Introduction to the New Energy Vehicle Traction Motor Core Landscape
New energy vehicles (NEVs) are reshaping the global automotive landscape by placing traction motor core design and performance at the heart of electrification efforts. Traction motor cores serve as the electromagnetic workhorses that convert electrical energy into mechanical torque, directly influencing vehicle range, efficiency, and cost. As governments and consumers increasingly prioritize sustainability, the demand for more power-dense, lightweight, and cost-effective core materials and manufacturing techniques has surged. Concurrent advances in materials science, electromagnetic modeling, and production automation have enabled designers to push the limits of motor efficiency and thermal management, while stringent regulatory frameworks on emissions and energy consumption are accelerating adoption across diverse vehicle segments.
Looking ahead to 2025 and beyond, the interplay between advancing core architectures and evolving supply chain dynamics will define the competitive landscape for motor core suppliers, OEMs, and end users. This executive summary offers a concise yet comprehensive overview of the key market drivers, transformative shifts, and strategic considerations shaping the NEV traction motor core market, furnishing decision-makers with the insights needed to navigate emerging challenges and capitalize on growth opportunities.
Emerging Technological and Regulatory Shifts in Motor Core Development
The NEV traction motor core domain has undergone rapid transformation driven by a confluence of technological breakthroughs, regulatory pressures, and shifting customer expectations. In recent years, major strides in optimizing permanent magnet synchronous motors through enhanced rare-earth magnet formulations and advanced lamination techniques have unlocked higher power densities, paving the way for longer vehicle range and reduced packaging constraints. Simultaneously, innovations in switched reluctance motor architectures have attracted interest for their reduced reliance on critical magnet materials, offering a resilient alternative amid rare-earth supply volatility.
On the regulatory front, increasingly stringent efficiency standards and incentives for zero-emission vehicles are catalyzing investment in next-generation core materials, including soft magnetic composites and novel silicon steel alloys. Digitalization across design and manufacturing-leveraging artificial intelligence for topology optimization and Industry 4.0–enabled production lines-has shortened development cycles and improved yield consistency. At the same time, heightened focus on end-of-life recyclability and circular economy principles is driving research into eco-friendly motor core materials and disassembly-friendly processes. Together, these shifts are setting the stage for an electrification ecosystem defined by agile supply chains, modular core designs, and cross-industry collaboration.
Cumulative Impact of U.S. Tariffs Announced for 2025 on Core Supply Chains
The implementation of additional tariff measures by the United States in 2025 targeting imported magnetic materials, electrical steels, and associated manufacturing equipment has introduced a new layer of complexity for traction motor core stakeholders. Suppliers reliant on cost-competitive laminations from overseas mills have encountered elevated input costs, prompting a reevaluation of procurement strategies. As tariffs on high-grade silicon steel and rare-earth magnets rise, many manufacturers are exploring domestic sourcing partnerships or nearshoring options to mitigate margin erosion and safeguard production continuity.
In response to these duties, several core producers have accelerated vertical integration, expanding in-house magnet processing and lamination stamping capabilities. Others are revisiting their design specifications to reduce material intensity, replacing ferrite cores or hard-to-procure alloys with locally abundant soft magnetic composites. Meanwhile, OEMs are consolidating supplier bases, prioritizing partners with strong compliance frameworks and proven cost-transmission mechanisms. Although tariff-induced cost pressures may translate into modest price increases for end users, the long-term impact is fostering increased resilience in domestic supply chains and spurring innovation in material substitution and process optimization.
Key Segmentation Insights across Motor Types, Applications, Materials, Processes, and End Users
Insight into market segmentation reveals that motor core demand is diversifying across both traditional and emerging categories. Analysis by motor type shows that asynchronous induction motors, including both slip ring induction and squirrel cage variants, continue to serve cost-sensitive segments, while brushless DC designs with inner and outer rotor configurations offer compactness for light-duty applications. At the premium end, permanent magnet synchronous machines employing interior magnet or surface-mounted magnet arrangements deliver superior torque density, and switched reluctance motors featuring salient pole or segmented rotor constructions are gaining traction for their robust thermal performance and reduced reliance on rare-earth elements.
