Introduction to Multi-Chamber Formic Acid Vacuum Furnaces
The adoption of multi-chamber formic acid vacuum furnaces has redefined modern heat treatment processes by combining precise atmospheric control with high-throughput capabilities. This introduction outlines the core principles and value proposition of these advanced systems, which leverage formic acid decomposition to generate a clean, reducing atmosphere that minimizes oxidation and decarburization. By configuring multiple chambers in series, manufacturers can carry out discrete process steps-such as heating, vacuuming, and cooling-within a single integrated platform, driving consistent quality and optimized cycle times.
As production volumes and material specifications become increasingly demanding, the multi-chamber architecture offers unparalleled flexibility. Operators can tailor each chamber’s thermal profile, gas flow, and pressure parameters to suit varied applications, from forging and sintering to brazing and carburizing. The result is a modular, scalable solution that addresses throughput requirements without compromising process integrity.
This introduction sets the stage for a detailed exploration of paradigm shifts, regulatory influences, segmentation insights, regional dynamics, and competitive intelligence. The following sections will equip decision-makers and subject-matter experts with a comprehensive understanding of emerging trends, tariff impacts, and strategic imperatives in the expanding landscape of formic acid vacuum furnaces.
Transformative Technological and Industry Shifts
The landscape of formic acid vacuum furnace technology is undergoing transformative shifts driven by digital integration, sustainability mandates, and evolving end-user expectations. First and foremost, Industry 4.0 integration has enabled real-time process monitoring and advanced data analytics, empowering manufacturers to optimize chamber transitions, ensure repeatable thermal cycles, and reduce energy consumption. Predictive maintenance protocols now leverage sensor arrays to detect temperature fluctuations and component wear, minimizing unplanned downtime.
Moreover, environmental sustainability imperatives are reshaping furnace design. Engineers are increasingly incorporating energy-recovery systems and low-emission burners to adhere to stringent carbon-reduction targets. Formic acid’s clean decomposition profile aligns with these goals, eliminating harmful byproducts and simplifying exhaust treatment. Consequently, producers can demonstrate compliance with regulatory frameworks while appealing to eco-conscious customers.
In parallel, end-user industries demand tighter tolerances and faster throughput. For aerospace and automotive manufacturers, precision heat treatment under controlled atmospheres is no longer a luxury but a necessity to uphold component integrity and safety. As a result, multi-chamber configurations are evolving to support shorter cycle times and seamless transitions between processes such as annealing, brazing, and hardening. This convergence of digitalization, sustainability, and performance is redefining competitive advantage in the heat treatment sector.
Assessing the Cumulative Impact of U.S. Tariffs in 2025
The introduction of revised U.S. tariff policies in 2025 has exerted a cumulative impact across supply chains, procurement strategies, and capital expenditure decisions within the heat treatment equipment sector. Tariff adjustments on European and Asian imports have elevated landed costs for key components such as vacuum pumps, control systems, and specialty alloys. Consequently, domestic manufacturers have seen a relative advantage, prompting a reassessment of global sourcing frameworks and spurring near-shoring initiatives.
Procurement teams now face the dual challenge of managing increased duties while maintaining process integrity. Many have responded by renegotiating contracts to include longer lead-time orders and exploring alternative suppliers with U.S.-based production capabilities. In parallel, equipment vendors have expanded domestic manufacturing footprints to mitigate tariff exposure and strengthen customer relationships through shorter delivery windows.
These shifts underscore the importance of supply chain resilience. Organizations that proactively adjusted to tariff changes by diversifying sourcing strategies and localizing critical component assembly have preserved profit margins and sustained project timelines. As tariff frameworks continue evolving, stakeholders will need to remain vigilant, balancing cost pressures with operational continuity to navigate this new trade environment successfully.
Comprehensive Insights Across Market Segmentation Dimensions
A granular segmentation analysis reveals diverse value drivers and adoption patterns across end-user industries, applications, furnace types, material mandates, technological architectures, process requirements, operating temperatures, control platforms, coating processes, and market verticals. Based on end-user industry classification, aerospace players prioritize maintenance, repair, and overhaul protocols alongside original equipment manufacturing operations; automotive stakeholders emphasize precision assembly operations and high-yield component fabrication; and heat treatment service providers optimize for both commercial treatment workloads and in-house facility demands.
Application-based differentiation highlights specialized demands for annealing of aluminum and steel alloys, while brazing workflows cater to both aerospace component assemblies and sensitive electronic subassemblies. Hardening processes focus on fastener production and tool steel enhancement to meet rigorous mechanical specifications. In the context of furnace architecture, horizontal and vertical vacuum furnace designs offer distinct benefits in footprint flexibility, loading ergonomics, and thermal uniformity.
