The Medical Device Outsourced Manufacturing Market size was estimated at USD 34.87 billion in 2024 and expected to reach USD 38.86 billion in 2025, at a CAGR 11.02% to reach USD 65.30 billion by 2030.

Shaping the Future of Outsourced Medical Device Manufacturing
The outsourced manufacturing segment for medical devices has evolved into a critical cornerstone for original equipment manufacturers seeking to optimize costs, accelerate time to market, and mitigate regulatory complexity. As product pipelines grow increasingly sophisticated, OEMs are leveraging specialized partners to deliver high-precision components, innovative materials, and end-to-end services that span design validation through sterilization. This shift reflects a broader transformation in which outsourcing has moved beyond commoditized labor to become a strategic lever for differentiation and risk management.
Recent advancements in additive manufacturing, miniaturized electronics, and biocompatible polymers have intensified demand for niche capabilities that are often beyond the scope of in-house operations. Meanwhile, global supply chain disruptions have underscored the importance of diversified sourcing and resilient logistics networks. In this context, leading manufacturers are no longer simply offloading production tasks; they are forging collaborative development models that align incentives, share intellectual property protections, and integrate planning systems. The interplay of these factors is reshaping cost structures, channel relationships, and R&D investment strategies.
This report delves into the key drivers and constraints shaping outsourced medical device manufacturing, offering a panoramic view of market dynamics without projecting specific forecasts. By examining current practices, emerging trends, and strategic imperatives, readers will gain a clear understanding of how to harness outsourced capabilities effectively while steering through regulatory, economic, and competitive headwinds.
Emerging Forces Redefining the Outsourcing Landscape
A confluence of technological breakthroughs, regulatory reforms, and shifting partnership models is driving a profound metamorphosis in the outsourced medical device manufacturing arena. Digitalization is at the forefront, with sophisticated automation platforms, data analytics, and digital twins enabling earlier defect detection, tighter quality controls, and accelerated validation cycles. This technological shift is complemented by demands for personalized therapies, which require agile production processes capable of low-volume, high-mix manufacturing without compromising compliance or traceability.
Concurrently, tightening regulatory scrutiny and evolving standards for biocompatibility, software validation, and cybersecurity are compelling both OEMs and contract manufacturers to invest heavily in quality management systems and audit readiness. The pandemic’s enduring lessons have also amplified the value of geographically diversified facilities and multi-sourced component strategies to preempt supply chain disruptions.
Partnership models have shifted from transactional engagements to strategic alliances characterized by shared roadmaps, co-developed intellectual property, and outcome-based contracting. This trend reflects an increased focus on end-to-end value creation rather than mere cost arbitrage. As a result, service providers are expanding capabilities to integrate design inputs, regulatory support, and post-market surveillance services, positioning themselves as holistic innovation enablers. The cumulative effect of these transformative forces is a more resilient, responsive, and technologically empowered outsourcing ecosystem.
Navigating the Ripple Effects of 2025 US Tariff Adjustments
The introduction of new US tariff measures in early 2025 has introduced additional cost pressures across the outsourced manufacturing supply chain. Components and raw materials imported from key manufacturing hubs now carry higher duties, driving up landed costs for contract manufacturers and their OEM clients. This tariff environment has forced many stakeholders to reevaluate sourcing strategies, with a growing emphasis on nearshoring options in North America and realigning supplier portfolios to manage duty exposure.
In response, several contract producers have accelerated investments in domestic capabilities for critical processes such as injection molding and CNC machining, while also negotiating long-term agreements with alternative international suppliers that benefit from preferential trade agreements. These shifts often carry trade-offs: while reshoring can reduce tariff-related expenses and lead times, it may also introduce higher labor costs or capacity constraints. As a result, stakeholders are employing hybrid manufacturing footprints that balance domestic and offshore production to optimize total landed cost and service levels.
