Introduction to Molybdenum Wire Spraying Applications
Molybdenum wire plays a pivotal role in spray coating technologies, delivering exceptional thermal stability, corrosion resistance, and mechanical strength. As industries from aerospace to medical devices push for ever-higher performance standards, the demand for precision-engineered molybdenum wire feedstock has surged. This executive summary illuminates the evolving market landscape, highlighting key technological innovations, policy shifts, and competitive dynamics. It sets the stage by examining transformative trends, the implications of recent U.S. tariffs, segmentation nuances, regional variations, and leading players. By synthesizing these insights, decision-makers can navigate complexities, optimize supply chains, and position their organizations for sustained growth in a market defined by rigorous performance requirements and regulatory headwinds.
Transformative Shifts Reshaping the Molybdenum Wire Landscape
Recent years have witnessed transformative shifts that are redefining how molybdenum wire is produced, processed, and applied in spray coating operations. Advanced alloy formulations such as molybdenum-lanthanum and titanium-zirconium-molybdenum (TZM) have unlocked new performance thresholds in wear protection and thermal barrier coatings. Concurrently, additive manufacturing and automated deposition systems now integrate real-time process monitoring, enabling tighter control over deposition rates, bond strength, and surface finish.
Sustainability considerations have spurred adoption of closed-loop recycling programs and energy-efficient production techniques, while digital twins and predictive analytics optimize equipment uptime and reduce scrap. Electrification of key end uses, particularly in aerospace and automotive power units, has driven demand for high-purity molybdenum wire capable of withstanding extreme thermal cycling. As a result, suppliers and end users alike are forging cross-industry collaborations to accelerate material development and streamline supply chains. These innovations are collectively reshaping competitive dynamics, creating new value pools, and elevating performance expectations across the spraying landscape.
Assessing the Cumulative Impact of U.S. Tariffs in 2025
In 2025, newly imposed U.S. tariffs on imported molybdenum wire have significantly altered cost and sourcing strategies across multiple industries. By raising import duties on key grades, including high-purity and alloyed variants, domestic wire prices have experienced upward pressure, prompting procurement teams to reassess global supply options. As a result, Tier-1 aerospace and automotive manufacturers are accelerating qualification of alternative suppliers and expanding domestic capacity to mitigate duty exposure.
Procurement-led cost-containment efforts have accelerated the trend toward near-shoring, while strategic stockpiling has emerged as a buffer against sudden duty adjustments. Some end users have negotiated cost-sharing agreements with system integrators, effectively distributing tariff impacts throughout the value chain. In parallel, molybdenum producers are exploring tariff-exempt routing through free trade zones and leveraging bilateral trade agreements to maintain competitive positioning. Collectively, these measures underscore the critical importance of agile sourcing and policy-informed supply chain strategies in navigating an increasingly complex tariff environment.
Key Segmentation Insights Driving Market Dynamics
Disaggregating market dynamics by type reveals that molybdenum alloys-particularly those engineered from molybdenum-lanthanum blends and TZM-are gaining traction for demanding thermal barrier coatings, while pure molybdenum continues to dominate corrosion protection applications due to its inherent stability. Sintered molybdenum, with its tailored porosity and density characteristics, is preferred for specialty restoration tasks.
Diameter range also influences application suitability: wire between 0.1 mm and 0.3 mm is favored for precision surface restoration, whereas wires exceeding 0.3 mm deliver higher deposition rates in high-volume wear protection. Ultra-fine wires under 0.1 mm enable intricate flame and arc spraying, enhancing bond strength in micro-scale coatings.
Production technique segmentation highlights cold drawing’s superiority in achieving tight dimensional tolerances, while hot drawing imparts ductility critical for high-velocity oxy-fuel (HVOF) processes. Conventional extrusion and rolling remain cost-effective for bulk coil and spool production.
On the spraying process front, arc spraying is widely adopted for economical corrosion mitigation, flame spraying for rapid surface restoration, HVOF for dense, high-adherence thermal barrier coatings, and plasma spraying when ultimate coating performance is essential.
Applications span corrosion protection in marine and chemical industries, restoration of worn components across oil & gas, high-performance thermal barrier coatings in gas turbines, and wear protection for mining equipment.
