Introduction to the Metal Abrasive Market Outlook
Metal abrasive materials have long served as the backbone of precision manufacturing, surface finishing and high-performance cutting applications. As global production requirements evolve, abrasive technologies must meet increasingly stringent standards for durability, efficiency and environmental compliance. This report provides a comprehensive executive summary of the current metal abrasive market, highlighting the key drivers, segmentation dynamics, regional trends and competitive landscape that shape buyer and supplier strategies. Through rigorous analysis of abrasive compositions including aluminum oxide variants such as fine and super fine grades, silicon carbide configurations spanning coarse to micro grades and zirconia alumina blends, we illuminate how material selection impacts performance metrics across aerospace, automotive and industrial metal finishing applications.
Moreover, the report unpacks product forms ranging from bonded and coated abrasives to powder formulations, each optimized through dry, mechanical, thermal or wet processing techniques for specific use cases. Technological innovation in advanced ceramics, electroplated solutions and nanostructured abrasives underscores the market’s shift toward higher precision and longer life spans, while emerging application methods such as robotic polishing and CNC machining drive automation trends. By examining process efficiency factors such as grinding, heat treatment and surface preparation, alongside quality assurance frameworks spanning industry standards, ISO certification and control measures, this analysis delivers an authoritative foundation for strategic decision-making.
Recent market projections estimate a compound annual growth rate exceeding 5% through the end of the decade, driven by increased capital expenditure in high precision sectors. By aligning product innovation with evolving regulatory landscapes and digital transformation roadmaps, suppliers can secure a greater share of this expanding market.
Transformative Shifts Reshaping the Metal Abrasive Landscape
Over the past five years, the metal abrasive sector has undergone transformative shifts driven by digitalization, sustainability mandates and an intensifying focus on productivity. The integration of Industry 4.0 protocols has enabled real-time monitoring of abrasive tool wear and process parameters, reducing downtime and extending service intervals. Simultaneously, regulatory pressures and environmental initiatives have spurred the adoption of eco-friendly production methods, prompting manufacturers to explore low-dust abrasive powders and recyclable resin bonds that minimize waste.
The rise of additive manufacturing and hybrid machining platforms has broadened material compatibility requirements, placing a premium on abrasives that deliver consistent surface finishes on complex geometries. In parallel, advances in nanostructured abrasives incorporating nano coating and nano integration techniques have unlocked unprecedented cutting efficiencies, fostering a new class of high-impact solutions. Automation trends are accelerating through robotic application systems and CNC machining cells, which demand abrasives that maintain uniform performance across extended runs. At the same time, the emergence of smart abrasives embedded with sensors is starting to reshape predictive maintenance strategies, enabling preemptive adjustments to process parameters.
Supply chain disruptions have also underscored the need for diversified raw material sourcing and strategic inventory management, prompting manufacturers to develop regional supply hubs and pursue vertical integration of abrasive media production. These measures enhance resilience and facilitate rapid responsiveness to global demand fluctuations.
In-Depth Segmentation Analysis Reveals Market Dynamics
Segmentation analysis reveals the nuanced drivers of demand and performance within the metal abrasive market. When considering abrasive composition, aluminum oxide dominates in applications requiring moderate hardness and thermal stability, with fine grades optimized for precision polishing and super fine grades catering to ultra-smooth surface requirements. Silicon carbide emerges as the material of choice for high‑hardness applications, with coarse granules excelling in aggressive stock removal and micro grades tailored for delicate finishing tasks. Zirconia alumina, known for its enhanced toughness and extended service life, addresses high-stress machining operations where resilience under thermal loads is critical.
Exploring end use applications, aerospace fabrication commands stringent quality standards for engine casings and landing gear surface treatments, driving demand for super fine aluminum oxide and precision-coated abrasives. In automotive manufacturing, engine components benefit from robust bonded solutions that withstand high-temperature grinding, while exhaust systems leverage silicon carbide abrasives for corrosion-resistant surface blends. Metal finishing across industrial sectors relies on a balanced mix of coated and bonded abrasives to achieve specifications in decorative and protective coatings.
Product form segmentation distinguishes bonded abrasives, which can be metal bonded for heavy-duty cutting or resin bonded for versatile day-to-day operations, from coated varieties engineered for high-speed belt grinding. Powder form abrasives, available as dry powders for minimal process contamination or wet mixtures for improved dust suppression, are gaining traction in niche finishing protocols.
Manufacturing processes—dry, mechanical, thermal and wet—create specialized abrasive profiles that align with specific operational contexts, whether rapid thermal bonding for ceramic grain attachment or precision mechanical processing for embossing abrasive patterns. Process efficiency categories such as grinding speed, targeted heat treatment and surface preparation techniques directly influence cost-per-part metrics and cycle times.
Technological innovation continues to reshape the market landscape, with advanced ceramics offering elevated hardness parameters, electroplated abrasives delivering robust grain-to-backing adhesion and nanostructured abrasives, through nano coating and integration, achieving cutting edge life cycles. Application methods range from fully automated polishing cells to manual grinding stations and robotics, each demanding abrasives that balance repeatability with adaptability. Finally, quality assurance frameworks encompassing industry standard compliance, ISO certification, process optimization tools and rigorous control measures ensure consistency, safety and regulatory alignment across global operations.
