Overview of the Metal Honeycomb Support Market: Context and Scope
Metal honeycomb support structures are engineered to deliver an exceptional balance of strength, rigidity, and lightweight performance across demanding industrial environments. Originating from aerospace applications where weight reduction and structural integrity are paramount, honeycomb supports now underpin a wide array of high-performance systems ranging from automotive crash management modules to furnace support assemblies in chemical and petrochemical plants. Their unique geometry-characterized by cells arranged in hexagonal, circular, rectangular, or bespoke configurations-enables unparalleled thermal insulation and energy absorption while minimizing material usage.
In recent years, technological innovations in manufacturing processes such as extrusion and additive techniques have expanded design possibilities, driving deeper penetration into emerging markets. Concurrently, stringent regulatory frameworks addressing emissions, durability, and energy efficiency are elevating demand for advanced metal honeycomb solutions capable of withstanding elevated temperatures and corrosive environments. This executive summary distills the core dynamics shaping this evolving landscape, offering decision-makers clear insights into the drivers, challenges, and strategic inflection points defining the metal honeycomb support sector today.
Transformative Shifts Reshaping the Metal Honeycomb Support Market
The metal honeycomb support ecosystem is undergoing transformative shifts propelled by material science breakthroughs, manufacturing innovations, and evolving end-user requirements. Additive manufacturing, notably selective laser melting and stereolithography, has unlocked intricate cell geometries and rapid prototyping capabilities that were previously unattainable through conventional extrusion methods. This convergence of process agility and design freedom is enabling entirely new support architectures tailored to optimize flow dynamics, thermal gradients, and mechanical resilience.
Moreover, heightened emphasis on decarbonization and circular economy principles is accelerating the adoption of recyclable alloys such as aluminum and stainless steel, while research into high-performance titanium and nickel-based honeycombs is gaining traction in extreme-temperature applications. In parallel, digital simulation and predictive analytics are becoming foundational tools for validating mechanical behavior under complex loading and thermal cycles, thereby reducing development timelines and enhancing product reliability.
These concurrent shifts are not occurring in isolation. As sustainability mandates tighten globally, supply chain resiliency is increasingly prioritized, leading organizations to diversify material sourcing and to forge strategic partnerships with regional fabricators. Against this backdrop, stakeholders who embrace a holistic view of material-process-application synergy will be best positioned to harness the next wave of growth in the metal honeycomb support market.
Assessing the Cumulative Impact of US Tariffs Effective in 2025
The imposition of new tariff schedules in the United States set to take effect in 2025 is reshaping competitive dynamics across the metal honeycomb support value chain. Increased duties on select imported alloys have driven input cost inflation, compelling integrators to reassess sourcing strategies and pass through higher prices to end users in aerospace, automotive, and industrial segments. In response, several manufacturers have accelerated investments in domestic production facilities to mitigate exposure to volatile trade policies and to qualify under ‘‘Made in USA’’ procurement mandates used by critical infrastructure projects.
At the same time, the tariff-driven cost pressures have catalyzed a shift toward alternative alloys with favorable supply availability and lower duty classifications. Aluminum honeycomb supports, for example, have seen renewed interest in applications traditionally dominated by stainless steel or nickel, given aluminum’s lighter weight profile and more stable import duties. Conversely, industries reliant on ultra-high-temperature performance-such as petrochemical refining and thermal power plants-continue to uphold demand for nickel-based honeycombs despite elevated costs, valuing their superior corrosion resistance and longevity.
In navigating this tariff environment, leading organizations are leveraging long-term supplier contracts, exploring tariff waiver opportunities for research and development purposes, and deploying cost-engineering initiatives to preserve margins. These adaptive strategies are critical for sustaining market share and profitability in a landscape defined by evolving trade barriers and material cost volatility.
Key Insights from Segmentation by Material, Application, Process, and Cell Structure
Insights drawn from segmentation across material type, application category, manufacturing process, and cell structure reveal differentiated growth trajectories and strategic priorities. An analysis of material type indicates that aluminum honeycomb supports continue to dominate weight-sensitive sectors such as automotive crash management modules and portable thermal insulation systems. Meanwhile, stainless steel retains prominence where corrosion resistance and moderate-temperature endurance are essential, especially in petrochemical refining environments. Titanium honeycombs are achieving niche growth in aerospace and defense applications that demand high strength-to-weight performance under extreme thermal loads. Nickel-based supports remain indispensable for furnace support systems due to their exceptional high-temperature stability.
