Introduction to the Multiple Spot Welding Machines Landscape
Multiple spot welding machines play a pivotal role in high-precision joining applications across automotive, aerospace, electronics, and construction sectors. As manufacturers face rising production volumes and increasingly complex material combinations, they demand equipment that delivers consistent weld integrity, high throughput, and minimal downtime. This executive summary provides a concise yet comprehensive overview of the current market environment for both laser and resistance spot welding systems. It examines critical shifts in technology adoption, assesses the cumulative impact of recent trade measures, and explores detailed segmentation insights across seven key dimensions-from material and machine type to operational mode and production capacity. By synthesizing the most relevant trends and competitive dynamics, this document equips decision-makers with the strategic context needed to optimize capital investments, enhance operational efficiency, and secure a leading edge in an increasingly competitive landscape.
Transformative Shifts Reshaping the Market Dynamics
The spot welding market is undergoing transformative shifts driven by automation, digitalization, and evolving material demands. Industry 4.0 initiatives have accelerated integration of robotics and artificial intelligence, enabling real-time monitoring of weld parameters, predictive maintenance, and adaptive process control. Manufacturers now deploy sensor-enabled welding guns paired with cloud-based analytics to maximize uptime and minimize defects. At the same time, the rise of electric vehicles and lightweight alloys-particularly aluminum and composite materials-has reshaped equipment requirements. Laser spot welding systems are gaining traction for their precision and minimal heat input, while resistance spot welding remains indispensable for traditional steel assemblies and heavy-duty applications.
Sustainability considerations further influence design choices. Energy-efficient power sources and recyclable electrode materials are becoming table stakes, while end users demand lower carbon footprints throughout the machine lifecycle. Simultaneously, the proliferation of custom applications in aerospace subassemblies and medical device manufacturing is fostering demand for modular, portable welding units that can operate in confined or remote environments. Together, these forces are redefining product roadmaps, forging new vendor partnerships, and establishing fresh benchmarks for performance.
Cumulative Impact of United States Tariffs 2025 on Supply Chains
Since the United States implemented expanded tariffs on imported welding equipment and essential components in early 2025, supply chains have adapted rapidly. Levies applied to machine imports from major manufacturing hubs-including China, Europe, and Japan-have led OEMs to reassess their sourcing strategies. To mitigate added costs, some producers have relocated assembly operations closer to end markets, while others have worked with suppliers to reclassify components under alternative tariff codes.
This realignment has had several cascading effects. Equipment vendors are negotiating volume-based pricing agreements and offering flexible financing to help customers absorb initial cost increases. At the same time, domestic contract manufacturers and system integrators have experienced higher demand for localized assembly and customization services. However, smaller fabricators have faced margin pressure, prompting many to explore joint ventures or strategic alliances that can unlock economies of scale. Meanwhile, end users are weighing the trade-off between short-term capital expense and long-term operational efficiencies, particularly in sectors such as automotive and aerospace where tight quality tolerances are non-negotiable.
In-Depth Segmentation Reveals Nuanced Market Opportunities
Based on technology type, the market segments into laser spot welding and resistance spot welding. Laser systems further divide between automated laser spot welding machines-often integrated with robotic cells or gantry systems-and manual laser spot welding machines used for intricate repairs or low-volume production. Resistance spot welding also splits into automated resistance spot welding machines, which drive high throughput in assembly lines, and manual resistance spot welding machines that support maintenance tasks or specialized joins.
When viewed through the lens of material type, opportunities diverge between metal and non-metal materials. Metal materials encompass aluminum, prized for its light weight in electric vehicles; copper, valued for its conductivity in electrical assemblies; and steel, the workhorse of heavy industry. Non-metal materials include composite materials leveraged in aerospace and plastics commonly found in consumer appliances.
Under machine type segmentation, fixed spot welding machines break down into multiple-point fixed machines for simultaneous welding across large assemblies and single-point fixed machines for individual joint applications. Portable spot welding machines bifurcate into heavy-duty portable machines-ideal for construction site repairs-and light-duty portable machines suited to field service and small-scale projects.
End-user industry segmentation reveals distinct demand pockets. In aerospace and defence, growth centers around aircraft manufacturing and military equipment manufacturing, each requiring stringent certification and traceability. The automotive segment includes commercial vehicles, electric vehicles, and passenger vehicles, with each sub-segment influencing equipment selection. Construction applications split between commercial and residential projects, while electronics and appliances encompass consumer electronics and industrial electronics production.
