Introduction to the Metal Cutting Bandsaw Blade Market
The global metal cutting bandsaw blade market stands at the heart of modern manufacturing, powering precision cuts across countless industries. As demand for complex components grows, manufacturers rely on advanced blade technologies to maintain accuracy, speed, and cost-efficiency. Recent strides in materials science have introduced hybrid alloys and nanocoatings that extend tool life and reduce downtime. Meanwhile, digital integration and automated cutting systems are reshaping production lines, enabling real-time monitoring and predictive maintenance.
This executive summary surveys the primary forces driving the market, including technological breakthroughs, regulatory shifts, and evolving supply chain dynamics. It highlights how stakeholder decisions-from tool selection to end-use applications-influence operational performance. By presenting critical segmentation insights, tariff impacts, and regional variations, this overview equips decision-makers with actionable intelligence to navigate shifting conditions. In addition, rising environmental and safety standards compel blade manufacturers to optimize cutting efficiency while minimizing material waste and energy consumption. Ultimately, this introduction defines the scope and methodology of our analysis, setting the stage for a deeper exploration of transformative trends and strategic imperatives.
Transformative Shifts in the Landscape
Manufacturers are embracing cutting-edge alloys and composite materials that enhance blade toughness and heat resistance. Bi-metal designs fuse flexibility with wear resistance, while carbide tipped and diamond blades carve new frontiers in high-precision cutting. The emergence of hybrid material blends within future sub-segments has delivered unmatched performance in aggressive and continuous-cut operations. At the same time, semi-automatic and fully automatic systems are reshaping labor dynamics, offering consistent cut quality and faster cycle times compared to manual processes.
Supply chain resilience has become a strategic imperative, prompting firms to diversify sources for blade steel, carbon composites, and advanced coatings to guard against tariff shifts and raw-material bottlenecks. Digital twins and real-time analytics enable predictive maintenance that slashes unplanned downtime and extends tool life. Strategic tooth pitch choices-coarse for rapid material removal, fine for precision finishes-further tailor solutions across sectors, from aerospace to metal fabrication.
Environmental stewardship is also driving innovation. Energy-efficient sawing equipment, recyclable blade components, and friction-reducing ceramic and lacquer coatings all converge to lower scrap rates and coolant consumption. Together, these technological, operational, and ecological shifts are redefining competitive advantage in the metal cutting bandsaw blade market.
Cumulative Impact of United States Tariffs 2025
New tariff measures introduced by the United States in 2025 have reshaped procurement strategies across the metal cutting bandsaw blade sector. Import duties on key raw materials such as specialized steel grades and high-performance carbide have elevated input costs, compelling blade manufacturers to re-evaluate sourcing and production footprints. As a result, some producers have accelerated localization efforts, investing in domestic alloy production and forging partnerships with U.S.-based mill operators to reduce exposure to cross-border levies.
End-users now face higher blade prices, which can translate into increased operational budgets for aerospace OEMs, automotive plants, and shipbuilders. To mitigate these cost pressures, companies are optimizing cutting parameters-like medium tooth pitch for general applications and fine pitch for precision tasks-to extend blade life and maximize throughput. Others are negotiating longer-term contracts with importers to secure duty-stabilized supplies or leveraging free trade agreement provisions for certain materials.
Regulatory compliance has taken on heightened importance, triggering more rigorous documentation and customs audits. Manufacturers with vertically integrated capabilities have gained an edge by capturing value upstream, buffering end-users against volatile tariff swings. The cumulative effect of these measures underscores the need for agile supply chain management and strategic planning to maintain margin stability amidst evolving trade policies.
Key Segmentation Insights
In the material type category, bi-metal blades continue to dominate thanks to their balance of flexibility and wear resistance, while carbide tipped options lead in high-volume cutting of ferrous and non-ferrous alloys; carbon blades remain cost-effective for general applications and diamond variants excel in ultra-hard material cuts. Notably, the future sub-segment centered on hybrid materials is emerging as a premium solution for demanding continuous operations.
Within tool type distinctions, portable saws offer versatility and on-site mobility, whereas stationary systems deliver higher precision and volume throughput. Tooth pitch choices reveal coarse configurations as the standard for rapid stock removal, medium pitch as a versatile compromise, and fine pitch as the go-to for smooth surface finishes. Blade width trends show narrow profiles optimizing tight-radius cuts, while wide blades ensure stability in heavy-gauge applications. In blade thickness, thin options cater to light-duty work, medium thickness provides general-purpose reliability, and thick blades underpin heavy industrial sawing.
Applications in the aerospace, automotive, construction, industrial, and metal fabrication sectors each demand tailored blade characteristics, reflecting diverse end-use industries, from aerospace and defense to agriculture equipment, machine manufacturing, mining, and shipbuilding. Blade length segmentation-long, medium, and short-aligns with cut volume and material size requirements. Both horizontal and vertical saw types serve unique production layouts, while cutting speed variations-fast, medium, and slow-match material hardness and finish standards. Finally, coating type analysis highlights advanced ceramic and zirconium coatings for heat and abrasion resistance, Teflon for reduced friction, titanium nitride for extended wear life, and a future nanocoating sub-segment poised to set new performance benchmarks.
