Introduction: Unveiling the Potential of High-Purity Atomized Metal Powder
High-purity atomized metal powder-boasting more than 99% metal content-has emerged as a cornerstone material in advanced manufacturing. Its exceptional characteristics, including uniform particle size distribution, controlled morphology, and superior flowability, have unlocked new possibilities across a spectrum of applications. From additive manufacturing to powder metallurgy and surface coatings, this grade of powder ensures repeatable performance, tighter tolerances, and enhanced material properties.
Driven by escalating demands for lightweight, high-strength components in aerospace and automotive sectors, alongside growing adoption in consumer electronics and medical device fabrication, the market is witnessing profound momentum. Environmental regulations and energy-efficiency targets further incentivize the transition toward atomized powders, whose precision and purity help minimize waste and optimize process yields. As industries pursue customized solutions and rapid prototyping, the ability to tailor alloy compositions-from iron-based to special-alloy formulations-underscores the transformative power of atomized powders.
In this executive summary, we provide a structured overview of the forces reshaping this landscape, analyze key drivers and headwinds, and offer strategic insights for stakeholders aiming to capitalize on this high-purity powder revolution.
Transformative Shifts in the Atomized Metal Powder Landscape
The atomized metal powder arena is undergoing several transformative shifts that are redefining competitive dynamics. First, digital manufacturing integration is accelerating, as industrial players embed real-time monitoring, machine-learning algorithms, and closed-loop quality control systems into atomization and post-processing workflows. This convergence of data and production enhances consistency, reduces scrap rates, and drives throughput gains.
Second, sustainability imperatives have elevated lifecycle analysis and green certifications to strategic priorities. Manufacturers are optimizing gas and plasma atomization processes to lower carbon footprints, recover inert gases, and implement water-recycling schemes. Third, supply-chain resilience has taken center stage; geopolitical uncertainties and raw-material sourcing constraints are prompting regional capacity investments and dual-sourcing strategies.
Lastly, process intensification-marked by hybrid atomization techniques and novel alloy development-is unlocking new performance thresholds. Companies are collaborating with research institutions to engineer powders with tailored porosity, enhanced corrosion resistance, and integration-ready surface chemistries. Together, these shifts signal a new era of agility, precision, and responsibility in the atomized metal powder industry.
Cumulative Impact of United States Tariffs 2025
The introduction of new United States tariffs in 2025 marks a critical inflection point. By imposing additional duties on key imported powder grades, cost structures have been materially altered. Suppliers reliant on gas and plasma atomization facilities in Asia and Europe are now grappling with increased landed costs, compelling many to reevaluate sourcing strategies.
In response, domestic producers have accelerated capacity expansion, leveraging proximity advantages to aerospace and defense contracts. While end-users face up to a 15% rise in input prices under the new tariff regime, the impetus for on-shore production has unlocked opportunities for retrofitting existing metallurgical plants and commissioning greenfield facilities.
Consequently, supply chains are diversifying, with secondary markets in Latin America and Southeast Asia emerging as alternative hubs. Although short-term price volatility may challenge procurement planning, the long-term effect will likely be a more balanced global footprint and bolstered domestic capabilities. Industry leaders who anticipate tariff-driven shifts and invest in local infrastructure stand to secure competitive advantage while mitigating exposure to trade policy headwinds.
Key Segmentation Insights Across Applications, Methods, and Performance
A deep dive into industry applications reveals that the aerospace sector leads demand for high-purity powders, driven by stringent safety standards and complex geometries. The automotive market, meanwhile, is rapidly adopting atomized metal powders for lightweight structural parts and thermal management components. Consumer electronics manufacturers are leveraging fine particle distributions to achieve miniaturized devices, while the energy industry incorporates specialized alloys into turbine blades and heat-exchanger elements. Industrial equipment producers utilize robust iron-based powders for wear-resistant parts, and medical device firms prioritize biocompatible compositions.
Examining production methods, centrifugal atomization offers cost advantages for larger particle sizes, whereas gas atomization remains the workhorse for general-purpose and high-performance alloys. Plasma atomization is gaining traction for specialty powders requiring extreme purity, and water atomization presents a sustainable, lower-cost route for ferrous applications.
When it comes to alloy composition, iron-based powders dominate volumetric consumption, nonferrous blends address corrosion-resistant applications, and special-alloy formulations unlock high-temperature and high-strength performance. Particle characteristics such as controlled morphology, narrow size distributions, and optimized surface area and porosity are critical for powder-bed fusion and binder-jetting processes.
Quality standards differentiate custom-certified offerings from mass-market grades, with high-purity and standard certifications guiding procurement decisions. In the innovation pipeline, powders at the research and development and prototype stages signal future commercial adoption, while fully commercialized grades meet today’s industrial throughput requirements. Performance metrics-cost efficiency, energy consumption, flowability, and stability-ultimately determine application fit, driving continuous process and material refinements.