Material-based segmentation addresses the contrast between ferrous substrates-where alloy steel and cast iron commands robust treatment protocols-and non-ferrous alloys, notably aluminum and titanium grades. Technological frameworks span continuous throughput lines, modular multi-chamber systems available in horizontal or vertical configurations, and single chamber units suited for custom process sequences. Key process variants include vacuum carburizing with gas quenching or low-pressure approaches, vacuum degassing tailored for aluminum and steel, and powder sintering platforms for ceramic and metal matrix components. Operating temperature regimes cover low, medium, and high-temperature furnaces, with advanced graphite and molybdenum heating elements addressing elevated thermal demands. Control infrastructures range from fully automatic systems to programmable logic controller setups, each delivering scalable process governance. Lastly, coating processes encompass chemical vapor deposition and physical vapor deposition techniques, while defense and electronics verticals target both rugged, high-reliability defense applications and consumer electronics component manufacturing as well as semiconductor production.
This comprehensive research report categorizes the Multi-Chamber Formic Acid Vacuum Furnace market into clearly defined segments, providing a detailed analysis of emerging trends and precise revenue forecasts to support strategic decision-making.
- End-User Industry
- Application
- Furnace Type
- Material Type
- Technology
- End Use Process
- Operating Temperature Range
- Control System
- Coating Process
- Market Vertical
Regional Dynamics Shaping Global Adoption
Regional dynamics play a pivotal role in shaping adoption rates and strategic priorities for multi-chamber formic acid vacuum furnace technology. In the Americas, a blend of mature manufacturing hubs and emerging specialty metallurgical centers has driven investment in advanced heat treatment platforms that prioritize throughput and energy efficiency. Companies across North and South America leverage local supply chains to fast-track installation and service support, while Latin American players focus on cost-effective upgrades to existing infrastructure.
Across Europe, the Middle East, and Africa, stringent environmental regulations and incentive programs for green manufacturing have accelerated the adoption of low-emission furnace technologies. European OEMs emphasize modular multi-chamber layouts to accommodate evolving product lines, while Middle Eastern industrial parks integrate integrated waste-heat recovery systems. In African markets, opportunities lie in retrofitting legacy equipment to meet rising quality standards in defense and automotive sectors.
In the Asia-Pacific region, rapid industrialization and high-volume electronics production have spurred demand for precision atmosphere control and ultra-clean process environments. Manufacturers in East Asia focus on automation and digital integration to maintain competitiveness, whereas South Asian economies invest in scalable, modular solutions to support burgeoning aerospace and automotive supply chains. These regional trends underscore the need for tailored strategies that align with local regulatory frameworks, customer preferences, and infrastructure capabilities.
This comprehensive research report examines key regions that drive the evolution of the Multi-Chamber Formic Acid Vacuum Furnace market, offering deep insights into regional trends, growth factors, and industry developments that are influencing market performance.
- Americas
- Asia-Pacific
- Europe, Middle East & Africa
Competitive Landscape: Leading Industry Players
Competitive intensity in the heat treatment arena is defined by a cohort of established and emerging players, each bringing distinct technical portfolios and service capabilities. Leading service providers such as Bodycote continue to expand their global footprint, leveraging proprietary process recipes and extensive lab facilities. Carbolite Gero’s focus on bespoke thermal profiles and rapid prototyping has earned strong demand among research institutions and specialized manufacturers.
Equipment manufacturers like CONSARC and EBNER Industrieofenbau have honed modular multi-chamber solutions, enabling agile reconfiguration across process stages. Ipsen Process Combustion and Nabertherm GmbH differentiate through integrated automation packages and energy-efficient burner systems that reduce overall operating costs. Norsk Gjenvinning Metall AS applies its scrap metal handling expertise to develop customized degassing solutions, while Seco/Warwick brings advanced control algorithms and digital interfaces to complex thermal cycles. Tenova Inc. integrates additive manufacturing compatibility for hybrid sintering applications, and Thermcraft, Inc. delivers tailored refractory designs that ensure long service life even under aggressive formic acid atmospheres.
Together, these leading organizations drive innovation cycles, establish best practices, and set performance benchmarks. Their collective emphasis on R&D investment, customer-centric service models, and strategic partnerships continues to raise the bar for process reliability and operational efficiency.
This comprehensive research report delivers an in-depth overview of the principal market players in the Multi-Chamber Formic Acid Vacuum Furnace market, evaluating their market share, strategic initiatives, and competitive positioning to illuminate the factors shaping the competitive landscape.
- Bodycote
- Carbolite Gero
- CONSARC
- EBNER Industrieofenbau
- Ipsen Process Combustion
- Nabertherm GmbH
- Norsk Gjenvinning Metall AS (NFM)
- Seco/Warwick
- Tenova Inc.
- Thermcraft, Inc.
