Introduction to Non-Ferrous Metal Cold Heading Machines: Setting the Stage
The non-ferrous metal cold heading machine sector is experiencing a pivotal moment driven by technological innovation, evolving material demands, and shifting global trade dynamics. As manufacturers strive to meet the uncompromising standards of precision and efficiency required by industries such as aerospace, automotive, and electronics, the role of cold heading machinery in producing high-strength, intricate components has never been more critical. With an emphasis on sustainable processes and advanced forging techniques, stakeholders are realigning their investments to take advantage of machines capable of handling aluminum alloys, copper alloys, and specialized non-ferrous metals without sacrificing cycle times or part quality.
In this environment, understanding the interplay of market drivers - from machine type diversification to material-specific processing challenges - is essential. Moreover, emerging regulatory policies, notably tariffs and environmental guidelines, are reshaping procurement strategies and supply chain configurations. This report provides a structured lens through which decision-makers can assess current capabilities, anticipate technological shifts, and craft resilient operational plans. By spotlighting segmentation nuances, regional differentiators, and the competitive landscape, the following sections guide industry leaders toward informed decisions that harness the full potential of non-ferrous metal cold heading machines.
Transformative Shifts Driving Innovation and Efficiency
The landscape of cold heading machinery has undergone transformative shifts, propelled by breakthroughs in servo-driven systems and smart factory integration. Hydraulic, mechanical, and servo-driven single-die cold headers now operate with unprecedented repeatability, while multi-die platforms have evolved from two-die configurations to sophisticated four-die arrangements that deliver enhanced throughput and precision. Concurrently, specialized machines for ball-pin production, bolt heads, and nut forming are leveraging adaptive controls to accommodate new alloys and complex geometries.
Meanwhile, the rise of Industry 4.0 has fostered real-time monitoring and predictive maintenance, driving down unscheduled downtime. The integration of sensor networks and digital twins has enabled continuous process optimization, reducing scrap rates and energy consumption. In parallel, manufacturers are exploring warm forging techniques, such as inductive forging, to expand the range of non-ferrous materials they can process. This shift toward hybrid forging approaches underscores a broader trend: operators must balance speed, flexibility, and sustainability to remain competitive. As the market continues to embrace automation and data-driven insights, the competitive edge will go to those who can seamlessly blend traditional forging expertise with cutting-edge technology.
Assessing the Cumulative Impact of United States Tariffs from 2025
The cumulative impact of United States tariffs introduced in 2025 has introduced both challenges and opportunities across the non-ferrous cold heading value chain. On one hand, increased duties on imported aluminum and copper feedstocks have elevated raw material costs, forcing domestic producers to reexamine sourcing strategies and negotiate long-term contracts to stabilize input expenses. Simultaneously, higher import levies on finished cold heading machinery have reshaped procurement decisions, encouraging manufacturers to invest in local production or seek tariff-exempt regions for equipment acquisition.
In response, several leading suppliers have expanded North American operations or forged joint ventures to localize manufacturing, thereby mitigating tariff exposure. At the same time, end users are reassessing total cost of ownership, weighing initial capital outlay against long-term savings from reduced customs duties. Despite these headwinds, the tariff environment has also accelerated innovation: companies are leveraging modular machine designs that can be produced domestically at lower cost, and aftermarket service offerings have gained prominence as a means to prolong equipment life and defer new capital expenditure. As a result, the industry is charting a course toward greater self-reliance and increased emphasis on agility in supply and production planning.
Key Segmentation Insights across Machines, Materials, and Applications
Delving into segmentation reveals nuanced opportunities across machine architectures, materials, components, industries, technologies, and production scales. Starting with machine type, multi-die cold headers-ranging from two-die to four-die configurations-deliver high throughput and repeatable precision, while single-die cold headers, whether hydraulic, mechanical, or servo-driven, excel in flexibility and tight tolerances. Special purpose machines, designed specifically for ball-pin, bolt head, and nut forming, address the exacting demands of niche applications. When examining material processed, aluminum and its alloys, including recycled compositions, stand out for lightweight applications, whereas high and low brass variations, along with pure and alloyed copper, cater to a balance of conductivity and strength. Nickel and its alloys serve markets requiring exceptional corrosion resistance and high-temperature performance.