This comprehensive research report categorizes the Metal Abrasive market into clearly defined segments, providing a detailed analysis of emerging trends and precise revenue forecasts to support strategic decision-making.
- Abrasive Composition
- End Use Application
- Product Form
- Manufacturing Process
- Process Efficiency
- Technological Innovation
- Application Method
- Quality Assurance
Regional Market Trends and Growth Drivers Across Key Territories
Regional analysis highlights divergent growth trajectories and strategic priorities across the Americas, Europe, Middle East & Africa and Asia-Pacific territories. In the Americas, robust automotive and aerospace manufacturing hubs in the United States and Canada are catalysts for high-volume consumption of bonded and coated abrasives, particularly as lean manufacturing initiatives prioritize process optimization and waste reduction. Shifting nearshoring trends are further stimulating investments in domestic abrasive production capabilities, reducing reliance on imports, while Latin American players gradually embrace automation and cost-effective solutions to upgrade aging infrastructures.
Across Europe, Middle East & Africa, stringent environmental regulations and energy efficiency mandates elevate demand for eco-conscious abrasive formulations, while EU member states invest heavily in next-generation manufacturing centers. Cross-border collaborations within the EU and Gulf Cooperation Council are accelerating joint abrasive research initiatives. Middle Eastern nations, buoyed by diversification strategies, expand metal fabrication capabilities, creating new avenues for abrasive consumption in oil and gas equipment maintenance. African markets, though emergent, witness initial uptake in manual grinding and polishing methods as part of broader industrialization efforts.
In the Asia-Pacific region, China and India lead in aggressive capacity expansions, driving unprecedented demand for high-performance abrasives across automotive, aerospace and heavy industries. Southeast Asian nations increase automation adoption in electronics and precision engineering sectors, fueling growth in micro grade silicon carbide and advanced ceramic abrasives. Japanese and South Korean manufacturers continue to pioneer innovations in nanostructured abrasives and electroplating techniques, maintaining their competitive edge within regional supply chains.
Collectively, these regional dynamics underscore the importance of tailored market entry strategies that account for regulatory frameworks, infrastructure maturity and technological adoption rates. Suppliers and stakeholders must calibrate product portfolios and value propositions to harness growth pockets across each geography effectively.
This comprehensive research report examines key regions that drive the evolution of the Metal Abrasive market, offering deep insights into regional trends, growth factors, and industry developments that are influencing market performance.
- Americas
- Asia-Pacific
- Europe, Middle East & Africa
Leading Players and Competitive Benchmarking in the Metal Abrasive Sector
Competitive benchmarking reveals a landscape where global conglomerates and specialized niche providers vie for share through product differentiation, strategic alliances and technological leadership. Major conglomerates such as 3M Company and Saint-Gobain Abrasives, Inc. leverage extensive R&D infrastructure to deliver advanced ceramic and coated abrasive solutions under premium branding. Regional specialists including Abrasive Solutions International LLC and Mirka Ltd. have strengthened their positions by focusing on targeted segments like automotive finishing and precision electronics.
Mid-tier players such as Belshaw Adamatic Abrasives, BristleTech Abrasives and Klingspor Abrasives concentrate on resin bonded and metal bonded product lines, balancing cost-effectiveness with performance reliability. Powder form innovators like Diacera Corporation and Diamond Innovations Inc. drive niche applications with customized granule formulations. Electroplated and nanostructured offerings from ECKART GmbH and Elite Abrasives Inc. underscore the push toward higher abrasion resistance and longer tool life.
Aggressive expansion by Covestro Abrasives Division, Excel Abrasives Inc. and Keradia Abrasives Inc. in emerging markets indicates a shift toward localized manufacturing footprints to reduce lead times. Visionary entrants such as Global Abrasive Technologies LLC and ProAbrasive Tools Inc. are challenging incumbents with digital integration features, while established heavy‑duty solution providers like Carborundum Universal and Tyrolit continue reinforcing industrial OEM partnerships. Additional notable players including Flexovit AG, Gesswein GmbH, Norton Abrasives, PFERD Abrasives GmbH, Precision Abrasives Ltd., RAS Technologies, Inc., RUD Abrasives, Sia Abrasives Corporation, Superior Surface Solutions Inc. and Uniflex Corporation complete the competitive panorama, each contributing unique value through specialized product attributes or regional expertise.
This comprehensive research report delivers an in-depth overview of the principal market players in the Metal Abrasive market, evaluating their market share, strategic initiatives, and competitive positioning to illuminate the factors shaping the competitive landscape.
- 3M Company
- Abrasive Solutions International LLC
- Belshaw Adamatic Abrasives
- BristleTech Abrasives
- Buehler Ltd.
- Carborundum Universal
- Covestro Abrasives Division
- Diacera Corporation
- Diamond Innovations Inc.
- ECKART GmbH
- Elite Abrasives Inc.
