The Metal Casting Market size was estimated at USD 136.70 billion in 2024 and expected to reach USD 144.14 billion in 2025, at a CAGR 5.29% to reach USD 186.33 billion by 2030.

Navigating the Metal Casting Market Landscape
Metal casting stands as a foundational technique in manufacturing, converting raw metals into complex components that drive industries from automotive to aerospace. This executive summary provides a holistic overview of the latest dynamics shaping the global metal casting market. It synthesizes the transformative trends, regulatory influences, and competitive strategies that define the sector’s current state and future trajectory.
In recent years, technological advancements such as automation, additive manufacturing integrations, and digital quality controls have elevated production efficiencies while meeting stringent environmental standards. Simultaneously, evolving trade policies and tariffs are compelling stakeholders to reassess supply chains and sourcing strategies. This analysis explores the cumulative impact of recent and projected United States tariffs in 2025, highlighting how cost structures and market positioning adapt under shifting regulatory landscapes.
The segmentation framework applied herein dissects the market across casting processes-ranging from investment casting to sand casting-as well as material composition, encompassing aluminum, iron, steel, and beyond. Further granularity is achieved by examining end-use industries and distribution channels, providing insight into where demand concentrates and how value migrates. Regionally, the Americas, Europe, the Middle East & Africa, and Asia-Pacific each exhibit distinct growth drivers and competitive dynamics.
Finally, this summary outlines actionable recommendations for industry leaders seeking to secure competitive advantage through strategic investments and operational excellence. The robust research methodology that underpins these findings combines exhaustive secondary analysis with expert interviews, ensuring the insights presented here are both credible and practical for decision-makers.
Transformative Trends Reshaping Metal Casting Industry
Rapid technological innovations are redefining the metal casting industry, ushering in a new era of precision, productivity, and sustainability. Additive manufacturing techniques now complement traditional casting processes, enabling the production of complex geometries with minimal material waste. Concurrently, the integration of automation and robotics on foundry floors accelerates batch turnover while reducing human error, laying the groundwork for truly smart manufacturing facilities.
Digital transformation extends beyond the production line as advanced sensors and IoT platforms facilitate real-time monitoring of molten metal properties and mold conditions. These data-driven insights empower operators to implement corrective actions proactively, minimizing scrap rates and optimizing energy consumption. Meanwhile, emerging software solutions for process simulation and predictive maintenance are further elevating operational reliability and shortening time-to-market.
Materials science breakthroughs are unlocking the potential of high-performance alloys tailored to meet the demands of aerospace, defense, and energy sectors. Novel formulations with enhanced heat resistance and corrosion protection are pushing the boundaries of component longevity. Coupled with the industry’s growing commitment to circular economy principles, foundries are increasingly investing in metal recycling and lower-carbon energy sources to align production with global decarbonization goals.
These transformative shifts not only improve cost efficiencies but also address regulatory pressures and customer expectations for greener, more resilient supply chains. As the pace of innovation accelerates, companies that embrace these trends will be best positioned to capture emerging opportunities and safeguard their competitive edge.
Assessing the 2025 US Tariffs Effect on Metal Casting Supply Chain
Trade policy developments have emerged as a critical variable influencing metal casting economics, with a series of cumulative tariff adjustments set to take effect in the United States in 2025. These measures, targeting both raw materials and imported cast components, introduce additional cost burdens that reverberate across value chains. Importers face elevated duties on steel and aluminum inputs, prompting a reevaluation of sourcing strategies and supplier agreements.
Domestic foundries anticipate short-term margin compression as they navigate higher feedstock prices and potential supply shortages. In response, many are accelerating investments in local procurement capabilities and diversifying their supplier base to mitigate exposure to tariff escalations. This strategic pivot also underscores the importance of lean manufacturing practices and process efficiencies in offsetting increased overheads without sacrificing throughput.
Exporters, particularly those serving sectors such as automotive and construction equipment, are recalibrating pricing models to remain competitive abroad. Some manufacturers are exploring opportunities to establish production footprints within free-trade zones or partner with overseas facilities to bypass tariff barriers. These maneuvers, while operationally complex, reflect the imperative to protect market share in key geographies.
