Introduction
Multi-spindle screw machining has emerged as a cornerstone of high-precision, high-throughput manufacturing, enabling simultaneous turning operations across multiple spindles to achieve unparalleled cycle times and dimensional accuracy. As industries pursue ever-more complex geometries and tighter tolerances, this technology underpins critical segments such as automotive engine components, aerospace hydraulic systems, precision connectors for consumer electronics, and surgical instruments. Manufacturers are compelled to adopt multi-spindle platforms to remain competitive, responding to pressures for lower unit costs, accelerated time-to-market, and sustainable material utilization. Moreover, ongoing advancements in tooling materials, spindle integration, and machine control systems are reshaping expectations around performance, uptime, and maintainability. Transitioning from traditional single-spindle lathes, industry leaders now prioritize flexible, modular architectures that accommodate rapid changeovers between prototyping, small-batch, and volume production runs. This executive summary navigates the transformative forces, trade-policy headwinds, market segmentation dynamics, regional hotspots, and key players defining today’s multi-spindle screw machining service landscape.
Transformative Shifts in the Landscape
The industry is undergoing transformative shifts driven by the convergence of smart manufacturing, digitalization, and sustainability mandates. As machine builders integrate embedded sensors and edge computing, real-time process monitoring and adaptive control reduce scrap rates and unplanned downtime. Digital twins now simulate spindle loads, thermal drift, and material removal to optimize cutting parameters before metal ever meets the tool. Furthermore, additive manufacturing complements subtractive multi-spindle operations by generating internal cooling channels and lattice structures, enhancing part performance without compromising cycle times.
In parallel, rising labor costs and talent shortages are accelerating deployment of collaborative robots and automated part-handling cells. These systems seamlessly link multi-spindle centers with secondary operations-deburring, heat treatment, surface finishing-ensuring lights-out production. Sustainability goals also steer material selection toward recycled alloys and bio-derived plastics, prompting service providers to certify closed-loop supply chains and circular-economy practices. Consequently, decision-makers are evaluating machine capacity not merely on volume output but on carbon footprint and waste reduction.
Lastly, geopolitical considerations and nearshoring trends are prompting manufacturing hubs to reassess supply-chain resilience. In response, facilities are adopting modular platforms that can pivot between high-volume and low-to-medium volume runs, ensuring responsiveness to shifting demand patterns and local content requirements.
Cumulative Impact of United States Tariffs 2025
In 2025, new cumulative U.S. tariffs are reshaping cost structures across multi-spindle screw machining services. Tariffs on primary materials such as aluminum, stainless steel, and nickel-based superalloys have increased landed costs, driving some service providers to secure longer-term domestic contracts. Finished components imported from key trade partners now carry additional levies, prompting end users to assess total cost of ownership rather than unit price alone.
As a result, manufacturers are exploring dual-sourcing strategies, balancing cost advantages of offshore suppliers against tariff-free domestic alternatives. Many have accelerated capital investments in U.S.-based machining centers to mitigate duty exposure and shorten supply-chain lead times. These shifts have also catalyzed greater collaboration between machine tool builders and material producers, leading to vertically integrated solutions that lock in raw-material pricing and capacity.
Moreover, tariff-induced cost inflation is being partially passed through to end users, particularly in automotive and aerospace segments where complex, high-precision components are mission-critical. Service bureaus that demonstrate tariff mitigation-through tariff classification audits, bonded warehousing, or Free Trade Zone partnerships-are increasingly preferred. In light of these developments, companies that proactively manage trade compliance and diversify their supplier base are better positioned to sustain margins and retain customer loyalty.
Key Segmentation Insights
Insight into key segmentation reveals that service type dictates competitive positioning: prototyping services leverage flexible multi-spindle rigs for quick turnarounds and design validation, small batch production emphasizes setup efficiency and cost-effective tooling, while volume production demands robust spindle indexing and minimal changeover times. Material type influences process planning and cycle strategy: aluminum components-whether cast or extruded-enable high-speed turning with minimal thermal distortion, whereas lead-free brass and phosphor bronze provide superior wear resistance in valve and connector applications. Plastics such as ABS, nylon, and PTFE find favor in low-load or electrical insulation components, while alloy, carbon, and stainless steels deliver structural integrity for high-pressure systems. Superalloys like Hastelloy and Inconel are reserved for corrosive or high-temperature environments, requiring specialized tooling and coolant management.