- Excel Abrasives Inc.
- Flexovit AG
- Gesswein GmbH
- Global Abrasive Technologies LLC
- Keradia Abrasives Inc.
- Klingspor Abrasives
- Metallix Abrasives Corporation
- Mirka Ltd.
- Norton Abrasives
- PFERD Abrasives GmbH
- Precision Abrasives Ltd.
- ProAbrasive Tools Inc.
- RAS Technologies, Inc.
- RUD Abrasives
- Saint-Gobain Abrasives, Inc.
- Sia Abrasives Corporation
- Superior Surface Solutions Inc.
- Tyrolit
- Uniflex Corporation
Strategic Recommendations for Industry Stakeholders to Optimize Growth
To capitalize on emerging opportunities and address evolving customer requirements, industry leaders should pursue a multi-pronged strategy. First, investing in nanostructured abrasive R&D and nano integration processes will unlock premium differentiation through enhanced cutting efficiency and extended service life. Next, expanding digital manufacturing capabilities by integrating sensor-enabled smart abrasives and predictive maintenance software will foster tighter operational control and customer loyalty. Diversifying product portfolios to include eco-friendly bonded and coated formulations aligned with global sustainability standards will position suppliers for regulatory compliance and brand reputation gains.
Market participants should also strengthen partnerships with end users in aerospace fabrication and advanced automotive manufacturing by offering co‑development programs that tailor abrasive solutions to specific engine casings, landing gear components, exhaust systems and precision assemblies. Geographic expansion into high‑growth Asia-Pacific and Middle East & Africa markets requires localized production and distribution assets to reduce lead times and customize value propositions. Additionally, implementing advanced quality assurance frameworks—combining ISO certification with real‑time process optimization tools—will ensure consistent output and reduce warranty costs. Finally, forging strategic alliances with additive manufacturing and automation technology vendors will create integrated value chains that deliver end‑to‑end process efficiency, solidifying market leadership in an increasingly competitive environment.
Explore AI-driven insights for the Metal Abrasive market with ResearchAI on our online platform, providing deeper, data-backed market analysis.
Ask ResearchAI anything
World's First Innovative Al for Market Research
Conclusion: Navigating the Future of the Metal Abrasive Market
In conclusion, the metal abrasive market stands at a pivotal juncture defined by technological innovation, sustainability imperatives and shifting regional demands. Segmentation insights across abrasive composition, end‑use applications and product forms reveal the granular drivers of market growth, while process efficiency and quality assurance dimensions underscore the importance of operational excellence. Regional trends highlight diverse opportunities in the Americas, Europe, Middle East & Africa and Asia‑Pacific, each necessitating tailored market entry and expansion approaches. Competitive analysis of established conglomerates, focused specialists and disruptive entrants illustrates the strategic pathways to differentiation.
Looking ahead, emerging digital twins for process simulation and the convergence of abrasive technology with additive manufacturing platforms will further redefine competitive parameters. Organizations that proactively invest in these forward‑looking capabilities will be best positioned to lead the market into its next era of performance and sustainability.
This section provides a structured overview of the report, outlining key chapters and topics covered for easy reference in our Metal Abrasive market comprehensive research report.
- Preface
- Research Methodology
- Executive Summary
- Market Overview
- Market Insights
- Cumulative Impact of United States Tariffs 2025
- Metal Abrasive Market, by Abrasive Composition
- Metal Abrasive Market, by End Use Application
- Metal Abrasive Market, by Product Form
- Metal Abrasive Market, by Manufacturing Process
- Metal Abrasive Market, by Process Efficiency
- Metal Abrasive Market, by Technological Innovation
- Metal Abrasive Market, by Application Method
- Metal Abrasive Market, by Quality Assurance
- Americas Metal Abrasive Market
- Asia-Pacific Metal Abrasive Market
- Europe, Middle East & Africa Metal Abrasive Market
- Competitive Landscape
- ResearchAI
- ResearchStatistics
- ResearchContacts
- ResearchArticles
- Appendix
- List of Figures [Total: 32]
- List of Tables [Total: 683 ]
Take the Next Step: Secure Your Comprehensive Metal Abrasive Market Intelligence
Elevate your strategic planning by securing comprehensive insights from our in‑depth metal abrasive market research. Connect directly with Ketan Rohom, Associate Director, Sales & Marketing, to access a detailed report that covers market sizing, segmentation analysis, regional forecasts and competitive benchmarking. Whether you seek to refine product roadmaps, identify growth pockets or benchmark against leading players, this tailored intelligence will empower your organization to make informed decisions with confidence. Reach out today to learn more about customization options, pricing and delivery timelines, and position your business at the forefront of the rapidly evolving metal abrasive industry.
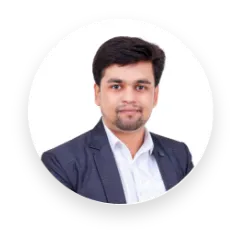
- When do I get the report?
- In what format does this report get delivered to me?
- How long has 360iResearch been around?
- What if I have a question about your reports?
- Can I share this report with my team?
- Can I use your research in my presentation?