Driving the Future of Precision Machining with Moving Column Gantry Systems
Moving column gantry milling systems stand at the forefront of precision machining, delivering unmatched rigidity, stability, and performance for complex, large-scale components. By integrating a movable column with a stationary table, these machines combine high throughput with exceptional accuracy, catering to the rigorous demands of aerospace, automotive, energy, and defense sectors. As manufacturing shifts toward greater customization and tighter tolerances, gantry milling platforms enable the production of heavy molds, large structural components, and intricate workpieces with minimal thermal deformation.
The combination of advanced spindle technologies, robust structural design, and precise linear guidance ensures consistent repeatability across extended runs. Moreover, modular configurations and adaptive software controls allow engineers to tailor machining envelopes to specific project requirements, reducing setup times and accelerating time to market. This executive summary delves into the latest transformative shifts, examines the cumulative impact of U.S. tariffs, explores key segmentation, regional growth patterns, and competitive dynamics, and presents actionable recommendations for decision-makers seeking to capitalize on emerging opportunities in this dynamic field.
Transformative Shifts Reshaping the Gantry Milling Landscape
The gantry milling landscape is undergoing a profound transformation driven by digitalization, automation, and sustainability imperatives. Industry 4.0 integration has elevated predictive maintenance capabilities through embedded sensors, real-time condition monitoring, and cloud-based analytics, enabling manufacturers to minimize unplanned downtime and optimize asset utilization. Concurrently, multi-axis control systems-spanning from 3-axis to full multiaxis architectures-are expanding envelope complexity and enhancing contouring performance.
In parallel, the push for lightweight, high-strength materials such as carbon fiber composites and titanium alloys has intensified demand for machines capable of high torque at low speeds, precise chip evacuation, and dynamic rigidity. Robotics and automated material-handling solutions are converging with gantry platforms to support lights-out operation and seamless workflow integration.
Sustainability considerations are reshaping procurement and operations, with energy-efficient drives, regenerative braking, and closed-loop coolant systems becoming standard design features. As these trends continue, the gantry milling sector is poised to deliver smarter, greener, and more flexible production ecosystems.
Cumulative Impact of United States Tariffs 2025 on Gantry Milling Operations
Recent U.S. tariff measures targeting heavy machinery and machine tool imports have reverberated across supply chains, compelling manufacturers to reevaluate sourcing strategies and cost structures. Increased duties on critical subcomponents have driven up input costs, prompting many OEMs to renegotiate supplier agreements, localize production, or explore near-shore partnerships to mitigate exposure. As a result, project lead times have lengthened in some segments while end users face higher acquisition prices.
In response, several gantry mill producers are shifting toward captive manufacturing of key assemblies, leveraging vertical integration to control quality and reduce duty burdens. Others are investing in automated material-handling and advanced machining centers to offset higher labor costs through productivity gains.
Furthermore, strategic classification reviews and legal appeals have yielded partial tariff relief for some specialized equipment, underscoring the importance of proactive trade compliance. By aligning capital investment plans with evolving tariff regimes and pursuing diversified supplier networks, industry leaders can stabilize margins and sustain competitive pricing.
Key Segmentation Insights Revealing Diverse Applications and Technologies
Segmentation by machine type highlights two primary architectures: horizontal moving column gantry and vertical moving column gantry machines, each available in large, medium, and small configurations to suit diverse part geometries and floor-space constraints. When considering end-user industries, aerospace & defense-including aircraft component manufacturing and defense equipment manufacturing-ranks among the most demanding, followed by automotive with assembly line applications and component manufacturing. Electronics users require specialized enclosures and semiconductor equipment, while energy & power operators demand nuclear power equipment and turbine components. Metal working & fabrication firms focus on precision machinery and steel production, whereas shipbuilding customers need both component manufacturing and hull construction capabilities.
Control system segmentation reveals that CNC control dominates, offering 3-axis, 5-axis, and multiaxis platforms, while manual control persists for low-volume or highly specialized tasks, incorporating manual adjustment and semi-automatic adjustment modes. PLC-controlled solutions provide programmable flexibility through advanced or basic programming logic.