End uses range from aerospace structural components to automotive brake systems and engine parts, high-reliability electronics, and biocompatible medical device surfaces. Within automotive, brake system coatings require precise heat management, while engine component layers demand exceptional wear resistance.
Finally, product form selection-from coiled wire to spooled or straight lengths-reflects handling preferences, equipment compatibility, and coating volume requirements, underscoring the importance of tailored supply to meet diverse operational workflows.
This comprehensive research report categorizes the Molybdenum Wire for Spraying market into clearly defined segments, providing a detailed analysis of emerging trends and precise revenue forecasts to support strategic decision-making.
- Type
- Diameter Range
- Production Technique
- Spraying Process
- Application
- End Use
- Product Form
Regional Variations Influencing Growth Patterns
Regional dynamics continue to shape strategic priorities for molybdenum wire suppliers and end users. In the Americas, established aerospace fabricators and automotive OEMs are investing heavily in domestic alloy R&D and production capacity expansion to offset tariff-induced cost pressures. Local policy incentives for advanced manufacturing and infrastructure spending further bolster demand for high-performance coatings.
Across Europe, the Middle East, and Africa, stringent environmental regulations and rising defense budgets are driving adoption of durable, thermal-stable coatings, while Middle Eastern oil and gas operators invest in corrosion-resistant piping and equipment linings. European Union carbon targets are accelerating energy-efficient production methods, favoring suppliers with robust sustainability credentials.
In Asia-Pacific, rapid industrialization, expanding electronics manufacturing hubs, and surging medical device production are fueling demand for ultra-fine wire in precision applications. China’s growing domestic milling and spraying capacities are complemented by government-backed technology platforms, while Southeast Asian OEM clusters in automotive and consumer electronics seek cost-effective, high-quality wire feedstock to support localized value chains.
This comprehensive research report examines key regions that drive the evolution of the Molybdenum Wire for Spraying market, offering deep insights into regional trends, growth factors, and industry developments that are influencing market performance.
- Americas
- Asia-Pacific
- Europe, Middle East & Africa
Competitive Landscape and Leading Company Profiles
The competitive landscape is defined by a diverse set of global and regional players, each leveraging unique strengths to capture market share. ALB Materials Inc. and ALMT Corp. have established advanced alloy development centers, accelerating proprietary formulation roll-outs. American Elements Inc. and ChinaTungsten Online (Xiamen) Manufacturing & Sales Corp. emphasize scalable production capabilities to serve large-volume end users.
Edgetech Industries LLC and Global Tungsten & Powders Corp have strengthened their market positions through targeted acquisitions, expanding downstream finishing and distribution networks. Goodfellow Cambridge Limited and H.C. Starck Solutions LLC are renowned for premium-quality wire optimized for critical aerospace and defense applications.
Luoyang Dingding Tungsten & Molybdenum Materials Co., Ltd and Xiamen Honglu Tungsten & Molybdenum Industry Co., Ltd focus on integrated domestic supply chains in China, while Midwest Tungsten Service Inc. specializes in engineered product forms and just-in-time delivery models for North American customers.
Plansee SE continues to invest in additive manufacturing integration, and Rhenium Alloys, Inc. is advancing composite wire solutions for extreme-temperature applications. Tekna Holding AS champions nanoparticle-enhanced powders, and Top Seiko Co., Ltd delivers precision drawing services for micro-diameter feedstock. Together, these firms drive continuous innovation, quality standards, and regional diversification across the molybdenum wire market.
This comprehensive research report delivers an in-depth overview of the principal market players in the Molybdenum Wire for Spraying market, evaluating their market share, strategic initiatives, and competitive positioning to illuminate the factors shaping the competitive landscape.
- ALB Materials Inc.
- ALMT Corp.
- American Elements Inc.
- ChinaTungsten Online (Xiamen) Manu. & Sales Corp.
- Edgetech Industries LLC
- Global Tungsten & Powders Corp
- Goodfellow Cambridge Limited
- H.C. Starck Solutions LLC
- Luoyang Dingding Tungsten & Molybdenum Materials Co., Ltd
- Midwest Tungsten Service Inc.
- Plansee SE
- Rhenium Alloys, Inc.
- Tekna Holding AS
- Top Seiko Co., Ltd.