Actionable Recommendations for Industry Leadership
Industry leaders seeking to capitalize on the multi-chamber formic acid vacuum furnace opportunity should adopt a multi-pronged strategic roadmap. First, establishing cross-functional teams that integrate R&D, process engineering, and supply chain experts will accelerate the development of tailored process recipes and modular system enhancements. Prioritizing collaboration between control system architects and sustainability specialists will yield energy-optimization features and smart diagnostics that resonate with end-users grappling with rising energy costs and environmental mandates.
Second, forging strategic partnerships with material suppliers and end-user consortiums can secure early feedback loops, enabling rapid iteration on chamber configurations and gas management protocols. This collaborative approach fosters co-innovation, de-risking product launches and reinforcing market credibility.
Third, investing in digital-twin simulations and advanced process analytics will unlock continuous improvement mechanisms, ensuring repeatable results and minimizing scrap rates. By coupling virtual commissioning with predictive maintenance platforms, organizations can reduce cycle-time variability and extend asset lifecycles.
Finally, aligning product roadmaps with regional regulatory frameworks and tariff environments will fortify supply chain resilience and market access. Crafting flexible manufacturing solutions that can be localized or upgraded in situ will provide decision-makers with cost-effective pathways to adopt next-generation heat treatment technology.
Explore AI-driven insights for the Multi-Chamber Formic Acid Vacuum Furnace market with ResearchAI on our online platform, providing deeper, data-backed market analysis.
Ask ResearchAI anything
World's First Innovative Al for Market Research
Conclusion: Harnessing Innovation for Competitive Advantage
In conclusion, multi-chamber formic acid vacuum furnaces represent a convergence of precision engineering, environmental stewardship, and digital innovation. Their modular architectures and atmosphere control capabilities address the stringent demands of aerospace, automotive, electronics, and defense segments. As Industry 4.0 principles permeate the heat treatment sector, organizations that harness real-time data analytics, energy recovery systems, and predictive maintenance protocols will differentiate through higher throughput, lower operating costs, and enhanced process repeatability.
Moreover, adapting to evolving tariff landscapes and regional regulatory frameworks requires agile supply chain strategies and localized manufacturing partnerships. By integrating advanced material handling, customizable chamber sequences, and smart control platforms, manufacturers can respond swiftly to customer demands while maintaining robust quality assurance.
Ultimately, success will hinge on cross-disciplinary collaboration, continuous refinement of process recipes, and a proactive stance toward sustainability objectives. Those who embrace these imperatives stand poised to secure leadership positions in the evolving landscape of precision heat treatment.
This section provides a structured overview of the report, outlining key chapters and topics covered for easy reference in our Multi-Chamber Formic Acid Vacuum Furnace market comprehensive research report.
- Preface
- Research Methodology
- Executive Summary
- Market Overview
- Market Dynamics
- Market Insights
- Cumulative Impact of United States Tariffs 2025
- Multi-Chamber Formic Acid Vacuum Furnace Market, by End-User Industry
- Multi-Chamber Formic Acid Vacuum Furnace Market, by Application
- Multi-Chamber Formic Acid Vacuum Furnace Market, by Furnace Type
- Multi-Chamber Formic Acid Vacuum Furnace Market, by Material Type
- Multi-Chamber Formic Acid Vacuum Furnace Market, by Technology
- Multi-Chamber Formic Acid Vacuum Furnace Market, by End Use Process
- Multi-Chamber Formic Acid Vacuum Furnace Market, by Operating Temperature Range
- Multi-Chamber Formic Acid Vacuum Furnace Market, by Control System
- Multi-Chamber Formic Acid Vacuum Furnace Market, by Coating Process
- Multi-Chamber Formic Acid Vacuum Furnace Market, by Market Vertical
- Americas Multi-Chamber Formic Acid Vacuum Furnace Market
- Asia-Pacific Multi-Chamber Formic Acid Vacuum Furnace Market
- Europe, Middle East & Africa Multi-Chamber Formic Acid Vacuum Furnace Market
- Competitive Landscape
- ResearchAI
- ResearchStatistics
- ResearchContacts
- ResearchArticles
- Appendix
- List of Figures [Total: 36]
- List of Tables [Total: 1072 ]
Next Steps: Engage with Ketan Rohom to Access Full Report
To gain comprehensive insights and actionable intelligence on multi-chamber formic acid vacuum furnace technologies, reach out to Ketan Rohom (Associate Director, Sales & Marketing at 360iResearch). His expertise will guide you through detailed capabilities, supply chain considerations, and strategic takeaways essential for informed decision-making. Engage today to access the full report and transform your heat treatment operations.
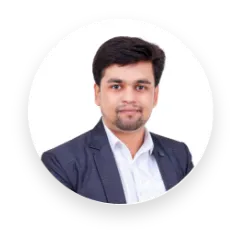
- When do I get the report?
- In what format does this report get delivered to me?
- How long has 360iResearch been around?
- What if I have a question about your reports?
- Can I share this report with my team?
- Can I use your research in my presentation?