This comprehensive research report categorizes the More than 99% Atomized Metal Powder market into clearly defined segments, providing a detailed analysis of emerging trends and precise revenue forecasts to support strategic decision-making.
- Industry Applications
- Production Methods
- Material And Alloy Composition
- Particle Characteristics
- Quality And Certification Standards
- Application Development Stages
- Performance And Efficiency Metrics
Key Regional Insights Shaping Demand and Production
In the Americas, a robust base of aerospace, defense, and automotive manufacturing underpins steady demand for atomized powders. The United States remains the largest consumer, supported by strong R&D ecosystems and investment incentives that favor domestic sourcing. Canada and Brazil contribute to regional growth, particularly in automotive parts and mining equipment sectors.
Europe, the Middle East & Africa feature a diverse landscape: Germany, France, and the UK lead advanced manufacturing and certification programs, while emerging Middle Eastern markets invest in localized production to reduce import dependencies. Regulatory harmonization across the EU and GCC countries fosters cross-border trade in high-purity powders.
Asia-Pacific is the fastest-growing region, propelled by China’s expansion of additive manufacturing parks, Japan’s focus on micro-scale powder applications, South Korea’s electronics sector, and India’s ramp-up in metal 3D printing. Southeast Asian nations are gradually adopting localized atomization capabilities to serve domestic industrial equipment and automotive clients. Together, these regional dynamics offer a roadmap for targeted market entry and strategic partnerships.
This comprehensive research report examines key regions that drive the evolution of the More than 99% Atomized Metal Powder market, offering deep insights into regional trends, growth factors, and industry developments that are influencing market performance.
- Americas
- Asia-Pacific
- Europe, Middle East & Africa
Key Company Insights in a Competitive Market Landscape
Leading players such as Advanced Atomized Materials and Advanced Metal Powders Inc. are at the forefront of capacity expansions and process innovations. Alloy Atomization Technologies Inc. and Apex Atomized Metals Solutions Inc. have launched proprietary atomization platforms to enhance powder uniformity. Specialized firms including Atomized Edge Manufacturing, Atomized Excellence Labs, and Atomized Industries LLC focus on ultra-high-purity segments for aerospace and medical applications.
AtomX Powders and Alloys, Elemental Atomics Industries, Elite Powder Metallurgy, and FineMetal Atomization Corporation maintain diversified portfolios spanning ferrous and nonferrous grades. Global Powder Technologies Ltd., HighPurity Powders Solutions, and Johnson Metallurgy Corporation emphasize regional partnerships and integrated supply chains. Meanwhile, Legacy Metal Powder Solutions, MetalMaster Atomized Solutions, MetalPride Atomized Systems Inc., and MetalTrail Atomized Technology are optimizing throughput through digital process controls.
Innovation leaders such as Micro Powder Technologies, Microstructural Metal Powders, Nanoforge Metal Powders Inc., Nanopowder Industries Ltd., and Next Level Powder Technologies specialize in sub-micron and nanoparticle formulations. NextGen Powder Innovations Ltd., Powder Precision Inc., Precision Alloy Atomics, Precision Metal Powders Corp., Prime Alloy Atomization Ltd., and Prime Powder Solutions LLC are setting new benchmarks in customization and certification. ProAtom Comparative GmbH, ProMetal Powders International, and PureAtom Metals Inc. drive cross-border alliances, while Superior Atomics & Alloys Inc., Superior Powder Craft Inc., UltraFine Metallic Powders Corp., UltraPure Atomics, and Zenith Alloy Powder Inc. deliver niche offerings with rigorous quality controls.
This comprehensive research report delivers an in-depth overview of the principal market players in the More than 99% Atomized Metal Powder market, evaluating their market share, strategic initiatives, and competitive positioning to illuminate the factors shaping the competitive landscape.
- Advanced Atomized Materials
- Advanced Metal Powders Inc.
- Alloy Atomization Technologies Inc.
- Apex Atomized Metals Solutions Inc.
- Atomized Edge Manufacturing
- Atomized Excellence Labs
- Atomized Industries LLC
- AtomX Powders and Alloys
- Elemental Atomics Industries
- Elite Powder Metallurgy
- FineMetal Atomization Corporation
- Global Powder Technologies Ltd.
- HighPurity Powders Solutions
- Johnson Metallurgy Corporation
- Legacy Metal Powder Solutions
- MetalMaster Atomized Solutions
- MetalPride Atomized Systems Inc.
- MetalTrail Atomized Technology
- Micro Powder Technologies
- Microstructural Metal Powders
- Nanoforge Metal Powders Inc.
