The Nonwoven Industrial Membrane Market size was estimated at USD 1.39 billion in 2024 and expected to reach USD 1.50 billion in 2025, at a CAGR 7.18% to reach USD 2.12 billion by 2030.

Setting the Stage for Nonwoven Industrial Membrane Evolution
Nonwoven industrial membranes represent a class of engineered fabrics designed to deliver high-performance separation, filtration and protective functions across critical sectors. By leveraging advanced manufacturing techniques and a diverse range of polymer chemistries, these membranes achieve precise control over porosity, mechanical strength and chemical compatibility. Their modular nature allows for rapid customization to address evolving demands in energy storage, water purification, medical devices and industrial processing.
This executive summary offers decision-makers a concise yet comprehensive overview of the key factors reshaping the nonwoven industrial membrane landscape. It synthesizes the transformative shifts in technology, regulatory influences and trade policies, providing a roadmap through detailed segmentation, regional dynamics and competitive analysis. By highlighting actionable recommendations, this summary equips industry leaders with the insights needed to develop resilient strategies and capitalize on emerging growth opportunities.
How Emerging Forces Are Redefining the Nonwoven Membrane Sector
Sustainability imperatives and digital transformation are driving a renaissance in membrane manufacturing. Environmental regulations and circular economy goals have accelerated the adoption of bio-based and recyclable polymers, while Industry 4.0 technologies enable real-time monitoring of fiber formation and bonding processes. Manufacturers harness data analytics and predictive maintenance tools to optimize production yields and ensure consistent membrane performance under demanding operational conditions.
Meanwhile, shifting end-user requirements emphasize enhanced selectivity, throughput and durability at competitive cost points. Companies respond by integrating nanofiber technologies and hybrid composite architectures, extending membrane lifetimes and reducing energy consumption during separation processes. As geopolitical tensions influence raw material availability, supply chain resilience and alternative sourcing strategies have become paramount, reinforcing the need for agile business models.
Navigating the 2025 United States Tariff Landscape for Nonwoven Membranes
The implementation of new United States tariffs in 2025 has introduced additional duties on a range of polymer imports used in nonwoven membrane production. Suppliers now face elevated material costs and complex compliance requirements, prompting many to reevaluate shipment routes and renegotiate long-term contracts. These changes have ripple effects across global supply chains, translating into extended lead times and increased inventory holding costs for downstream end users.
To mitigate the impact of higher import charges, several membrane producers are investing in local polymer compounding facilities and strengthening relationships with domestic resin manufacturers. Others have adopted dynamic pricing models that more accurately reflect cost fluctuations. Collaborative sourcing agreements and joint ventures with material suppliers are also emerging as a strategic response, ensuring consistent supply while preserving competitive margins.
Unveiling Market Dynamics Through Comprehensive Segmentation
Understanding market behavior requires a granular look at applications that drive demand. Battery separators in advanced energy storage leverage membranes for thermal and chemical stability, while diaphragms in electrochemical cells optimize ion transfer. Filtration needs span from high-efficiency air filters to complex liquid separation processes, including microfiltration for particle removal, nanofiltration for selective molecule rejection and ultrafiltration for both organic and inorganic solute concentration. Protective apparel applications demand membranes that balance barrier protection with breathability, and general separation uses rely on tailored porosity and mechanical integrity.
Material selection plays a pivotal role in defining membrane characteristics. Polyester and polypropylene remain foundational due to their cost efficiency and mechanical robustness, while polyethylene offers improved chemical resistance in aggressive environments. Polytetrafluoroethylene (PTFE) serves critical roles where high-temperature stability and exceptional chemical inertness are required. By aligning polymer properties with process requirements, manufacturers can optimize performance across diverse conditions.