This comprehensive research report categorizes the Metal Cutting Bandsaw Blade market into clearly defined segments, providing a detailed analysis of emerging trends and precise revenue forecasts to support strategic decision-making.
- Material Type
- Tool Type
- Tooth Pitch
- Blade Width
- Blade Thickness
- Application
- End-Use Industry
- Blade Length
- Saw Type
- Cutting Speed
- Technology
- Coating Type
Key Regional Insights
In the Americas region, robust automotive and aerospace manufacturing centers in the United States and Canada drive strong demand for high-performance blades. Tariff measures have prompted companies to locate more fabrication and coating facilities domestically, while Mexico continues to serve as a cost-effective machining hub, leveraging its proximity to U.S. assembly lines. Localized sourcing strategies have enhanced supply chain resilience, reducing lead times and exposure to cross-border duties.
Europe, Middle East & Africa presents a mosaic of mature and emerging markets. Western Europe’s stringent quality and environmental regulations favor premium carbide tipped and ceramic-coated blades, particularly in aviation and defense applications. Eastern European nations are rapidly expanding light industrial capabilities, fueling demand for versatile medium-pitch and bi-metal blades. In the Middle East and Africa, infrastructure projects in construction and mining sectors are driving large-volume orders of durable, wide-width blades suited to heavy-gauge materials.
Asia-Pacific remains the largest growth frontier. Established manufacturing powerhouses like China, Japan, and South Korea lead in both production and consumption of bandsaw blades. Local blade producers are investing heavily in automatic systems and nanocoating technologies to meet soaring automotive and electronics sector requirements. Emerging economies in Southeast Asia are following suit, establishing regional distribution networks to serve rising demand for portable and stationary sawing solutions.
This comprehensive research report examines key regions that drive the evolution of the Metal Cutting Bandsaw Blade market, offering deep insights into regional trends, growth factors, and industry developments that are influencing market performance.
- Americas
- Asia-Pacific
- Europe, Middle East & Africa
Key Companies Insights
Leading manufacturers have solidified their market positions through targeted innovation and strategic alliances. Amada Co., Ltd. continues to invest in integrating automatic sawing solutions with advanced materials, while Bahco Tools leverages its global distribution network to promote premium bi-metal and carbide tipped blades. Dakin-Flathers Ltd has strengthened its presence in the aerospace and defense end-use industry by developing custom-design blades for titanium and nickel alloys. Delta Power Equipment Corporation and DoALL Sawing Products emphasize turnkey sawing systems, integrating medium and fine-tooth configurations for metal fabrication lines.
Hanska Abrasive Company and HE&M Saw focus on abrasion-resistant coatings, particularly zirconium and ceramic, to extend tool life in high-speed operations. Kastel Bandsaw Blades and Lenox Tools differentiate through specialized portable saw attachments and blade thickness optimization for on-site cutting. M. K. Morse Company and Rontgen Saw LTD have made inroads in the mining and construction segments with wide-width, high-torque blades. Select Tool, Inc. and Simonds International compete fiercely in the stationary saw market, offering hybrid material options within future sub-segments.
Meanwhile, Starrett L.S. Company, Inc. emphasizes precision cutting solutions, catering to fine-pitch applications in the electronics and medical device sectors, and The American Saw and Manufacturing Company bolsters its North American footprint by supplying horizontal and vertical saw configurations with comprehensive after-sales support. Several leaders are also expanding digital services; for example, Lenox Tools and DoALL Sawing Products now offer remote blade health monitoring, while Select Tool, Inc. and Simonds International introduce predictive maintenance packages. At the same time, Kastel and HE&M Saw pursue joint ventures with nanocoating specialists to accelerate next-generation blade performance.
This comprehensive research report delivers an in-depth overview of the principal market players in the Metal Cutting Bandsaw Blade market, evaluating their market share, strategic initiatives, and competitive positioning to illuminate the factors shaping the competitive landscape.
- Amada Co., Ltd.
- Bahco Tools
- Dakin-Flathers Ltd
- Delta Power Equipment Corporation
- DoALL Sawing Products
- Hanska Abrasive Company
- HE&M Saw
- Kastel Bandsaw Blades
- Lenox Tools
- M. K. Morse Company
- Rontgen Saw LTD
- Select Tool, Inc.
- Simonds International
- Starrett L.S. Company, Inc.
- The American Saw and Manufacturing Company
Actionable Recommendations for Industry Leaders
To stay ahead in this competitive market, manufacturers should prioritize investment in hybrid materials and nanocoating research, ensuring blades deliver exceptional wear resistance and heat management. Establishing partnerships with advanced steel mills and coating specialists will diversify raw-material sourcing and mitigate tariff-induced cost fluctuations. Integrating digital twin platforms and real-time performance analytics into production workflows can proactively identify wear patterns, enabling predictive maintenance that reduces unplanned downtime by capturing early-stage blade degradation signals.