End-user applications further stratify service offerings: aerospace hydraulic systems and landing gear parts demand NADCAP and ISO compliance, automotive engine components and transmission systems prioritize cycle consistency and defect reduction, electronics connectors and consumer assemblies benefit from sub-micron surface finishes, industrial pumps and valves rely on tight concentricity, and orthopedic implants along with surgical instruments mandate biocompatibility certifications. Machine capacity considerations-high volume versus low-to-medium volume-drive layout design and automation levels, while client type distinguishes aftermarket service providers from original equipment manufacturers seeking turnkey partnerships. Secondary operations such as deburring, heat treatment, surface finishes (anodizing, electroplating), tapping, and external or internal threading add value and ensure functional readiness. Finally, adherence to ASTM, ISO, and NADCAP standards remains a non-negotiable requirement, reinforcing quality assurance and regulatory acceptance across global supply chains.
This comprehensive research report categorizes the Multi-spindle Screw Machining Service market into clearly defined segments, providing a detailed analysis of emerging trends and precise revenue forecasts to support strategic decision-making.
- Service Type
- Material Type
- End User Applications
- Machine Capacity
- Client Type
- Secondary Operations
- Industry Standards & Compliance
Key Regional Insights
Regional dynamics underscore the Americas as a mature market characterized by extensive reshoring initiatives and strong downstream demand from automotive and medical device manufacturers. In Europe, Middle East & Africa, regulatory harmonization across the EU, coupled with rapid aerospace expansions in the Middle East, creates opportunities for high-precision service bureaus. Africa’s growing industrial equipment sector, particularly in petrochemicals and power generation, further diversifies demand patterns. Meanwhile, Asia-Pacific stands out for its rapid expansion in consumer electronics, automotive, and telecommunications infrastructure. Investment in advanced machining centers across China, Japan, South Korea, and India reflects the region’s drive toward vertical integration and export competitiveness. Navigating regional tariff structures, local content rules, and logistical constraints is essential for service providers seeking to optimize footprint and customer responsiveness.
This comprehensive research report examines key regions that drive the evolution of the Multi-spindle Screw Machining Service market, offering deep insights into regional trends, growth factors, and industry developments that are influencing market performance.
- Americas
- Asia-Pacific
- Europe, Middle East & Africa
Key Companies Insights
Leading companies showcase distinct strategic emphases: AccuRounds, Inc. has bolstered its multi-spindle platform portfolio with automated part-handling cells, while Ardel Engineering & Manufacturing Inc. targets medical device micro-components with ultra-tight tolerances. Clow Stamping Company differentiates through hybrid stamping and screw machining workflows. Davenport Machine’s modular multi-spindle architectures enable rapid reconfiguration between small and large batch runs. Pacific Swiss & Manufacturing Inc. focuses on stainless steel and superalloy components for chemical and semiconductor industries. Peterson Tool Company, Inc. delivers custom tooling solutions optimized for cycle time reduction. Pioneer Service Inc. excels in aftermarket retrofits and performance upgrades. Precipart Group, Inc. specializes in complex geometry production for aerospace and defense. Production Machining & Mfg emphasizes throughput scaling with integrated secondary operations. Sparton Corporation leverages aerospace heritage to secure high-integrity certifications. SwisTech Precision Inc. embeds Industry 4.0 sensors and analytics to deliver predictive maintenance and continuous process improvement.
This comprehensive research report delivers an in-depth overview of the principal market players in the Multi-spindle Screw Machining Service market, evaluating their market share, strategic initiatives, and competitive positioning to illuminate the factors shaping the competitive landscape.
- AccuRounds, Inc.
- Ardel Engineering & Manufacturing Inc.
- Clow Stamping Company
- Davenport Machine
- Pacific Swiss & Manufacturing Inc.
- Peterson Tool Company, Inc.
- Pioneer Service Inc.
- Precipart Group, Inc.
