The Monocrystalline Silicon Wafer Market size was estimated at USD 11.94 billion in 2024 and expected to reach USD 12.69 billion in 2025, at a CAGR 6.02% to reach USD 16.96 billion by 2030.
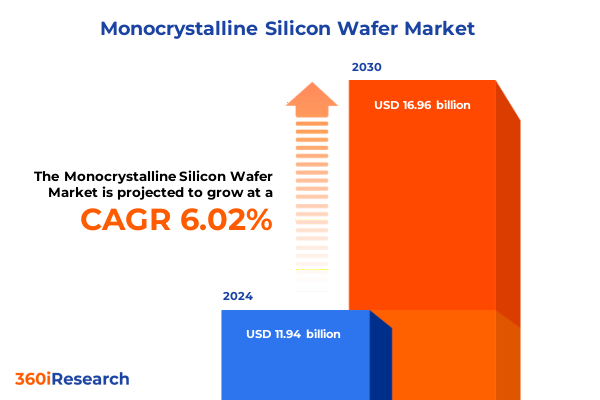
Executive Summary: Unlocking the Power of Monocrystalline Silicon Wafers
Monocrystalline silicon wafers have emerged as the cornerstone material for advanced photovoltaic modules, high-performance electronics, and cutting-edge semiconductor applications. Characterized by superior electron mobility, exceptional uniformity, and high energy conversion efficiency, these wafers enable transformative breakthroughs across multiple industries. In recent years, rapid technological evolution in solar energy systems, autonomous mobility solutions, and medical diagnostic devices has elevated the demand for wafers with impeccable crystal quality and purity.
Amid a dynamic global landscape, market participants face both unprecedented opportunities and intricate challenges. Manufacturers are racing to optimize production processes such as the Czochralski and float zone methods, while investors pour capital into heterojunction, PERC, and TOPCon innovations. Simultaneously, policy shifts-most notably proposed U.S. tariffs scheduled for 2025-promise to reshape supply chains and competitive positioning. For policymakers and corporate strategists alike, understanding these forces is essential to anticipate disruptions and seize growth trajectories.
This executive summary synthesizes key developments, delivers actionable insights on segmentation and regional dynamics, and highlights the leading players driving progress. It culminates in strategic recommendations designed to fortify resilience and capture emerging value in the monocrystalline silicon wafer arena.
Transformative Shifts in the Monocrystalline Silicon Wafer Landscape
Over the past decade, the monocrystalline silicon wafer domain has witnessed sweeping transformations driven by breakthroughs in cell architectures and scaling ambitions. Shifts from monofacial PERC to bifacial PERC designs have unlocked greater energy yields, while the advent of heterojunction technology (HJT) blends crystalline silicon with amorphous silicon layers to minimize recombination losses. Additionally, TOPCon cell stacks, with their multi-junction and single-junction configurations, are extending efficiency frontiers above 25 percent.
Beyond core technologies, the proliferation of autonomous and electric vehicles has created a parallel demand stream for wafers optimized for power electronics. Wearable health monitors and diagnostic equipment likewise require wafers with ultra-high purity and minimal defect densities. As renewable energy plants scale, wafer diameters have expanded from legacy 100 mm formats to 300 mm and beyond, driving economies of scale and cost reductions. Consequently, manufacturers are reevaluating their process footprints-whether ribbon growth for niche applications or large-boule Czochralski runs for mass production.
These converging trends have reshaped investment flows, shifted competitive dynamics, and catalyzed new strategic alliances. From government-backed R&D initiatives to startup ventures challenging incumbents, the landscape is more dynamic than ever. Looking ahead, agility in adopting emerging cell technologies and optimizing wafer dimensions will determine market leadership.
Cumulative Impact of U.S. Tariffs in 2025 on Wafer Supply Chains
Anticipated U.S. tariffs slated for implementation in 2025 are poised to reverberate across global wafer supply chains. Historically reliant on imports from Asia and Europe, U.S. module makers face the prospect of increased input costs, compelling them to diversify sourcing strategies post-tariff. As duties rise, vertical integration among semiconductor producers and solar manufacturers may accelerate, driving domestic wafer fabrication expansions to mitigate cost shocks.
Moreover, higher import levies could incentivize international producers to localize production in the Americas, leveraging free trade agreements to maintain price competitiveness. Simultaneously, non-U.S. markets may seize a supply window, redirecting Asian exports to Europe, the Middle East & Africa, and Asia-Pacific regions. This redirection will likely intensify competition in those territories, prompting suppliers to refine product portfolios across cell, module, and wafer segments.
In some cases, smaller wafer diameter sizes-such as 100 mm and 150 mm-could see price premiums as manufacturers allocate larger substrates to more profitability-sensitive applications like solar farms. Consequently, stakeholders must monitor tariff timelines closely, engage with policy forums, and proactively restructure supply agreements to retain operational continuity.