When examining application categories, the aerospace segment leads in stringent qualification cycles and premium pricing, driving continuous advancements in certification processes for both extruded and additively manufactured honeycombs. The automotive sector is rapidly expanding its footprint, integrating honeycomb supports into battery cooling systems, acoustic dampening panels, and safety structures. Furnace support applications maintain steady demand through the chemical processing and petrochemical refining subcategories, where thermal insulation and flow dynamics are critical for process efficiency and equipment longevity.
From a manufacturing process standpoint, extrusion continues to provide cost-efficiency and scalability for large-volume, uniform cell structures, making it the default choice for many industrial use cases. In contrast, 3D printing via selective laser melting is proving transformative for complex, low-volume prototypes and highly customized cell patterns that enhance fluid flow and heat transfer. Stereolithography, although less prevalent for metal alloys, is gaining traction for hybrid polymer-metal frameworks used in specialized insulation and acoustic solutions.
The cell structure type segmentation underscores the enduring appeal of hexagonal configurations for uniform stress distribution and mass efficiency. Rectangular cell layouts are favored in directional load-bearing applications, while circular cells excel in acoustic attenuation panels. Custom-designed honeycombs are emerging as a strategic differentiator for OEMs seeking bespoke performance characteristics in sectors ranging from renewable energy to advanced electronics cooling.
This comprehensive research report categorizes the Metal Honeycomb Support market into clearly defined segments, providing a detailed analysis of emerging trends and precise revenue forecasts to support strategic decision-making.
- Material Type
- Application Category
- Manufacturing Process
- Cell Structure Type
Regional Dynamics: Performance in Americas, EMEA, and Asia-Pacific
Regional performance trends underscore the importance of geographic diversification and market-specific strategies. In the Americas, robust aerospace manufacturing clusters in the United States and automotive assembly hubs in Mexico and Brazil are propelling demand for lightweight honeycomb supports, while nearshoring trends are enhancing supply chain agility. Europe, Middle East & Africa is witnessing steady growth driven by stringent environmental and safety regulations, extensive petrochemical refining operations in the Middle East, and ongoing investments in renewable energy infrastructure across Europe. Meanwhile, Asia-Pacific stands out for its expansive manufacturing base in China, Japan, and South Korea, combined with emerging aerospace and petrochemical projects in India and Southeast Asia. Cross-border collaborations and technology transfers among these regions are further accelerating innovation and driving localized production models to meet stringent quality and lead-time requirements.
This comprehensive research report examines key regions that drive the evolution of the Metal Honeycomb Support market, offering deep insights into regional trends, growth factors, and industry developments that are influencing market performance.
- Americas
- Asia-Pacific
- Europe, Middle East & Africa
Competitive Landscape: Profiles of Leading Metal Honeycomb Support Manufacturers
The competitive landscape is anchored by a diverse array of leading manufacturers, each leveraging unique strengths to capture market share. 3M Company applies its expertise in advanced materials and process automation to innovate high-performance aluminum and stainless steel honeycombs. Argosy International specializes in custom fabrication solutions for furnace support applications, focusing on nickel-based alloys. Corex Honeycomb integrates composite skins with honeycomb cores to deliver hybrid structures optimized for thermal insulation and impact resistance. Duocel offers a portfolio of reticulated foam-based structures and high-alloy metal honeycombs tailored for extreme-temperature environments. Euro-Composites distinguishes itself through patented cell geometry designs that enhance mechanical strength and fluid dynamics. Hexcel Corporation combines its aerospace-grade composite systems with honeycomb cores to produce ultra-lightweight, high-stiffness panels. M.C. Gill Corporation targets acoustic insulation and architectural applications with precision-formed honeycomb panels. Plascore Incorporated delivers both standard and customized cell sizes across multiple alloys, emphasizing rapid lead times. The Gill Corporation excels in precision extrusion and post-processing services that ensure tight tolerances for critical aerospace components. Toray Advanced Composites focuses on carbon-fiber reinforced honeycomb assemblies that meet the most demanding weight and performance specifications in defense and commercial aerospace.