As stakeholders adapt to the evolving policy landscape, the interplay between regulatory compliance, cost management, and supply chain resilience will define the next phase of growth. Companies that proactively assess tariff impacts and implement agile sourcing frameworks will emerge more robust and better equipped to navigate future trade uncertainties.
Deep Dive into Metal Casting Market Segmentation Insights
Understanding the market by casting process offers valuable clarity on where technological advancements and demand are most pronounced. Centrifugal casting, with its horizontal and vertical variants, continues to gain traction for high-strength cylindrical parts in the energy and automotive sectors. Billet, bloom, and slab casting under the continuous casting umbrella remain indispensable for bulk steel production, responding to infrastructure and industrial machinery requirements. Die casting’s hot chamber and cold chamber methods deliver precision components for electronics and consumer goods, while investment casting enables the fabrication of intricate shapes with tight tolerances for aerospace applications. Permanent mold casting has diversified through gravity, low-pressure, and vacuum die techniques, optimizing part quality and throughput. Sand casting methods, including green sand, no-bake, and resin sand processes, retain their cost-effectiveness for large, complex parts where surface finish can be refined post-casting.
Analyzing the market through material composition reveals nuanced performance characteristics and value propositions. Aluminum alloys dominate lightweighting efforts in automotive and electronics, with both die cast and sand cast variants offering competitive strength-to-weight ratios. Copper-derived alloys such as brass and bronze remain essential for electrical connectors and marine hardware due to their conductivity and corrosion resistance. Iron castings, spanning ductile, grey, malleable, and white iron, address structural and machinery requirements with robust mechanical properties. Emerging interest in magnesium for lightweight applications-as both die cast and sand cast magnesium-signals potential growth niches. Steel castings, differentiated into carbon and stainless grades, support high-temperature and corrosive environments, particularly within energy and industrial sectors. Zinc-based alloys expand options for intricate, high-volume consumer parts through die and sand casting.
Segmenting by end-use industry highlights evolving demand drivers and customization trends. Aerospace and defense components such as landing gear and engine parts demand stringent quality controls. Within automotive, body, engine block, transmission, and wheel castings require adaptation to electrified powertrains and autonomous vehicle platforms. Construction sector needs for architectural components, HVAC fittings, and structural elements are influenced by sustainability regulations and modular construction methods. Electronics housings, connectors, and electrical parts increasingly leverage miniaturization, while energy applications in oil and gas, power generation, and renewables prioritize corrosion resistance and high-temperature performance. Healthcare devices-ranging from diagnostic equipment to implants-call for biocompatible alloys and traceability. Industrial and agricultural machinery castings maintain steady demand driven by global mechanization trends.
The sales channel dimension underscores the balance between original equipment manufacturers and aftermarket channels. OEM relationships drive high-volume, long-term contracts that support capacity planning and innovation cycles. Aftermarket demand for replacement and spare parts ensures ongoing utilization of installed equipment fleets, presenting stable revenue streams. The interplay between these channels shapes inventory strategies, lead times, and customer service models across the industry.
This comprehensive research report categorizes the Metal Casting market into clearly defined segments, providing a detailed analysis of emerging trends and precise revenue forecasts to support strategic decision-making.
- Casting Process
- Material
- End-Use Industry
- Sales Channel
Regional Dynamics Driving Metal Casting Growth Worldwide
Across the Americas, the metal casting market benefits from a strong manufacturing base anchored by automotive, aerospace, and industrial machinery sectors. Investments in reshoring and nearshoring initiatives have bolstered domestic foundry capacities, creating opportunities for local suppliers to partner with OEMs on strategic projects. Environmental regulations are driving the adoption of cleaner production technologies and recycled content, which in turn influence casting process selection and material sourcing strategies.
In Europe, the Middle East & Africa, market growth is propelled by varying regional priorities. Western Europe’s stringent emissions targets and circular economy policies incentivize advanced casting solutions and lightweight alloys. In contrast, growth markets in Eastern Europe and the Middle East are investing in heavy industries, infrastructure projects, and energy developments that rely on robust iron and steel castings. Africa’s emerging manufacturing hubs are gradually adopting modern casting technologies, presenting an untapped frontier for equipment suppliers and foundry service providers.