Component-level analysis highlights that production of nuts and bolts-from flange and hex variants to precision hex nuts-pins, including cotter and dowel pins, as well as rivets, whether pop or solid, and screws, whether for machine or wood applications, each demand tailored machine settings and tooling. Industry applications further differentiate needs: aerospace airframe and propulsion components necessitate the highest quality controls, automotive body, electrical, and transmission parts require robustness and volume, and construction fixtures, consumer electronics, and durable goods call for versatility. Cold forging and warm forging technologies, whether direct, indirect, furnace-based, or inductive, provide avenues to process a wider array of alloys. Finally, end-user capacity ranges from mass production lines to prototype runs, with continuous and batch operations offering distinct advantages in cost efficiency and customization. Synthesizing these segments equips stakeholders with the insight to align machine selection and process parameters to their precise operational goals.
This comprehensive research report categorizes the Non-ferrous Metal Cold Heading Machine market into clearly defined segments, providing a detailed analysis of emerging trends and precise revenue forecasts to support strategic decision-making.
- Machine Type
- Material Processed
- Components Produced
- Industry Application
- Technology
- End-User Capacity
Key Regional Insights Shaping Market Demand and Support
Regional dynamics exert a profound influence on machine adoption, supply chain logistics, and service availability. In the Americas, a robust presence of automotive and aerospace OEMs drives demand for high-precision, high-volume cold heading solutions, catalyzing domestic production and aftermarket support. Meanwhile, Europe, Middle East & Africa hosts a diverse industrial base-from aerospace hubs in Western Europe to construction and energy projects in the Middle East-requiring adaptable machines capable of processing specialized alloys under stringent regulatory standards. Emerging markets in Eastern Europe and Africa present growth corridors for entry-level to mid-range equipment, supported by localized service networks.
Across Asia-Pacific, a fertile manufacturing ecosystem spans from high-tech electronics clusters to large-scale construction initiatives, sustaining demand for both standard and custom cold heading systems. Firms are investing in smart factory upgrades to optimize yield across aluminum, brass, copper, and nickel production. Regional trade agreements and local content policies further shape procurement strategies, compelling global suppliers to strike partnerships and establish service centers close to end users. Collectively, these regional insights underscore the importance of flexible supply models and responsive technical support to seize growth and mitigate disruptions.
This comprehensive research report examines key regions that drive the evolution of the Non-ferrous Metal Cold Heading Machine market, offering deep insights into regional trends, growth factors, and industry developments that are influencing market performance.
- Americas
- Asia-Pacific
- Europe, Middle East & Africa
Key Company Insights Driving Technological and Service Excellence
A number of industry players are at the forefront of driving innovation and customer satisfaction through advanced machine offerings, service excellence, and strategic expansion. Leading the charge is Asahi Sunac Corporation, whose modular designs facilitate rapid integration and scalability. BRUDERER AG’s precision four-die platforms set benchmarks for high-speed production, while Carlo Salvi Machinery Limited is renowned for its turnkey solutions in special-purpose cold heading. Deringer-Ney Inc. and Hatebur Metalforming Equipment Ltd. have strengthened their North American and Swiss-manufactured portfolios respectively, enhancing local support networks.
Ingramatic Spa and Komatsu Industries Corp. have pioneered servo-driven single-die technologies that reduce setup times and energy consumption, and Manassero & C. Srl continues to expand its custom machine range for niche applications. Nakashimada Engineering Works, Ltd. and National Machinery entities deliver robust aftermarket services to maximize uptime. NEDSCHROEF Machinery and Sacma Group leverage their European heritage to innovate in warm forging processes, while Sakamura Machine Co., Ltd. and Smart Manufacturing Solutions GmbH integrate IoT and predictive maintenance features. These combined efforts from established and emerging players are shaping the competitive landscape, raising performance expectations and driving continuous improvement.
This comprehensive research report delivers an in-depth overview of the principal market players in the Non-ferrous Metal Cold Heading Machine market, evaluating their market share, strategic initiatives, and competitive positioning to illuminate the factors shaping the competitive landscape.
- Asahi Sunac Corporation
- BRUDERER AG
- Carlo Salvi Machinery Limited
- Deringer-Ney Inc.