End use industries impose unique specifications that shape product development. Chemical processing facilities require membranes resilient to corrosive fluids and fluctuating pH levels, whereas electronics applications prioritize ultra-pure filtration for manufacturing consistency. The food and beverage sector adheres to stringent sanitation and regulatory guidelines, driving demand for hygienic membrane designs. Within the medical segment, healthcare apparel, medical devices and surgical procedures each call for precise barrier performance and biocompatibility. Oil and gas operations extend from drilling and completion to exploration, production and refining, necessitating membranes that can withstand high pressures and complex fluid chemistries. Water treatment applications range from large-scale industrial treatment to municipal supply systems and residential purification units. Manufacturing processes such as meltblown fiber deposition, needlepunch bonding, spunbond network formation, spunlace entanglement and thermal bonding contribute distinct textural and functional attributes. Product grade offerings include custom-engineered solutions, high performance lines and standard grades optimized for cost. Fabric weight classifications from light to medium to heavy gauge influence mechanical strength and flow characteristics. Sales pathways encompass both aftermarket distribution networks and original equipment manufacturer integrations.
This comprehensive research report categorizes the Nonwoven Industrial Membrane market into clearly defined segments, providing a detailed analysis of emerging trends and precise revenue forecasts to support strategic decision-making.
- Application
- Material Type
- End Use Industry
- Manufacturing Process
- Product Grade
- Fabric Weight
- Sales Channel
Decoding Regional Drivers Across the Global Nonwoven Membrane Market
Regional dynamics in the Americas reflect strong investment in water treatment infrastructure across the United States and Canada, driven by regulatory mandates for clean water and wastewater management. Latin American markets display growing interest in energy sector applications and portable filtration solutions, supported by international development funding and public–private partnerships.
In Europe, stringent environmental and safety regulations spur demand for advanced filtration and protective membrane solutions, particularly in automotive and pharmaceutical industries. The Middle East continues to rely on membrane technologies for desalination and petrochemical processing, reinforcing major capital projects. Africa presents burgeoning opportunities in municipal water purification and healthcare membrane applications, backed by expanding aid programs and infrastructure initiatives.
Asia-Pacific exhibits robust growth underpinned by large-scale manufacturing ecosystems in China and India, where cost-competitive production fosters widespread adoption of nonwoven membranes. Japan and South Korea focus on high-value segments such as electronics-grade filtration and medical device membranes, leveraging technological leadership. Emerging Southeast Asian markets are investing in municipal supply upgrades and industrial effluent treatment, creating new growth corridors for membrane suppliers.
This comprehensive research report examines key regions that drive the evolution of the Nonwoven Industrial Membrane market, offering deep insights into regional trends, growth factors, and industry developments that are influencing market performance.
- Americas
- Europe, Middle East & Africa
- Asia-Pacific
Competitive Landscape: Profiles and Strategic Moves of Key Players
Leading membrane manufacturers continue to invest heavily in research and development, expanding pilot lines for novel polymer blends and next-generation nanofiber processes. Strategic expansion into high-growth regions and capacity additions align production capabilities with anticipated demand in water treatment, energy storage and medical sectors. At the same time, specialized start-ups introduce disruptive technologies, including electrospun fiber techniques that enable ultrathin membrane layers and enhanced surface area for filtration.
Consolidation remains an active trend, with mergers and acquisitions allowing established players to integrate complementary portfolios and access new end-use channels. Partnerships between material suppliers and membrane producers accelerate co-development of application-specific solutions. Companies differentiate themselves through digital platforms that provide product tracking and performance analytics, reinforcing customer engagement and enabling service-based business models.
This comprehensive research report delivers an in-depth overview of the principal market players in the Nonwoven Industrial Membrane market, evaluating their market share, strategic initiatives, and competitive positioning to illuminate the factors shaping the competitive landscape.
- Toray Industries, Inc.
- DuPont de Nemours, Inc.
- Nitto Denko Corporation
- LG Chem Ltd.
- SUEZ SA
- Veolia Environnement S.A.
- Pentair plc
- Koch Industries, Inc.
- Asahi Kasei Corporation
- Danaher Corporation
Strategic Imperatives for Industry Leaders to Drive Growth
Industry leaders must adopt sustainable material strategies and implement circular economy principles to reduce environmental impact and comply with evolving regulations. Integrating digital monitoring systems across fiber production lines will optimize process consistency and enable predictive maintenance routines that minimize downtime. Investments in advanced polymer science and composite architectures promise to elevate separation performance and open doors to emerging application spaces.
