An in-depth overview of the modified specialty polymer materials sector highlighting pivotal industry drivers, technological advancements, and market evolution
The modified specialty polymer materials sector stands at a pivotal juncture, driven by the convergence of technological advancements, shifting regulatory pressures, and evolving end-use requirements. In recent years, manufacturers have leveraged chemical modification techniques to enhance performance attributes such as thermal stability, mechanical strength, and chemical resistance, opening new frontiers for applications in demanding environments. Moreover, sustainability imperatives have accelerated the adoption of bio-based and recycled polymers, prompting innovators to refine formulations that align with circular economy principles without compromising material performance.
This dynamic environment has been further enriched by cross-industry collaborations, where research teams in automotive, electronics, and construction converge to tailor polymer properties for specific use cases. As electric vehicles gain momentum, lightweight epoxy systems are engineered for battery enclosures, while silicone polymers are fine-tuned for high-voltage insulation in renewable energy infrastructure. Meanwhile, polyurethane foams optimized for thermal insulation underscore the material’s versatility in energy-efficient building envelopes.
Looking ahead, the interplay of digital design tools and additive manufacturing techniques promises to accelerate prototyping cycles, empowering formulators to simulate and iterate polymer modifications with unprecedented precision. Consequently, stakeholders across the value chain-from raw material suppliers to end-use OEMs-must navigate this rapidly shifting landscape by aligning R&D investments with emerging market demands and regulatory trajectories.
Emerging technological breakthroughs, regulatory overhauls, and evolving market needs driving transformative shifts in the specialty polymer materials landscape
The specialty polymer ecosystem is undergoing an inflection point driven by breakthrough innovations in nanocomposite engineering, sustainable feedstocks, and advanced manufacturing processes. In particular, the integration of functional nanoparticles into epoxy and polyurethane matrices has yielded striking enhancements in barrier properties and thermal conductivity, enabling next-generation coatings and adhesives for harsh service conditions. In parallel, the maturation of bio-sourced monomers has catalyzed the emergence of silicone and polyurethane variants that meet stringent environmental standards without sacrificing durability.
Regulatory landscapes are also evolving at a rapid pace, as governments worldwide tighten restrictions on volatile organic compound emissions and mandate higher recycling quotas. These shifts are compelling material developers to pivot toward water-based systems and novel crosslinking chemistries that reduce ecological footprints. Furthermore, policy incentives for circularity have intensified competition among suppliers to demonstrate cradle-to-grave sustainability credentials, spurring investments in chemical recycling and closed-loop manufacturing models.
In addition to these technological and regulatory forces, end-use markets are redefining their material requirements. The demand for lightweight structural adhesives in automotive interiors and underhood components is escalating, driven by fuel efficiency targets and electric powertrain integration. Similarly, the electronics sector is seeking polymer formulations that balance miniaturization with robust fire retardancy and dielectric performance. Taken together, these converging factors are reshaping the specialty polymer landscape and setting the stage for transformative growth trajectories.
Assessing the cumulative repercussions of the 2025 United States tariffs on modified specialty polymer materials across supply chains and regional hubs
The introduction of new tariff measures in the United States during 2025 has introduced additional layers of complexity to global supply chains for modified specialty polymer materials. Building upon existing duties on certain resin and polymer imports, the expanded tariff classifications now cover a broader array of epoxy resin subtypes and specialty silicones, resulting in higher landed costs for affected products. In response, many end-users have accelerated their sourcing diversification strategies, seeking alternative suppliers in regions with preferential trade agreements to mitigate exposure to these levies.
Furthermore, the cumulative impact of these duties has prompted a reevaluation of domestic production capacities. Several North American compounders have announced capacity add-backs and forward integration initiatives to capture margin opportunities created by the elevated import barriers. At the same time, the shift toward localized feedstock production has underscored the importance of securing stable supplies of key intermediates such as bisphenol derivatives and MDI precursors.
