The Mining Chemicals Market size was estimated at USD 11.03 billion in 2024 and expected to reach USD 11.65 billion in 2025, at a CAGR 5.74% to reach USD 15.43 billion by 2030.

Unveiling the Dynamics of the Mining Chemicals Sector Amid Geopolitical Shifts, Technological Innovation, and Environmental Imperatives
The landscape of mining chemicals is undergoing rapid evolution as forces of innovation, environmental responsibility, and global supply dynamics converge to redefine value creation. In this introduction, we establish the foundational context by examining how commodity demands, technological breakthroughs, and stakeholder expectations are collectively shaping the future trajectory. Through integrated approaches that balance cost efficiency with sustainability goals, industry participants are charting new paradigms in reagent design, process optimization, and value-chain collaboration.
Building on this context, we underscore the criticality of strategic foresight and adaptive capabilities. As fluctuations in raw material availability intersect with stringent regulatory frameworks, organizations are compelled to adopt holistic risk management frameworks that encompass procurement diversification, circular economy practices, and digital twins for process simulation. With these drivers in mind, this report embarks on a journey to explore transformative shifts, policy impacts, segmentation insights, and regional dynamics that collectively illuminate the next horizon for mining chemicals.
Tracing the Pivotal Transformative Shifts Reshaping Mining Chemicals Through Digitalization, Process Intensification, and Circular Economy Integration
The mining chemicals sector is experiencing transformative shifts that extend far beyond incremental improvements in reagent performance. Advances in digitalization have enabled the adoption of real-time analytics and machine learning algorithms to optimize dosage, predict reagent efficacy, and reduce waste generation. These innovations not only enhance throughput and recovery rates but also strengthen environmental stewardship by minimizing chemical footprints and water usage.
Simultaneously, process intensification techniques are revolutionizing equipment design and operational paradigms. Compact reaction systems, modular plant configurations, and intensified mixing technologies are unlocking unprecedented gains in mass transfer and energy efficiency. When these engineering innovations are coupled with circular economy principles-such as reagent recycling, by-product valorization, and bio-based reagent formulations-the sector is positioned to break traditional trade-offs between productivity and sustainability. As a result, companies that integrate these transformative shifts will be primed to lead in both economic and environmental performance.
Assessing the Cumulative Impact of 2025 United States Tariffs on Mining Chemicals Supply Chains, Cost Structures, and Strategic Sourcing Decisions
The imposition of United States tariffs in 2025 has introduced a complex array of cost pressures, supply-chain realignments, and strategic sourcing challenges for stakeholders across the mining chemicals domain. While the initial intent of the tariffs focused on safeguarding domestic production capabilities, the cumulative effect has been a recalibration of global reagent flows, with end-users seeking alternative suppliers in regions less impacted by trade barriers.
Consequently, procurement teams have ramped up near-shoring initiatives and intensified partnerships with regional reagent manufacturers to mitigate lead-time uncertainties and currency volatility risks. At the same time, chemistry developers are investing in local manufacturing facilities and joint-venture arrangements to preserve market access in key geographies. Against this backdrop, forward-looking organizations are leveraging scenario-planning tools to stress-test their portfolios, ensuring resilience in the face of ongoing policy fluctuations and evolving tariff regimes.
Key Segmentation Insights Illuminating How Type, Form, and Application Dynamics Drive Differentiated Value in the Mining Chemicals Landscape
Insights into market segmentation reveal nuanced performance drivers across multiple dimensions. When analyzing by type, collectors distinguish themselves through tailored surface-chemistry interactions that enhance recovery rates, whereas depressants are optimized for selective inhibition in complex ore matrices. Dilutants and dust suppressants play critical roles in operational safety and environmental compliance, while extractants and flocculants exhibit differentiated efficacy based on their chemical origins-spanning inorganic flocculants, natural polysaccharides, and synthetic polymers. Frothers and grinding aids further refine flotation performance and comminution efficiency, underscoring the importance of type selection in reagent blending strategies.
Form-based differentiation also shapes procurement and application choices. Liquid formulations offer rapid solubility and precise dosing control, enabling dynamic process adjustments, while solid reagents provide logistical advantages in remote operations and simplified handling protocols. In terms of application, explosives and drilling chemicals dominate surface and underground operations with tailored energy-release profiles, while mineral processing reagents adapt to metallic and non-metallic mineral matrices. Water and wastewater treatment chemicals address effluent management imperatives, driving innovations in reagent recovery, sludge dewatering, and discharge compliance. By examining these segmentation insights holistically, decision-makers can identify high-impact intervention points to enhance operational flexibility and cost efficiency.