Across application segments, heavy duty trucks and light duty commercial vehicles are driving demand through electrification mandates, spurring growth in battery electric and hybrid electric bus deployments. Passenger vehicle adoption spans on-road models as well as off-road specialty vehicles, while two-wheeler electrification, from motorcycles to scooters, is accelerating in urban mobility contexts. Material-wise, core selection spans copper-banded aluminum and laminated aluminum cores within the broader aluminum category; manganese-zinc and nickel-zinc ferrite cores; grain oriented and non-oriented electrical steel laminations; and advanced iron-based alloy or pure iron composite soft magnetic composites. Manufacturing processes vary from chequer pattern or V-notch interlocking, blanking and nibbling punching techniques, conventional or progressive die stamping, to arc or laser welding. End users range from motor repair shops and spare parts dealers within the aftermarket, to automotive part suppliers and electric vehicle manufacturers, as well as machinery plants and robotics manufacturers in industrial settings.
This comprehensive research report categorizes the NEV Traction Motor Core market into clearly defined segments, providing a detailed analysis of emerging trends and precise revenue forecasts to support strategic decision-making.
- Motor Type
- Application
- Material
- Manufacturing Process
- End User
Regional Dynamics Shaping Global Motor Core Supply and Demand
Regional dynamics play a critical role in shaping competitive positioning and investment priorities. In the Americas, strong incentives for local manufacturing and robust EV adoption rates have encouraged the expansion of domestic lamination facilities and magnet processing plants, reinforcing North America as a strategic hub. Latin American markets are ramping up pilot programs for electric buses and commercial trucks, leveraging locally produced core materials to reduce import dependencies.
Meanwhile, Europe, the Middle East & Africa exhibit a nuanced landscape: European Union targets for carbon neutrality are driving major OEMs to secure stable supplies of high-grade electrical steel and rare-earth magnets, leading to joint ventures with magnet mining firms. In the Middle East and Africa, nascent charging infrastructure rollouts and fleet electrification pilots are creating pockets of demand, though supply chain maturity varies widely across subregions.
The Asia-Pacific region remains the largest concentrated market, underpinned by established electrical steel mills, magnet refiners, and a dense network of motor core fabricators. China dominates production volumes, while Japan and South Korea continue to lead in ultra-fine-grain silicon steel and high-performance composite cores. Southeast Asian nations are emerging as attractive low-cost manufacturing alternatives for both lamination and winding operations.
This comprehensive research report examines key regions that drive the evolution of the NEV Traction Motor Core market, offering deep insights into regional trends, growth factors, and industry developments that are influencing market performance.
- Americas
- Asia-Pacific
- Europe, Middle East & Africa
Competitive Landscape and Strategic Moves among Leading Core Manufacturers
Leading motor core suppliers and automotive technology giants are fiercely competing to secure next-generation material sources and scale advanced manufacturing. BorgWarner Inc. is leveraging its global footprint to enhance in-house magnet bonding processes, while Bosch Mobility Solutions is piloting high-efficiency laminated steel cores tailored for premium EV models. BYD Company Limited and Tesla, Inc. are deepening vertical integration, controlling magnet refinement, lamination production, and motor assembly under one roof.
Continental AG and DENSO Corporation are partnering with specialized alloy producers to develop low-loss grain oriented electrical steel, and Faurecia SA is investing in soft magnetic composite research to reduce steel dependency. Hitachi Metals, Ltd. and Mitsubishi Electric Corporation maintain leadership in specialty silicon steel grades, whereas Hyundai Mobis Co., Ltd. and Valeo SA are focusing on modular core architectures for flexible platform integration. Johnson Electric Holdings Limited and Magna International Inc. are expanding robotics-enabled stamping and welding processes, and Panasonic Corporation is exploring next-gen iron-based composites. Siemens AG and ZF Friedrichshafen AG collaborate with academic institutions to accelerate AI-driven design optimization, positioning themselves at the forefront of rapid prototyping and digital twin methodologies.