This comprehensive research report delivers an in-depth overview of the principal market players in the Metal Honeycomb Support market, evaluating their market share, strategic initiatives, and competitive positioning to illuminate the factors shaping the competitive landscape.
- 3M Company
- Argosy International
- Corex Honeycomb
- Duocel
- Euro-Composites
- Hexcel Corporation
- M.C. Gill Corporation
- Plascore Incorporated
- The Gill Corporation
- Toray Advanced Composites
Actionable Recommendations for Industry Leaders to Drive Growth
To capitalize on evolving market dynamics and reinforce competitive advantage, industry leaders should consider the following actions. First, diversify material procurement by establishing multi-source agreements for aluminum, stainless steel, and nickel alloys to mitigate tariff and supply disruptions. Second, invest strategically in additive manufacturing capabilities-particularly selective laser melting-for rapid prototyping and low-volume, high-complexity designs that command premium margins. Third, forge collaborative partnerships with key end users in aerospace, automotive, and petrochemical sectors to co-develop tailored cell geometries that address specific thermal and mechanical requirements. Fourth, prioritize sustainability by integrating recycled materials into honeycomb cores and by optimizing production processes to reduce energy consumption and scrap rates. Fifth, expand regional footprints through licensing or joint ventures in high-growth markets such as Southeast Asia and the Middle East, enabling faster time to market and compliance with local content regulations. Sixth, implement advanced digital simulation platforms to predict product performance across thermal, fluidic, and structural scenarios, shortening development cycles and lowering validation costs. Lastly, develop comprehensive workforce training programs in advanced manufacturing and quality assurance to ensure consistent delivery of high-precision honeycomb supports.
Explore AI-driven insights for the Metal Honeycomb Support market with ResearchAI on our online platform, providing deeper, data-backed market analysis.
Ask ResearchAI anything
World's First Innovative Al for Market Research
Conclusion: Strategic Imperatives for the Metal Honeycomb Support Sector
The metal honeycomb support market stands at a pivotal juncture where material innovation, manufacturing excellence, and strategic agility converge to define winners and challengers alike. Success will hinge on an integrated approach that balances cost efficiency with performance differentiation. Manufacturers who seamlessly blend traditional extrusion methods with cutting-edge additive techniques, while actively managing tariff exposure and regional supply chains, will emerge as industry frontrunners. Equally important is the ability to anticipate end-user demands for bespoke cell structures and to deliver sustainably manufactured solutions that align with global decarbonization goals.
By embracing a forward-looking mindset and committing to continuous improvement across product design, process optimization, and market development, organizations can not only navigate present challenges but also unlock new avenues for value creation in sectors ranging from aerospace and automotive to chemical processing and renewable energy.
This section provides a structured overview of the report, outlining key chapters and topics covered for easy reference in our Metal Honeycomb Support market comprehensive research report.
- Preface
- Research Methodology
- Executive Summary
- Market Overview
- Market Dynamics
- Market Insights
- Cumulative Impact of United States Tariffs 2025
- Metal Honeycomb Support Market, by Material Type
- Metal Honeycomb Support Market, by Application Category
- Metal Honeycomb Support Market, by Manufacturing Process
- Metal Honeycomb Support Market, by Cell Structure Type
- Americas Metal Honeycomb Support Market
- Asia-Pacific Metal Honeycomb Support Market
- Europe, Middle East & Africa Metal Honeycomb Support Market
- Competitive Landscape
- ResearchAI
- ResearchStatistics
- ResearchContacts
- ResearchArticles
- Appendix
- List of Figures [Total: 24]
- List of Tables [Total: 281 ]
Take the Next Step: Connect with Ketan Rohom to Secure Your Comprehensive Report
Take the next step toward gaining a comprehensive understanding of market trends, competitive dynamics, and strategic opportunities. Connect with Ketan Rohom, Associate Director, Sales & Marketing, to secure your full research report today and equip your organization with the insights needed to lead in the metal honeycomb support industry.
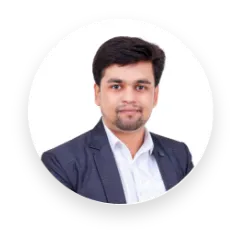
- When do I get the report?
- In what format does this report get delivered to me?
- How long has 360iResearch been around?
- What if I have a question about your reports?
- Can I share this report with my team?
- Can I use your research in my presentation?