This comprehensive research report categorizes the Mining Chemicals market into clearly defined segments, providing a detailed analysis of emerging trends and precise revenue forecasts to support strategic decision-making.
- Type
- Form
- Application
Key Regional Insights Demystifying the Roles of Americas, Europe Middle East Africa, and Asia-Pacific in Diversifying Mining Chemicals Demand and Innovation
Regional dynamics profoundly influence strategic priorities and investment trajectories in the mining chemicals sector. In the Americas, end-users are increasingly prioritizing decarbonization pathways and tailings management solutions, spurring demand for green reagents and automated monitoring systems. Meanwhile, in Europe, Middle East, and Africa, regulatory harmony coupled with ambitious sustainability targets is driving partnerships focused on low-emission reagent platforms and closed-loop water treatment processes. The diversity of ore bodies across these regions further amplifies the need for bespoke reagent chemistries that align with local mineralogy and operational infrastructures.
Across the Asia-Pacific region, rapid capacity expansions and infrastructure investments are fueling robust growth in both traditional reagent lines and next-generation formulations. Emerging markets within the region are accelerating technology adoption through government incentives and public-private collaborations, while established players are deepening their R&D footprints to tailor solutions for complex orebodies and challenging geographies. These regional insights underscore the imperative for adaptable supply strategies and targeted innovation roadmaps that resonate with localized market drivers and stakeholder expectations.
This comprehensive research report examines key regions that drive the evolution of the Mining Chemicals market, offering deep insights into regional trends, growth factors, and industry developments that are influencing market performance.
- Americas
- Europe, Middle East & Africa
- Asia-Pacific
Key Companies Insights Highlighting Strategic Positioning, Collaborative Ventures, and Innovation Programs Powering Leadership in Mining Chemicals Domain
Leading chemical manufacturers and specialized reagent providers are driving competitive dynamics through differentiated value propositions and collaborative ecosystems. Strategic alliances between mining houses and chemistry developers have accelerated co-development of proprietary reagents, enabling rapid field validation and technology scaling. Meanwhile, established multinationals are pursuing bolt-on acquisitions of niche players to bolster portfolios in high-growth segments such as bio-inspired reagents and nano-engineered flocculants.
Investment in innovation hubs and technical service centers has emerged as a key differentiator, allowing companies to offer integrated lifecycle support-from laboratory feasibility studies to full-scale plant optimization. This service-oriented approach reinforces customer loyalty and unlocks cross-selling opportunities, particularly in regions navigating stringent environmental regulations. As a result, companies that can seamlessly integrate R&D, technical services, and supply-chain agility will be best positioned to capture long-term value in evolving mining chemicals markets.
This comprehensive research report delivers an in-depth overview of the principal market players in the Mining Chemicals market, evaluating their market share, strategic initiatives, and competitive positioning to illuminate the factors shaping the competitive landscape.
- AECI Mining Chemicals
- Arkema SA
- Ashland Inc.
- BASF SE
- Betachem (Pty) Ltd.
- Celanese Corporation
- Charles Tennant & Company by Tenant Company
- Chevron Phillips Chemical Company LLC
- Clariant AG
- Ecolab Inc.
- Evonik Industries AG
- ExxonMobil Corporation
- Fardad Mining Chem
- InterChem
- International Chemical Group
- Kemira Oyj
- Marlyn Chemicals
- Nasaco International Ltd.
- Nouryon Chemicals Holding B.V.
- Orica Limited
- Protea Mining Chemicals by Omnia Group
- Qingdao Ruchang Mining Industry Co. Ltd
- Quaker Chemical Corporation
- Sasol Limited
- SNF Group
- Solenis International LLC
- Solvay S.A.
- The Dow Chemical Company
- Vizag Chemicals
- Wego Chemical Group
- Y&X Beijing Technology Co., Ltd.
Actionable Recommendations for Industry Leaders to Navigate Disruptions, Capitalize on Emerging Technologies, and Foster Sustainable Mining Chemicals Practices
To navigate emerging disruptions and capture untapped opportunities, industry leaders should adopt a multi-pronged strategy that prioritizes both innovation and resilience. First, investing in advanced analytics platforms with predictive capabilities can streamline reagent usage patterns and anticipate maintenance needs, thereby reducing downtime and optimizing total cost of ownership. Second, forging cross-industry collaborations-spanning chemical suppliers, technology providers, and mining operators-will accelerate co-innovation cycles and foster shared risk-reward frameworks.
Moreover, embedding circular economy principles into reagent lifecycles can unlock cost savings and enhance environmental credentials, particularly through reagent recovery, solvent recycling, and waste valorization pathways. Complementing these measures, robust talent development programs that upskill process engineers, data scientists, and sustainability experts will ensure a future-ready workforce capable of translating strategic ambitions into operational outcomes. Finally, proactive engagement with regulators and community stakeholders can safeguard social license to operate, enabling timely permitting and fostering goodwill that underpins project viability.