Application-based divisions encompass 3D contour milling for complex part production and prototyping, heavy material milling targeting aluminum and steel & iron, and precision component milling for automotive precision parts and medical equipment parts. Power source considerations separate electric powered machines-available in standard electric and variable frequency drive options-from hydraulic powered units featuring constant or variable pressure systems. Material handling technology splits between automated solutions such as conveyor belts and robotic handling and manual methods using cranes and forklifts. Finally, industry certification influences purchasing decisions, with industry-specific credentials like AS certification for aerospace and CE certification and broader ISO standards including ISO 14001 and ISO 9001.
This comprehensive research report categorizes the Moving Column Gantry Milling Machine market into clearly defined segments, providing a detailed analysis of emerging trends and precise revenue forecasts to support strategic decision-making.
- Type
- End-User Industry
- Control System
- Application
- Power Source
- Material Handling Technology
- Industry Certification
Key Regional Insights Driving Gantry Milling Growth Globally
The Americas continue to lead in investment for gantry milling platforms, driven by reshoring initiatives, robust aerospace and defense spending, and capacity expansion in automotive electrification. Additionally, end users in North America are accelerating digital transformation, with a high adoption rate of IIoT-enabled machining cells and integrated enterprise resource planning.
Across Europe, the Middle East & Africa region, strong demand for lightweight structures in aerospace and precision components in medical and luxury automotive is fueling purchases of high-rigidity gantry systems. Moreover, incentive programs for advanced manufacturing and industry-specific grants in Western Europe are reducing total cost of ownership and fostering innovation hubs.
In Asia-Pacific, rapid industrialization in Southeast Asia and continued strength in China’s energy and shipbuilding sectors are driving gantry mill uptake. Furthermore, local manufacturers are enhancing indigenous R&D capabilities to develop tailored solutions that address regional material preferences and compliance standards, cementing Asia-Pacific’s role as both a major consumer and emerging exporter of gantry milling technology.
This comprehensive research report examines key regions that drive the evolution of the Moving Column Gantry Milling Machine market, offering deep insights into regional trends, growth factors, and industry developments that are influencing market performance.
- Americas
- Asia-Pacific
- Europe, Middle East & Africa
Key Companies Insights Shaping Competitive Dynamics
Global leaders such as Breton S.p.A., DMG MORI Co., Ltd., and FPT INDUSTRIE S.p.A. continually elevate performance benchmarks through innovative structural designs and integrated software suites. German manufacturers including HEDELIUS Maschinenfabrik GmbH and Waldrich Coburg GmbH excel in high-precision, high-rigidity solutions, while Swiss firms like Mikron Group (Mikron Machining Solutions) and Starrag Group Holding AG deliver ultra-fine surface finishes and exceptional thermal stability. North American companies-involving Ingersoll Machine Tools, Inc., MAG America, Inc., MAG IAS GmbH, and SORALUCE America Inc.-focus on robust service networks and modular automation packages, and complement this with hybrid additive manufacturing options from MECALAC Construction Equipment UK Ltd.
Meanwhile, Japanese stalwarts Mitsubishi Heavy Industries Machine Tool Co., Ltd. and Toshiba Machine Co., Ltd. push multiaxis control integration, and Spanish innovators such as JUARISTI Innovaciones Eléctricas S.A. and Nicholas Correa SA offer cost-effective, high-throughput alternatives. SORALUCE S.Coop. and Zimmermann GmbH further diversify the market with specialized solutions for niche applications. Through strategic partnerships, acquisitions, and continuous R&D, these companies shape competitive dynamics and accelerate adoption of advanced gantry milling platforms.
This comprehensive research report delivers an in-depth overview of the principal market players in the Moving Column Gantry Milling Machine market, evaluating their market share, strategic initiatives, and competitive positioning to illuminate the factors shaping the competitive landscape.
- Breton S.p.A.
- DMG MORI Co., Ltd.
- FPT INDUSTRIE S.p.A.
- HEDELIUS Maschinenfabrik GmbH
- Ingersoll Machine Tools, Inc.
- JUARISTI Innovaciones Eléctricas S.A.
- MAG America, Inc.
- MAG IAS GmbH
- MECALAC Construction Equipment UK Ltd.
- Mikron Group (Mikron Machining Solutions)
- Mitsubishi Heavy Industries Machine Tool Co., Ltd.
- Nicholas Correa SA
- SORALUCE America Inc.
- SORALUCE S.Coop.