- Production Machining & Mfg
- Sparton Corporation
- SwisTech Precision Inc.
Actionable Recommendations for Industry Leaders
Industry leaders should pursue a multi-pronged strategy to strengthen market position and deliver unmatched service value. First, invest in digitalization initiatives-implement digital twins, advanced analytics, and IoT-enabled controls-to enhance process visibility and predictive maintenance. Second, diversify raw-material sourcing by establishing strategic agreements with domestic and nearshore suppliers, mitigating tariff exposure and supply-chain disruptions. Third, expand secondary-operation capabilities by integrating in-house surface treatments, heat-treating ovens, and automated deburring cells, delivering turnkey solutions that reduce customer inventory and handling costs.
Furthermore, cultivate workforce expertise through targeted training programs in multi-axis programming, robotics integration, and quality compliance protocols. Establish partnerships with tooling manufacturers and software vendors to co-develop cutting-edge toolpaths and adaptive control algorithms. Pursue certifications under ASTM, ISO, and NADCAP to differentiate in high-reliability sectors. Finally, embed sustainability metrics into capacity-planning decisions, adopting closed-loop coolant systems and energy-efficient spindle drives to meet corporate responsibility targets and appeal to environmentally conscious customers.
Explore AI-driven insights for the Multi-spindle Screw Machining Service market with ResearchAI on our online platform, providing deeper, data-backed market analysis.
Ask ResearchAI anything
World's First Innovative Al for Market Research
Conclusion
Multi-spindle screw machining stands at the intersection of precision engineering, advanced automation, and strategic supply-chain optimization. The convergence of smart manufacturing technologies, compounded by trade-policy shifts and evolving end-market demands, underscores the need for agile, data-driven service models. By aligning segmentation strategies with regional strengths, leveraging key partnerships, and embedding continuous improvement methodologies, service providers can capture growth opportunities and defend against margin erosion.
As the market matures, maintaining a competitive edge will hinge on the ability to integrate digital workflows, diversify material and supplier portfolios, and enhance turnkey capabilities. Ultimately, those who proactively address tariff pressures, regulatory requirements, and sustainability imperatives will emerge as preferred partners in critical industries ranging from aerospace to medical devices.
This section provides a structured overview of the report, outlining key chapters and topics covered for easy reference in our Multi-spindle Screw Machining Service market comprehensive research report.
- Preface
- Research Methodology
- Executive Summary
- Market Overview
- Market Dynamics
- Market Insights
- Cumulative Impact of United States Tariffs 2025
- Multi-spindle Screw Machining Service Market, by Service Type
- Multi-spindle Screw Machining Service Market, by Material Type
- Multi-spindle Screw Machining Service Market, by End User Applications
- Multi-spindle Screw Machining Service Market, by Machine Capacity
- Multi-spindle Screw Machining Service Market, by Client Type
- Multi-spindle Screw Machining Service Market, by Secondary Operations
- Multi-spindle Screw Machining Service Market, by Industry Standards & Compliance
- Americas Multi-spindle Screw Machining Service Market
- Asia-Pacific Multi-spindle Screw Machining Service Market
- Europe, Middle East & Africa Multi-spindle Screw Machining Service Market
- Competitive Landscape
- ResearchAI
- ResearchStatistics
- ResearchContacts
- ResearchArticles
- Appendix
- List of Figures [Total: 30]
- List of Tables [Total: 860 ]
Call-To-Action: Connect with Ketan Rohom for the Full Market Research Report
To gain comprehensive insights into the multi-spindle screw machining service market, including detailed competitive landscapes, technology assessments, and implementation roadmaps, contact Ketan Rohom, Associate Director, Sales & Marketing. Engage directly to secure full access to the market research report and discover actionable intelligence tailored to your strategic objectives.
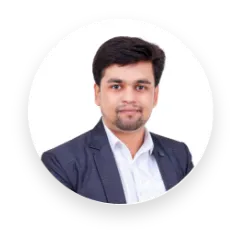
- When do I get the report?
- In what format does this report get delivered to me?
- How long has 360iResearch been around?
- What if I have a question about your reports?
- Can I share this report with my team?
- Can I use your research in my presentation?