This comprehensive research report delivers an in-depth overview of the principal market players in the NEV Traction Motor Core market, evaluating their market share, strategic initiatives, and competitive positioning to illuminate the factors shaping the competitive landscape.
- BorgWarner Inc.
- Bosch Mobility Solutions
- BYD Company Limited
- Continental AG
- DENSO Corporation
- Faurecia SA
- Hitachi Metals, Ltd.
- Hyundai Mobis Co., Ltd.
- Johnson Electric Holdings Limited
- Magna International Inc.
- Mitsubishi Electric Corporation
- Nidec Corporation
- Panasonic Corporation
- Siemens AG
- Tesla, Inc.
- Valeo SA
- ZF Friedrichshafen AG
Actionable Recommendations for Traction Motor Core Stakeholders
Industry leaders should prioritize the following strategic actions to navigate this rapidly evolving environment effectively:
- Secure diversified material sources by establishing partnerships with both domestic and international suppliers of electrical steel, rare-earth magnets, and soft magnetic composites, thereby mitigating tariff and geopolitical risks.
- Accelerate adoption of advanced manufacturing technologies-such as laser welding, progressive die stamping, and AI-driven process control-to improve yield rates, reduce cycle times, and enhance core precision.
- Invest in modular core architectures that support multi-voltage systems and simplified assembly to accommodate diverse vehicle platforms and reduce time-to-market for new models.
- Strengthen supply chain resilience through nearshoring initiatives and contingency planning, ensuring continuity in magnet and lamination supplies amid trade fluctuations.
- Embrace circular economy principles by integrating end-of-life core recycling programs and exploring eco-friendly binder systems, thereby aligning with sustainability mandates and reducing raw material dependency.
Explore AI-driven insights for the NEV Traction Motor Core market with ResearchAI on our online platform, providing deeper, data-backed market analysis.
Ask ResearchAI anything
World's First Innovative Al for Market Research
Conclusion and Strategic Outlook
The convergence of advanced materials, innovative manufacturing processes, and evolving trade policies is redefining the traction motor core market. Stakeholders who proactively adapt to these shifts-by embracing design flexibility, investing in resilient supply chains, and fostering cross-sector collaboration-will secure competitive advantage. As electrification accelerates across commercial, passenger, and emerging two-wheeler segments, the imperative to optimize core efficiency, reduce costs, and uphold sustainability commitments has never been greater. The insights outlined here provide a strategic foundation for guiding investment decisions and driving long-term success in the dynamic NEV ecosystem.
This section provides a structured overview of the report, outlining key chapters and topics covered for easy reference in our NEV Traction Motor Core market comprehensive research report.
- Preface
- Research Methodology
- Executive Summary
- Market Overview
- Market Dynamics
- Market Insights
- Cumulative Impact of United States Tariffs 2025
- NEV Traction Motor Core Market, by Motor Type
- NEV Traction Motor Core Market, by Application
- NEV Traction Motor Core Market, by Material
- NEV Traction Motor Core Market, by Manufacturing Process
- NEV Traction Motor Core Market, by End User
- Americas NEV Traction Motor Core Market
- Asia-Pacific NEV Traction Motor Core Market
- Europe, Middle East & Africa NEV Traction Motor Core Market
- Competitive Landscape
- ResearchAI
- ResearchStatistics
- ResearchContacts
- ResearchArticles
- Appendix
- List of Figures [Total: 26]
- List of Tables [Total: 1076 ]
Call to Action: Secure Your Comprehensive Traction Motor Core Market Report Now
To access in-depth analysis, granular segmentation data, and comprehensive supply chain mapping, contact Ketan Rohom (Associate Director, Sales & Marketing) to purchase the full market research report. Gain the strategic intelligence required to make informed decisions and position your organization at the forefront of traction motor core innovation.
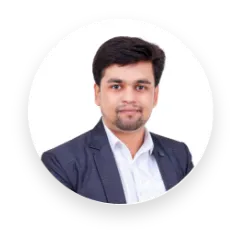
- When do I get the report?
- In what format does this report get delivered to me?
- How long has 360iResearch been around?
- What if I have a question about your reports?
- Can I share this report with my team?
- Can I use your research in my presentation?