- Starrag Group Holding AG
- Toshiba Machine Co., Ltd.
- Waldrich Coburg GmbH
- Zimmermann GmbH
Actionable Recommendations for Industry Leaders to Navigate Market Complexities
To capitalize on evolving market dynamics, industry leaders should prioritize digital integration by deploying digital twins and advanced analytics to optimize toolpaths and reduce cycle times. They must also conduct comprehensive tariff classification audits and develop alternative sourcing strategies to cushion against policy shifts. Collaborative R&D initiatives with material suppliers and automation partners will accelerate the development of machines capable of machining novel composites and high-temperature alloys.
Manufacturers should diversify their service portfolios by offering predictive maintenance as a subscription and remote diagnostics to enhance customer retention. Investing in modular machine architectures with quick-change spindle interfaces and adaptable material-handling cells will support both high-volume production and low-volume customization. Pursuit of ISO 9001 and ISO 14001 certifications, alongside industry‐specific credentials, will reinforce credibility in regulated sectors.
Finally, talent development programs focused on digital skills, robotics-SME integration, and advanced process simulation are essential for sustaining innovation pipelines. By aligning capital budgets with these strategic imperatives, companies can secure operational resilience and drive profitable growth.
Explore AI-driven insights for the Moving Column Gantry Milling Machine market with ResearchAI on our online platform, providing deeper, data-backed market analysis.
Ask ResearchAI anything
World's First Innovative Al for Market Research
Conclusion: Seizing Opportunities in Moving Column Gantry Milling
Moving column gantry milling machines are critical enablers of high-precision, large-scale manufacturing across diverse industries. Emerging trends in automation, material innovation, and sustainability are redefining performance criteria, while tariff pressures underscore the need for agile supply chains and strategic sourcing. Segmentation analysis reveals opportunities to tailor machine configurations by type, control system, application, power source, material-handling technology, and certification requirements. Regional insights highlight robust growth in the Americas, evolving opportunities in Europe, Middle East & Africa, and rapid uptake in Asia-Pacific. Competitive dynamics remain intense, driven by a roster of global and regional leaders advancing multi-axis integration, digital platforms, and customer-centric service models.
By synthesizing these insights, decision-makers can shape investment roadmaps, optimize manufacturing footprints, and forge collaborations that accelerate innovation. As the industry continues to mature, those who proactively adapt to shifting market forces will emerge as the premier partners for tomorrow’s precision machining challenges.
This section provides a structured overview of the report, outlining key chapters and topics covered for easy reference in our Moving Column Gantry Milling Machine market comprehensive research report.
- Preface
- Research Methodology
- Executive Summary
- Market Overview
- Market Dynamics
- Market Insights
- Cumulative Impact of United States Tariffs 2025
- Moving Column Gantry Milling Machine Market, by Type
- Moving Column Gantry Milling Machine Market, by End-User Industry
- Moving Column Gantry Milling Machine Market, by Control System
- Moving Column Gantry Milling Machine Market, by Application
- Moving Column Gantry Milling Machine Market, by Power Source
- Moving Column Gantry Milling Machine Market, by Material Handling Technology
- Moving Column Gantry Milling Machine Market, by Industry Certification
- Americas Moving Column Gantry Milling Machine Market
- Asia-Pacific Moving Column Gantry Milling Machine Market
- Europe, Middle East & Africa Moving Column Gantry Milling Machine Market
- Competitive Landscape
- ResearchAI
- ResearchStatistics
- ResearchContacts
- ResearchArticles
- Appendix
- List of Figures [Total: 30]
- List of Tables [Total: 1208 ]
Connect with Ketan Rohom to Secure the Comprehensive Gantry Milling Market Report
To explore these insights in full and gain a competitive edge, connect with Ketan Rohom, Associate Director, Sales & Marketing. Secure the comprehensive gantry milling market research report today and equip your organization with the data-driven guidance needed to thrive in an evolving manufacturing landscape.
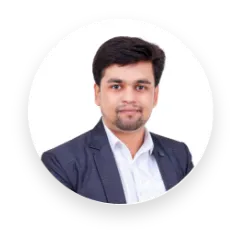
- When do I get the report?
- In what format does this report get delivered to me?
- How long has 360iResearch been around?
- What if I have a question about your reports?
- Can I share this report with my team?
- Can I use your research in my presentation?