- Nanopowder Industries Ltd.
- Next Level Powder Technologies
- NextGen Powder Innovations Ltd.
- Powder Precision Inc.
- Precision Alloy Atomics
- Precision Metal Powders Corp.
- Prime Alloy Atomization Ltd.
- Prime Powder Solutions LLC
- ProAtom Comparative GmbH
- ProMetal Powders International
- PureAtom Metals Inc.
- Superior Atomics & Alloys Inc.
- Superior Powder Craft Inc.
- UltraFine Metallic Powders Corp.
- UltraPure Atomics
- Zenith Alloy Powder Inc.
Actionable Recommendations for Industry Leaders
To succeed in this dynamic environment, industry leaders should prioritize strategic investments in advanced atomization technologies, focusing on methods that balance throughput with purity requirements. Collaborative partnerships with academic and research institutions can accelerate development of next-generation alloys and morphologies. Expanding domestic capacity will mitigate exposure to tariff-induced cost pressures, while dual-sourcing strategies enhance supply-chain resilience.
Further, companies must adopt digital quality systems, leveraging machine-learning analytics and in-line sensors to ensure consistent powder properties and batch traceability. Pursuing internationally recognized quality and certification standards will open new aerospace, medical, and defense markets. Sustainability initiatives-such as inert gas recapture, water recycling in atomization, and carbon-neutral energy sourcing-will differentiate offerings and satisfy evolving regulatory frameworks.
Finally, a customer-centric approach that integrates rapid prototyping support, application-specific testing services, and collaborative supply-chain logistics will drive enduring partnerships. By aligning technological roadmaps with end-user requirements and policy trends, industry leaders can secure competitive advantage and long-term growth.
Explore AI-driven insights for the More than 99% Atomized Metal Powder market with ResearchAI on our online platform, providing deeper, data-backed market analysis.
Ask ResearchAI anything
World's First Innovative Al for Market Research
Conclusion: Navigating Opportunity in the High-Purity Atomized Powder Era
The atomized metal powder market is poised for sustained expansion, fueled by high-purity requirements, technological advancements, and regional diversification. As tariffs and sustainability mandates reshape cost structures, stakeholders must adopt agile production strategies and build robust domestic networks. Segmentation analysis underscores the importance of tailoring powder properties to specific applications and performance metrics, while competitive intelligence highlights a crowded landscape of specialized providers.
Success in this sector will hinge on the ability to integrate digital manufacturing, certify material quality, and collaborate across the value chain. Those who invest in next-generation atomization platforms, forge strategic alliances, and emphasize environmental stewardship will lead the market’s evolution. Ultimately, a data-driven, customer-focused approach will ensure that high-purity atomized powders continue to unlock innovation in aerospace, automotive, medical, and beyond.
This section provides a structured overview of the report, outlining key chapters and topics covered for easy reference in our More than 99% Atomized Metal Powder market comprehensive research report.
- Preface
- Research Methodology
- Executive Summary
- Market Overview
- Market Dynamics
- Market Insights
- Cumulative Impact of United States Tariffs 2025
- More than 99% Atomized Metal Powder Market, by Industry Applications
- More than 99% Atomized Metal Powder Market, by Production Methods
- More than 99% Atomized Metal Powder Market, by Material And Alloy Composition
- More than 99% Atomized Metal Powder Market, by Particle Characteristics
- More than 99% Atomized Metal Powder Market, by Quality And Certification Standards
- More than 99% Atomized Metal Powder Market, by Application Development Stages
- More than 99% Atomized Metal Powder Market, by Performance And Efficiency Metrics
- Americas More than 99% Atomized Metal Powder Market
- Asia-Pacific More than 99% Atomized Metal Powder Market
- Europe, Middle East & Africa More than 99% Atomized Metal Powder Market
- Competitive Landscape
- ResearchAI
- ResearchStatistics
- ResearchContacts
- ResearchArticles
- Appendix
- List of Figures [Total: 30]
- List of Tables [Total: 330 ]
Call-To-Action: Connect with Ketan Rohom to Secure Your Comprehensive Market Report
To access the full breadth of insights, data, and strategic analysis detailed in this report, please contact Ketan Rohom (Associate Director, Sales & Marketing at 360iResearch) to secure your copy and drive your next phase of growth.
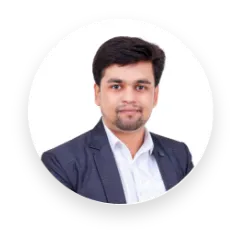
- When do I get the report?
- In what format does this report get delivered to me?
- How long has 360iResearch been around?
- What if I have a question about your reports?
- Can I share this report with my team?
- Can I use your research in my presentation?