Key Segmentation Insights for Strategic Market Positioning
A rigorous examination of market segmentation reveals nuanced drivers shaping demand and strategic focus. In automotive applications, wafer requirements span autonomous vehicle sensors to powertrain inverters for electric and hybrid vehicles, each demanding precise electrical properties and robustness. Consumer electronics further subdivides into laptops, smartphones, and the burgeoning wearables category, where fitness trackers and smartwatches impose stringent size and purity tolerances.
Energy sector adoption covers both utility-scale renewable energy plants and distributed solar energy systems installed in commercial and residential settings, with bifacial and heterojunction cell technologies increasingly preferred. In healthcare, monocrystalline wafers underpin diagnostic equipment and therapeutic devices, alongside wearable health monitors designed for continuous patient monitoring. Telecommunications deployments involve wafers for data centers’ server power modules and telecom tower grid interfaces, requiring wafers tailored to high-temperature stability.
From a technology perspective, half-cell designs are gaining traction for enhanced shading tolerance, while back-contact IBC cells promise minimal resistive losses. Bifacial PERC continues to dominate, complemented by monofacial PERC for cost-sensitive installations. TOPCon’s multi-junction and single-junction variants are emerging as next-generation standards for high-performance modules.
Product-type segmentation underscores wafers as the foundational element, feeding into cell and module manufacturing ecosystems. Diameter optimization trends show a clear shift toward 200 mm and 300 mm-plus formats to lower per-watt production costs. End-user industries vary from automotive and consumer electronics device manufacturers to renewable energy developers, semiconductor fabs, and telecommunications infrastructure providers. Process selection spans the traditional Czochralski and float zone techniques and the less common ribbon growth for specialty applications. Material quality considerations split between standard and high-purity wafers, depending on downstream performance criteria. Finally, investments and research activities-backed by government funding, corporate R&D initiatives, and dynamic startup ventures-continue to push the envelope of crystal growth and wafer finishing technologies.
This comprehensive research report categorizes the Monocrystalline Silicon Wafer market into clearly defined segments, providing a detailed analysis of emerging trends and precise revenue forecasts to support strategic decision-making.
- Application
- Technology
- Product Type
- Diameter Size
- End-User Industry
- Manufacturing Process
- Material Quality
- Investments and Research
Key Regional Insights Driving Global Demand
Regional dynamics further delineate growth and competitive hotspots. In the Americas, strong policy incentives and domestic fabrication efforts are bolstering wafer production, particularly in the United States, where renewable energy targets and EV mandates drive local manufacturing. Moreover, partnerships between silicon suppliers and automotive OEMs illustrate a trend toward onshore supply chains to reduce geopolitical risk.
Over in Europe, the Middle East & Africa, sustainability regulations and solar deployment goals have ignited demand for high-efficiency wafers. Energy-intensive fabrication facilities in Germany and the Nordics leverage green energy sources, while emerging markets in the Middle East eye large-scale solar parks requiring bifacial and TOPCon modules, thus stimulating wafer orders.
Asia-Pacific remains the epicenter of wafer manufacturing capacity, led by China and Taiwan. Extensive integration between wafer producers and module assemblers has created a cost-competitive environment, encouraging continuous investments in PERC and heterojunction lines. Japan and South Korea, meanwhile, focus on specialty wafers for semiconductor and high-power electronics applications, maintaining diversified regional portfolios.
This comprehensive research report examines key regions that drive the evolution of the Monocrystalline Silicon Wafer market, offering deep insights into regional trends, growth factors, and industry developments that are influencing market performance.
- Americas
- Asia-Pacific
- Europe, Middle East & Africa
Key Company Insights Shaping Competitive Dynamics
Competitive dynamics are defined by a blend of diversified portfolios, technological leadership, and scale. Canadian Solar Inc. and First Solar, Inc. have made strategic moves into in-house wafer capabilities to secure supply and differentiate their module offerings. GCL-Poly Energy Holdings Limited continues to expand its wafer output, leveraging integration with solar cell lines to maintain cost advantages.
East Asian manufacturers such as Hanwha Q CELLS Co., Ltd., JA Solar Technology Co., Ltd., LONGi Green Energy Technology Co., Ltd., and Trina Solar Limited lead in PERC and bifacial wafer production, consistently pushing average efficiency benchmarks higher. Tongwei Co., Ltd. and Tongwei’s aggressive capacity growth underline China’s commitment to wafer leadership, while Toshiba Group’s affiliate Mitsubishi Materials Corporation emphasizes high-purity wafers for power electronics and automotive semiconductors.
Specialty suppliers such as Hemlock Semiconductor Corporation, Ohara Corporation, Tokuyama Corporation, and Sumco Corporation focus on high-cadence float zone and ribbon growth processes to serve diagnostic equipment and aerospace segments. Meanwhile, OCI Company Ltd., REC Silicon ASA, and Renewable Energy Corporation (REC) maintain balanced portfolios across standard and high-purity wafer lines. SunPower Corporation’s integrated model spans from wafer manufacturing to module assembly, and Wacker Chemie AG continues to invest in R&D for next-generation HJT and TOPCon substrates.