Despite the initial cost pressures, the tariff environment has also stimulated innovation in cost-effective formulation techniques. Formulators are increasingly leveraging reactive diluents, synergistic crosslinkers, and recycled content to offset higher resin acquisition costs. Consequently, while the tariff adjustments pose short-term challenges, they are catalyzing a more resilient and regionally diversified specialty polymer supply network.
Unveiling critical segmentation insights across polymer type, end use industry, application area, and form factor that define specialty polymer dynamics
Critical segmentation analysis reveals that polymer type remains a fundamental determinant of material performance and value proposition. Within the epoxy resin category, formulations based on bisphenol A continue to dominate applications demanding high mechanical strength and corrosion resistance, whereas bisphenol F variants have carved a niche in electronics manufacturing thanks to their reduced brittleness and low ionic content. In the polyurethane segment, MDI-based systems offer superior rigidity and abrasion resistance for underhood components, while TDI-based chemistries excel in flexible foam and sealant formulations where elongation and resilience are paramount. Silicone polymers, divided between dimethyl backbones for broad-spectrum thermal stability and phenylmethyl hybrids for enhanced low-temperature flexibility, illustrate the nuanced trade-offs that formulators must balance.
End use industry segmentation underscores the diverse demand drivers guiding specialty polymer adoption. In the automotive sector, interior applications such as seat trim adhesives prioritize aesthetic durability and chemical resistance, contrasting with underhood sealants engineered for high temperatures and fluid exposure. Construction markets split between coatings designed for decorative appeal and specialized sealants and adhesives that ensure structural integrity and weatherproofing. Electronics and electrical end uses bifurcate into PCB laminates requiring exceptional dielectric performance and wire and cable insulation systems optimized for flame retardancy and mechanical endurance.
Application area analysis shows that adhesives and sealants leverage silicone sealants for gap-filling and structural adhesives for load-bearing joints, while decorative coatings aim for visual finishes and protective coatings emphasize abrasion and chemical resistance. Foam applications diverge into flexible foam tailored for cushioning and comfort and rigid foam engineered for insulation and structural support. Form factor segmentation further differentiates material delivery systems, as cast films and extruded films offer thin-gauge protection layers, solvent-based and water-based liquids cater to diverse environmental requirements, and thermoplastic and thermoset powders enable advanced coating techniques with minimal overspray.
This comprehensive research report categorizes the Modified Specialty Polymer Material market into clearly defined segments, providing a detailed analysis of emerging trends and precise revenue forecasts to support strategic decision-making.
- Polymer Type
- End Use Industry
- Application Area
- Form Factor
Key regional insights decoding growth catalysts and strategic challenges across the Americas, Europe Middle East and Africa, and Asia-Pacific markets
Regional dynamics in the Americas reflect both maturity in established markets and rapid growth in emerging economies. North America exhibits robust capacity expansions in epoxy and polyurethane compounding, driven by nearshoring trends and decarbonization mandates that favor localized supply. Latin America, meanwhile, is witnessing an uptick in demand for construction sealants and automotive adhesives as infrastructure investments accelerate and vehicle production rebounds. These divergent trajectories underscore the importance of region-specific strategies that accommodate varying regulatory frameworks and logistical considerations.
The Europe Middle East and Africa region presents a mosaic of regulatory complexities and opportunity zones. Stricter emissions and sustainability requirements across the European Union have galvanized formulation shifts toward water-based and low-VOC systems, while petrochemical-rich nations in the Middle East are investing in integrated chemical parks to capture higher value in specialty polymer production. Africa’s nascent markets, though currently smaller in scale, are gradually opening to imported advanced sealants and coatings as urbanization and energy needs grow.
Asia-Pacific continues to anchor global specialty polymer supply, bolstered by vast production capacities in China, South Korea, and Japan. China’s domestic innovation in bisphenol derivatives and reactive silicone precursors is complementing government incentives aimed at upgrading chemical manufacturing. Elsewhere in the region, India is expanding its polyurethane foam and coatings sectors to support residential and commercial construction booms, while Southeast Asian hubs are emerging as cost-competitive sources for both film and powder form factors.