Mitigating supply chain disruptions through geographic diversification and multi-sourcing agreements will strengthen resilience against tariff fluctuations and geopolitical uncertainties. Collaborations with academic and research institutions can accelerate the translation of laboratory breakthroughs into commercial membrane products. Establishing localized manufacturing footprints in high-growth regions, coupled with targeted sales and technical support, will ensure rapid response to customer requirements and build competitive positioning.
Robust Research Framework Underpinning Market Insights
This analysis integrates insights from primary interviews with senior executives, process engineers and materials scientists, supported by detailed survey responses from end users across target industries. Secondary sources encompass regulatory documents, trade association reports, patent filings and company technical publications. The research team applied both quantitative and qualitative methods to validate findings, utilizing triangulation techniques to cross-reference data points and eliminate inconsistencies.
An iterative review process involving independent experts ensured methodological rigor and objectivity. Segment-level analysis and regional breakouts provide granular visibility into market heterogeneity, while strategic recommendations emerge from in-depth scenario planning and trend extrapolation. The resulting report reflects a balanced approach that combines empirical evidence with thought-leadership insights.
Explore AI-driven insights for the Nonwoven Industrial Membrane market with ResearchAI on our online platform, providing deeper, data-backed market analysis.
Ask ResearchAI anything
World's First Innovative Al for Market Research
Harnessing Insights to Shape the Future of Nonwoven Membranes
The convergence of technological advancements, shifting regulations and evolving trade policies has created an inflection point for nonwoven industrial membranes. Stakeholders who embrace data-driven segmentation insights, anticipate regional growth patterns and monitor tariff impacts can develop agile strategies that capture value across the supply chain.
By aligning R&D investments with high-potential applications and reinforcing supply chain diversity, industry participants will secure a competitive edge. The nuanced understanding of material, process and channel dynamics presented here lays the groundwork for strategic decision-making that drives innovation and sustainable growth in the nonwoven membrane sector.
This section provides a structured overview of the report, outlining key chapters and topics covered for easy reference in our Nonwoven Industrial Membrane market comprehensive research report.
- Preface
- Research Methodology
- Executive Summary
- Market Overview
- Market Dynamics
- Market Insights
- Cumulative Impact of United States Tariffs 2025
- Nonwoven Industrial Membrane Market, by Application
- Nonwoven Industrial Membrane Market, by Material Type
- Nonwoven Industrial Membrane Market, by End Use Industry
- Nonwoven Industrial Membrane Market, by Manufacturing Process
- Nonwoven Industrial Membrane Market, by Product Grade
- Nonwoven Industrial Membrane Market, by Fabric Weight
- Nonwoven Industrial Membrane Market, by Sales Channel
- Americas Nonwoven Industrial Membrane Market
- Europe, Middle East & Africa Nonwoven Industrial Membrane Market
- Asia-Pacific Nonwoven Industrial Membrane Market
- Competitive Landscape
- ResearchAI
- ResearchStatistics
- ResearchContacts
- ResearchArticles
- Appendix
- List of Figures [Total: 30]
- List of Tables [Total: 515 ]
Take the Next Step with Our Market Research Report
To delve deeper into these insights and access exclusive data on market segments, regional forecasts and strategic profiles, connect with Ketan Rohom, Associate Director Sales & Marketing. He can guide you through tailored options and demonstrate how the full report supports your strategic initiatives.
Secure your comprehensive analysis today to drive informed investment, innovation and market positioning in the dynamic nonwoven industrial membrane landscape.
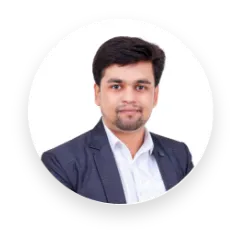
- How big is the Nonwoven Industrial Membrane Market?
- What is the Nonwoven Industrial Membrane Market growth?
- When do I get the report?
- In what format does this report get delivered to me?
- How long has 360iResearch been around?
- What if I have a question about your reports?
- Can I share this report with my team?
- Can I use your research in my presentation?