This comprehensive research report delivers an in-depth overview of the principal market players in the Monocrystalline Silicon Wafer market, evaluating their market share, strategic initiatives, and competitive positioning to illuminate the factors shaping the competitive landscape.
- Canadian Solar Inc.
- First Solar, Inc.
- GCL-Poly Energy Holdings Limited
- Hanwha Q CELLS Co., Ltd.
- Hemlock Semiconductor Corporation
- JA Solar Technology Co., Ltd.
- LONGi Green Energy Technology Co., Ltd.
- Mitsubishi Materials Corporation
- OCI Company Ltd.
- Ohara Corporation
- REC Silicon ASA
- Renewable Energy Corporation (REC)
- Shin-Etsu Chemical Co., Ltd.
- Sumco Corporation
- SunPower Corporation
- Tokuyama Corporation
- Tongwei Co., Ltd.
- Trina Solar Limited
- Wacker Chemie AG
- Zhejiang Jinko Solar Co., Ltd.
Actionable Recommendations for Industry Leaders
Industry leaders must embrace a multi-pronged strategy to capitalize on evolving market realities. First, diversifying technology roadmaps by piloting emerging cell architectures-such as heterojunction and TOPCon multi-junction designs-will secure performance leadership. Second, strengthening supply chain resilience through geographic diversification of wafer sources and strategic partnerships can mitigate tariff and logistics risks.
Third, investing in advanced manufacturing processes for larger diameter wafers and high-purity crystal growth will reduce per-watt costs and open new application segments in power electronics and medical devices. Fourth, aligning with government funding programs and forging alliances with research institutes can accelerate innovation cycles and de-risk R&D investments. Fifth, fostering agility in production lines to switch between wafer sizes, material purities, and process technologies will enable rapid response to end-user demands across automotive, consumer electronics, renewable energy, healthcare, and telecommunications.
Explore AI-driven insights for the Monocrystalline Silicon Wafer market with ResearchAI on our online platform, providing deeper, data-backed market analysis.
Ask ResearchAI anything
World's First Innovative Al for Market Research
Conclusion: Navigating Future Monocrystalline Silicon Wafer Trends
Monocrystalline silicon wafers will remain at the heart of global energy transition and high-performance electronics ecosystems. Technological evolution toward heterojunction, TOPCon, and advanced PERC variants promises continued gains in efficiency and reliability. Regional policy frameworks and tariff developments will dictate supply chain realignments, while rising demand across automotive, consumer electronics, and renewable energy sectors will sustain capacity expansions.
As the industry matures, strategic differentiation will hinge on the ability to integrate upstream crystal growth with downstream cell and module production, leverage scale economies in larger wafer formats, and maintain agility across process technologies. By synthesizing the insights presented here, stakeholders can navigate asymmetrical risks and unlock value in an increasingly competitive and dynamic market environment.
This section provides a structured overview of the report, outlining key chapters and topics covered for easy reference in our Monocrystalline Silicon Wafer market comprehensive research report.
- Preface
- Research Methodology
- Executive Summary
- Market Overview
- Market Dynamics
- Market Insights
- Cumulative Impact of United States Tariffs 2025
- Monocrystalline Silicon Wafer Market, by Application
- Monocrystalline Silicon Wafer Market, by Technology
- Monocrystalline Silicon Wafer Market, by Product Type
- Monocrystalline Silicon Wafer Market, by Diameter Size
- Monocrystalline Silicon Wafer Market, by End-User Industry
- Monocrystalline Silicon Wafer Market, by Manufacturing Process
- Monocrystalline Silicon Wafer Market, by Material Quality
- Monocrystalline Silicon Wafer Market, by Investments and Research
- Americas Monocrystalline Silicon Wafer Market
- Asia-Pacific Monocrystalline Silicon Wafer Market
- Europe, Middle East & Africa Monocrystalline Silicon Wafer Market
- Competitive Landscape
- ResearchAI
- ResearchStatistics
- ResearchContacts
- ResearchArticles
- Appendix
- List of Figures [Total: 32]
- List of Tables [Total: 948 ]
Call to Action: Connect with Ketan Rohom to Secure Your Market Intelligence
To secure comprehensive intelligence and tailor your strategic roadmap in light of shifting tariffs, emerging technologies, and competitive forces, connect with Ketan Rohom (Associate Director, Sales & Marketing at 360iResearch). Engage directly to explore the full market research report and actionable insights that will drive your organization’s growth and resilience in the monocrystalline silicon wafer arena.
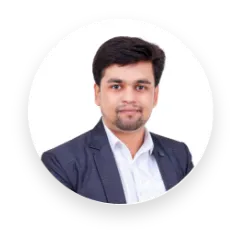
- How big is the Monocrystalline Silicon Wafer Market?
- What is the Monocrystalline Silicon Wafer Market growth?
- When do I get the report?
- In what format does this report get delivered to me?
- How long has 360iResearch been around?
- What if I have a question about your reports?
- Can I share this report with my team?
- Can I use your research in my presentation?