This comprehensive research report examines key regions that drive the evolution of the Modified Specialty Polymer Material market, offering deep insights into regional trends, growth factors, and industry developments that are influencing market performance.
- Americas
- Europe, Middle East & Africa
- Asia-Pacific
Profiling influential market participants and their strategic initiatives shaping the competitive landscape of modified specialty polymer materials
Industry leaders in specialty polymer materials are deploying multifaceted strategies to secure competitive advantage. Global chemical majors are directing significant R&D funds toward next-generation crosslinker systems and bio-based monomer platforms, recognizing that material innovation is a critical differentiator. Simultaneously, several companies are forging alliances with downstream OEMs to co-develop turnkey formulations tailored to specific performance criteria, thereby deepening customer engagement and accelerating time-to-market.
Mergers and acquisitions remain instrumental in consolidating value chain capabilities, with key players acquiring niche compounding businesses to enhance their product portfolios in electronic laminates and high-temperature silicones. In parallel, smaller specialized firms are carving out unique positions by focusing on high-marginal segments such as structural adhesives for aerospace and precision coating powders for additive manufacturing. Sustainability commitments are also reshaping competitive dynamics, as market participants vie to achieve carbon neutrality targets and secure eco-certifications that resonate with environmentally conscious end users.
To navigate supply chain complexities, leading suppliers are investing in digital platforms that provide real-time visibility into raw material sourcing and inventory levels. By integrating advanced analytics and predictive maintenance protocols, these organizations aim to enhance operational resilience and reduce downtime. Collectively, these strategic imperatives are defining the competitive contours of the modified specialty polymer materials market.
This comprehensive research report delivers an in-depth overview of the principal market players in the Modified Specialty Polymer Material market, evaluating their market share, strategic initiatives, and competitive positioning to illuminate the factors shaping the competitive landscape.
- Arkema S.A.
- Evonik Industries AG
- BASF SE
- Dow Inc.
- Solvay S.A.
- Celanese Corporation
- DuPont de Nemours, Inc.
- Mitsubishi Chemical Holdings Corporation
- LANXESS AG
- Covestro AG
Actionable strategies for industry leaders to capitalize on emerging opportunities and mitigate risks within the specialty polymer materials sector
Industry leaders seeking to capitalize on the dynamic specialty polymer marketplace should prioritize supply chain diversification, ensuring access to critical bisphenol and isocyanate feedstocks from multiple geographic sources. Embedding alternative resin chemistries into product roadmaps can further mitigate raw material volatility while demonstrating sustainability credentials. Moreover, investing in modular manufacturing platforms will enable rapid line reconfiguration as formulation requirements evolve under regulatory and commercial pressures.
Strategic collaboration with end users is equally crucial. Co-innovation partnerships that align R&D efforts with customer performance targets can unlock differentiated products and deepen market penetration. These partnerships should be supported by agile pilot plants and digital simulation tools that accelerate the iterative testing of novel polymer blends. In addition, aligning product offerings with circular economy frameworks-such as designing for recyclability and incorporating post-consumer recycled content-will strengthen market positioning and future-proof portfolios against tightening environmental regulations.
Finally, leveraging data analytics for predictive maintenance and quality assurance can significantly reduce operational risk. Implementing integrated dashboards that monitor critical process parameters and raw material quality metrics will enhance consistency and drive cost efficiencies. By embracing these combined strategies, industry leaders can not only navigate near-term tariff headwinds but also secure long-term competitive advantage.
Comprehensive research methodology employing rigorous primary and secondary approaches to ensure the reliability of specialty polymer market insights
This study employs a rigorous research methodology that integrates both primary and secondary data sources to ensure the validity of its findings. Primary research encompassed in-depth interviews with senior R&D managers, procurement executives, and technical directors across key specialty polymer producers and end-use industries. These engagements provided firsthand insights into formulation trends, supply chain challenges, and application requirements.