Research Methodology Overview Detailing Rigorous Data Collection, Qualitative Interviews, and Multilayered Analysis Underpinning the Mining Chemicals Study
This research employs a multi-layered methodology combining quantitative rigor with qualitative depth to deliver actionable insights. Primary data collection involved in-depth interviews with senior R&D leaders, procurement heads, and technical service managers to capture firsthand perspectives on reagent performance, emerging requirements, and investment priorities. Secondary research encompassed peer-reviewed journals, industry white papers, and regulatory filings to validate technological trends and sustainability benchmarks.
Data triangulation techniques were applied to reconcile findings across diverse sources, ensuring analytical robustness and minimizing bias. Additionally, scenario-planning models were constructed to assess the sensitivity of supply chains, cost structures, and regulatory impacts under varying market conditions. Expert workshops facilitated collaborative validation of preliminary insights and refined strategic frameworks based on real-world operational constraints. The integration of these methodological pillars underpins the report’s credibility and equips stakeholders with a nuanced understanding of the mining chemicals domain.
Explore AI-driven insights for the Mining Chemicals market with ResearchAI on our online platform, providing deeper, data-backed market analysis.
Ask ResearchAI anything
World's First Innovative Al for Market Research
Concluding Reflections Emphasizing Strategic Agility, Collaborative Innovation, and Sustainable Stewardship as Pillars for the Future of Mining Chemicals Industry
Reflecting on the insights presented, it becomes evident that the mining chemicals sector is at a strategic inflection point driven by technological innovation, policy dynamics, and sustainability imperatives. Organizations that embrace process intensification, digitalization, and circular economy principles will unlock new performance thresholds while mitigating environmental footprints. Simultaneously, agility in navigating trade policy shifts-such as the 2025 tariffs-will be critical to maintaining supply-chain resilience and financial discipline.
Ultimately, the future of mining chemicals will be characterized by collaborative innovation ecosystems, where cross-sector partnerships and decentralized production models drive localized value creation. By synthesizing segmentation nuances with regional market dynamics and competitive landscapes, decision-makers can craft targeted strategies that bolster operational excellence and drive long-term growth. The insights distilled in this report offer a strategic blueprint for stakeholders seeking to lead in the evolving mining chemicals arena.
This section provides a structured overview of the report, outlining key chapters and topics covered for easy reference in our Mining Chemicals market comprehensive research report.
- Preface
- Research Methodology
- Executive Summary
- Market Overview
- Market Dynamics
- Market Insights
- Cumulative Impact of United States Tariffs 2025
- Mining Chemicals Market, by Type
- Mining Chemicals Market, by Form
- Mining Chemicals Market, by Application
- Americas Mining Chemicals Market
- Europe, Middle East & Africa Mining Chemicals Market
- Asia-Pacific Mining Chemicals Market
- Competitive Landscape
- ResearchAI
- ResearchStatistics
- ResearchContacts
- ResearchArticles
- Appendix
- List of Figures [Total: 24]
- List of Tables [Total: 622 ]
Call-To-Action Encouraging Engagement with Associate Director Sales Marketing to Secure Advanced Mining Chemicals Market Research for Informed Decision Making
Don’t miss the opportunity to gain a competitive edge by accessing the most comprehensive research on the mining chemicals sector. Connect with Ketan Rohom, Associate Director of Sales & Marketing, to discuss how this in-depth report can address your specific strategic challenges and equip you with insights tailored to accelerate growth. Engage directly with Ketan Rohom to explore customized solutions, secure exclusive early access to critical data sets, and leverage expert consultation to refine your operational roadmap. Embark on a data-driven journey that empowers you to optimize procurement strategies, enhance process efficiency, and strengthen stakeholder alignment across your value chain. Reach out now to schedule a personalized briefing, unlock sample excerpt chapters, and negotiate package options designed around your unique objectives. Your pathway to actionable intelligence starts today-take the decisive step towards informed decision-making and sustained market leadership in the dynamic mining chemicals landscape.
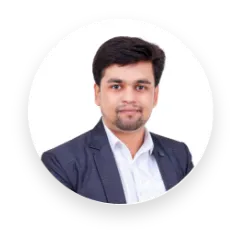
- How big is the Mining Chemicals Market?
- What is the Mining Chemicals Market growth?
- When do I get the report?
- In what format does this report get delivered to me?
- How long has 360iResearch been around?
- What if I have a question about your reports?
- Can I share this report with my team?
- Can I use your research in my presentation?