Industry leaders must also adopt a flexible segmentation strategy, tailoring product portfolios to capture opportunities across tool types and tooth pitch configurations; portable blade systems will serve on-site maintenance teams, while stationary solutions can address high-volume fabrication demands. Expanding regional footprints through localized manufacturing hubs-particularly in key Americas and Asia-Pacific markets-will shorten lead times and enhance customer responsiveness. In addition, companies should develop end-to-end service models that include blade recycling programs and energy-efficient sawing processes, aligning operations with sustainability mandates and environmental regulations.
Finally, fostering cross-functional collaboration between R&D, sales, and supply chain teams will accelerate time-to-market for innovative offerings. By implementing these recommendations, industry leaders can maintain margin stability, drive customer loyalty, and secure a decisive advantage in the evolving metal cutting bandsaw blade landscape.
Explore AI-driven insights for the Metal Cutting Bandsaw Blade market with ResearchAI on our online platform, providing deeper, data-backed market analysis.
Ask ResearchAI anything
World's First Innovative Al for Market Research
Conclusion
The metal cutting bandsaw blade market is undergoing rapid transformation driven by advanced materials, automation, and evolving trade policies. Hybrid alloys and nanocoatings are setting new performance standards, while digital integration and predictive analytics optimize production efficiency and tool longevity. Tariff changes in the United States underscore the importance of supply chain agility and localized sourcing, compelling manufacturers to reassess procurement strategies and operational footprints.
Comprehensive segmentation analysis reveals that material type, tooth pitch, blade dimensions, and coating choices must align precisely with end-use requirements across aerospace, automotive, construction, and industrial applications. Regional dynamics in the Americas, Europe, Middle East & Africa, and Asia-Pacific further influence market priorities, from premium precision requirements to large-scale infrastructure projects. Moreover, in an environment where environmental stewardship and regulatory compliance hold equal weight with performance metrics, aligning innovation with sustainability objectives will become a critical differentiator. Additionally, industry leaders are differentiating through automatic systems, portable saw attachments, and integrated service offerings such as remote blade monitoring.
By synthesizing these insights, decision-makers can navigate uncertainties, capitalize on emerging opportunities, and sustain competitive momentum. A proactive approach to R&D, strategic partnerships, and digital transformation will define market leadership in the years ahead.
This section provides a structured overview of the report, outlining key chapters and topics covered for easy reference in our Metal Cutting Bandsaw Blade market comprehensive research report.
- Preface
- Research Methodology
- Executive Summary
- Market Overview
- Market Dynamics
- Market Insights
- Cumulative Impact of United States Tariffs 2025
- Metal Cutting Bandsaw Blade Market, by Material Type
- Metal Cutting Bandsaw Blade Market, by Tool Type
- Metal Cutting Bandsaw Blade Market, by Tooth Pitch
- Metal Cutting Bandsaw Blade Market, by Blade Width
- Metal Cutting Bandsaw Blade Market, by Blade Thickness
- Metal Cutting Bandsaw Blade Market, by Application
- Metal Cutting Bandsaw Blade Market, by End-Use Industry
- Metal Cutting Bandsaw Blade Market, by Blade Length
- Metal Cutting Bandsaw Blade Market, by Saw Type
- Metal Cutting Bandsaw Blade Market, by Cutting Speed
- Metal Cutting Bandsaw Blade Market, by Technology
- Metal Cutting Bandsaw Blade Market, by Coating Type
- Americas Metal Cutting Bandsaw Blade Market
- Asia-Pacific Metal Cutting Bandsaw Blade Market
- Europe, Middle East & Africa Metal Cutting Bandsaw Blade Market
- Competitive Landscape
- ResearchAI
- ResearchStatistics
- ResearchContacts
- ResearchArticles
- Appendix
- List of Figures [Total: 40]
- List of Tables [Total: 645 ]
Call-to-Action
Unlock the full depth of analysis and strategic data by securing your copy of the comprehensive metal cutting bandsaw blade market research report. Reach out directly to Ketan Rohom, Associate Director, Sales & Marketing, to discuss your specific industry needs and customization options. Our team will guide you through detailed segmentation findings, tariff impact assessments, and regional intelligence to support your growth initiatives. Schedule a personalized consultation to explore tailored insights and actionable strategies that will drive your competitive edge. Contact Ketan today to take the next step toward market leadership.
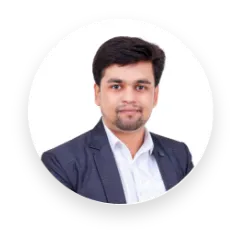
- When do I get the report?
- In what format does this report get delivered to me?
- How long has 360iResearch been around?
- What if I have a question about your reports?
- Can I share this report with my team?
- Can I use your research in my presentation?