Secondary research involved the systematic review of peer-reviewed journals, patent databases, and regulatory filings to track technological breakthroughs and compliance shifts. Trade association reports and industry conferences supplemented this process by revealing real-time developments in production capacities and market collaborations. Data triangulation techniques were applied to reconcile discrepancies between sources and generate a coherent narrative of market dynamics.
Quantitative analysis focused on segment-level data derived from customs records, trade flows, and shipment volumes, while qualitative assessments explored strategic initiatives and partnership models. Throughout the research process, stringent validation protocols were enforced, including cross-verification of critical metrics with end-user feedback and expert panel reviews, to uphold the accuracy and reliability of the insights presented.
Explore AI-driven insights for the Modified Specialty Polymer Material market with ResearchAI on our online platform, providing deeper, data-backed market analysis.
Ask ResearchAI anything
World's First Innovative Al for Market Research
Synthesizing the critical findings and future outlook for modified specialty polymer materials to equip stakeholders with strategic clarity
In synthesizing the key findings, it becomes clear that the modified specialty polymer materials domain is characterized by rapid technological evolution, intricate regulatory landscapes, and nuanced segmentation dynamics. The interplay between epoxy, polyurethane, and silicone chemistries underpins a rich tapestry of performance options that end-use industries must navigate with precision. Geopolitical shifts and tariff adjustments are reshaping supply chain geographies, urging stakeholders to pursue localized manufacturing and diversified sourcing.
Looking ahead, sustained investment in sustainable feedstocks and digital design tools will be instrumental in unlocking next-generation polymer solutions that meet stringent environmental targets and performance benchmarks. Strategic partnerships between material suppliers and OEMs will accelerate the translation of laboratory breakthroughs into commercial applications, particularly in high-growth sectors such as electric vehicles, renewable energy, and advanced electronics.
Ultimately, equipping decision-makers with these insights will foster more informed strategic planning and enable organizations to seize emerging opportunities while mitigating the inherent risks of a rapidly evolving marketplace. The comprehensive perspective offered herein provides a solid foundation for navigating the complexities of the specialty polymer landscape with confidence and foresight.
This section provides a structured overview of the report, outlining key chapters and topics covered for easy reference in our Modified Specialty Polymer Material market comprehensive research report.
- Preface
- Research Methodology
- Executive Summary
- Market Overview
- Market Dynamics
- Market Insights
- Cumulative Impact of United States Tariffs 2025
- Modified Specialty Polymer Material Market, by Polymer Type
- Modified Specialty Polymer Material Market, by End Use Industry
- Modified Specialty Polymer Material Market, by Application Area
- Modified Specialty Polymer Material Market, by Form Factor
- Americas Modified Specialty Polymer Material Market
- Europe, Middle East & Africa Modified Specialty Polymer Material Market
- Asia-Pacific Modified Specialty Polymer Material Market
- Competitive Landscape
- ResearchAI
- ResearchStatistics
- ResearchContacts
- ResearchArticles
- Appendix
- List of Figures [Total: 26]
- List of Tables [Total: 1434 ]
Secure your advanced market research report on modified specialty polymer materials today to drive informed decisions and strategic growth
To unlock comprehensive intelligence on modified specialty polymer materials and gain exclusive access to actionable insights, we invite you to secure your copy of the full market research report. Reach out directly to Ketan Rohom, Associate Director, Sales & Marketing, who will guide you through the detailed findings and ensure you receive tailored support for your strategic planning needs. Don’t miss the opportunity to leverage this in-depth analysis to fortify your market position and drive informed decisions that propel growth.
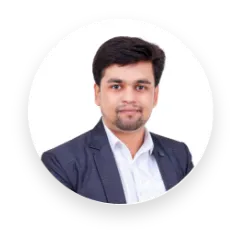
- When do I get the report?
- In what format does this report get delivered to me?
- How long has 360iResearch been around?
- What if I have a question about your reports?
- Can I share this report with my team?
- Can I use your research in my presentation?