- Xiamen Honglu Tungsten & Molybdenum Industry Co., Ltd.
Actionable Recommendations for Industry Leaders
Industry leaders should pursue a multi-faceted strategy to capitalize on emerging opportunities and mitigate risks. First, invest in advanced alloy R&D and co-development partnerships with key end users to create application-specific wire solutions that command premium pricing. Second, optimize production by integrating digital process controls, predictive maintenance, and energy-efficient manufacturing to reduce costs and bolster sustainability credentials.
Third, diversify sourcing and establish dual-sourcing arrangements across multiple geographies to buffer against tariff fluctuations and supply disruptions. Fourth, align with OEMs through early-stage collaboration on new coating technologies-especially in electrified powertrains and additive manufacturing sectors-to secure long-term offtake agreements.
Fifth, expand value-added services such as on-site technical support, customized wire form fabrication, and lifecycle coating performance analysis to deepen customer relationships and drive aftermarket revenue. Sixth, monitor policy developments in regional free trade zones and leverage favorable trade agreements to optimize cost structure. Finally, prioritize workforce training in advanced drawing and spraying technologies, fostering the talent pool necessary to sustain innovation and operational excellence.
Explore AI-driven insights for the Molybdenum Wire for Spraying market with ResearchAI on our online platform, providing deeper, data-backed market analysis.
Ask ResearchAI anything
World's First Innovative Al for Market Research
Conclusion and Strategic Outlook
The molybdenum wire for spraying market stands at an inflection point, driven by performance-critical applications, tightening regulations, and evolving trade policies. Technological advances in alloy composition, process automation, and sustainability are redefining competitive boundaries, while U.S. tariffs compel agile sourcing and near-shoring strategies. Segmentation analysis reveals distinct growth pockets in high-performance alloy wire, ultra-fine diameters, and specialized spraying processes, underpinned by diverse end-use requirements across aerospace, automotive, electronics, and medical sectors.
Regional insights highlight North America’s focus on domestic capacity, EMEA’s environmental and defense imperatives, and Asia-Pacific’s scale-driven precision applications. The competitive landscape is populated by global incumbents and agile regional specialists, each advancing unique value propositions through R&D, vertical integration, and strategic partnerships. By synthesizing these insights into coherent strategic plans, industry stakeholders can navigate volatility, unlock new value, and build resilient supply chains poised for long-term success.
This section provides a structured overview of the report, outlining key chapters and topics covered for easy reference in our Molybdenum Wire for Spraying market comprehensive research report.
- Preface
- Research Methodology
- Executive Summary
- Market Overview
- Market Dynamics
- Market Insights
- Cumulative Impact of United States Tariffs 2025
- Molybdenum Wire for Spraying Market, by Type
- Molybdenum Wire for Spraying Market, by Diameter Range
- Molybdenum Wire for Spraying Market, by Production Technique
- Molybdenum Wire for Spraying Market, by Spraying Process
- Molybdenum Wire for Spraying Market, by Application
- Molybdenum Wire for Spraying Market, by End Use
- Molybdenum Wire for Spraying Market, by Product Form
- Americas Molybdenum Wire for Spraying Market
- Asia-Pacific Molybdenum Wire for Spraying Market
- Europe, Middle East & Africa Molybdenum Wire for Spraying Market
- Competitive Landscape
- ResearchAI
- ResearchStatistics
- ResearchContacts
- ResearchArticles
- Appendix
- List of Figures [Total: 30]
- List of Tables [Total: 461 ]
Next Steps: Engage with Ketan Rohom to Secure the Full Report
Ready to leverage these insights and secure a competitive edge in the molybdenum wire spraying market? Contact Ketan Rohom, Associate Director, Sales & Marketing, to purchase the comprehensive market research report and gain full access to in-depth analysis, proprietary data, and strategic guidance tailored to your business objectives.
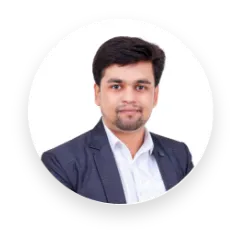
- When do I get the report?
- In what format does this report get delivered to me?
- How long has 360iResearch been around?
- What if I have a question about your reports?
- Can I share this report with my team?
- Can I use your research in my presentation?