Moreover, the repercussions of tariffs extend beyond immediate cost implications; they are reshaping capital allocation decisions, encouraging consolidation among smaller suppliers, and catalyzing strategic collaborations aimed at achieving economies of scale. These evolving dynamics underscore the imperative for OEMs and their partners to develop agile supply chain models and leverage data-driven scenario planning to navigate escalating trade tensions.
Dissecting Market Segments to Uncover Growth Opportunities
A nuanced understanding of market segmentation reveals where value creation and competitive differentiation are most pronounced. In terms of product type, opportunities are particularly robust in cardiology device components and in catheters and tubing systems, where precision manufacturing and stringent material standards are paramount. Orthopedic implants and surgical instruments likewise command premium outsourcing expertise given the critical nature of tolerances and implantable biocompatibility. The dental and diagnostic equipment segments are also drawing heightened attention as manufacturers seek specialized design validation and rapid prototyping services to address evolving clinician requirements.
Service type segmentation further illuminates strategic imperatives. Providers offering integrated assembly and packaging solutions that span primary and secondary packaging tasks are differentiating through end-to-end quality control and regulatory documentation capabilities. Meanwhile, design and development partners that combine concept ideation with engineering analysis are accelerating productization cycles. Logistics specialists capable of both cold chain and general freight management are in demand as temperature-sensitive biologics and point-of-care devices proliferate. On the manufacturing front, firms delivering both custom and high-volume production are positioning to meet diverse volume requirements, while prototyping services-ranging from bridge manufacturing to rapid turnaround modeling-enable iterative design validation. Sterilization options utilizing E-beam, ethylene oxide, or gamma irradiation complete the service spectrum and ensure compliance with global sterilization standards.
Process type analysis highlights the rising prominence of additive manufacturing methods such as electron beam melting, fused deposition modeling, selective laser sintering, and stereolithography for complex, lightweight components. Traditional processes like blow molding, CNC machining, extrusion, and injection molding remain foundational, particularly where economies of scale and tight tolerances are essential. Material type segmentation underscores the criticality of electronic components, including circuit boards and sensor integration, alongside metal alloys such as aluminum, stainless steel, and titanium for structural parts. Plastics-encompassing polycarbonate, polyethylene, polypropylene, and PVC-share space with high consistency and liquid silicones in applications demanding flexibility or biocompatibility. End use is likewise diversified, spanning ambulatory care centers, clinics, home healthcare devices, hospitals, and specialty centers, each with distinct regulatory and logistical requirements.
This comprehensive research report categorizes the Medical Device Outsourced Manufacturing market into clearly defined segments, providing a detailed analysis of emerging trends and precise revenue forecasts to support strategic decision-making.
- Product Type
- Service Type
- Process Type
- Material Type
- End Use
Regional Dynamics Driving Outsourced Manufacturing Strategies
Regional dynamics play a pivotal role in shaping outsourced manufacturing strategies. In the Americas, proximity to major OEM headquarters and favorable trade agreements have spurred capacity expansions in precision machining and contract assembly. Robust IP protection and a mature regulatory framework continue to attract investments in advanced manufacturing capabilities, particularly for high-value cardiology and orthopedic device production.
Across Europe, the Middle East and Africa, a diversified regulatory landscape and the presence of numerous small- to medium-sized medtech innovators have driven demand for modular and scalable outsourcing models. Providers in this region are leveraging advanced automation and digital quality management to support complex multi-market registrations and post-market surveillance requirements. The integration of risk-based quality frameworks is facilitating faster market access while ensuring compliance with evolving EU Medical Device Regulation standards.
In Asia-Pacific, the convergence of cost competitiveness, rapidly maturing regulatory regimes, and burgeoning domestic OEMs is fostering significant growth. Investment is particularly pronounced in cleanroom manufacturing, electronic component assembly, and emerging additive manufacturing hubs. Partnerships between regional contract manufacturers and global technology providers are enhancing process capabilities and driving export-oriented production. Collectively, these regional insights underscore the importance of geographically balanced networks that can flex in response to regulatory shifts, trade dynamics, and customer-specific demands.