- Hatebur Metalforming Equipment Ltd.
- Ingramatic Spa
- Komatsu Industries Corp.
- Manassero & C. Srl
- Nakashimada Engineering Works, Ltd.
- National Machinery Exchange, Inc.
- National Machinery LLC
- NEDSCHROEF Machinery
- Sacma Group
- Sakamura Machine Co., Ltd.
- Smart Manufacturing Solutions GmbH
Actionable Recommendations for Industry Leaders to Enhance Competitiveness
Industry leaders seeking to capitalize on market dynamics should focus on several strategic initiatives. First, forging partnerships or joint ventures to localize manufacturing can mitigate tariff exposure and improve delivery timelines. Second, integrating smart sensors and digital-twin capabilities into both new and legacy equipment will unlock predictive maintenance savings and boost overall equipment effectiveness. Third, diversifying material expertise-particularly in recycled alloys and advanced nickel grades-can open new customer segments and support sustainability goals.
Further, aligning machine portfolios to end-user capacity segments, from mass production to prototype workshops, ensures more precise value propositions. Leaders should also invest in modular designs that simplify aftermarket upgrades, thereby extending machine lifecycles and generating recurring service revenue. Finally, implementing targeted training and certification programs enhances operator proficiency and safety, translating to lower defect rates and higher throughput. By pursuing these actions with a clear roadmap, executives can strengthen their market positions and reinforce resilient, future-proof operations.
Explore AI-driven insights for the Non-ferrous Metal Cold Heading Machine market with ResearchAI on our online platform, providing deeper, data-backed market analysis.
Ask ResearchAI anything
World's First Innovative Al for Market Research
Conclusion: Charting a Path Forward in a Dynamic Market
The non-ferrous metal cold heading machine market stands at the intersection of technological innovation, evolving material demands, and regulatory complexity. By synthesizing insights on machine types, material processing, application requirements, regional nuances, and competitive capabilities, decision-makers can construct strategies that accelerate time to market, optimize total cost of ownership, and deliver superior product quality. As the sector continues to embrace automation, digitalization, and sustainability imperatives, stakeholders equipped with a deep understanding of segmentation and regional dynamics will be best positioned to navigate uncertainty and harness emerging opportunities.
This section provides a structured overview of the report, outlining key chapters and topics covered for easy reference in our Non-ferrous Metal Cold Heading Machine market comprehensive research report.
- Preface
- Research Methodology
- Executive Summary
- Market Overview
- Market Dynamics
- Market Insights
- Cumulative Impact of United States Tariffs 2025
- Non-ferrous Metal Cold Heading Machine Market, by Machine Type
- Non-ferrous Metal Cold Heading Machine Market, by Material Processed
- Non-ferrous Metal Cold Heading Machine Market, by Components Produced
- Non-ferrous Metal Cold Heading Machine Market, by Industry Application
- Non-ferrous Metal Cold Heading Machine Market, by Technology
- Non-ferrous Metal Cold Heading Machine Market, by End-User Capacity
- Americas Non-ferrous Metal Cold Heading Machine Market
- Asia-Pacific Non-ferrous Metal Cold Heading Machine Market
- Europe, Middle East & Africa Non-ferrous Metal Cold Heading Machine Market
- Competitive Landscape
- ResearchAI
- ResearchStatistics
- ResearchContacts
- ResearchArticles
- Appendix
- List of Figures [Total: 28]
- List of Tables [Total: 1213 ]
Call to Action: Connect with Ketan Rohom for Market Intelligence
Ready to unlock the full potential of non-ferrous metal cold heading technologies? Reach out to Ketan Rohom (Associate Director, Sales & Marketing at 360iResearch) to learn how our comprehensive research report can inform your strategic decisions and drive competitive advantage.
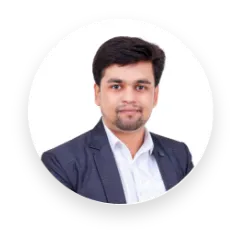
- When do I get the report?
- In what format does this report get delivered to me?
- How long has 360iResearch been around?
- What if I have a question about your reports?
- Can I share this report with my team?
- Can I use your research in my presentation?