The Asia-Pacific region remains the largest and fastest-growing market, driven by robust demand from automotive, electronics, and construction industries. China continues to scale up production capabilities, supported by government initiatives that promote advanced manufacturing and sustainability compliance. India’s expanding infrastructure programs and rising domestic demand are catalyzing growth in both ferrous and non-ferrous casting segments. Meanwhile, Southeast Asian countries are emerging as key hubs for contract foundry services, leveraging competitive labor costs and improving technological capabilities.
These regional dynamics underscore the importance of tailored market strategies that account for local regulatory environments, supply chain structures, and end-user requirements. Companies that align their investments with regional growth drivers will be well positioned to capture new opportunities and mitigate localized risks.
This comprehensive research report examines key regions that drive the evolution of the Metal Casting market, offering deep insights into regional trends, growth factors, and industry developments that are influencing market performance.
- Americas
- Europe, Middle East & Africa
- Asia-Pacific
Leading Players Shaping the Metal Casting Landscape
Global foundries and casting specialists are intensifying efforts to secure market leadership through capacity expansions, strategic partnerships, and technology investments. Industry frontrunners have launched ambitious digitalization initiatives, integrating IoT-enabled equipment and advanced analytics to drive real-time process optimization and predictive maintenance. These efforts enhance product quality and reduce downtime, delivering measurable cost savings across the production cycle.
In response to evolving customer demands, key companies are broadening their service portfolios to include design for manufacturability consultations and value-added post-casting processes such as heat treatment and precision machining. Such end-to-end solutions strengthen client relationships and promote long-term volume contracts. Concurrently, several market leaders are actively pursuing mergers and acquisitions to consolidate capabilities, achieve scale economies, and gain entry into new geographic markets.
Sustainability is increasingly a differentiator among prominent players, with leading foundries setting ambitious targets for carbon emissions reduction and waste minimization. Investments in electric melting furnaces, renewable energy sourcing, and closed-loop recycling systems are becoming standard practice. These environmental initiatives not only mitigate regulatory risk but also appeal to end customers who prioritize green supply chains.
As competition intensifies, agility and innovation will determine future market shares. Companies that harness emerging technologies, align product offerings with sector-specific requirements, and uphold stringent sustainability standards will continue to define the competitive contours of the global metal casting industry.
This comprehensive research report delivers an in-depth overview of the principal market players in the Metal Casting market, evaluating their market share, strategic initiatives, and competitive positioning to illuminate the factors shaping the competitive landscape.
- Nemak S.A.B. de C.V.
- Arconic Corporation
- Thyssenkrupp AG
- American Axle & Manufacturing, Inc.
- Ryobi Limited
- Aisin Seiki Co., Ltd.
- Riken Corporation
- Georg Fischer AG
- Bharat Forge Limited
- Tower International, Inc.
Strategic Roadmap for Advancing in Metal Casting Market
To thrive amid technological disruption and shifting trade policies, industry leaders must embrace a multifaceted strategic approach. Investing in advanced casting technologies-such as additive manufacturing integration, automation, and digital quality assurance-will enhance production agility and support rapid scale-up in response to market fluctuations. Prioritizing lean manufacturing principles and continuous process improvement fosters cost discipline, enabling foundries to maintain healthy margins in the face of external cost pressures.
Material diversification plays a critical role in capturing emerging forward-looking segments, particularly lightweight alloys like magnesium and specialized stainless steels for energy and defense applications. Cultivating strategic partnerships with material suppliers can secure preferential access to high-performance alloys and enable joint development projects that yield proprietary advantages. Strengthening domestic supply chains through local procurement initiatives and vendor accreditation programs reduces tariff exposure and enhances resilience against geopolitical disruptions.
A targeted sustainability agenda is essential to meet rising regulatory and customer expectations. Implementing energy-efficient melting technologies, recycling scrap metal, and adopting renewable energy sources will help foundries achieve tangible environmental targets. Transparent reporting on carbon footprint reductions will bolster credibility with stakeholders and support access to green financing options.
Finally, fostering a skilled workforce through training programs and cross-functional collaboration ensures that both technical expertise and digital competencies remain ahead of industry evolution. By aligning these strategic pillars with specific regional and end-user requirements, foundries can capture incremental market share, achieve operational excellence, and secure long-term growth.
