a heterogeneous landscape where stringent environmental regulations and an emphasis on energy efficiency are accelerating the uptake of low-leakage, sustainable designs. Collaborative research initiatives in Germany and the Netherlands are advancing sensor materials and hermetic sealing technologies, while investments in AI-powered predictive maintenance platforms are gaining traction across the region.
Asia-Pacific remains the largest and fastest-evolving market, led by capacity expansions in China, Taiwan, South Korea, and Japan. The aggressive scaling of 300-millimeter wafer fabs and diversification into specialty semiconductor segments-such as power electronics and compound semiconductors-are driving orders for high-throughput, multi-gas controllers. Local manufacturing capabilities combined with government support for strategic technology sovereignty underpin a robust competitive environment.
This comprehensive research report examines key regions that drive the evolution of the Mass Flow Controller For Semiconductor market, offering deep insights into regional trends, growth factors, and industry developments that are influencing market performance.
- Americas
- Asia-Pacific
- Europe, Middle East & Africa
Competitive Landscape and Leading Provider Strategies
The competitive landscape is defined by a mix of global conglomerates and specialized innovators. Advanced Energy Industries, Inc. has strengthened its position through integrated power and flow platforms, while Alicat Scientific, Inc. continues to disrupt the market with rapid-response digital controllers. Azbil Corporation leverages its automation core to deliver fully networked solutions, and Bronkhorst High-Tech B.V. focuses on miniaturized Coriolis meters for portable analytics. Brooks Instrument’s deep expertise in thermal mass technology contrasts with HORIBA STEC, CO., LTD.’s precision-calibrated product lines tailored for Japanese fabs.
MKS Instruments, Inc. and Parker Hannifin Corporation have both expanded their semiconductor portfolios via strategic acquisitions, broadening their materials compatibility and service offerings. Sensirion AG’s MEMS-based sensors and Teledyne Hastings Instruments’ vacuum meter heritage cater to niche vacuum-centric processes. Vögtlin Instruments GmbH emphasizes modularity in high-pressure applications, while Yokogawa Electric Corporation integrates flow control with comprehensive process automation suites. This ecosystem of established brands and agile newcomers fosters continuous innovation and intensifies the race for software-driven differentiation.
This comprehensive research report delivers an in-depth overview of the principal market players in the Mass Flow Controller For Semiconductor market, evaluating their market share, strategic initiatives, and competitive positioning to illuminate the factors shaping the competitive landscape.
- Advanced Energy Industries, Inc.
- Alicat Scientific, Inc.
- Azbil Corporation
- Bronkhorst High-Tech B.V.
- Brooks Instrument
- HORIBA STEC, CO., LTD.
- MKS Instruments, Inc.
- Parker Hannifin Corporation
- Sensirion AG
- Teledyne Hastings Instruments
- Vögtlin Instruments GmbH
- Yokogawa Electric Corporation
Actionable Recommendations for Industry Leaders to Gain Competitive Advantage
Industry leaders must adopt a multi-pronged strategy to thrive in this dynamic environment. First, investing in digital enablement-by embedding cloud connectivity, advanced analytics, and remote calibration capabilities-will differentiate offerings and support predictive maintenance services. Second, diversifying supply chains and qualifying multiple raw-material sources will hedge against tariff volatility and ensure uninterrupted production, particularly for exotic alloy and fluoride-resistant components.
Third, deepening partnerships with semiconductor equipment OEMs and fab integrators will accelerate co-development cycles, ensuring new controller designs align with emerging process nodes and materials. Fourth, prioritizing sustainability through energy-efficient designs, leak-detection technologies, and recyclable materials will appeal to regulators and socially responsible customers alike. Fifth, expanding modular product lines that balance analog simplicity with digital sophistication will address the full spectrum of end-user preferences. Lastly, allocating R&D resources to next-generation measurement technologies-such as miniaturized Coriolis and ultrasonic sensors-will position organizations to capture growth in specialty semiconductor applications.
Explore AI-driven insights for the Mass Flow Controller For Semiconductor market with ResearchAI on our online platform, providing deeper, data-backed market analysis.
Ask ResearchAI anything
World's First Innovative Al for Market Research
Conclusion: Navigating Complexity with Strategic Insight
Mass flow controllers have evolved from standalone instruments to integrated nodes within the semiconductor fabrication ecosystem, balancing precision, reliability, and connectivity. As the industry contends with advanced nodes, diversified materials, and geopolitical headwinds, controller manufacturers must navigate complex segmentation, regional nuances, and tariff-induced supply chain shifts. The convergence of digital transformation, sustainability imperatives, and collaborative innovation underscores the necessity of a holistic approach-one that synchronizes product development, strategic partnerships, and service offerings.
By leveraging insights into flow rate, material compatibility, technological architectures, and regional dynamics, stakeholders can tailor strategies to specific market pockets, while remaining agile in the face of regulatory and geopolitical changes. The future belongs to those who embrace data-driven differentiation and foster collaborative ecosystems that anticipate the evolving demands of semiconductor fabrication.
This section provides a structured overview of the report, outlining key chapters and topics covered for easy reference in our Mass Flow Controller For Semiconductor market comprehensive research report.
- Preface
- Research Methodology
- Executive Summary
- Market Overview
- Market Dynamics
- Market Insights
- Cumulative Impact of United States Tariffs 2025
- Mass Flow Controller For Semiconductor Market, by Flow Rate
- Mass Flow Controller For Semiconductor Market, by Type
- Mass Flow Controller For Semiconductor Market, by Material
- Mass Flow Controller For Semiconductor Market, by Compatibility
- Mass Flow Controller For Semiconductor Market, by Application
- Mass Flow Controller For Semiconductor Market, by Technology
- Mass Flow Controller For Semiconductor Market, by Flow Meter Functionality
- Mass Flow Controller For Semiconductor Market, by End-User Industry
- Mass Flow Controller For Semiconductor Market, by Pressure Range
- Mass Flow Controller For Semiconductor Market, by Demand
- Mass Flow Controller For Semiconductor Market, by Flow Direction
- Americas Mass Flow Controller For Semiconductor Market
- Asia-Pacific Mass Flow Controller For Semiconductor Market
- Europe, Middle East & Africa Mass Flow Controller For Semiconductor Market
- Competitive Landscape
- ResearchAI
- ResearchStatistics
- ResearchContacts
- ResearchArticles
- Appendix
- List of Figures [Total: 38]
- List of Tables [Total: 640 ]
Contact Ketan Rohom to Acquire the Full Market Research Report
To explore these insights in greater depth and tailor them to your organization’s goals, please reach out to Ketan Rohom, Associate Director, Sales & Marketing, for access to the full mass flow controller market research report. His expertise will guide you through customized findings and actionable intelligence to inform your strategic roadmap.
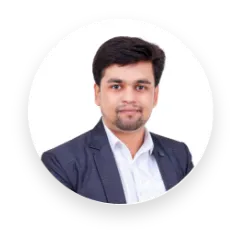
- When do I get the report?
- In what format does this report get delivered to me?
- How long has 360iResearch been around?
- What if I have a question about your reports?
- Can I share this report with my team?
- Can I use your research in my presentation?