Operational mode further refines the landscape into automatic mode and manual mode. Automatic systems can be non-programmable for basic repeat tasks or programmable for complex welding sequences, whereas manual operations rely on button-type controls for simple joins or lever-type mechanisms when higher force and control are needed.
Application-based segmentation targets assemblies and joining thin sheets. Assemblies include appliance assemblies and automotive assemblies, each with unique cycle time and weld strength requirements. Joining thin sheets encompasses aluminum sheets-commonly used in body panels-and steel sheets prevalent in structural components.
Finally, welding production capacity distinguishes high-volume production environments-often aligned with industrial standard production-from low-volume production runs tailored to custom applications. This duality influences machine durability, maintenance cycles, and overall cost of ownership.
This comprehensive research report categorizes the Multiple Spot Welding Machines market into clearly defined segments, providing a detailed analysis of emerging trends and precise revenue forecasts to support strategic decision-making.
- Technology Type
- Material Type
- Machine Type
- End-User Industry
- Operational Mode
- Application
- Welding Production Capacity
Regional Dynamics: Key Insights across Global Markets
In the Americas, robust automotive manufacturing and defense modernization programs drive demand for both resistance and laser spot welding equipment. North American OEMs prioritize energy-efficient systems that meet stringent environmental regulations, while Latin American markets are beginning to adopt portable units for mining and construction maintenance.
Europe, Middle East & Africa presents a diverse picture. Western Europe benefits from incentives supporting smart factories and green energy initiatives, prompting manufacturers to invest in automated laser spot welding for lightweight vehicle programs. Emerging markets in the Gulf and North Africa are investing heavily in infrastructure, creating a need for heavy-duty portable machines and fixed multiple-point systems for large-scale construction projects.
Asia-Pacific leads global consumption and production. China’s expansive electronics and electric vehicle sectors fuel adoption of both manual and high-speed automated units. Japan and South Korea focus on precision laser welding for semiconductors and medical devices, while Southeast Asia is expanding capacity in household appliance assembly, driving demand for programmable automatic resistance spot welding machines. Across the region, local manufacturing clusters and free trade agreements influence sourcing strategies, allowing vendors to optimize logistics and after-sales support networks.
This comprehensive research report examines key regions that drive the evolution of the Multiple Spot Welding Machines market, offering deep insights into regional trends, growth factors, and industry developments that are influencing market performance.
- Americas
- Asia-Pacific
- Europe, Middle East & Africa
Leading Industry Players Driving Technological Innovation
Leading industry players span global conglomerates to specialized integrators, each leveraging distinct strengths to capture market share. ABB Ltd. enhances its robotics-enabled welding cells with advanced motion control and digital twin functionality. ARO Welding Technologies SAS customizes resistance spot welding lines for European automakers, while Daihen Corporation invests in modular laser platforms that can adapt to shifting production requirements. DENGENSHA America Corporation focuses on turnkey resistance units supported by rapid deployment teams.
Esab Group, Inc. and Fronius International GmbH compete on data-driven power sources that optimize energy consumption, and Hyundai Welding Co., Ltd. teams up with local partners to expand service offerings in Asia. Kemppi Oy emphasizes user-friendly interfaces and remote diagnostics, whereas KUKA AG integrates intelligent spot welding heads within its well-established robotics portfolio. Lincoln Electric Holdings, Inc. and Miller Electric Mfg. LLC draw on decades of welding expertise to deliver comprehensive training and aftermarket support, ensuring low total cost of ownership. NIMAK GmbH, Panasonic Corporation, ROBOTIC SYSTEMS INTEGRATION, INC., and RobotWorx, Inc. further enrich the ecosystem by providing system upgrades, turnkey automation integration, and specialized programming services that streamline deployment and accelerate return on investment.
This comprehensive research report delivers an in-depth overview of the principal market players in the Multiple Spot Welding Machines market, evaluating their market share, strategic initiatives, and competitive positioning to illuminate the factors shaping the competitive landscape.
- ABB Ltd.
- ARO Welding Technologies SAS
- Daihen Corporation
- DENGENSHA America Corporation
- Esab Group, Inc.
- Fronius International GmbH
- Hyundai Welding Co., Ltd.
- Kemppi Oy
- KUKA AG
- Lincoln Electric Holdings, Inc.