Rigorous Methodology Underpinning the Research Findings
This analysis is grounded in a comprehensive research methodology that harmonizes qualitative insights with quantitative data. Secondary research involved an exhaustive review of industry publications, government reports, trade association studies, and company disclosures to establish market context, historic trends, and regulatory frameworks. Specialized databases were leveraged to extract granular data on production yields, material consumption, and trade flows.
Primary research efforts included structured interviews with C-level executives, technical directors, and supply chain managers across leading foundries and OEMs. These dialogues provided firsthand perspectives on operational challenges, investment priorities, and future market opportunities. Expert feedback was iteratively incorporated to validate critical assumptions and ensure the robustness of segmentation criteria.
Quantitative analyses employed data triangulation techniques to reconcile disparate data sources, while sensitivity analyses were conducted to test the stability of key findings under alternative scenarios. Geographic and end-use industry breakdowns were modeled to capture demand variances, and tariff impact assessments were formulated using scenario-based cost modeling. The integration of these methodological layers yields a balanced, data-driven perspective that supports confident decision-making.
Explore AI-driven insights for the Metal Casting market with ResearchAI on our online platform, providing deeper, data-backed market analysis.
Ask ResearchAI anything
World's First Innovative Al for Market Research
Concluding Perspectives on Metal Casting Market Trajectory
In summary, the metal casting industry stands at a convergence of technological innovation, regulatory evolution, and shifting global trade dynamics. Companies that capitalize on advanced manufacturing processes, expand material portfolios, and reinforce supply chain resilience will be best positioned to navigate competitive pressures and achieve sustainable growth. The cumulative impact of United States tariffs in 2025 underscores the need for agile sourcing strategies and proactive cost management, particularly in regions with high import dependencies.
Segmentation insights reveal that demand patterns vary markedly by casting process, material, end-use industry, and sales channel, emphasizing the importance of tailored product offerings and service models. Regional analysis highlights distinct growth drivers across the Americas, Europe, Middle East & Africa, and Asia-Pacific, underscoring the value of region-specific market entry or expansion plans.
Looking ahead, leading players must balance operational efficiency with environmental stewardship and digital transformation to unlock new avenues for differentiation. By drawing on the strategic recommendations outlined here, decision-makers can accelerate innovation pipelines, strengthen market positioning, and realize resilient growth in an increasingly dynamic metal casting landscape.
This section provides a structured overview of the report, outlining key chapters and topics covered for easy reference in our Metal Casting market comprehensive research report.
- Preface
- Research Methodology
- Executive Summary
- Market Overview
- Market Dynamics
- Market Insights
- Cumulative Impact of United States Tariffs 2025
- Metal Casting Market, by Casting Process
- Metal Casting Market, by Material
- Metal Casting Market, by End-Use Industry
- Metal Casting Market, by Sales Channel
- Americas Metal Casting Market
- Europe, Middle East & Africa Metal Casting Market
- Asia-Pacific Metal Casting Market
- Competitive Landscape
- ResearchAI
- ResearchStatistics
- ResearchContacts
- ResearchArticles
- Appendix
- List of Figures [Total: 24]
- List of Tables [Total: 1049 ]
Secure Your Comprehensive Metal Casting Market Report Today
Equip your organization with the insights needed to outpace competitors and capitalize on emerging opportunities in the metal casting sector. To obtain the full market research report and access in-depth analyses of market drivers, segmentation breakdowns, regional dynamics, and actionable strategic recommendations, engage with Ketan Rohom, Associate Director of Sales & Marketing at 360iResearch. His expertise will ensure you receive a tailored briefing that aligns with your strategic objectives and investment priorities.
Reach out today to explore customized data packages, competitive benchmarking services, and dedicated support for implementing the report’s findings within your organization. Make data-driven decisions with confidence and steer your metal casting operations toward long-term success.
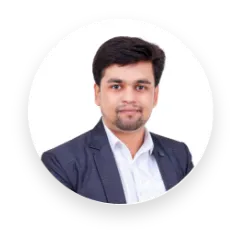
- How big is the Metal Casting Market?
- What is the Metal Casting Market growth?
- When do I get the report?
- In what format does this report get delivered to me?
- How long has 360iResearch been around?
- What if I have a question about your reports?
- Can I share this report with my team?
- Can I use your research in my presentation?