This comprehensive research report examines key regions that drive the evolution of the Medical Device Outsourced Manufacturing market, offering deep insights into regional trends, growth factors, and industry developments that are influencing market performance.
- Americas
- Europe, Middle East & Africa
- Asia-Pacific
Competitive Landscape and Strategic Moves of Industry Leaders
Leading players in the outsourced manufacturing space are aligning their strategies around service breadth, technological prowess, and integrated quality systems. Several top contract manufacturers have broadened their portfolios to offer turnkey solutions that encompass design transfer, regulatory submission support, and post-market services. These firms are establishing centers of excellence for advanced process development, such as additive manufacturing cells equipped with electron beam and laser-based systems, while expanding capacity in traditional injection molding and CNC machining.
Collaborations between contract providers and component specialists are another emerging theme. By jointly investing in pilot production lines for sensor integration or smart packaging, companies are co-creating differentiated offerings that address the convergence of digital health and device manufacturing. Strategic acquisitions are consolidating segment expertise, enabling scale efficiencies in sterilization services or pneumatic tubing production.
Moreover, select companies are pioneering digital platforms that unify supply chain visibility, quality tracking, and design iteration feedback, thereby transforming static outsourcing relationships into dynamic, data-driven partnerships. These innovations are not merely incremental improvements; they are redefining the metrics by which outsourcing success is measured, shifting the emphasis from cost reduction to speed, flexibility, and co-innovation potential.
This comprehensive research report delivers an in-depth overview of the principal market players in the Medical Device Outsourced Manufacturing market, evaluating their market share, strategic initiatives, and competitive positioning to illuminate the factors shaping the competitive landscape.
- Jabil Inc.
- Flex Ltd.
- Sanmina Corporation
- Celestica Inc.
- Plexus Corp.
- Benchmark Electronics, Inc.
- TT Electronics plc
- Kimball Electronics, Inc.
- Integer Holdings Corporation
- SMTC Corporation
Strategic Imperatives for Leading Outsourcing Stakeholders
To thrive in a market characterized by rapid technological change, regulatory scrutiny, and supply chain volatility, industry leaders must embrace a series of strategic imperatives. First, integrating digital quality management systems that leverage real-time production data will be essential for accelerating validation cycles and reducing non-conformance rates. Second, developing modular manufacturing footprints that combine select nearshore sites with cost-effective offshore facilities can optimize total landed cost while ensuring resilience.
Third, forging co-development agreements with key OEMs around emerging technologies such as advanced polymers or microfluidic components can establish early mover advantages and protect margins. Fourth, investing in sterilization capacity with multiple modalities will secure end-to-end control over product release timelines. Fifth, expanding service bundles to include design and regulatory support will position contract providers as indispensable strategic partners rather than transactional vendors.
Finally, embedding sustainability metrics into operational processes-from material selection to waste treatment-will address evolving customer and regulatory expectations, while also unlocking potential cost savings. By aligning these actionable recommendations with internal capabilities and external market trends, stakeholders can transform outsourcing from a cost center into a catalyst for innovation and growth.
Robust Methodology Underpinning the Market Analysis
This analysis is built upon a comprehensive research framework that combines primary and secondary information sources. Primary insights were gathered through in-depth interviews with senior executives at OEMs, contract manufacturers, industry consultants, and regulatory authorities to uncover firsthand perspectives on outsourcing strategies, quality systems, and capacity planning. Secondary inputs were sourced from industry publications, regulatory databases, patent filings, and company disclosures to validate market trends and identify technology adoption patterns.
A rigorous data triangulation process ensured consistency across qualitative narratives and documented evidence. Comparative analysis of service offerings, process capabilities, and regional footprints was performed to map competitive positioning. Historical trade data and tariff schedules were examined to assess the impact of recent policy changes on sourcing decisions. Moreover, technology roadmaps and academic research were reviewed to gauge the maturity of advanced manufacturing methods such as stereolithography and electron beam melting.