- Miller Electric Mfg. LLC
- NIMAK GmbH
- Panasonic Corporation
- ROBOTIC SYSTEMS INTEGRATION, INC.
- RobotWorx, Inc.
Strategic Recommendations for Industry Leaders to Stay Ahead
To capitalize on emerging opportunities, industry leaders should adopt a multi-pronged strategy. First, prioritize investment in programmable automatic modes that balance non-programmable simplicity with programmable flexibility, enabling rapid changeovers and consistent weld quality. Second, diversify material handling capabilities by specifying machines capable of welding aluminum, copper, steel, composite materials, and plastics, thereby addressing a broader application spectrum.
Third, develop modular platforms that accommodate both fixed multiple-point installations for high-volume assembly lines and portable heavy-duty units for field service, expanding addressable markets. Fourth, mitigate tariff impacts by strengthening local assembly partnerships and exploring nearshoring opportunities to maintain competitive pricing. Fifth, integrate digital twins, IoT connectivity, and predictive maintenance tools to optimize uptime and reduce unplanned downtime across both manual and automatic modes.
Finally, cultivate strategic collaborations with electric vehicle OEMs, aerospace integrators, and electronics manufacturers to co-develop tailored solutions, secure recurring service revenues, and enhance customer loyalty. By combining these initiatives, leaders can reinforce operational resilience, accelerate innovation cycles, and sustain long-term growth.
Explore AI-driven insights for the Multiple Spot Welding Machines market with ResearchAI on our online platform, providing deeper, data-backed market analysis.
Ask ResearchAI anything
World's First Innovative Al for Market Research
Conclusion: Navigating the Evolving Spot Welding Market
Navigating today’s spot welding market requires a balanced approach that harmonizes technological innovation, supply chain agility, and customer-centric services. The interplay between laser and resistance systems, evolving material requirements, and regulatory influences underscores the importance of segmentation-driven strategies. By adopting programmable automation, localizing assembly operations, and forging partnerships across the value chain, stakeholders can overcome tariff challenges and capitalize on growth pockets.
Furthermore, leveraging digital tools-such as IoT-enabled sensors, predictive analytics, and digital twins-will unlock new efficiencies and reduce total cost of ownership. Collaboration with end-users in high-growth sectors like electric vehicles, aerospace, and electronics ensures solutions remain aligned with evolving performance standards. With a disciplined focus on innovation, operational excellence, and market segmentation, organizations are well-positioned to thrive in an environment defined by rapid change and heightened competition.
This section provides a structured overview of the report, outlining key chapters and topics covered for easy reference in our Multiple Spot Welding Machines market comprehensive research report.
- Preface
- Research Methodology
- Executive Summary
- Market Overview
- Market Dynamics
- Market Insights
- Cumulative Impact of United States Tariffs 2025
- Multiple Spot Welding Machines Market, by Technology Type
- Multiple Spot Welding Machines Market, by Material Type
- Multiple Spot Welding Machines Market, by Machine Type
- Multiple Spot Welding Machines Market, by End-User Industry
- Multiple Spot Welding Machines Market, by Operational Mode
- Multiple Spot Welding Machines Market, by Application
- Multiple Spot Welding Machines Market, by Welding Production Capacity
- Americas Multiple Spot Welding Machines Market
- Asia-Pacific Multiple Spot Welding Machines Market
- Europe, Middle East & Africa Multiple Spot Welding Machines Market
- Competitive Landscape
- ResearchAI
- ResearchStatistics
- ResearchContacts
- ResearchArticles
- Appendix
- List of Figures [Total: 30]
- List of Tables [Total: 1025 ]
Take the Next Step: Secure Your Competitive Advantage Today
To gain comprehensive insights and actionable data tailored to your strategic objectives, contact Ketan Rohom, Associate Director, Sales & Marketing. Unlock the full market research report and empower your team with in-depth analysis, proven recommendations, and competitive intelligence. Reach out today to secure your competitive advantage and drive sustainable growth.
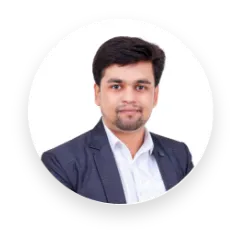
- When do I get the report?
- In what format does this report get delivered to me?
- How long has 360iResearch been around?
- What if I have a question about your reports?
- Can I share this report with my team?
- Can I use your research in my presentation?