Throughout the research, quality checkpoints and peer reviews were institutionalized to maintain analytical integrity and minimize cognitive biases. The resultant framework delivers a holistic view of the outsourced medical device manufacturing landscape, enabling stakeholders to make informed strategic decisions.
Explore AI-driven insights for the Medical Device Outsourced Manufacturing market with ResearchAI on our online platform, providing deeper, data-backed market analysis.
Ask ResearchAI anything
World's First Innovative Al for Market Research
Synthesis of Key Takeaways and Industry Implications
The outsourced medical device manufacturing industry is at an inflection point where technological innovation, regulatory complexity, and geopolitical influences intersect. Quality and speed have become equally non-negotiable, demanding that contract partners evolve from passive suppliers to proactive collaborators. The segmentation analysis underscores how distinct product types, service offerings, processes, materials, and end-use applications each present unique challenges and opportunities.
Regional dynamics further highlight that a one-size-fits-all approach to outsourcing is untenable. Instead, a tailored network that leverages the strengths of the Americas, Europe, the Middle East and Africa, and Asia-Pacific will be essential for balancing cost, compliance, and responsiveness. Leading companies are already differentiating through integrated digital platforms, co-development alliances, and strategic capacity expansions.
Looking ahead, the organizations that succeed will be those that treat outsourced manufacturing as a strategic asset-one that amplifies innovation, mitigates risk, and supports sustainable growth. By embracing the actionable recommendations and leveraging the insights detailed in this report, stakeholders can navigate the complexity of the current landscape and position themselves to capitalize on the next wave of medical device advancements.
This section provides a structured overview of the report, outlining key chapters and topics covered for easy reference in our Medical Device Outsourced Manufacturing market comprehensive research report.
- Preface
- Research Methodology
- Executive Summary
- Market Overview
- Market Dynamics
- Market Insights
- Cumulative Impact of United States Tariffs 2025
- Medical Device Outsourced Manufacturing Market, by Product Type
- Medical Device Outsourced Manufacturing Market, by Service Type
- Medical Device Outsourced Manufacturing Market, by Process Type
- Medical Device Outsourced Manufacturing Market, by Material Type
- Medical Device Outsourced Manufacturing Market, by End Use
- Americas Medical Device Outsourced Manufacturing Market
- Europe, Middle East & Africa Medical Device Outsourced Manufacturing Market
- Asia-Pacific Medical Device Outsourced Manufacturing Market
- Competitive Landscape
- ResearchAI
- ResearchStatistics
- ResearchContacts
- ResearchArticles
- Appendix
- List of Figures [Total: 26]
- List of Tables [Total: 737 ]
Engage with Ketan Rohom to Access the Full Market Intelligence
To access the comprehensive analysis of outsourced medical device manufacturing, including detailed segment and regional breakdowns, strategic company profiles, and forward-looking recommendations, reach out to Ketan Rohom, Associate Director of Sales & Marketing. Engaging with Ketan provides direct insights into how this intelligence can support capital allocation, partnership decisions, and operational roadmaps tailored to your organization’s unique needs. Secure your copy of the full report today to gain a competitive edge in an increasingly complex and rapidly evolving market. Let Ketan guide you through a personalized briefing and unlock the strategic clarity necessary to navigate upcoming challenges and capture emerging opportunities in medical device manufacturing.
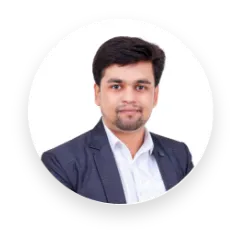
- How big is the Medical Device Outsourced Manufacturing Market?
- What is the Medical Device Outsourced Manufacturing Market growth?
- When do I get the report?
- In what format does this report get delivered to me?
- How long has 360iResearch been around?
- What if I have a question about your reports?
- Can I share this report with my team?
- Can I use your research in my presentation?